Boosting Accuracy and Efficiency: Leveraging ChatGPT for Inspection in GD&T Technology
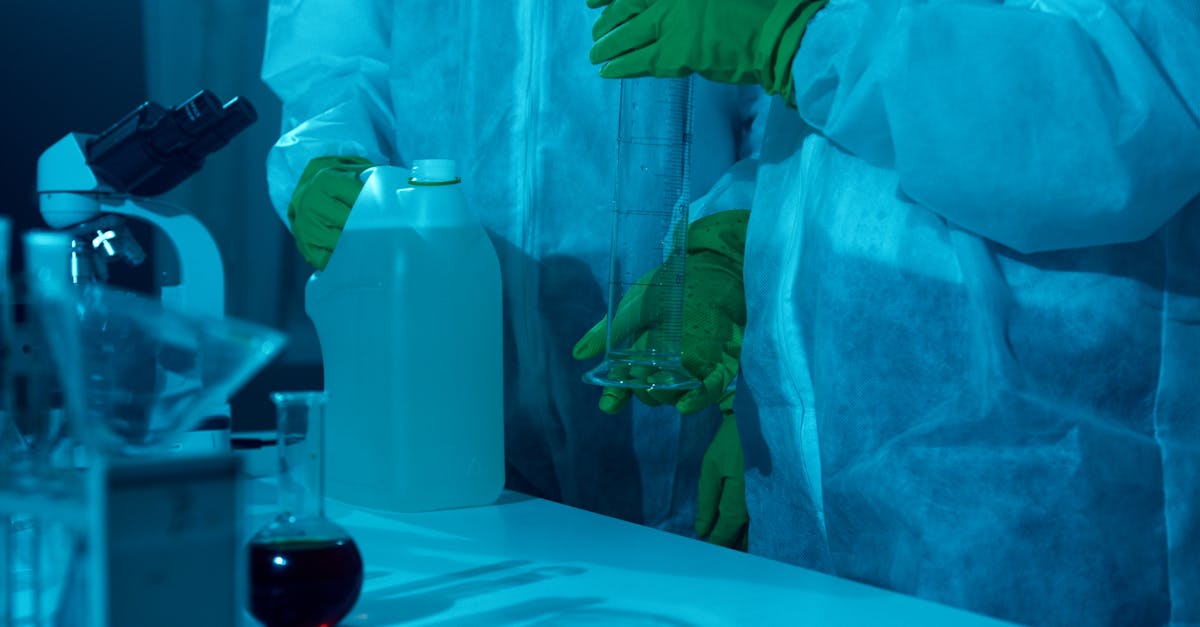
Introduction to GD&T
Geometric Dimensioning and Tolerancing (GD&T) is a symbolic language used in engineering and manufacturing to ensure accurate and consistent communication of design specifications. It establishes a set of guidelines for defining and inspecting the geometric features of components.
The Role of Inspection in GD&T
Inspection plays a critical role in GD&T as it verifies whether components conform to the specified geometric tolerances and other requirements. Traditional inspection methods often involve manual measurements and visual inspections which are time-consuming and prone to human error.
The Rise of Chatbots
With advancements in artificial intelligence and natural language processing, chatbots have emerged as a powerful tool in various industries. Chatbots are computer programs that simulate human conversations and provide automated responses. They can be implemented in messaging platforms, websites, or dedicated applications.
Chatbots for GD&T Inspection
Chatbots can aid in the inspection of components for compliance with GD&T guidelines. By providing the necessary information about the component, such as design drawings and specifications, the chatbot can analyze the geometric features and compare them against the required tolerances.
The chatbot can guide users in performing inspections by asking relevant questions and providing step-by-step instructions. It can assist in identifying critical features, calculating tolerance zones, and evaluating dimensional and geometric deviations. The chatbot can also generate inspection reports and provide recommendations for corrective actions if deviations are found.
Benefits of Chatbot-based Inspection
Implementing chatbots for GD&T inspection offers several benefits:
- Efficiency: Chatbots can quickly analyze and interpret GD&T requirements, reducing the time and effort required for inspections.
