Enhancing Design for Manufacturing Technology through ChatGPT: A Game-Changing Simulation and Modeling Approach
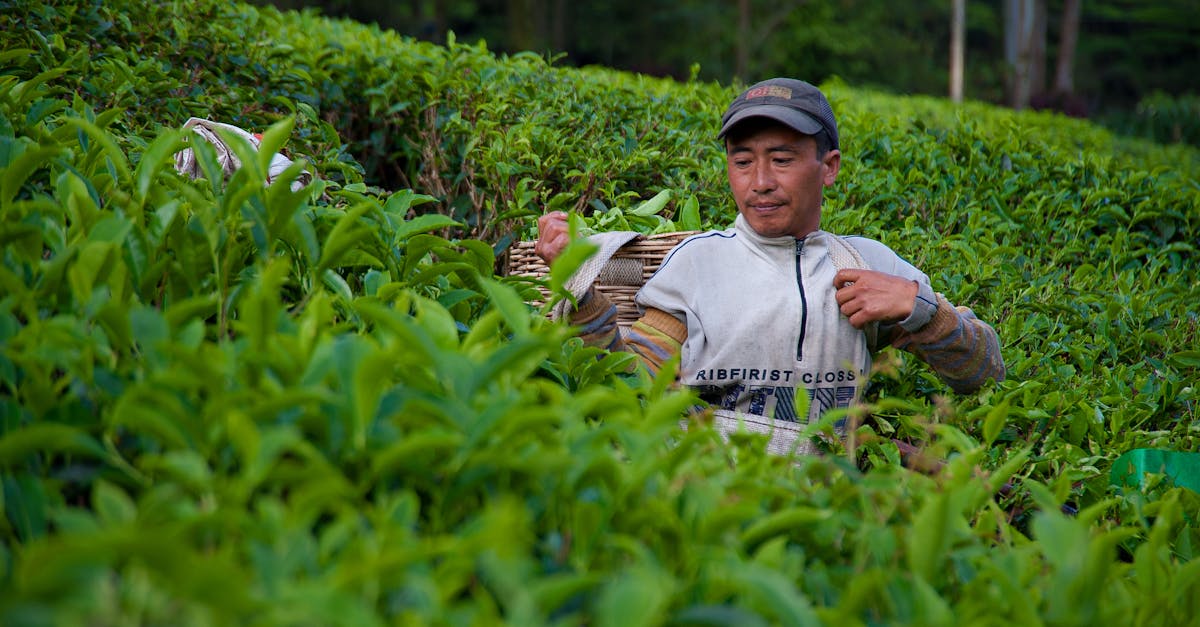
In the field of manufacturing, the design process plays a crucial role in ensuring the efficiency and effectiveness of the production process. Design for Manufacturing (DFM) is an approach that focuses on optimizing design decisions to improve manufacturing processes and reduce costs. Simulation and modeling, as a technology within the DFM framework, provide valuable insights and suggestions based on simulated design and manufacturing conditions.
Simulation and Modeling in Design for Manufacturing
Simulation and modeling techniques enable manufacturers to analyze and evaluate the product design and manufacturing process before physical prototypes are even created. By accurately representing real-world conditions, these technologies allow engineers and designers to identify potential issues and design constraints early on, saving both time and resources.
Simulation and modeling in DFM can aid in various aspects of the manufacturing process, including:
- Assembly Simulation: By creating virtual representations of the product assembly process, manufacturers can identify potential assembly issues, optimize assembly sequences, and ensure that the design allows for smooth and efficient production.
- Process Simulation: Simulating the manufacturing process helps identify potential bottlenecks, optimize production flow, and make informed decisions regarding equipment procurement and layout.
- Material Selection: With simulation and modeling, manufacturers can assess different materials' characteristics, such as strength, flexibility, and durability, before making final material decisions.
- Performance Analysis: Through virtual testing and analysis, engineers can evaluate a product's performance under various conditions, allowing for design improvements and optimization.
Benefits and Usage
The use of simulation and modeling in Design for Manufacturing brings several benefits to manufacturers:
- Cost Reduction: By identifying and resolving design and manufacturing issues early on, simulation and modeling reduce the likelihood of costly rework or production delays.
- