ChatGPT: Empowering Continuous Improvement with Lean Tools Technology
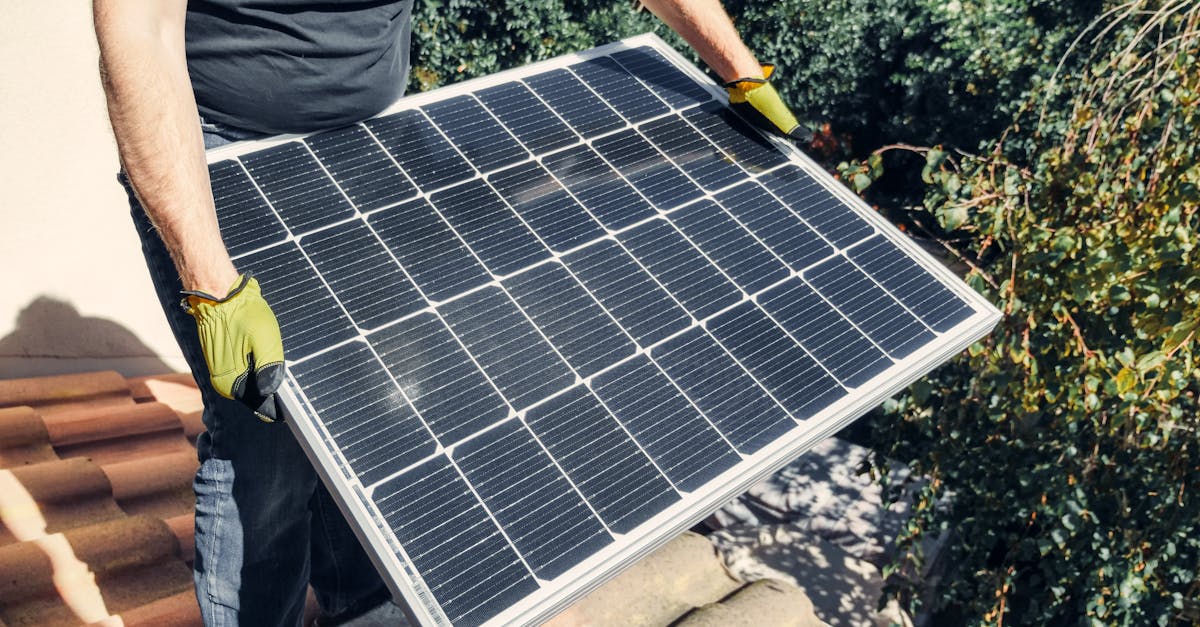
Continuous improvement is a crucial aspect of any successful business. It involves identifying areas for improvement and implementing changes to streamline processes, enhance productivity, and boost overall performance. Lean tools are widely used in various industries to support continuous improvement efforts. These tools provide organizations with the means to analyze data, identify areas of waste, and implement effective solutions.
Lean tools are based on the principles of Lean Manufacturing, a systematic method aimed at eliminating waste and reducing variation in processes. These tools can be applied to any business process, regardless of the industry or sector. They provide a framework for data analysis, problem-solving, and continuous improvement.
Benefits of Lean Tools for Continuous Improvement
- Data Analysis: Lean tools enable organizations to collect and analyze data on various aspects of their operations. This data-driven approach helps identify areas of inefficiency, bottlenecks, and waste. By analyzing data, organizations can make informed decisions and prioritize improvement efforts.
- Identifying Waste: Lean tools help identify different forms of waste, such as overproduction, defects, waiting time, unnecessary inventory, and motion waste. By eliminating waste, organizations can reduce costs, improve efficiency, and enhance customer satisfaction.
- Process Improvement: Lean tools provide organizations with a structured approach to process improvement. They help identify and eliminate non-value-added activities, optimize workflows, and streamline processes. This results in increased productivity, reduced lead times, and improved quality.
- Problem-Solving: Lean tools, such as root cause analysis and the 5 Whys technique, help organizations identify the underlying causes of problems. By addressing root causes, organizations can implement effective solutions that prevent problems from recurring.
