Enhancing 3D Meshing with ChatGPT: Revolutionizing Hypermesh Technology
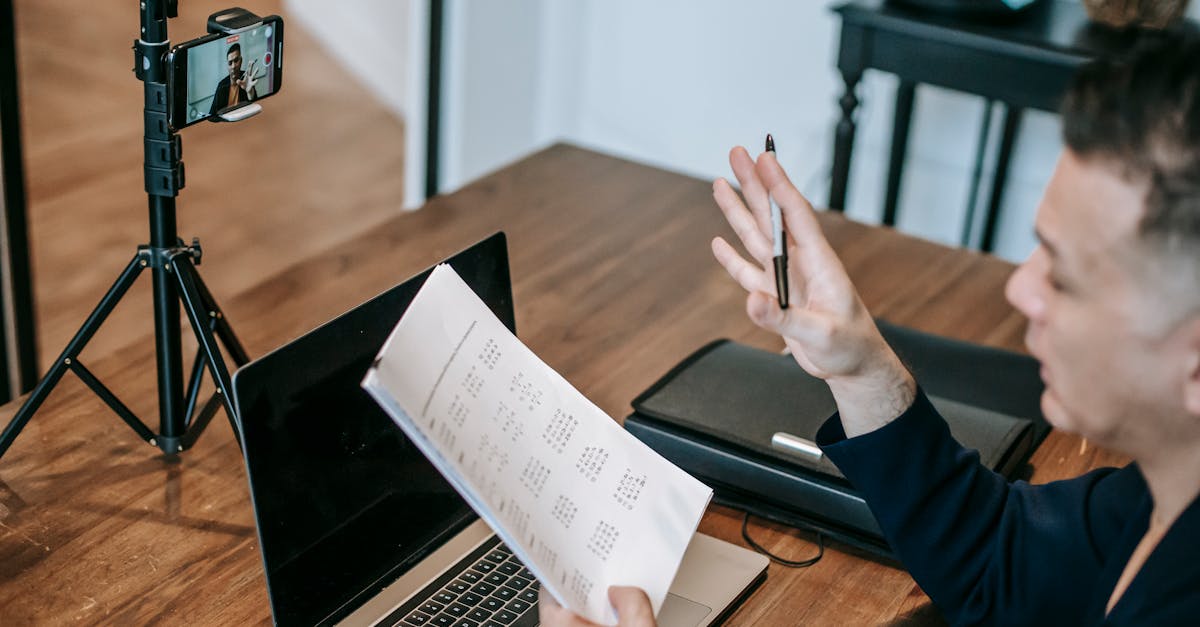
Introduction
Hypermesh is a powerful software tool used extensively in the field of 3D meshing. It provides engineers and designers with the ability to generate high-quality meshes for various simulation and analysis purposes. This article aims to offer advice on 3D meshing approaches and common pitfalls to avoid when working with Hypermesh.
Understanding 3D Meshing
Before diving into the specifics of using Hypermesh, it is important to have a basic understanding of 3D meshing. Meshing is the process of dividing a solid object into a collection of small, interconnected elements called mesh elements or simply elements. These elements act as the building blocks for numerical simulations, such as finite element analysis (FEA) or computational fluid dynamics (CFD).
Approaches for 3D Meshing
When approaching 3D meshing using Hypermesh, there are a few key considerations to keep in mind:
- Geometry Cleanup: Before meshing, it is crucial to ensure that the geometry is clean and free from any errors or inconsistencies. Fixing issues such as gaps, overlaps, or intersecting surfaces will significantly improve the meshing process and the overall quality of the mesh.
- Mesh Element Types: Depending on the nature of the simulation, the choice of element type is essential. Hypermesh offers various element types, such as tetrahedral, hexahedral, and shell elements, each suitable for specific applications. Carefully select the appropriate element type to accurately represent the behavior of the simulated object.
