Boosting Efficiency and Streamlining Processes: Leveraging ChatGPT in Manufacturing Operations for Process Improvement
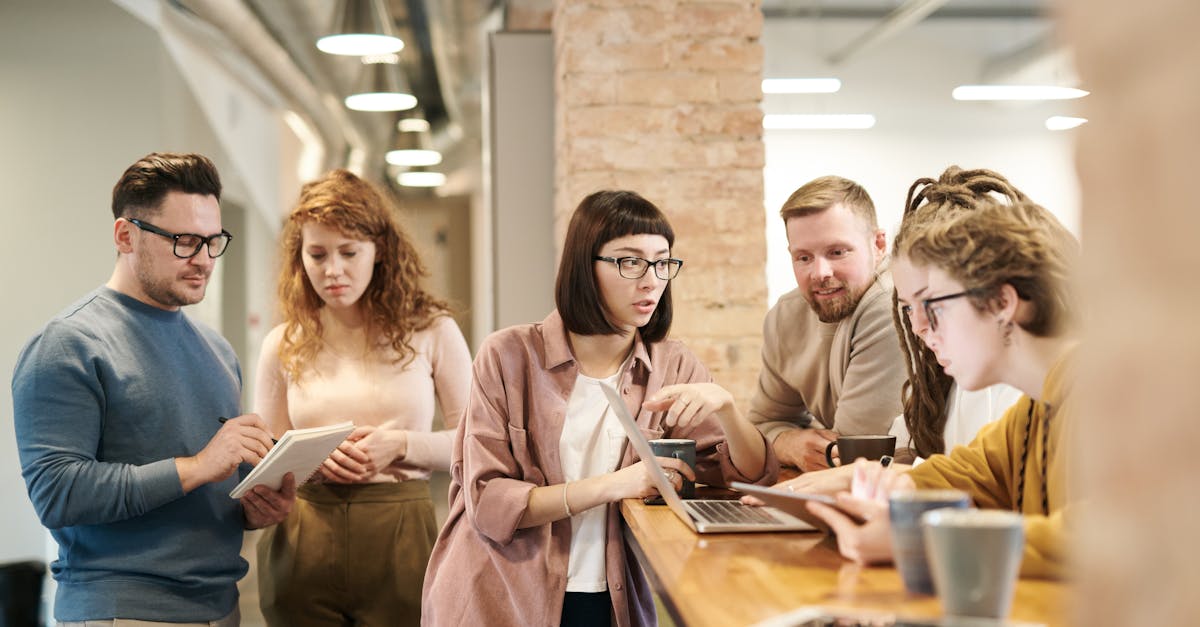
In the manufacturing industry, process improvement plays a crucial role in ensuring efficient operations and maximizing productivity. As technology continues to evolve, businesses are constantly exploring innovative ways to optimize their manufacturing processes. One such technology that is making significant strides in process improvement is the use of advanced models that can identify bottlenecks and recommend improvements.
Introduction to the Model
The model used for process improvement in manufacturing operations is a sophisticated algorithm that analyzes data from various stages of the production line. It takes into account factors such as production time, inventory levels, resource utilization, and quality control to identify areas that are causing delays or inefficiencies in the process.
Identifying Bottlenecks
Bottlenecks are the stages or processes in the manufacturing line that slow down the overall production. These bottlenecks can be caused by various factors, including limited resources, equipment breakdowns, or inefficient work methods. The model analyzes the data collected from sensors and other sources to pinpoint the exact location and cause of these bottlenecks.
By identifying bottlenecks, manufacturers can focus their efforts on improving those specific areas to increase overall productivity. It allows them to prioritize their resources and make informed decisions about process optimization strategies.
Recommendations for Improvement
Once the bottlenecks are identified, the model generates recommendations for process improvement. These recommendations can range from small adjustments to major changes in the manufacturing workflow. For example, the model might suggest reallocating resources to the bottleneck area, implementing preventive maintenance to reduce equipment breakdowns, or redesigning the production layout.
Additionally, the model can also predict the potential impact of implementing these recommendations. It provides manufacturers with valuable insights into the benefits and risks associated with each improvement strategy, allowing them to make informed decisions about which changes to prioritize.
Benefits of the Model
The use of advanced models for process improvement in manufacturing operations offers several benefits:
- Increased Efficiency: By identifying bottlenecks and recommending improvements, the model helps manufacturers streamline their processes, leading to increased productivity and reduced production time.