- Employee Engagement: Lean tools promote employee involvement and engagement in continuous improvement initiatives. By involving employees in problem-solving and process improvement activities, organizations can tap into their knowledge and experience, leading to more effective solutions and a culture of continuous improvement.
Examples of Lean Tools for Continuous Improvement
There are several lean tools available that can be used for continuous improvement efforts. Some commonly used lean tools include:
- Value Stream Mapping: A visual tool used to analyze and improve the flow of materials and information in a process. It helps identify areas of waste and opportunities for improvement.
- Kaizen Events: Short-term improvement projects focused on a specific process or area. These events involve cross-functional teams and aim to implement small but impactful changes.
- Poka-Yoke: Also known as error-proofing or mistake-proofing, poka-yoke tools are used to prevent errors or defects from occurring during the production process.
- 5S: A workplace organization method that focuses on improving efficiency, safety, and productivity. The 5S principles include Sort, Set in Order, Shine, Standardize, and Sustain.
- Overall Equipment Effectiveness (OEE): A metric used to measure the efficiency and effectiveness of equipment. OEE helps identify areas for improvement and track progress over time.
These are just a few examples of the many lean tools available for continuous improvement. Each tool serves a specific purpose and can be used to address different types of waste or process improvement opportunities.
Conclusion
Lean tools play a crucial role in continuous improvement efforts. They help organizations identify areas for improvement based on regular data analysis, eliminate waste, optimize processes, and engage employees in problem-solving activities. By using lean tools, organizations can achieve higher levels of efficiency, productivity, and customer satisfaction.
Implementing lean tools and embracing a culture of continuous improvement can lead to long-term success and competitiveness in today's fast-paced business environment.
Comments:
Thank you all for reading my article on ChatGPT and its implementation of Lean Tools Technology. I'm excited to hear your thoughts and perspectives!
Great article, Marcia! I found the concept of combining ChatGPT with Lean Tools fascinating. It has the potential to revolutionize continuous improvement processes.
Hey Adam, I completely agree with you. The merging of ChatGPT with Lean Tools can pave the way for faster problem-solving, resulting in reduced waste and improved productivity.
Olivia, you're spot on! The synergy between AI and Lean Tools can empower organizations to tackle complex problems and foster a culture of continuous improvement.
James, I couldn't agree more! AI and Lean Tools together can help organizations uncover hidden improvement opportunities and drive sustainable growth.
Emma, your point is crucial. AI can act as a catalyst for unlocking untapped potential within lean processes, leading to significant improvements in efficiency and effectiveness.
Adam, it's great to see how ChatGPT combined with Lean Tools can spark such enthusiasm among professionals like us. The potential it holds for continuous improvement is remarkable!
Emily, absolutely! It's an exciting time where technology and lean thinking converge, ushering in a new era of improvement methodology.
Adam, I couldn't agree more! The synergy between ChatGPT and Lean Tools has the potential to reshape how organizations approach continuous improvement and achieve operational excellence.
I totally agree, Adam! This integration opens up possibilities for enhancing problem-solving capabilities and streamlining improvement initiatives.
Emily, I've had firsthand experience implementing ChatGPT in lean projects. It significantly aided our continuous improvement efforts by suggesting innovative solutions and providing real-time assistance.
Daniel, that sounds amazing! Did you face any challenges while implementing ChatGPT in the lean environment?
Sophie, I encountered a few challenges while implementing ChatGPT in a lean environment. The main one was ensuring that the AI predictions aligned with the lean principles and didn't introduce unnecessary complexity.
Sarah, that's an important consideration. Ensuring that AI predictions align with lean principles avoids any unintended consequences that could hinder process improvement.
Marcia, your article highlights the importance of deploying AI in lean environments. It enables better decision-making and boosts operational efficiency.
Absolutely, Jack! AI integration in lean environments can provide valuable insights for optimizing processes and eliminating non-value-added activities.
Thank you, Adam, Emily, and Jack, for your positive feedback! The combination of AI and Lean Tools indeed promises significant benefits. Has anyone had experience implementing such a system?
