Bridging the Gap with ChatGPT: Revolutionizing Technology in the Welding Industry
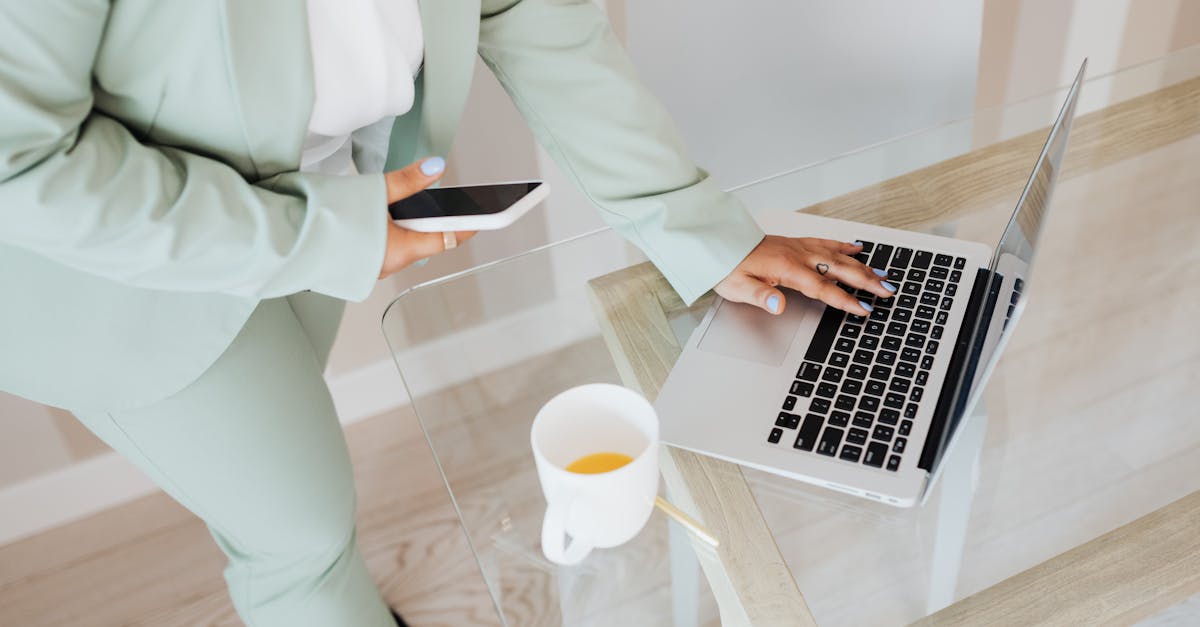
Welding is a crucial process in various industries where two or more materials are joined together to create a solid, continuous bond. Welding procedures need to be carefully developed to ensure the structural integrity and quality of the welded joint. With the advancements in technology, the use of artificial intelligence and machine learning has brought significant improvements to the field of welding. One such technology is ChatGPT-4, an AI-powered assistant that can suggest possible weld procedures based on environmental conditions, materials, and design constraints.
Understanding Weld Procedure Development
Weld procedure development involves determining the optimal parameters for a welding operation, such as the welding process, heat input, pre- and post-weld treatments, and more. It is a complex and time-consuming task that requires expertise and experience. Traditionally, weld procedure development relied on manual evaluation and testing, which could be subjective and time-consuming. However, with the integration of AI technology, the process has become more efficient and accurate.
The Role of ChatGPT-4 in Weld Procedure Development
ChatGPT-4 is a powerful AI assistant that utilizes deep learning techniques to understand and generate meaningful responses in natural language. It has been trained on a vast amount of welding data, including weld parameters, material properties, environmental conditions, and more. By analyzing this data, ChatGPT-4 can provide valuable suggestions for weld procedure development.
1. Environmental Conditions
Environmental conditions play a significant role in welding as they can impact the quality and stability of the weld joint. Factors such as temperature, humidity, and outdoor exposure can affect the welding process. By inputting the specific environmental conditions, ChatGPT-4 can recommend suitable weld procedures that can withstand and adapt to these conditions. This ensures that the final weld joint remains strong and durable.