- Cost Savings: Process improvements result in cost savings through reduced downtime, optimized resource utilization, and minimized waste.
- Quality Enhancement: By addressing bottlenecks and inefficiencies, manufacturers can improve the overall quality and consistency of their products, leading to increased customer satisfaction.
- Competitive Advantage: Implementing process improvements can give manufacturers a competitive edge by allowing them to deliver products faster, at lower costs, and with improved quality.
Conclusion
The use of advanced models for process improvement in manufacturing operations has revolutionized the way businesses optimize their production processes. By accurately identifying bottlenecks and providing actionable recommendations, these models help drive efficiency, cost savings, and improved product quality. As technology continues to evolve, we can expect further advancements in this area, allowing manufacturers to stay ahead of the competition and deliver exceptional products to the market.
Comments:
Great article, Ann! ChatGPT seems like a powerful tool for improving manufacturing operations. Have any companies started implementing it yet?
Thank you, David! Yes, several companies have already started implementing ChatGPT in their manufacturing operations. It has shown promising results in terms of boosting efficiency and streamlining processes.
I find the idea of leveraging AI in manufacturing fascinating. How does ChatGPT specifically help improve process efficiency?
Good question, Lisa! ChatGPT can assist in various ways. It can provide real-time guidance to workers, help identify bottlenecks, suggest process improvements, and even troubleshoot issues. Its ability to understand context and generate detailed responses makes it an invaluable tool.
I can see how ChatGPT can enhance communication and collaboration on the production floor. Instead of waiting for supervisors or engineers, workers can quickly get support and guidance from the AI system.
Absolutely, Emma! Reduced downtime and quicker problem-solving contribute to overall process efficiency. Workers can focus on their tasks without unnecessary delays.
While ChatGPT can be a useful tool, are there any potential drawbacks to relying too heavily on AI in manufacturing?
That's an important point, Brian. While AI like ChatGPT can enhance efficiency, it's crucial to maintain a balance. Over-reliance on AI without human oversight can lead to dependency issues and potential risks if the system encounters unexpected scenarios.
I agree with Brian. It's essential to consider the impact on the workforce. Will ChatGPT replace human workers or just supplement their capabilities?
Great concern, Oliver. ChatGPT is designed to supplement human capabilities, not replace them. It can handle repetitive or mundane tasks, provide guidance, and free up workers' time for more critical thinking and complex tasks.
I think it's important to involve workers in the adoption of ChatGPT. Their input and feedback will ensure that the system aligns with their needs and improves their work experience.
Well said, Sophia. Workers' involvement is crucial from the early stages to address any concerns, train the AI system more effectively, and leverage their expertise in improving manufacturing processes.
What potential challenges might companies face when implementing ChatGPT in their manufacturing operations?
Good question, Karen. One challenge can be the initial training period to adapt ChatGPT to specific manufacturing contexts. Also, ensuring data security and privacy, addressing potential biases, and handling system failures are important considerations during implementation.
I can imagine the need to integrate ChatGPT with existing manufacturing systems and workflows seamlessly. Compatibility and integration challenges should be addressed for smooth operations.
Exactly, Michael. Integration with existing systems and processes is vital. Companies should ensure ChatGPT becomes an integral part of the workflow, enhancing operations without causing disruptions or inefficiencies.
Are there any specific industries where ChatGPT can provide significant benefits in manufacturing operations?
Certainly, Emily! ChatGPT has potential applications in various industries, including automotive, electronics, pharmaceuticals, and consumer goods. Any sector where process optimization, quality control, and efficiency are crucial can benefit from leveraging ChatGPT.
I wonder if smaller manufacturing companies can also implement ChatGPT effectively, considering their limited resources compared to larger enterprises.
Great point, Robert. While smaller companies may have limited resources, they can still reap the benefits of ChatGPT by starting with targeted implementations. Focusing on specific areas or processes where AI can have the greatest impact and gradually expanding from there can be a feasible approach.
Has there been any research on cost-effectiveness when implementing ChatGPT in manufacturing?
Absolutely, Michelle. Research studies have shown that the benefits of improved process efficiency, reduced downtime, and enhanced decision-making outweigh the costs of implementing ChatGPT. However, companies should conduct their own cost-benefit analysis based on their specific operations.
Can ChatGPT generate insights that would otherwise be missed by human workers?
