Boosting Efficiency and Collaboration in Manufacturing Operations: Leveraging ChatGPT for Workforce Management
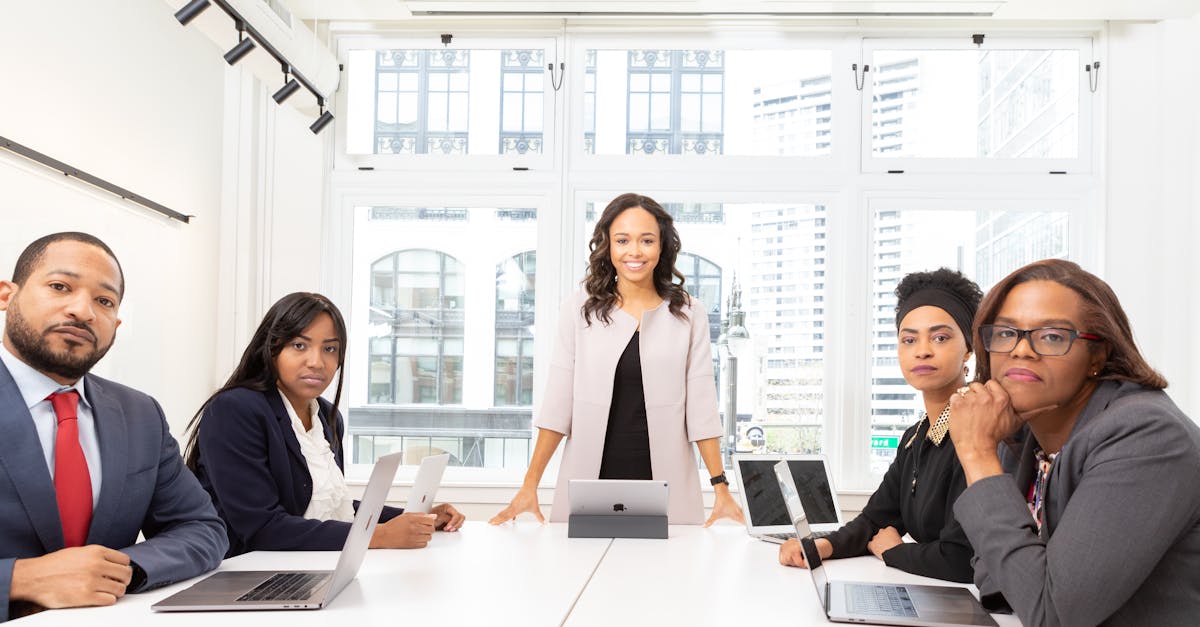
In the realm of manufacturing operations, the efficient management of the workforce is crucial for achieving production goals and maintaining optimal productivity levels. Workforce management technology plays a significant role in streamlining this process by providing predictive analytics and recommendations for workforce deployment. By utilizing this technology, manufacturers can ensure that they have the right number of skilled employees in the right place at the right time, ultimately enhancing overall operational efficiency.
Understanding Workforce Management Technology
Workforce management technology is a comprehensive system that combines various tools, applications, and processes designed to optimize the allocation of human resources in a manufacturing environment. It enables manufacturers to accurately forecast their staffing needs, aligning them with production objectives. This technology takes into account factors such as demand fluctuations, production volumes, and employee skill sets to generate data-driven insights for effective decision-making.
Predictive Staffing
One of the key benefits of workforce management technology in manufacturing operations is its ability to predict staffing requirements. By analyzing historical data and considering current production goals, the software can forecast the number of employees needed for each shift or workday. It takes into account factors such as product demand, production cycle time, and the desired rate of output. This predictive capability allows manufacturers to proactively plan their workforce deployment, ensuring they have the right number of workers to meet production targets efficiently.
Optimized Workforce Deployment
Workforce management technology goes beyond just predicting staffing needs; it also provides recommendations for workforce deployment based on the analysis of various factors. It takes into account employee skill sets, availability, and preferences, along with production requirements and desired outcomes. By considering these variables, the software can suggest the most appropriate employee assignments, shift schedules, and resource allocation strategies. As a result, manufacturers can optimize their workforce deployment, ensuring that the right employees with the right skills are assigned to appropriate tasks and shifts.