2. Materials
The choice of materials used in welding greatly affects the weld procedure. Different materials have distinct properties, including melting points, thermal conductivity, and mechanical strength. By providing information about the materials being welded, ChatGPT-4 can suggest appropriate welding techniques and parameters to achieve a high-quality weld. This helps in preventing material failures and ensures the desired joint performance.
3. Design Constraints
Design constraints, such as joint type, joint thickness, and accessibility, can affect the feasibility and efficiency of the weld procedure. ChatGPT-4 can take these constraints into consideration and offer suggestions tailored to the specific design requirements. By optimizing the weld procedure based on the design constraints, ChatGPT-4 helps in saving time, reducing costs, and improving overall productivity.
Benefits of Using ChatGPT-4
Integrating ChatGPT-4 into weld procedure development processes offers several advantages:
- Efficiency: ChatGPT-4 can quickly analyze input data and generate relevant suggestions, saving time and effort compared to manual evaluation.
- Accuracy: With its extensive training and access to a vast amount of welding data, ChatGPT-4 can provide accurate recommendations based on historical performance and industry best practices.
- Consistency: Human operators may have variations in their decision-making process, but ChatGPT-4 offers consistency in generating weld procedure recommendations, ensuring a higher level of quality control.
- Expertise Augmentation: Even experienced welding engineers can benefit from ChatGPT-4's suggestions, as it can provide insights and alternative approaches that may have been overlooked.
Conclusion
As technology continues to progress, AI assistants like ChatGPT-4 are revolutionizing various industries, including welding. By leveraging its deep learning capabilities, ChatGPT-4 can suggest optimized weld procedures based on environmental conditions, materials, and design constraints. This brings increased efficiency, accuracy, and consistency to the weld procedure development process, leading to improved quality and productivity in welding operations.
Comments:
Thank you all for reading my article on ChatGPT in the welding industry. I would love to hear your thoughts and opinions.
Great article, Patricia! I never thought AI could have such an impact in welding. It's amazing how technology keeps evolving.
Thank you, Sarah! It's true, AI opens up a whole new world of possibilities in various industries.
I'm a welder and I'm a bit skeptical about AI taking over our jobs. How can ChatGPT revolutionize the welding industry?
Hi Michael, great question! ChatGPT can assist welders by providing real-time guidance, suggesting optimal welding parameters, and detecting potential defects. It helps in increasing efficiency and reducing errors.
Thanks for clarifying, Patricia. I can see how it can be useful now.
As an engineer, I can see the potential benefits of AI in welding. It can enhance precision and help optimize welding techniques. Exciting stuff!
Although AI can assist, it will never fully replace skilled welders. Experience and craftsmanship are irreplaceable.
Absolutely, Daniel! AI is meant to augment human abilities, not replace them. Skilled welders will always be crucial.
Wow, this is fascinating! I had no idea AI had such applications in welding.
Glad you find it fascinating, Linda! AI is advancing rapidly, and its potential is expanding across various industries.
Is ChatGPT accessible for smaller welding businesses or is it mainly for larger corporations?
Good question, Robert! While implementation costs may vary, ChatGPT can be tailored to suit both larger corporations and smaller welding businesses. It aims to make AI technology accessible to all.
I'm concerned about the security aspect. How can we ensure that the data shared with ChatGPT is protected?
Security is indeed a crucial concern, Sophia. When utilizing ChatGPT, data protection measures must be implemented to safeguard sensitive information. It's important to work with reliable and trustworthy providers.
I can see how AI can enhance productivity in welding, but what about the learning curve for operators to adapt to this technology?
That's a valid concern, Grace. Proper training and support are essential to help operators effectively utilize AI technologies like ChatGPT. Familiarizing them with the system and its benefits can streamline the learning curve.
Are there any limitations to ChatGPT's accuracy in the welding industry? How well does it adapt to different welding techniques?
