Accelerating Process Improvement with ChatGPT: Transforming GD&T Technology
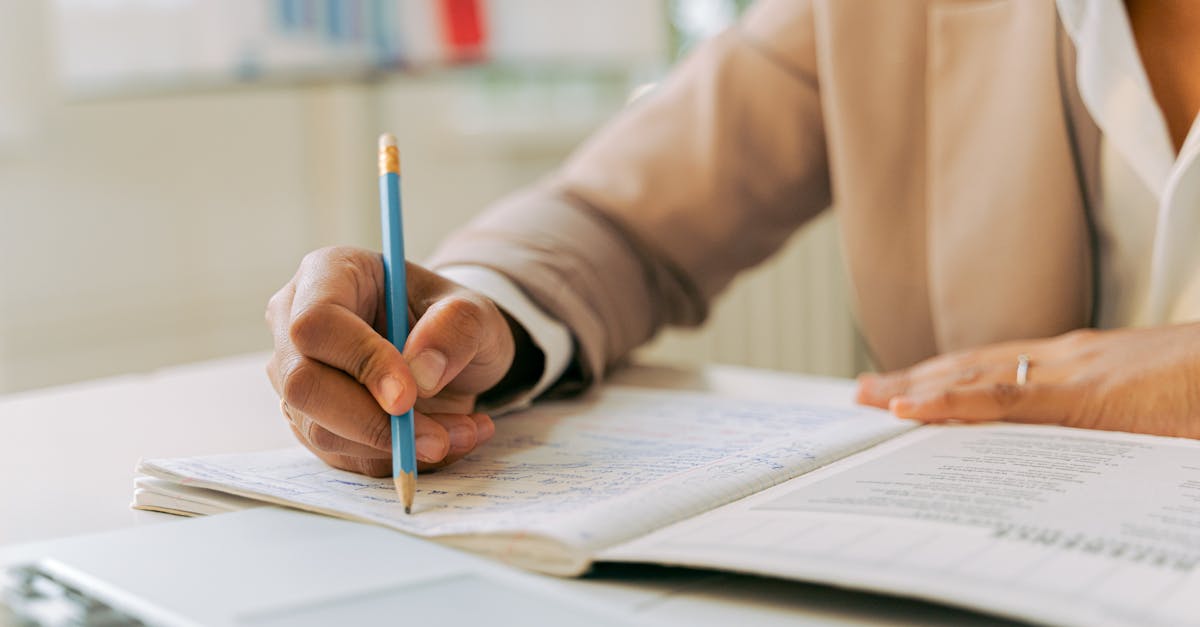
Geometric Dimensioning and Tolerancing (GD&T) is a system used to communicate tolerances and dimensions on engineering drawings. It provides a consistent and symbolic language for engineers, manufacturers, and inspectors to ensure designs are produced accurately and consistently. While GD&T is highly effective, there is always room for improvement. One way to enhance GD&T processes is by leveraging prior data to suggest process improvements.
What is GD&T?
GD&T is a symbolic language used to specify the geometry and allowable variation of parts in engineering drawings. It provides a clear and standardized way to communicate the design intent and define the acceptable limits of variation for features on a part.
By using GD&T, engineers can ensure that parts will fit and function as intended, even when they are manufactured by different suppliers or in different locations. GD&T eliminates ambiguity and allows for consistent interpretation of engineering drawings, which is particularly important in industries such as aerospace, automotive, and manufacturing.
The Role of Prior Data in GD&T Process Improvement
Prior data refers to historical data collected from previous manufacturing processes involving GD&T. This data can include measurements, inspection results, and feedback from manufacturing teams and customers. Leveraging this prior data helps identify patterns, trends, and areas for improvement in GD&T processes.
By analyzing prior data, organizations can gain valuable insights into the effectiveness of their existing GD&T processes and identify areas where improvements can be made. For example, if certain features consistently require excessive rework or have high rejection rates, adjustments can be made to the GD&T specifications to reduce errors and increase efficiency.
Benefits of Improving GD&T Processes with Prior Data
Improving GD&T processes with prior data can offer several benefits to organizations:
- Cost Reduction: By identifying and addressing recurring issues, GD&T process improvements can help reduce rework, scrap, and quality-related costs.
- Enhanced Quality: Adjustments based on prior data analysis can lead to higher product quality, improved customer satisfaction, and reduced warranty claims.
- Increased Efficiency: Fine-tuning GD&T processes can streamline manufacturing operations, reduce cycle times, and improve overall productivity.
- Standardization: Identifying common issues allows organizations to establish better standards and guidelines for GD&T, promoting consistency and minimizing confusion.
Implementing GD&T Process Improvements with Prior Data
To effectively implement GD&T process improvements using prior data, organizations can follow these steps:
- Data Collection: Gather relevant data from previous GD&T processes, including dimensional measurements, inspection results, and feedback.