Benefits and Impact on Manufacturing Operations
Implementing workforce management technology in manufacturing operations offers several benefits. Firstly, it helps in reducing labor costs by eliminating overtime, minimizing redundancies, and ensuring optimal staffing levels. Secondly, it enhances productivity by eliminating gaps and bottlenecks in the workforce, thus allowing for better production planning and resource allocation. Thirdly, it improves employee satisfaction by considering their preferences and skill sets when making assignments, leading to increased engagement and motivation. Furthermore, workforce management technology also improves accuracy in time and attendance tracking, allowing manufacturers to gain better insights into employee productivity and performance. It also facilitates schedule adherence, ensuring that employees show up on time, reducing any disruptions in the production process. In conclusion, the implementation of workforce management technology in manufacturing operations enables accurate prediction of staffing needs and provides recommendations for optimal workforce deployment. The software's forecasting capabilities and data-driven insights enhance overall operational efficiency, reducing labor costs, improving productivity, and increasing employee satisfaction. By leveraging this technology, manufacturers can successfully achieve their production goals and maximize their manufacturing operations' effectiveness.
Comments:
This article on leveraging ChatGPT for workforce management is fascinating! It's incredible to see how AI technology is transforming industries like manufacturing. I'm eager to learn more about the specific benefits and challenges of implementing ChatGPT in manufacturing operations.
Thank you all for your comments and questions! I'm thrilled to see your interest in leveraging ChatGPT for workforce management in manufacturing. David, to answer your question, some specific benefits of implementing ChatGPT include improved workforce productivity, streamlined information retrieval, and reduced training time for new employees.
Ann, it's reassuring to know that biases are taken seriously during the implementation of ChatGPT. Ensuring fairness and inclusivity should always be a priority when deploying AI technologies.
Thank you, David. I couldn't agree more. Responsible AI deployment requires continuous efforts to identify and address any biases that may arise. By doing so, we can ensure that AI can be a force for good in the manufacturing industry.
Absolutely, Ann. Embracing AI technologies like ChatGPT while maintaining a human-centric approach will lead to the most successful outcomes.
I agree, David. AI-powered workforce management seems to have great potential. I wonder if anyone here has experience with implementing ChatGPT in a manufacturing setting?
I've actually had some experience using ChatGPT in manufacturing operations. It can definitely boost efficiency and collaboration. However, the initial training and customization process can be time-consuming and requires a good understanding of the specific workflows and terminology in the industry.
I'm curious, Robert. What were some of the specific benefits you observed after implementing ChatGPT in a manufacturing setting?
Good question, Sarah. One of the main benefits was improved communication and knowledge sharing among the workforce. ChatGPT acted as a virtual assistant, providing instant answers to questions, troubleshooting guidance, and suggesting best practices. It significantly sped up decision-making processes and reduced the time spent on manual research.
As impressive as ChatGPT sounds, I'm curious about its limitations. Are there any downsides or challenges that you encountered while implementing it, Robert?
Great question, Jonathan. One of the challenges we faced was the need for continuous monitoring and fine-tuning of ChatGPT's responses. Sometimes it would provide inaccurate or inadequate information, especially when faced with complex or uncommon scenarios. It's crucial to have human oversight in place to ensure the accuracy and quality of the AI-generated responses.
I completely agree with the need for human oversight, Robert. AI should assist and enhance human capabilities, not replace them entirely. Did you encounter any resistance or skepticism from the workforce during the implementation?
Absolutely, Emma. Some employees initially expressed concerns about job security and the AI potentially replacing their roles. Communication and transparency were key to address these concerns, emphasizing that ChatGPT serves as a helpful tool rather than a replacement. We provided training sessions to help employees understand how it can enhance their work and save time.
Thanks for sharing, Robert. It's essential to strike a balance between relying on AI and maintaining human involvement to ensure accurate and context-aware responses.
Jonathan, based on my experience, ChatGPT has the potential to significantly enhance both efficiency and collaboration in manufacturing operations. It can provide real-time guidance, answer frequently asked questions, and assist with complex problem-solving.