Good question, Oliver! ChatGPT's accuracy can be influenced by the quality and relevance of training data. It can adapt to different techniques, but continuous improvement is necessary to refine its knowledge and predictions.
AI certainly has the potential to transform the welding industry. I'm excited to see how it develops further.
Indeed, Alexandra! The evolution of AI in welding will likely bring forth innovative advancements, benefitting the industry as a whole.
I'm interested to know if ChatGPT can assist in identifying and troubleshooting welding defects.
Absolutely, William! ChatGPT can help identify potential defects and troubleshoot them by analyzing welding parameters and providing insights into potential causes and solutions.
I can also see potential applications of AI in weld quality inspection. It could greatly improve efficiency and accuracy in that area.
You're right, Emily! AI can play a significant role in weld quality inspection, enabling faster and more precise detection of imperfections.
I'm impressed by the potential of ChatGPT. It seems like a game-changer for the welding industry.
Thank you, Robert! It's wonderful to witness how technology can revolutionize industries, and ChatGPT certainly holds immense potential.
I'm concerned about the job market for human welders if AI takes over major tasks. Will there be enough opportunities left?
Valid concern, Grace. While AI can assist welders, it's unlikely to completely replace them. There will always be a need for skilled human labor in the welding industry.
I agree with Patricia. AI can be a valuable tool, but it won't devalue the importance of skilled welders.
Precisely, Sarah! The integration of AI should be seen as a means of enhancing human capabilities, not eliminating them.
Can ChatGPT handle complex welding projects, or is it more suitable for simpler tasks?
ChatGPT can handle a wide range of welding projects, Linda, from simple to complex. However, for highly specialized tasks, additional customization or integration with other systems may be needed.
I'm curious to know how the implementation of AI in the welding industry has progressed so far. Is it widely adopted?
Good question, Daniel. While AI adoption in welding is still progressing, it's being increasingly recognized as a valuable technology. Larger corporations have been early adopters, but smaller businesses are also starting to explore AI's potential.
Are there any concerns about potential errors or biases in AI systems when used in welding?
Yes, Sophia. Bias and errors can be a concern when using AI systems. It's crucial to validate and constantly improve the performance of such systems, ensuring fairness and accuracy in their predictions.
What kind of data does ChatGPT rely on to provide accurate insights in welding?
ChatGPT relies on a combination of historical welding data, industry standards, and best practices. Continuous collection and analysis of relevant data contribute to its accuracy and insights.
I'm amazed by the advancements in AI and its potential in so many industries. Welding is just one example.
Indeed, Alexandra! The potential for AI is vast, and we're only scratching the surface of its capabilities in various sectors.
Will ChatGPT be able to adapt to future advancements and changes in the welding industry?
Absolutely, William! ChatGPT's flexibility allows it to adapt to emerging technologies and changes in the welding industry, ensuring its continued relevance and usefulness.
Patricia, do you have any real-world examples of ChatGPT being used in welding applications?
Yes, Sarah! One example is a major shipyard that implemented ChatGPT to assist welders in optimizing welding parameters and improving overall efficiency. It resulted in significant time and cost savings.
That shipyard example is impressive, Patricia. It's good to see practical use cases of AI in the welding industry.
Absolutely, Michael! Real-world success stories demonstrate the tangible benefits AI can bring to the welding industry.
Can ChatGPT be integrated with existing welding equipment or software systems?
Yes, Robert! Integration with existing equipment and software is possible. Collaborating with equipment manufacturers or software developers can facilitate seamless integration of ChatGPT into the welding workflow.
It's exciting to see how AI technology is advancing across industries. Welding definitely stands to benefit from it.
Indeed, Emily! AI's potential extends far beyond what we can currently foresee. It's exciting to witness its transformative impact on various sectors.
Are there any limitations or challenges in implementing ChatGPT in the welding industry?
Good question, Daniel. Some challenges include ensuring data accuracy, addressing potential biases, and providing proper training and support to operators. However, with collaboration and continuous improvement, these challenges can be overcome.
