Empowering Tolerance Analysis in Assembly Sequence Analysis with ChatGPT: Unlocking New Possibilities
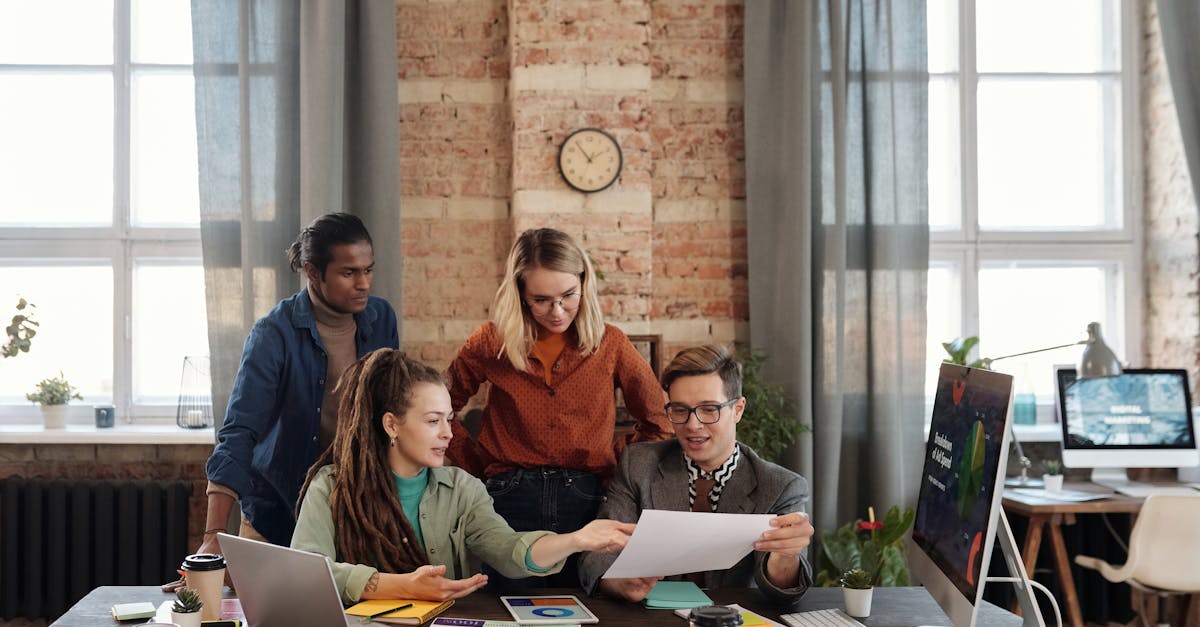
In the field of manufacturing and engineering, ensuring the proper fit and functionality of assembled components is of paramount importance. Tolerance analysis is a key process used to determine the permissible variations in dimensions and characteristics of individual components, while assembly sequence analysis provides insights into how the sequence of assembly can affect component tolerances. By integrating these two technologies, manufacturers can optimize their assembly processes and improve the overall quality of their products.
What is Tolerance Analysis?
Tolerance analysis is a systematic process that helps in understanding the impact of manufacturing variations on the functional requirements of an assembly. It involves analyzing the dimensions, tolerances, and variations of individual components and assessing their cumulative effect on the final product. Tolerance analysis ensures that components can be assembled within predetermined limits to achieve proper fit, functionality, and quality.
What is Assembly Sequence Analysis?
Assembly sequence analysis, on the other hand, focuses on evaluating the effect of the order in which components are assembled on the overall tolerances of the final product. It considers factors such as distortion, accumulation of variations, and the potential for misalignment or interference during assembly. By simulating different assembly sequences, manufacturers can identify potential issues and make informed decisions to optimize the assembly process.
Integration and Benefits
Integrating tolerance analysis with assembly sequence analysis allows manufacturers to gain valuable insights into how the sequence of assembly can impact the tolerances of individual components. By considering not only the individual variations of each component but also the interaction between components during assembly, manufacturers can make informed decisions to minimize assembly issues, reduce rework and scrap, and improve overall product quality.