- Data Analysis: Use statistical tools and techniques to analyze the collected data for trends, patterns, and potential areas for improvement.
- Identifying Improvement Opportunities: Identify specific areas within the GD&T process that can be enhanced based on the analysis of prior data.
- Implementing Adjustments: Based on the identified improvement opportunities, make adjustments to GD&T specifications, inspection methods, or training programs.
- Monitoring and Evaluation: Continuously monitor the impact of the implemented improvements and evaluate their effectiveness in reducing errors, rework, and rejection rates.
Conclusion
GD&T is a powerful system that ensures accurate and consistent communication of geometric tolerances and dimensions. By leveraging prior data, organizations can identify areas for improvement and make adjustments to their GD&T processes to enhance quality, reduce costs, and increase efficiency. The continuous improvement of GD&T processes through data-based analysis is essential to maintaining a competitive edge in industries that rely on precise engineering specifications.
Comments:
This article provides a great overview of how ChatGPT can be used to accelerate process improvement in GD&T technology. It's impressive to see the advancements in AI and how it can transform various industries.
I agree, Liam. The potential applications of ChatGPT are vast, and it's exciting to see it being implemented in areas like GD&T technology. I'm curious to know more about how it specifically enhances process improvement.
The use of ChatGPT in GD&T technology is undoubtedly a game-changer. It allows for faster and more accurate analysis, reducing errors and improving overall efficiency.
I've been following the development of ChatGPT, and it's fascinating to see it being used in such practical applications. Aditi, could you elaborate on the specific ways ChatGPT helps accelerate process improvement in GD&T technology?
Thank you for your comments! ChatGPT can assist in GD&T process improvement by quickly analyzing design data, identifying inconsistencies, and suggesting improvements. It can also help in automating certain tasks, freeing up valuable time for engineers to focus on more complex challenges.
Aditi, could you provide examples of industries or companies that have successfully implemented ChatGPT for GD&T process improvement? I'm curious to hear some real-world use cases.
Certainly, Jacob! Several automotive companies have implemented ChatGPT to enhance GD&T process efficiency, resulting in improved manufacturing quality. Additionally, aerospace companies have utilized ChatGPT to identify potential issues early in the design phase, avoiding costly delays later.
The benefits of ChatGPT in GD&T process improvement are undeniable. Its ability to analyze large datasets and provide valuable insights seems invaluable. Has anyone here personally used ChatGPT for process improvement?
I haven't personally used ChatGPT, but I've seen demos of its capabilities, and it's certainly impressive. I can imagine it being a valuable tool for GD&T process improvement.
I've started exploring ChatGPT for process improvement in another domain, and so far, it has shown promise. I believe it has the potential to revolutionize various industries, including GD&T.
I have experience using ChatGPT for process improvement in GD&T, and it has greatly improved our efficiency. The AI-powered suggestions helped us identify design inconsistencies early on, leading to better overall quality.
It's fantastic to hear success stories from those who have utilized ChatGPT for GD&T process improvement. Aditi, are there any challenges or limitations to consider when implementing ChatGPT in this context?
Great question, Emily. While ChatGPT has proven to be a powerful tool, it's essential to carefully review and verify its suggestions. Sometimes, it may suggest improvements that may not be practically feasible or violate certain constraints. It's crucial to exercise engineering judgment in such cases.
Aditi, how does ChatGPT handle complex design specifications and tolerances in GD&T? Can it accurately interpret and analyze all types of GD&T requirements?
ChatGPT has been trained on vast amounts of data, including complex design specifications and tolerances. While it can handle a wide range of GD&T requirements, there may be instances where explicit human intervention is required to ensure the accuracy and compliance of the analysis.
Aditi, I'm curious about the implementation process of ChatGPT for GD&T process improvement. Is it a straightforward integration, or are there specific requirements or preparations to consider?
Integrating ChatGPT for GD&T process improvement involves training the model on relevant data, validating its performance, and fine-tuning it to specific requirements. It's crucial to ensure the quality and accuracy of the data used for training to achieve the desired results.
Aditi, what are the potential cost savings or efficiency gains that companies can expect when implementing ChatGPT in GD&T process improvement?
The cost savings and efficiency gains can vary depending on the specific context and the extent of ChatGPT's implementation. However, companies can expect reduced errors, faster analysis, improved design quality, and overall time savings that can be utilized for complex problem-solving.
It's intriguing to see how AI technology like ChatGPT is reshaping industries and improving processes. Aditi, do you foresee any future advancements or developments in the GD&T domain that can leverage AI even further?
Absolutely, Sophia! As AI continues to evolve, we can expect even more sophisticated capabilities in GD&T technology. This may include advanced analysis of manufacturing processes, optimization algorithms, and enhanced predictive analytics to further streamline the overall design and manufacturing workflow.