- Mesh Density and Quality: Achieving a balanced mesh density is crucial. A mesh that is too coarse may not capture the details of the object accurately, while an overly refined mesh may lead to excessive computational costs. Additionally, ensuring mesh quality is important to obtain reliable results. Avoid elements with poor aspect ratios or high distortions as they can introduce numerical errors.
- Boundary Conditions: Properly defining boundary conditions, such as fixing or applying loads to specific regions, is essential for accurate simulations. Ensure that the mesh is appropriately refined near regions with expected high stress or deformation, while maintaining a smooth transition between different mesh densities.
Common Pitfalls to Avoid
When using Hypermesh for 3D meshing, it is important to be aware of common pitfalls that can affect the quality of the mesh and its subsequent analysis results:
- Incorrect Element Size: Selecting an inappropriate element size can lead to inaccurate results. Balance the element size to capture important features of the object without compromising computational efficiency.
- Element Distortion: Avoid elements with high aspect ratios or excessive distortions as they can introduce errors and inaccuracies in the simulation results. Regularly check the mesh quality metrics provided by Hypermesh to identify and correct any distorted elements.
- Boundary Incompatibilities: Ensure that the boundary conditions defined in the analysis are compatible with the mesh topology. Incompatibilities, such as having a fixed boundary on a deformable region, can lead to unrealistic simulations.
- Lack of Mesh Sensitivity Analysis: Perform mesh sensitivity analysis to assess the impact of varying mesh densities and element types on the simulation results. This will help identify regions where the mesh needs refinement for accurate predictions.
Conclusion
Hypermesh is an excellent tool for 3D meshing, but understanding the underlying concepts and following best practices is vital for obtaining accurate and reliable simulation results. By considering the approaches for 3D meshing and avoiding common pitfalls, engineers and designers can harness the full potential of Hypermesh to achieve their desired outcomes.
Comments:
Thank you all for joining this discussion! I'm excited to hear your thoughts on this article.
This article is fascinating! ChatGPT can really revolutionize the field of hypermesh technology. Can you provide more details on how it works?
Absolutely, Oliver! ChatGPT is a language model that uses advanced deep learning techniques. It can generate human-like responses based on the input it receives. By leveraging ChatGPT, we can enhance 3D meshing by automating certain processes and improving efficiency.
That sounds promising, Ethan! How accurate is ChatGPT in generating responses? Sometimes, AI models tend to produce incorrect or nonsensical outputs.
Great question, Emily! While ChatGPT has made significant progress in generating coherent and contextually relevant responses, it's important to note that it can sometimes produce incorrect or nonsensical outputs. This is why we have a moderation system in place to ensure accuracy and validity in the generated content.
As someone working in the field of hypermesh technology, I'm excited by the potential of ChatGPT. Will it be integrated into existing software platforms or will it be a standalone tool?
That's an excellent question, David! Our plan is to integrate ChatGPT into existing software platforms used in the field of hypermesh technology. This will allow users to seamlessly incorporate the power of ChatGPT into their existing workflows.
I'm curious about the training data used for ChatGPT. How diverse and representative is it?
That's an important point, Sophia! The training data for ChatGPT comes from a wide range of internet sources, which helps capture a diverse set of perspectives and information. However, we actively work on improving the diversity and reducing biases in the training data to ensure better representation.
The potential of ChatGPT in hypermesh technology is promising, but what are the limitations? Are there any scenarios where it might struggle to provide accurate responses?
Good question, Liam! While ChatGPT can generate impressive responses in many cases, it can struggle in scenarios where the input instructions are ambiguous, contradictory, or require deep domain-specific knowledge. It's important to fine-tune and validate its responses in such cases, which is why it's not a fully autonomous tool.
Thanks for explaining, Ethan! The integration of ChatGPT into existing software platforms seems like a game-changer for the industry. When can we expect to see it in action?