Emma, ChatGPT seems to have diverse applications in manufacturing. Are there any specific use cases where it stood out in facilitating collaboration across departments?
Michael, one notable use case was during product design and development. ChatGPT enabled seamless collaboration between design, engineering, and quality assurance teams. It offered instant access to design specifications, material information, and troubleshooting tips. This led to faster iterations, reduced errors, and overall improved product development cycles.
That's fantastic, Emma. It's impressive how ChatGPT can facilitate cross-functional collaboration and enhance the overall efficiency of product development processes.
Indeed, Michael. It's exciting to see how AI technologies become integral parts of our day-to-day work, transforming traditional workflows and fostering innovation.
Emma, I agree with your observation. ChatGPT's ability to support complex problem-solving can be a game-changer in manufacturing. It opens up opportunities for employees to work on more critical and strategic tasks.
Absolutely, Sarah. By delegating repetitive and time-consuming tasks to AI-powered assistants, employees can focus on high-value activities that require human ingenuity and decision-making.
That's impressive, Robert. It sounds like ChatGPT can truly revolutionize workforce management in the manufacturing industry. Thank you for sharing your firsthand experience.
Thank you, Sarah. It's reassuring to know that companies prioritize data protection while implementing AI solutions like ChatGPT. This can help build trust between employees and the technology.
Robert, your insights into the challenges and benefits of ChatGPT implementation are valuable. It's crucial to assess these factors before adopting AI solutions to ensure successful integration into manufacturing operations.
You're absolutely right, Christine. A thorough evaluation of the benefits, challenges, and readiness of the organization is key to successful implementation and realizing the full potential of ChatGPT.
I'm intrigued by the potential of ChatGPT in manufacturing, but I have concerns about data privacy and security. How can companies ensure that sensitive information remains protected?
Excellent point, Chris. Data privacy and security are crucial. During our implementation, we ensured that sensitive company data was encrypted and stored securely. Strict access controls and regular audits were implemented to minimize the risk of unauthorized access.
I'm concerned about the potential biases in AI-generated responses. With ChatGPT being trained on large datasets, how can we ensure that it doesn't adopt or reinforce any existing biases in manufacturing operations?
Michael, addressing biases is indeed crucial. During the implementation, we invested significant effort in training ChatGPT on diverse datasets and testing it extensively to identify potential biases. Ongoing monitoring and feedback from the workforce help us continually improve the system and ensure unbiased and fair responses.
That's reassuring, Ann. It's vital to have mechanisms in place to prevent biased or discriminatory information from being propagated. Transparency and accountability are key.
Absolutely, Michael. Transparency and accountability are the foundation for responsible AI deployment. We take concerns about biases seriously and continually work to make the system more reliable and fair.
That's great to hear, Ann. It's important to have a proactive approach in addressing biases and ensuring that AI technologies act as unbiased allies.
I see a lot of potential for ChatGPT in enhancing collaboration between different departments within a manufacturing company. Has anyone here experienced improved inter-departmental communication with ChatGPT?
Christine, in our company, ChatGPT has been instrumental in bridging the communication gap between departments. It has facilitated quick access to information and enabled collaborative problem-solving. It's definitely boosted our cross-functional collaboration.
I couldn't agree more, Emma. ChatGPT can break down silos and create a more integrated and streamlined manufacturing operation. The benefits it brings to interdepartmental communication are remarkable.
Indeed, Sarah. It's exciting to witness how AI technologies like ChatGPT can transform the way we work and collaborate across different functions.
Addressing biases and ensuring transparency also helps build trust among employees, ensuring they feel comfortable using AI-powered solutions like ChatGPT.
Well said, Jonathan. Establishing trust with employees is essential to foster a positive and productive AI-assisted work environment.
Striking that balance between AI assistance and human expertise is crucial, especially in manufacturing where precision and accuracy are paramount.
Thank you all for engaging in this enlightening discussion. It's clear that leveraging ChatGPT in manufacturing operations can bring significant benefits, but it requires careful consideration of its implementation, potential limitations, and the need for human oversight. Let's embrace AI responsibly to maximize its potential!