Efficient Downtime Reduction with ChatGPT: Optimizing GD&T Technology
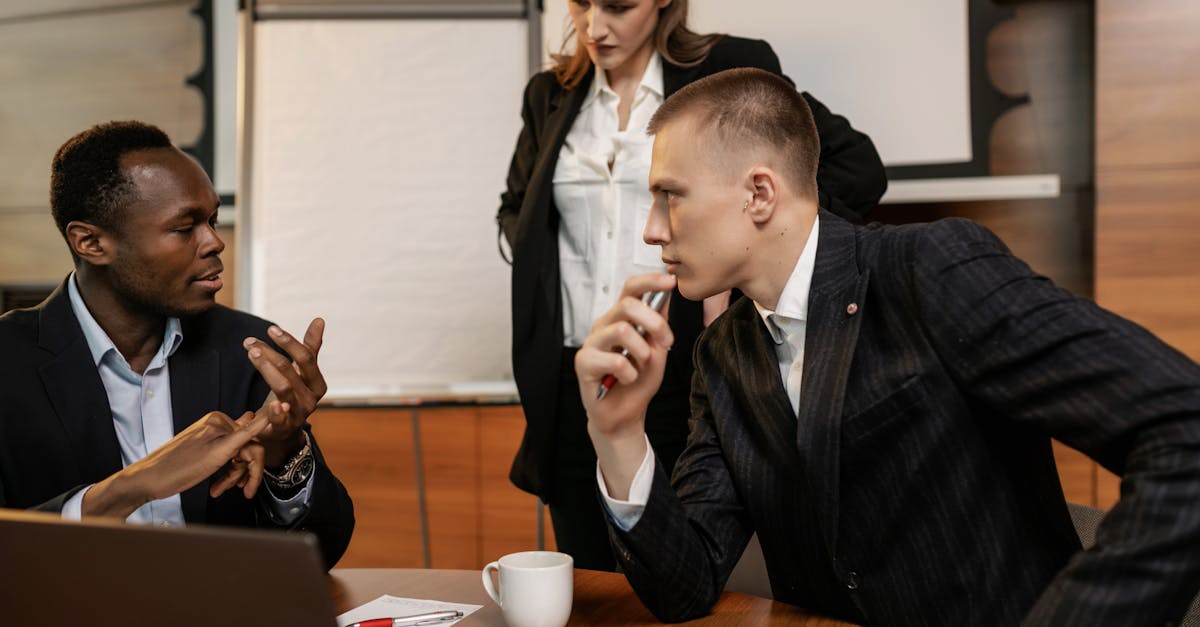
Geometric Dimensioning and Tolerancing (GD&T) is a technological approach used in design, engineering, and manufacturing industries to define and communicate the allowable variations in form, size, and orientation of features on a part. By applying this standardized system, manufacturers can ensure that parts are produced to meet design specifications consistently.
Understanding Downtime
Downtime refers to the period of time when a machine or a system is not operating as intended. For manufacturing companies, any unplanned downtime can be disruptive and costly, often resulting in lost production and missed deadlines. It is crucial for these companies to find ways to anticipate and prevent potential downtime issues.
How GD&T Helps in Downtime Reduction
GD&T plays a vital role in downtime reduction by providing a comprehensive framework for defining and controlling part features. Here are the key ways in which GD&T helps in anticipating and preventing downtime issues:
Accurate Dimensional Control
GD&T ensures accurate dimensional control by defining the allowable tolerances for part features. This helps prevent issues such as improper fit, misalignment, or excessive wear that can lead to downtime. By clearly specifying the acceptable variations in size and form, GD&T promotes consistency in part production and assembly, reducing the likelihood of downtime due to dimensional issues.
Enhanced Assembly Quality
GD&T provides clear instructions for aligning and mating parts during assembly. By utilizing geometric symbols and feature controls, GD&T enables manufacturers to communicate the intended relationships between different parts accurately. This promotes proper fit and alignment, reducing the chances of assembly errors that can cause downtime.
Effective Inspection and Verification
GD&T facilitates effective inspection and verification processes, ensuring that parts and assemblies meet the required specifications. By using geometric symbols and characteristics, GD&T enables inspectors to quickly identify and measure critical features, reducing inspection time and preventing production delays. This proactive approach to quality control helps in minimizing potential downtime associated with dimensional non-conformities.