Marcia, I've personally implemented a ChatGPT-driven improvement system. It was a game-changer in terms of identifying bottlenecks and suggesting optimization strategies.
Lucas, that's fantastic! How did you ensure that the suggestions provided by ChatGPT were reliable and aligned with the lean goals?
Isabella, as we progressed, we fine-tuned the ChatGPT model based on feedback and validation from lean experts within our organization. It was crucial to strike a balance between leveraging AI insights and maintaining lean principles.
Lucas, I'm amazed by your approach to refining ChatGPT based on lean expert feedback. It's essential to adapt AI tools to fit individual organizational contexts and goals.
Lucas, your experience aligns with the key aspect of any AI implementation: continuous improvement. It's crucial to refine and validate AI-driven solutions to maximize their potential.
Emma, absolutely! We engaged in iterative experimentation, validating the suggestions made by ChatGPT against real-world lean metrics and continuously refining the system.
This article is a game-changer, Marcia! Incorporating ChatGPT into Lean Tools can enhance problem-solving capabilities, leading to accelerated improvements.
Paul, you're absolutely right! By harnessing the power of AI, Lean Tools can evolve further to address complex challenges and promote continuous innovation.
Sophia, aligning AI with lean principles is indeed important. It ensures that the focus remains on eliminating waste and driving customer value rather than just adopting technology for the sake of it.
Ethan, you raised a vital point. It's crucial to ensure that technology is leveraged to support lean goals, rather than becoming a distraction or complicating the improvement process.
Mia, you're absolutely right. Technology should always serve as an enabler for lean principles, fostering continuous improvement and delivering value to customers.
Amelia, technology should never overshadow the essence of lean methodologies. Its role is to support the elimination of waste and enable value creation through continuous improvement.
Ethan, I completely agree. It's vital to avoid the temptation of implementing AI for the sake of it. Instead, we should focus on using it strategically to support lean goals.
Sophia, your insights on the potential of AI in lean environments are spot on. It's a powerful combination that can propel organizations towards operational excellence.
Sophia, I couldn't agree more! The AI-powered Lean Tools can augment problem-solving capabilities and empower organizations to drive sustainable improvements.
Nathan, indeed! By incorporating AI capabilities into lean practices, organizations can continuously adapt, innovate, and outperform their competitors.
Paul, I couldn't agree more! The integration of AI with Lean Tools presents exciting possibilities for achieving operational excellence and pushing boundaries.
Nicole, precisely! The fusion of AI and Lean Tools can unlock novel approaches for problem-solving, enabling organizations to surpass traditional improvement methods.
David, indeed! The amalgamation of AI and Lean Tools can push the boundaries of operational efficiency and foster a culture of continual learning and development.
Sophie, precisely! The combination opens new horizons for problem-solving and helps organizations stay ahead in highly competitive markets.
David, I completely agree. In today's fast-paced business environment, leveraging AI in lean practices is necessary to drive innovation and continuous improvement.
Lucy, you're absolutely right! To thrive in a rapidly changing landscape, organizations need to embrace AI as a strategic enabler of lean practices.
The idea of leveraging AI to amplify the power of Lean Tools is intriguing. It offers the potential for data-driven decisions and faster problem resolution.
Lila, I'm glad you find the idea intriguing! With AI-powered Lean Tools, organizations can harness data-driven insights to optimize processes and ensure prompt problem resolution.
Olivia, you hit the nail on the head! AI and Lean Tools together enable organizations to leverage data in real-time, identify improvement opportunities, and drive higher efficiencies.
Olivia, it is fascinating to witness how AI-driven Lean Tools can empower organizations to make informed decisions and drive continuous improvement.
Olivia, completely agreed! The amalgamation of AI and Lean Tools helps organizations achieve a data-driven approach to improvement and foster a culture of continuous learning.
Olivia, the combination of AI and Lean Tools can significantly enhance problem-solving capabilities by augmenting human intelligence with machine intelligence.
Thank you all for sharing your insights and experiences on the integration of ChatGPT and Lean Tools. Your comments highlight the potential impact and challenges associated with such implementation.