Aditi, what are the potential limitations of using language models like ChatGPT in process improvement? Are there certain scenarios where it may not be as effective or suitable?
Language models like ChatGPT perform exceptionally well in assisting process improvement tasks. However, in scenarios where the data is limited or highly specific, or where significant engineering judgment is vital, a combination of AI-powered analysis and human expertise may be the most effective approach.
The collaboration between AI and human expertise seems crucial to ensure the best outcome in GD&T process improvement. Aditi, what are your thoughts on striking the right balance between relying on AI suggestions and human decision-making?
Emily, you're absolutely right. Striking the right balance is essential to leverage the benefits of AI while ensuring human decision-making and engineering expertise are appropriately valued. A collaborative approach, effectively utilizing AI suggestions and human judgment, can lead to optimal process improvements.
Aditi, could ChatGPT be applied to other engineering domains beyond GD&T? It seems like the potential applications of this technology are immense.
Absolutely, Jacob! ChatGPT can be adapted and applied to various engineering domains beyond GD&T. Its ability to analyze data, suggest improvements, and automate certain tasks can benefit industries such as civil engineering, mechanical design, and more.
I'm excited to see how AI technology will continue to evolve and transform the engineering landscape. Aditi, what kind of resources or knowledge would be required for a company looking to implement ChatGPT for GD&T process improvement?
Implementing ChatGPT for GD&T process improvement would require resources such as relevant data, computational power, AI expertise, and engineering domain knowledge. Collaboration between data scientists and domain experts is crucial to ensure the successful implementation and utilization of the technology.
Aditi, how customizable is ChatGPT for specific GD&T requirements? Can it be adapted to suit different industries or unique process improvement needs?
ChatGPT can be customized to suit specific GD&T requirements by training the model on relevant data and fine-tuning it to the desired context. This adaptability makes it versatile enough to cater to different industries and unique process improvement needs.
The flexibility and adaptability of ChatGPT make it a promising tool for various process improvement needs. Aditi, are there any specific data requirements or challenges to consider when training ChatGPT for GD&T?
When training ChatGPT for GD&T, it's essential to have a diverse range of high-quality design data that represents various scenarios and tolerance specifications. Ensuring data quality, relevance, and accuracy are paramount to achieve reliable results.
Aditi, I'm curious about the potential risks associated with using AI like ChatGPT in process improvement. Are there any ethical or safety concerns that companies should be aware of?
Emily, ethical considerations and safety concerns are important aspects to address when utilizing AI like ChatGPT in process improvement. Companies should be mindful of biases in the training data, validate the suggestions made by the model, and ensure compliance with applicable regulations and standards.
Aditi, what kind of feedback have you received from engineers or companies who have implemented ChatGPT for GD&T process improvement?
The feedback has been overwhelmingly positive. Engineers and companies have reported significant time savings, improved design quality, and the ability to focus on higher-level tasks. They have found ChatGPT to be a valuable tool in their GD&T process improvement initiatives.
The success stories and feedback shared about ChatGPT are encouraging. Aditi, do you have any recommendations for companies planning to integrate ChatGPT for GD&T process improvement?
For companies planning to integrate ChatGPT for GD&T process improvement, I would recommend thoroughly understanding the technology, validating its performance, collaborating closely with domain experts, and continuously refining and improving the system based on real-world feedback.
It's been an insightful discussion about the potential of ChatGPT in GD&T process improvement. Thank you, Aditi, for sharing your knowledge and answering our questions.
You're welcome, Ava! I'm glad I could be part of this discussion and provide more insights into ChatGPT's role in transforming GD&T technology. Thank you all for your interesting questions and engagement!
Thank you, Aditi, for taking the time to address our inquiries. This discussion has sparked my interest even more in exploring ChatGPT for process improvement.
Aditi, your expertise and insights have shed light on the benefits and considerations of using ChatGPT for GD&T. I appreciate your valuable input.
Thank you, Aditi, for sharing your expertise. ChatGPT's potential in GD&T process improvement is truly exciting, and your explanations have been very informative.
Aditi, thanks for providing real-world examples and insights. It has been a pleasure participating in this discussion and learning more about how ChatGPT can accelerate GD&T process improvement.
Thank you, Aditi, for your comprehensive responses. I now have a better understanding of ChatGPT's role in GD&T process improvement.
It's been a great exchange of thoughts and ideas. Aditi, your expertise has enhanced our understanding of ChatGPT and its potential in GD&T process improvement.
Indeed, this discussion has been enlightening. Aditi, thank you for sharing your knowledge and insights with us.
Thank you, Aditi, and everyone else for their valuable input. This dialogue has expanded my understanding of ChatGPT and its applications in GD&T process improvement.
Aditi, thank you once again for being part of this discussion. It has been enriching, and I'm excited to explore ChatGPT's potential further.