Improved Communication and Collaboration
GD&T acts as a common language for design, manufacturing, and quality teams, fostering effective communication and collaboration. By standardizing the language and symbols used to define product features, GD&T eliminates ambiguity and interpretation errors. This shared understanding facilitates problem-solving, reduces rework, and minimizes downtime resulting from miscommunication or misunderstandings.
Conclusion
GD&T serves as a valuable tool in downtime reduction by enabling manufacturers to anticipate and prevent potential issues related to part features. By providing accurate dimensional control, promoting enhanced assembly quality, facilitating effective inspection and verification, and improving communication and collaboration, GD&T plays a critical role in ensuring the smooth operation of manufacturing processes. Incorporating GD&T into the design and manufacturing workflow can help companies enhance productivity, reliability, and efficiency while reducing costly downtime.
Comments:
Thank you all for taking the time to read my blog article on Efficient Downtime Reduction with ChatGPT and GD&T Technology. I'm excited to hear your thoughts and answer any questions you may have!
Great article, Aditi! ChatGPT seems like an amazing tool. I have a question, though. Can you tell us more about how GD&T technology is being optimized with ChatGPT?
Thank you, Rohan! ChatGPT is helping optimize GD&T technology by enabling real-time communication between designers, engineers, and manufacturing teams. It improves collaboration, reduces downtime, and minimizes errors by ensuring effective understanding and implementation of GD&T principles.
I've used ChatGPT for other projects, and it's been a game-changer. Combining it with GD&T technology sounds like a winning combination!
Absolutely, Sara! ChatGPT's natural language processing capabilities coupled with the precision and reliability of GD&T technology can significantly enhance manufacturing processes.
As an engineer, I'm always looking for ways to improve efficiency. I'm curious if there are any specific examples where ChatGPT and GD&T have made a notable impact.
Certainly, Liam! One example is the reduction of miscommunication between stakeholders during the design phase. ChatGPT ensures everyone is on the same page, reducing errors and rework. It also aids in real-time troubleshooting during production, minimizing downtime.
This article provides valuable insights into how evolving technologies are improving manufacturing processes. Kudos to the author for sharing this!
Thank you, Nadia! I'm glad you found the article insightful and valuable. It's crucial to explore how technology can positively impact the manufacturing industry.
Aditi, have you come across any challenges while implementing ChatGPT and GD&T technology?
Absolutely, Rohan! One challenge is ensuring ChatGPT understands technical GD&T terms and contexts accurately. It requires training the model with domain-specific data and fine-tuning for industry-specific jargon. However, once overcome, the benefits are immense.
I'm impressed with the potential of ChatGPT and GD&T. It would be interesting to know if there are any other industries where this combination of technologies could be beneficial.
Indeed, Michael! While GD&T and ChatGPT are particularly valuable in manufacturing, their applications can extend to industries like aerospace, automotive, electronics, and more, where precision, collaboration, and reducing downtime are essential.
Aditi, I appreciate your article, but I'm concerned about potential issues with bias in AI models like ChatGPT. How can we ensure the technology doesn't perpetuate existing biases?
Thank you for raising a crucial point, Renuka. Bias mitigation is important, and the developers of ChatGPT and GD&T technology are actively working on addressing these concerns. It's an ongoing challenge but vital for responsible and equitable use of AI.
ChatGPT seems like an excellent tool, but is it accessible for small businesses or only applicable to large manufacturing organizations?
Good question, James! While large organizations can benefit from the scalability of ChatGPT, efforts are being made to make it more accessible to small businesses. The potential cost savings and improved efficiency make it a valuable investment for businesses of various sizes.
I enjoyed reading your article, Aditi. It's exciting to see how technology continues to revolutionize the manufacturing industry!
Thank you, Priya! The advancements in technology indeed open up new possibilities for optimizing manufacturing processes and driving continuous improvement.
I'm curious about the implementation process. Is adopting ChatGPT and GD&T technology complicated or time-consuming?
Great question, Sneha! While implementation may require initial setup and familiarization, integrating ChatGPT and GD&T technology is designed to be user-friendly and efficient. The goal is to minimize disruptions and maximize the benefits for manufacturing teams.
This article highlights the potential of AI in revolutionizing manufacturing operations. Well-written, Aditi!
Thank you, Vikram! AI technologies like ChatGPT have indeed transformed multiple aspects of manufacturing, including communication, collaboration, and productivity.
Aditi, can you elaborate on the benefits of GD&T technology alone, without ChatGPT?