You're welcome, Oliver! We're currently working on integrating ChatGPT into our hypermesh software platform and conducting rigorous testing to ensure the reliability and effectiveness of the solution. While I can't provide an exact timeline, we aim to release it within the next year.
I'm curious about the potential impact of ChatGPT on the job market. Do you think it will replace human professionals in the field of hypermesh technology?
That's an important concern, Emily. ChatGPT is designed to assist and enhance the work of professionals rather than replace them. It can automate repetitive tasks, provide suggestions, and improve efficiency, but human expertise will remain crucial for complex problem-solving and decision-making.
The implications of integrating AI like ChatGPT into hypermesh technology are exciting but also raise ethical questions. How do you address concerns around bias and misuse?
An excellent point, Daniel! We prioritize addressing bias and preventing misuse of ChatGPT. Our moderation system works to filter and minimize harmful or biased outputs. We also encourage feedback from users to continuously improve the tool's performance and mitigate potential risks.
I'm glad to hear that measures are in place to tackle bias and misuse, Ethan. What about data privacy? How is user data handled when utilizing ChatGPT?
Data privacy is a crucial aspect, Sophia. We prioritize user privacy and handle data in accordance with strict privacy protocols. User data is anonymized and used solely for research and improving the model, with proper consent and security measures in place.
Ethan, what level of customization can users expect when using ChatGPT for hypermesh technology? Can it be tailored to specific project requirements?
Great question, Liam! While ChatGPT can learn from specific prompts and contexts, it has limitations in terms of project-specific tailoring. We're actively working on providing more customization options, but it's important to balance generalization and specificity to ensure reliability and accuracy.
I'm concerned about potential biases in the training data, given the widespread biases present on the internet. How does OpenAI tackle that?
Addressing biases is a priority for us, David. OpenAI is actively working on reducing both glaring and subtle biases in ChatGPT's responses. We invest heavily in research and engineering to improve the model's understanding and handling of different perspectives without favoring any particular bias.
Ethan, are there any research papers or case studies available that discuss the effectiveness of ChatGPT in the field of hypermesh technology?
Certainly, Oliver! While specific research papers may not be available yet, we are actively conducting case studies and evaluating the effectiveness of ChatGPT in hypermesh technology. Once we have the outcomes, we'll be publishing the results to share insights with the community.
It's great to see companies exploring AI in innovative ways. What kind of support or assistance will be provided to users who integrate ChatGPT into their workflows?
Absolutely, Emily! We'll provide comprehensive documentation, tutorials, and user support to ensure a smooth integration process. Our aim is to empower users and make adopting ChatGPT in hypermesh technology as seamless as possible.
Ethan, can you share any success stories or early adopter feedback from organizations using ChatGPT in the field of hypermesh technology?
At the moment, Sophia, we're still in the development and testing phase with ChatGPT in the field of hypermesh technology. However, initial feedback from early adopters has been positive, with users expressing increased efficiency and productivity in certain aspects of their workflows.
Are there any plans for making ChatGPT available in languages other than English? Language diversity in such tools is crucial.
Indeed, Daniel, language diversity is vital. OpenAI is actively working on expanding ChatGPT's capabilities to support more languages. Our goal is to make this technology accessible and inclusive for users around the world.
Ethan, can you explain the potential cost implications for organizations that wish to incorporate ChatGPT into their hypermesh technology workflows?
Certainly, Oliver! While exact pricing details are not available at this stage, we aim to offer affordable options that align with the requirements of organizations using ChatGPT in their hypermesh technology workflows. Our goal is to provide value while ensuring accessibility.
Ethan, can you provide some examples of how ChatGPT can assist with specific tasks in hypermesh technology? It would help us visualize its potential use cases.
Absolutely, Emily! ChatGPT can assist with tasks such as automatic mesh generation, suggesting optimal mesh parameters based on specific requirements, identifying potential meshing errors or inconsistencies, and even providing contextual guidance for complex meshing problems. It's a versatile tool that can greatly streamline the process.
Do you foresee any challenges in user adoption when implementing ChatGPT? Some professionals might be reluctant to rely on AI for critical tasks.
That's a valid concern, David. User adoption challenges may arise due to the shift in traditional workflows and concerns about AI reliability. Addressing these concerns through proper education, transparent communication, and support is key to fostering user confidence and encouraging the adoption of ChatGPT in the field.
Ethan, what kind of computational resources would organizations need to run ChatGPT alongside their existing hypermesh software? Will it be resource-intensive?
The computational resource requirements for running ChatGPT depend on the scale and complexity of the tasks and the specific implementation. While it does require computational resources, our aim is to provide efficient and optimized integration options that can work alongside existing hypermesh software without overwhelming the infrastructure.
This article has definitely piqued my interest in ChatGPT for hypermesh technology. Are there any public demos or previews available for users to try it out themselves?
Currently, Sophia, we don't have public demos or previews available for ChatGPT in hypermesh technology. However, we'll be actively informing the community about any potential opportunities to engage with the tool and provide feedback during its development and testing stages.
I appreciate your transparency, Ethan. It's important to set realistic expectations and be aware of the limitations.
Ethan, as AI continues to advance, what future enhancements or developments are you envisioning for ChatGPT in the field of hypermesh technology?
Looking into the future, Daniel, we envision ChatGPT becoming more refined, accurate, and capable in supporting complex problem-solving within the hypermesh technology domain. Continuous improvement, user feedback, and staying at the forefront of AI research are key to unlocking its full potential.
Indeed, a well-rounded and insightful discussion. Thank you, Ethan, for sharing your expertise and providing clarity.
It was a pleasure being a part of this discussion. Thank you, Ethan, for your time and informative responses.
Thank you, Ethan, for your time and patience in addressing our questions. It's been a wonderful discussion.
The potential use cases seem vast, Ethan! Are there any limitations to the scale or complexity of projects where ChatGPT can be effectively utilized?
Good question, Oliver! ChatGPT is best suited for tasks that involve medium-scale projects with well-defined parameters and requirements. While it's capable of handling certain levels of complexity, it may struggle with extremely large or intricate projects that require domain-specific understanding beyond its capabilities.
I agree, Oliver! It would be interesting to know more about the underlying algorithms and training techniques used in ChatGPT.
Ethan, what kinds of feedback or inputs from users are valuable for OpenAI to continuously improve and enhance ChatGPT for the field of hypermesh technology?
Emily, user feedback plays a critical role in making ChatGPT more effective and valuable. Inputs such as reporting incorrect or biased outputs, highlighting areas where it performs well or struggles, and suggesting improvements or specific use cases are highly valuable. The collective insights help us refine the model and cater to the evolving needs of the user community.
Great insights, Ethan! Thank you for your time and for providing us with valuable information about ChatGPT.
Thank you, Ethan, for your detailed explanations. Wishing you and the team success with ChatGPT integration.
Thank you once again, Ethan, for being so engaging and informative throughout this discussion.
Ethan, you've been incredibly responsive and informative. Thank you for sharing your expertise and insights.
Ethan, as AI technology advances, some express concerns about the potential risks it poses. What steps are taken to ensure that ChatGPT remains beneficial and safe for users?
Ensuring the safety and beneficial use of ChatGPT is a top priority, David. OpenAI takes extensive measures to identify and mitigate risks associated with AI systems. This includes robust testing, strict moderation guidelines, transparent communication, and ongoing research to advance the overall safety and reliability of the technology.
Thank you, Ethan, for engaging with us in this discussion. ChatGPT's potential for enhancing 3D meshing in hypermesh technology is exciting, and I'm looking forward to its future developments.
Thanks for explaining! The application of ChatGPT in hypermesh technology brings a new level of automation and collaboration possibilities.