Indeed, Samuel. ChatGPT's ability to analyze vast amounts of data and provide suggestions based on patterns and correlations can uncover insights that may not be readily apparent to human workers. It acts as a valuable decision-support tool.
Are there any ethical considerations when deploying AI like ChatGPT in manufacturing?
Excellent question, Jennifer. Ethical considerations are crucial. Transparency, accountability, and fairness in AI decision-making, data privacy, and ensuring the system doesn't perpetuate biases are some of the important aspects that should be addressed throughout the implementation.
Companies must ensure that the data used to train ChatGPT is representative and diverse, avoiding biases that may lead to discriminatory outcomes.
Absolutely, Daniel. Diverse and unbiased training data is crucial to ensure fair and inclusive guidance from ChatGPT. Regular monitoring and continuous improvement of the AI system's performance in this regard are important responsibilities.
Are there any limitations or potential risks to consider when implementing ChatGPT in manufacturing operations?
Certainly, Steven. ChatGPT, like any AI system, has limitations. It relies on the training data and might not handle novel scenarios well. There's always a risk of incorrect or misleading guidance if not monitored carefully. Safeguards should be in place, and human oversight is crucial.
Considering the potential risks, what steps can manufacturing companies take to ensure reliable and safe implementation of ChatGPT?
Great question, Laura. Thorough testing and validation of ChatGPT in different manufacturing scenarios is essential. Implementing a feedback loop from workers to continuously improve the system, providing training on AI ethics, and maintaining human judgment as a final decision-making authority are crucial steps.
Could ChatGPT be used for predictive maintenance or identifying potential equipment failures?
Absolutely, William. ChatGPT can analyze sensor data, historical information, and maintenance logs to identify patterns that indicate potential equipment failures. This proactive approach enables timely maintenance and minimizes unexpected downtime.
How do you see the future of AI in manufacturing? Will ChatGPT continue to evolve and play a bigger role?
Great question, Sarah. AI will continue to evolve and play an increasingly significant role in manufacturing. ChatGPT is just the beginning of the potential AI applications. As the technology advances, we can expect more sophisticated AI systems tailored to the manufacturing context, enabling further process improvements and operational excellence.
Ann, do you have any recommendations on how companies can start implementing ChatGPT in their manufacturing operations? Any best practices?
Certainly, David. Firstly, identify specific areas or processes where AI can have the most significant impact. Collaborate extensively with workers, involve them in the early stages to address concerns, and capitalize on their expertise. Pilot projects and gradual scaling allow for learning and refining the implementation strategy.
I assume having a clear implementation plan and proper training for employees are also essential elements for successful integration.
Absolutely, Emma. A clear implementation plan, employee training, and regular communication regarding AI's role and expectations are crucial. Companies should create a culture that embraces AI as a helpful tool rather than a replacement, ensuring successful integration and acceptance.
How can ChatGPT handle multiple languages in a manufacturing environment?
Good question, Kevin. ChatGPT can indeed handle multiple languages. It can be trained on multilingual datasets and fine-tuned to provide responses in different languages based on the requirements of the manufacturing environment and workers' language preferences.
What measures should be taken to ensure the security of sensitive manufacturing data when using ChatGPT?
Data security is critical, Daniel. Manufacturing companies should ensure the AI system operates within secure network environments, regular data backups, encrypted communication channels, role-based access controls, and compliance with relevant data protection regulations. Data should be handled with utmost care to protect sensitive information.
I'm curious about the potential impact on job roles. Will workers need to acquire new skills or adapt to AI-integrated processes?
Good question, Jennifer. With the integration of AI, workers may need to acquire new skills. Upskilling programs that focus on AI literacy, data analysis, and working collaboratively with AI systems can help workers adapt to the AI-integrated processes and continue to contribute effectively.
I think providing opportunities for continuous learning and career development will also help workers embrace AI technologies without feeling threatened.
Exactly, Sophia. Emphasizing lifelong learning, providing career advancement prospects, and involving workers in the evolving AI initiatives foster a positive and collaborative environment, ensuring a smooth transition to AI-integrated processes.
How can companies measure the success and impact of implementing ChatGPT in their manufacturing operations?
Measuring success is vital, William. Key performance indicators (KPIs) related to process efficiency, quality improvement, reduced downtime, and worker satisfaction can be used to evaluate the impact of implementing ChatGPT. Regular data analysis and feedback from workers will provide valuable insights into the system's effectiveness.