What kind of expertise is required to implement and maintain ChatGPT in the welding field?
Implementing and maintaining ChatGPT in the welding field requires a combination of AI expertise and welding domain knowledge. Collaboration between AI specialists and welding experts is crucial for successful deployment.
I appreciate your article, Patricia. It sheds light on the potential synergies between AI and welding.
Thank you, Grace! I'm glad the article resonated with you. The synergies between AI and welding indeed hold exciting prospects for the industry.
Would ChatGPT be able to adapt to different welding standards and regulations across countries?
Absolutely, Oliver! Customization of ChatGPT ensures compliance with different welding standards and regulations, enabling its seamless adoption across countries.
Do you think AI advancements will eventually lead to fully automated welding processes?
While AI can automate certain aspects of welding, fully automated processes might not be feasible or ideal in all scenarios. Skilled human welders will likely continue to play a pivotal role in complex and specialized tasks.
I'm glad to see AI making its way into the welding industry. It has so much potential for growth and improvement.
Absolutely, Linda! The welding industry can greatly benefit from AI's potential, and embracing technology opens up new avenues for growth and improvement.
AI has come a long way in recent years, and its applications in welding are impressive. What do you see as the next big step in this field, Patricia?
Great question, William. The next big step would likely involve further advancements in machine learning algorithms specific to welding, enabling more accurate predictions and improved decision-making capabilities.
What about the potential cost savings with ChatGPT? Would it be financially beneficial for businesses?
Indeed, Emily! ChatGPT can lead to substantial cost savings by reducing errors, optimizing welding parameters, and improving overall efficiency. Implementing AI can be financially beneficial in the long run.
I'm curious about the level of accuracy ChatGPT can achieve when suggesting welding parameters. Are there any statistics available?
Accurate parameter suggestions by ChatGPT can vary depending on the specific use case and quality of input data. It's important to test and fine-tune the system in each unique application to achieve optimal results.
Patricia, could you briefly explain how the training process for ChatGPT in welding works?
Sure, Sophia! Training ChatGPT involves feeding it with a large dataset of welding information, including parameters, defect examples, and best practices. The model learns to generate relevant responses and insights based on this training data.
I wonder if there are any ethical considerations when implementing AI in the welding industry.
Ethical considerations are indeed important. Transparency, fairness, and accountability must be prioritized when developing and implementing AI systems in the welding industry. Responsible AI practices should be followed.
What would you say are the major advantages of using ChatGPT in welding compared to traditional methods?
Great question, Oliver! ChatGPT brings real-time guidance, increased efficiency, error reduction, and the ability to analyze vast amounts of data quickly. It complements traditional methods, enhancing accuracy and decision-making.
Are there any potential risks associated with dependence on AI systems like ChatGPT in the welding industry?
While AI systems like ChatGPT can enhance productivity, overreliance without proper monitoring and human oversight could have potential risks. It's essential to strike the right balance between AI assistance and human expertise.
How can the welding industry prepare itself to adopt AI technologies effectively?
To effectively adopt AI technologies, the welding industry should prioritize AI education and upskilling programs for its workforce. Collaboration between AI experts and welding professionals is crucial to navigating the transition smoothly.
Do you foresee potential regulatory challenges in adopting AI in the welding industry?
Regulatory challenges can arise, Emily, as AI technologies continue to evolve. Collaborative efforts between industry stakeholders, regulators, and researchers are important to establish guidelines and ensure the responsible adoption of AI in the welding industry.
I appreciate your insights, Patricia. It's exciting to see how AI is transforming our world in myriad ways.
Thank you, Robert! The potential of AI is indeed awe-inspiring, and it's amazing to witness its transformational impact across industries.
I'm grateful for the opportunity to learn more about AI in welding. Thank you, Patricia, for sharing your knowledge.
You're most welcome, Grace! I'm glad I could provide valuable insights. Feel free to reach out if you have any further questions.
Indeed, thank you, Patricia! Your article has sparked my interest in the potential of AI in the welding field.
It's my pleasure, Oliver! I'm delighted that the article has sparked your interest. AI's potential in the welding field is truly exciting!
Thank you, Patricia, for sharing your expertise. AI's role in the welding industry is definitely intriguing.
You're welcome, William! I'm glad I could share my knowledge and insights on AI's role in the welding industry with all of you.
Thank you, Patricia. The potential applications of AI in welding are fascinating and have broad implications.
Absolutely, Sophia! The potential applications of AI in welding go far beyond what we can currently envision, opening up exciting possibilities.
Thank you, Patricia, for answering our questions. Your expertise on this subject is greatly appreciated.
You're all very welcome, Sarah! I'm glad I could provide valuable insights into the fascinating realm of AI in the welding industry.
Thank you, Patricia, for an engaging discussion. AI's potential in welding is quite exciting.
Thank you, Daniel! I'm thrilled that you found the discussion engaging. AI's potential in welding continues to cultivate excitement and promise.
Thank you, Patricia, for sharing your expertise and insights on the transformative potential of AI in the welding industry.
You're very welcome, Emily! It was my pleasure to share my expertise and insights with all of you. The transformative potential of AI in the welding industry is truly remarkable.
That's interesting, Patricia! So ChatGPT acts as a real-time welding advisor, providing guidance to welders based on the requirements of the task at hand?
That's fascinating, Patricia! How scalable is ChatGPT for different welding environments and processes?
Thank you, Patricia, for your time and valuable responses. AI's impact on the welding industry is something to look forward to.
You're welcome, Robert! I'm glad I could provide valuable responses. AI's impact on the welding industry is indeed something to be excited about.
Thank you all once again for your active participation in this discussion. Your insights and questions have made this conversation engaging and thought-provoking. Feel free to reach out for any further discussions or clarifications. Have a great day!
Thank you all for reading my article on ChatGPT in the welding industry! I'm excited to hear your thoughts and engage in a discussion.
I wonder how ChatGPT can assist in quality control during welding processes. Any thoughts on that, Patricia?
Lisa, ChatGPT can assist in quality control by analyzing data from various sensors and providing real-time feedback on welding parameters. It can detect deviations and suggest adjustments to ensure high-quality welds.
So, Patricia, could ChatGPT potentially replace the need for welding experts and inspectors in the long run, or is it more of a support tool?
Lisa, ChatGPT is more of a support tool, complementing human expertise rather than replacing it. It can assist in decision-making, provide valuable insights, and enhance efficiency, but the knowledge and experience of human welders remain essential in achieving optimal results.
Thank you for clarifying, Patricia! It's reassuring to know that ChatGPT is designed as a tool to enhance human expertise and not replace it.
Great article, Patricia! I never thought AI could play a role in welding. It'll be interesting to see how it revolutionizes the industry.
I agree, Michael! The potential applications in the welding industry are fascinating. AI has been transforming various sectors, and it's exciting to see it entering the manufacturing field.
Patricia, excellent article! The advancements in AI-powered automation in welding can greatly contribute to increased efficiency and precision. Can you provide some examples of specific tasks where ChatGPT can be helpful?
David, ChatGPT can be helpful in several tasks. It can assist in creating optimized welding sequences, generating welding parameters based on material properties, and providing troubleshooting guidance to welders.
That's impressive, Patricia! ChatGPT seems to enhance a welder's capabilities by providing them with real-time expertise. It could be a valuable tool for both novice and experienced welders alike.
I work in the welding industry, and I'm excited to learn more about ChatGPT. Patricia, do you have any details on the compatibility of this technology with existing welding equipment?
Sophia, ChatGPT can be compatible with existing welding equipment. It can integrate with the control systems and provide recommendations for optimizing welding parameters, ensuring seamless integration into the workflow.
Reducing costs and improving efficiency sounds promising, Patricia! How long do you think it will take for ChatGPT to become widely adopted in the welding industry?