It's great to see OpenAI acknowledge potential issues and prioritize accuracy in generated responses.
Validating responses in complex cases is crucial to prevent any unintended consequences or errors. Thanks for addressing that.
It's great to see OpenAI taking ethical concerns seriously and actively working to reduce biases and misuse.
I'm glad to hear that user data privacy is a priority. It's essential to handle data responsibly.
Finding the right balance between generalization and specificity is indeed important. It ensures reliability while accommodating specific project needs.
Addressing biases is a continuous process, and it's great that OpenAI is actively working on it.
I'll keep an eye out for the future research papers and case studies. Exciting times ahead!
Providing comprehensive support and documentation is crucial for a seamless integration experience. Great to hear that it'll be available.
Early positive feedback from users is encouraging. I'm looking forward to more success stories in the future.
Supporting more languages will undoubtedly increase ChatGPT's accessibility and usefulness on a global scale.
Affordability is another important factor for organizations. It's good to know that OpenAI aims to offer accessible pricing options.
Absolutely, David! Addressing concerns and ensuring accurate responses are key aspects of responsible AI development.
Thank you, Ethan, for your prompt and informative responses. It was a pleasure participating in this discussion.
Thank you, Ethan, for being so responsive and providing us with insightful answers. Looking forward to future updates!
It's been an insightful conversation. Thank you, Ethan, for your valuable time and the great discussion.
Thank you, Ethan, for your prompt and insightful answers. It's been a pleasure discussing with you.
Those specific use cases provide a clear idea of how ChatGPT can be an invaluable asset in hypermesh technology.
Change can bring reluctance, but with proper education and support, professionals may embrace ChatGPT as a valuable tool.
Addressing concerns and supporting users through the adoption process will be crucial for the successful integration of ChatGPT.
Indeed, Oliver! Support, education, and open communication are vital to make ChatGPT integration a success.
Thank you, Ethan, for engaging with us and providing such informative responses! It's been a great discussion.
Thank you, Ethan, for taking the time to answer our questions and providing us with valuable insights into the potential of ChatGPT.
Thank you, Ethan, for patiently addressing all our queries. It was a pleasure discussing with you.
Thank you for providing us with such detailed and informative responses, Ethan. It has been a pleasure.
Thank you, Ethan, for being so generous with your knowledge and addressing all our queries. Best of luck with the future developments of ChatGPT!
Efficiency is key, but it's essential to ensure that the computational resource requirements don't become a hindrance.
User feedback is invaluable for continuous improvement and refining the capabilities of ChatGPT. Collaboration with users is a win-win approach.
Thank you, Sophia! User collaboration and feedback are invaluable in shaping the future of ChatGPT.
Thank you, Ethan, for addressing our questions and concerns. It was a pleasure discussing ChatGPT with you.
Thank you, Ethan, for your patience and for sharing your expertise with us. All the best for the future endeavors!
Thank you, Ethan, for your openness and informative responses. Excited to see the advancements of ChatGPT.
Thank you, Ethan, for your knowledge and insights throughout this discussion. All the best with your work!
Prioritizing safety and reliability is vital in the development and deployment of AI systems. Great to hear that OpenAI has robust measures in place.
Thank you, Liam! Your enthusiasm is much appreciated, and we're excited to bring ChatGPT's potential to the field of hypermesh technology.
Looking forward to witnessing the positive impact ChatGPT will make in the field. Keep up the great work, Ethan!
Thank you, Ethan, for sharing your knowledge and engaging with us. Best of luck with the development of ChatGPT!
Thank you once again, Ethan, for your time and for sharing your knowledge. Best of luck with the ongoing developments!
Ethan, thank you for sharing your expertise and providing us with a comprehensive understanding of ChatGPT.
Thank you, Ethan, for your time and expertise in guiding us through the potential of ChatGPT in hypermesh technology.
Language diversity is important, and we recognize the need to support more languages to cater to a broader user base.