Certainly, Ashok! GD&T technology improves manufacturing processes by enabling clear communication, minimizing errors, allowing for more precise designs, cost reduction, and enhanced product quality. However, introducing ChatGPT adds real-time collaboration and further optimizes these benefits.
I appreciate the practical insights you provided, Aditi. It's crucial to bridge the gap between design and production, and ChatGPT seems to facilitate that.
Thank you, Neha! Bridging the gap between design and production is indeed a challenge, and ChatGPT helps streamline the process by ensuring effective communication and reduced misunderstandings.
Aditi, could you share any success stories of companies using ChatGPT and GD&T together?
Certainly, Hiroshi! We've seen several companies significantly enhance their productivity and reduce downtime by adopting ChatGPT and combining it with GD&T technology. Testimonials from businesses across various sectors demonstrate the success of this integration.
I'm glad to see technology being harnessed to improve efficiency in manufacturing. Aditi, how do you see these technologies evolving in the next few years?
Great question, Ayesha! In the coming years, we can expect even more advancements in ChatGPT and GD&T technology. Their capabilities will continue to expand, allowing for more nuanced conversations, better context understanding, and further optimization of manufacturing processes.
I'm impressed with the potential of ChatGPT and GD&T technology. Aditi, do you think they will eventually replace traditional communication channels within manufacturing organizations?
Thank you, Daniel! While it's unlikely that ChatGPT and GD&T technology will completely replace traditional communication channels, they will certainly become integral tools for collaboration, problem-solving, and driving efficiency across manufacturing organizations.
ChatGPT and GD&T working together can undoubtedly improve processes, but are there any potential limitations or drawbacks we should be aware of?
Great question, Leah! Like any technology, there are limitations. ChatGPT's accuracy is reliant on the data it's trained on, so ensuring it understands technical jargon is critical. Additionally, while it aids in communication, it should not replace engineering expertise for complex decisions.
Aditi, your article sheds light on an exciting application of AI in the manufacturing sector. I'm curious if there are any similar technologies being developed in parallel.
Absolutely, Emma! Various AI technologies like computer vision, digital twin models, and predictive analytics are being developed to complement solutions like ChatGPT and GD&T. This holistic approach ensures a comprehensive transformation of manufacturing processes.
Aditi, as an industry professional, I appreciate the depth of knowledge shared in your article. It's evident that these technologies are reshaping manufacturing.
Thank you for your kind words, Kumar! I'm thrilled to share insights that contribute to a better understanding of how technology is revolutionizing the manufacturing industry.
Aditi, I see the potential benefits, but are there any specific case studies or statistical data available to support the claims made in this article?
Valid point, Tina! While I didn't include specific case studies in this article, there are several studies and reports available that demonstrate the positive impact of ChatGPT and GD&T technology integration. I can share some resources with you after this discussion.
Aditi, I'm interested in knowing if there are any potential security concerns associated with implementing AI tools like ChatGPT in manufacturing processes.
Great question, Luca! Data security is an essential consideration while implementing AI tools. Organizations must adhere to best practices in data protection, access control, and secure communication protocols. Ensuring compliance with relevant regulations and industry standards is crucial.
Thank you for answering my question earlier, Aditi! Your explanations clarified how ChatGPT and GD&T work together.
You're welcome, Rohan! I'm glad I could provide you with the information you were looking for. If you have any more questions, feel free to ask!
Aditi, your article highlights the potential for improved collaboration in manufacturing. How do you envision this technology impacting the role of engineers and designers?
Thank you, Elisa! ChatGPT and GD&T technology can empower engineers and designers by reducing time spent on clarifications and rework. It allows them to focus more on innovation and problem-solving, ultimately enhancing their productivity and creativity.
The combination of ChatGPT and GD&T seems to be a game-changer for manufacturing. Aditi, what would be your advice for organizations looking to leverage these technologies?
Thank you, Varun! My advice would be to start with smaller pilot projects, identifying areas where communication gaps and downtime reduction can have a significant impact. Collaborating with experts in AI, design, and engineering also helps ensure a smooth implementation and maximize the benefits of these technologies.
Aditi, thank you for sharing your expertise. It's inspiring to see how technology can transform traditional industries like manufacturing.
You're welcome, Hannah! I'm thrilled to have been able to contribute to the discussion and highlight the tremendous potential technology holds for the manufacturing industry.