- Consistency: Chatbots provide consistent and standardized inspections, eliminating the potential for human errors and variations.
- Accessibility: Chatbots are accessible 24/7 and can be used by multiple users simultaneously, improving the availability of inspection support.
- Knowledge Capture: Chatbot interactions can be logged, capturing valuable information that can be used for analysis, training, and continuous improvement.
Conclusion
Chatbots offer a promising solution for streamlining GD&T inspection processes. By leveraging their capabilities in artificial intelligence and natural language processing, chatbots can enhance efficiency, consistency, and accessibility in inspecting components for compliance with GD&T guidelines. Implementing chatbots can help organizations improve quality control and reduce inspection errors, ultimately leading to enhanced product quality.
Comments:
This article offers great insights into leveraging ChatGPT for Inspection in GD&T Technology. It seems like it could significantly enhance accuracy and efficiency in the inspection process.
I agree, Michael. The application of ChatGPT in GD&T technology can revolutionize the inspection industry by automating certain aspects. It would be interesting to see how this technology evolves.
I'm curious about the potential limitations of using ChatGPT for inspection. While it can improve efficiency, is there any risk of errors or misinterpretations in complex GD&T applications?
That's a valid concern, David. While ChatGPT has shown impressive capabilities, it's essential to carefully validate its performance in complex scenarios to avoid potential risks.
Thank you all for your comments. I understand the potential concerns related to accuracy. In our testing, ChatGPT has generally performed well in GD&T applications, but it's crucial to have human oversight to catch any errors or misinterpretations.
I can see the benefits of leveraging ChatGPT for inspection tasks. The time saved by automating certain processes can be utilized in more complex analysis or decision-making, ultimately improving productivity.
Absolutely, Oliver. ChatGPT can handle repetitive and time-consuming inspection tasks, allowing experts to focus on more critical aspects. It could be a valuable tool in the industry.
One concern that comes to mind is the potential for bias. How can we ensure that ChatGPT doesn't introduce any biases, particularly in GD&T inspections that require objective evaluations?
Excellent point, Sarah. Bias mitigation is a critical consideration when using AI models. We need to train and evaluate the model on diverse datasets and continuously monitor its performance to ensure unbiased outcomes.
Aditi, regarding bias mitigation, should companies implementing ChatGPT for inspections have guidelines or policies in place to double-check the model's decisions? Human intervention could help identify any potential biases.
Certainly, Michael. Having established guidelines or policies for human intervention can be an effective way to ensure the model's decisions align with the company's standards. It provides an additional layer of assurance and reduces the risk of biases.
I'm impressed by the potential cost reductions that leveraging ChatGPT for inspection can offer. By automating certain tasks, it can save both time and resources, benefiting companies across different sectors.
Absolutely, Samantha. The financial advantages of implementing ChatGPT in inspection processes are substantial. However, we should ensure careful cost-benefit analysis to identify the areas where automation would bring the most ROI.
I wonder how easily ChatGPT can adapt to specific GD&T standards. Each company may have slightly different requirements, and flexibility is crucial in the implementation process.
Good question, Anna. ChatGPT can be fine-tuned on specific data to align with different GD&T standards. Customization plays a vital role, and companies can work closely with developers to adapt the model effectively.
That's an important point, Anna. While ChatGPT has shown versatility, it would be interesting to know more about its adaptability to different GD&T standards and how customization can be achieved.
I'm curious to know if there are any real-world case studies or success stories where ChatGPT has been implemented in GD&T inspection processes. It would be helpful to learn from practical examples.
I agree, John. Real-world case studies can provide valuable insights into the implementation of ChatGPT in GD&T inspections, including its benefits, challenges, and lessons learned.
There are indeed several real-world case studies where ChatGPT has been successfully utilized in GD&T inspections. I will share some relevant examples in a follow-up article to provide practical insights into its implementation.
I look forward to reading the follow-up article, Aditi. Hearing about real-world experiences helps us understand the potential impact of ChatGPT in GD&T inspection processes better.