Sophia, the speed of widespread adoption depends on various factors, including research advancements, industry interest, regulatory considerations, and the evolution of AI technologies. However, as more success stories emerge, adoption is likely to accelerate.
I'm curious about the safety aspect. Can ChatGPT help identify potential hazards or improve worker safety in the welding industry?
That's an excellent question, Oliver! AI technologies like ChatGPT can help identify potential safety hazards, like improper ventilation, inadequate protective gear, or even detect anomalies in welding operations that could lead to accidents or equipment failure.
This technology sounds promising! Will ChatGPT be accessible to small businesses in the welding industry, or will it mostly benefit larger companies with advanced equipment?
Grace, ChatGPT can benefit both small businesses and larger companies. Once the technology matures, there will be options for varying levels of implementation, allowing businesses of all sizes to leverage its advantages.
I'm intrigued by the potential cost savings. Can utilizing ChatGPT in welding processes lead to reduced material wastage and overall project costs?
Bryan, yes, ChatGPT can help reduce material wastage by optimizing welding parameters, ensuring the right amount of material is used without compromising strength or quality. This can lead to substantial cost savings.
This could be a game-changer! Are there any potential limitations or challenges in implementing ChatGPT in the welding industry that we should be aware of?
Mark, while ChatGPT holds great potential, there are indeed challenges in implementing it. Ensuring robustness, accuracy, and training the model with a diverse range of welding scenarios are a few areas that require careful consideration.
I'm curious about the learning process behind ChatGPT. How is it trained to provide accurate recommendations and advice in welding scenarios?
Eric, ChatGPT is trained on a large dataset of welding processes and welding experts' knowledge. By utilizing machine learning techniques, it learns patterns and can generate accurate recommendations based on the input it receives.
Thanks for explaining, Patricia! It's impressive to see how machine learning techniques can be applied to such specialized fields.
I'm concerned about the potential job losses due to the integration of AI in the welding industry. Can ChatGPT lead to fewer job opportunities for human welders?
Olivia, while AI integration might change the nature of some tasks, it can also create new opportunities. ChatGPT can enhance human welders' capabilities, leading to improved productivity, innovative applications, and the need for skilled workers to work alongside the technology.
Patricia, are there any privacy concerns regarding the use of ChatGPT in the welding industry? How is data protection addressed?
Maxwell, data protection and privacy are crucial considerations. Companies developing AI technologies like ChatGPT must have robust data security and privacy measures in place. Anonymizing and encrypting data, complying with privacy regulations, and establishing secure data storage are some of the steps taken to address these concerns.
The potential of AI in the welding industry is immense. Patricia, do you foresee any other areas besides quality control and process optimization where ChatGPT could contribute?
Victor, besides quality control and process optimization, ChatGPT can contribute to welding training and education, assisting in knowledge transfer and providing guidance to trainees. It can also aid in documentation and record-keeping of welding procedures.
The potential for error reduction in welding processes with AI assistance is intriguing. Patricia, have there been any successful case studies or real-world implementations of ChatGPT in the welding industry so far?
Liam, there have been successful case studies where ChatGPT has been utilized in welding processes to improve efficiency, reduce defects, and optimize parameters. Real-world implementations demonstrate the potential of this technology in enhancing productivity and quality.
I'm curious about the training process for ChatGPT. How is the AI model exposed to the vast knowledge and expertise of the welding industry?
Emma, the training process involves exposing the AI model to extensive datasets of welding processes, including parameters, materials, and expert knowledge. It also incorporates feedback loops to refine and improve the model over time.
With the rise of AI in welding, do you think welders will need to acquire additional skills or knowledge to adapt to this changing landscape, Patricia?
William, like with any technological advancement, adapting to change is essential. Welders can benefit from upskilling and familiarizing themselves with AI-assisted welding technologies. Acquiring knowledge in AI and data analysis can help them leverage the capabilities of ChatGPT and work collaboratively with this tool.