Some of the key benefits of integrating tolerance analysis with assembly sequence analysis include:
- Identification of critical assembly sequences: By analyzing different assembly sequences, manufacturers can identify the ones that are more prone to causing assembly issues or exceeding tolerance limits. This information allows them to prioritize and optimize their assembly processes.
- Optimization of tolerances: Through simulation and analysis, manufacturers can identify opportunities to optimize tolerances by adjusting the dimensions or characteristics of individual components. This optimization can help improve the overall fit and functionality of the final product.
- Reduction of rework and scrap: By understanding the potential assembly issues upfront, manufacturers can take preventive measures to reduce rework and scrap. This not only saves costs but also improves the efficiency of the production process.
- Improved product quality: By ensuring that components are assembled within the permissible limits, manufacturers can enhance the overall quality of their products. This leads to increased customer satisfaction and loyalty.
Conclusion
Tolerance analysis and assembly sequence analysis are powerful tools that can significantly impact the manufacturing process. By integrating these technologies, manufacturers can gain valuable insights into how assembly sequences can affect component tolerances and make informed decisions to optimize their assembly processes. The benefits include improved product quality, reduction of rework and scrap, and optimization of tolerances. By investing in these technologies, manufacturers can enhance their competitiveness, streamline their production processes, and deliver high-quality products to their customers.
Comments:
Thank you all for joining this discussion! I'm excited to hear your thoughts on the article.
I found the article very informative. ChatGPT seems like a powerful tool to enhance tolerance analysis in assembly sequence analysis.
I agree, Anna. It opens up new possibilities and can streamline the analysis process. I'm curious to know if there are any limitations to using ChatGPT in this context.
Great point, Michael. It would be helpful to understand potential challenges or constraints when implementing ChatGPT in assembly sequence analysis.
From my understanding, one limitation could be the accuracy of ChatGPT's responses based on the input it receives. It heavily relies on the quality and relevance of the initial data it was trained on.
That's a valid concern, Andrew. So, the accuracy of the analysis would depend on the training data provided to ChatGPT.
I wonder if there are any privacy or security risks associated with using ChatGPT in assembly sequence analysis. Has the article addressed this?
Good question, Sara. I didn't see any specific mention of privacy concerns. Erik, could you shed some light on this?
Sara and Anna, thanks for bringing up this important point. The usage of ChatGPT in assembly sequence analysis should adhere to proper data privacy and security measures. It would be ideal to encrypt any sensitive data before utilizing the tool.
Erik, what are some practical examples or use cases where ChatGPT has already shown promising results in assembly sequence analysis?
Daniel, while ChatGPT is still relatively new, initial tests have shown promising results in improving efficiency and accuracy in various manufacturing industries. Case studies are being conducted to further validate its benefits.
That's intriguing, Erik. I'll keep an eye out for those case studies to get a better understanding of real-world applications and outcomes.
Erik, I'm curious to know if ChatGPT can handle multiple assembly sequences simultaneously or if it's limited to one sequence at a time.
Rachel, as of now, ChatGPT is designed to handle one assembly sequence at a time. However, future developments may explore the possibility of multiple sequence analysis.
Thank you for clarifying, Erik. It would be interesting to see how ChatGPT evolves to handle complex scenarios with multiple sequences.
Agreed, Rachel. Multi-sequence analysis would be a valuable enhancement to tackle intricate assembly scenarios. Exciting possibilities lie ahead!
Erik, are there any plans to make ChatGPT more domain-specific or customizable for assembly analysis, taking into account unique requirements of different industries?
Andrew, OpenAI is actively researching approaches to make ChatGPT more customizable and adaptable to domain-specific needs. The goal is to provide flexibility for different industries, including assembly analysis.
That's great to hear, Erik. Customization would be valuable in tailoring ChatGPT to specific assembly analysis challenges and increasing its relevance in various sectors.
Indeed, Julia. By allowing customization, ChatGPT can better align with industry-specific requirements, ultimately delivering more accurate and insightful assembly analysis results.