ChatGPT's ability to leverage natural language processing technology opens up several possibilities in GD&T inspections. It can enhance communication, improve analysis, and empower stakeholders to make informed decisions.
Very true, Oliver. The potential applications of ChatGPT in GD&T inspections go beyond just accuracy and efficiency. It can foster collaboration, standardize interpretations, and drive overall improvement in the industry.
I'm interested in the potential challenges during the initial deployment of ChatGPT for inspection. Are there any implementation complexities, training requirements, or data limitations to consider?
That's an important aspect, Sarah. Planning the initial deployment of ChatGPT requires careful consideration of infrastructure, data availability, and training requirements to ensure a smooth integration into existing inspection processes.
I assume there would be a learning curve for inspectors and experts when incorporating ChatGPT into their workflows. Training and familiarization sessions would be necessary for optimal adoption.
You're right, David. Training and familiarization sessions for inspectors and experts are crucial to ensure a smooth onboarding process. Providing clear guidance and sufficient support can help them adapt to the technology effectively.
Security is an important concern when implementing AI models like ChatGPT. How can we ensure the protection of sensitive data during inspections?
Security is definitely a critical aspect, Anna. Companies should establish robust data security protocols, including data encryption, access controls, and regular audits to ensure the confidentiality and integrity of sensitive information during inspections.
In addition to security, data privacy is also a significant consideration. Striking the right balance between leveraging data for accurate inspection and protecting individuals' privacy is essential.
Absolutely, Clara. Companies must follow relevant data protection guidelines, such as anonymization practices and obtaining consent when necessary, to maintain a responsible approach toward data privacy while leveraging AI models like ChatGPT.
Considering the substantial benefits offered by ChatGPT in GD&T inspections, it's crucial to have a robust feedback loop for continuous improvement. Learning from user experiences and incorporating enhancements will be valuable.
I completely agree, Samantha. Continuous improvement based on user feedback and actively involving domain experts will ensure that ChatGPT evolves to meet the specific needs of the GD&T inspection industry effectively.
One aspect worth exploring is how ChatGPT can assist in quality management during inspections. It could potentially analyze patterns, trends, and anomalies to help identify areas for process optimization.
That's an interesting perspective, Oliver. ChatGPT's ability to analyze large volumes of data and detect patterns can certainly aid in quality management, leading to improved inspection outcomes and overall process optimization.
I'm impressed by the potential scalability of ChatGPT in GD&T inspections. As the technology evolves and more data becomes available, it could handle increasingly complex inspection tasks, further improving accuracy and efficiency.
Indeed, Rachel. With advancements in AI and access to comprehensive datasets, ChatGPT's scalability in the GD&T inspection realm is promising. It opens up avenues for even more accurate and efficient inspection processes.
Are there any ethical considerations to keep in mind while using ChatGPT in GD&T inspections? AI models have shown potential biases and unintended consequences in various domains.
Ethical considerations are crucial, Anna. Transparency, fairness, and accountability should be central in the development and deployment of ChatGPT to mitigate biases and ensure unbiased, ethical inspections.
Providing explainable AI capabilities alongside ChatGPT for inspections could also address ethical concerns. The ability to understand and explain the model's decision-making process can build trust among users.
You're right, Clara. Explainability is crucial to build trust and understand how the model reaches its conclusions. Efforts in research and development are ongoing to enhance the explainability of AI models like ChatGPT.
Overall, leveraging ChatGPT for inspection in GD&T technology seems to be a promising direction. Balancing automation, human expertise, and addressing potential challenges will be key to successful implementation.
I agree, Oliver. ChatGPT has the potential to significantly improve accuracy and efficiency in GD&T inspections. However, close collaboration between developers, inspectors, and domain experts will be crucial throughout the implementation and evolution process.
Thank you all for this insightful discussion. It has given me a better understanding of how ChatGPT can be leveraged in GD&T inspections. I look forward to further advancements in this field.
Thank you, Sarah. I'm glad this discussion provided valuable insights. As the field progresses, there will undoubtedly be exciting developments in leveraging ChatGPT for GD&T inspections.