Additionally, it would be worth exploring how the data shared with ChatGPT is handled in terms of retention and access by OpenAI. Transparency is critical here.
I completely agree, Robert. Data handling practices should be disclosed to ensure user trust and compliance with privacy regulations.
Apart from potential limitations and privacy concerns, I'm curious about the computational resources required for implementing ChatGPT effectively in assembly sequence analysis.
Good point, Emily. Considering the scale and complexity of assembly sequence analysis, it's important to understand the computational demands of utilizing ChatGPT.
I believe the article should have provided insights into the hardware requirements and computational efficiency of ChatGPT in this context.
Exactly, Thomas. It would help practitioners assess the feasibility and cost-effectiveness of incorporating ChatGPT into their assembly sequence analysis workflows.
While we explore potential limitations and constraints, it's important to acknowledge the benefits of ChatGPT. The article already highlighted its empowering aspects, but what other advantages do you see?
One advantage I can think of is the potential reduction in manual effort required for tolerance analysis. ChatGPT can assist in automating certain aspects, making the process more efficient.
Absolutely, Alex. By providing real-time feedback and suggestions, ChatGPT can significantly speed up the analysis process and improve overall productivity.
It's impressive to see how AI-powered tools like ChatGPT can enhance decision-making and problem-solving in complex engineering domains.
Agreed, Michael. The integration of AI into these processes has the potential to revolutionize how we approach assembly sequence analysis.
In addition to data handling and privacy concerns, it would be beneficial to know if there are any ethical considerations associated with using AI in assembly sequence analysis.
I second your thought, Emma. As AI continues to evolve, ensuring ethical practices becomes vital to prevent biases or unintended consequences in AI-assisted analysis.
Emma and Sara, I believe incorporating ethics into AI implementation should be a key concern across all industries. It's crucial to minimize any potential harm caused by AI algorithms.
While the benefits of ChatGPT are evident, it's essential to strike a balance between automation and human expertise. Engineers' domain knowledge remains valuable in assembly sequence analysis.
I completely agree, David. AI should augment human capabilities, not replace them entirely. Engineers' expertise combined with AI assistance can lead to optimal analysis outcomes.
Well said, Alex. The augmented intelligence approach, where both humans and AI work collaboratively, holds great promise in complex engineering domains.
Considering the ever-growing complexity of assembly analysis, I wonder if ChatGPT can adapt and learn on-the-fly from user interactions or experience.
That's an interesting thought, Grace. The ability for ChatGPT to learn and adapt over time could significantly enhance its effectiveness in assembly sequence analysis.
Indeed, Thomas. Continuous learning and improvement of ChatGPT's models can lead to more accurate and context-aware analysis in the long run.
To ensure ethical AI implementation, it would be valuable for organizations to establish guidelines or frameworks specifically for using AI-driven tools like ChatGPT in assembly analysis.
Absolutely, Emma. Ethical guidelines can provide a structured approach to addressing potential biases, unintended consequences, and other ethical challenges associated with AI integration.
Organizations should also foster a culture of ethical AI usage, where practitioners are encouraged to question and challenge the decisions made by AI algorithms in assembly analysis.
Well said, David. Transparency and accountability should be integral components of any ethical framework implemented in AI-assisted assembly sequence analysis.
Another benefit of ChatGPT is the potential to capture and analyze historical data, thus enabling continuous improvement of assembly processes over time.
Robert, that's a valuable point. The insights gained from analysis can contribute to refining assembly strategies, reducing errors, and enhancing overall efficiency in the long term.
Exactly, Oliver. This iterative improvement facilitated by ChatGPT can drive optimization and cost savings in assembly operations.
It's fascinating to witness the impact that AI-driven tools like ChatGPT can have on long-term process improvement. The future of assembly analysis looks promising!
Continual analysis and improvement can also contribute to enhancing product quality, which is crucial for ensuring customer satisfaction.
Absolutely, Michael. By leveraging ChatGPT in assembly sequence analysis, organizations can strive for higher quality standards, fostering stronger customer relationships.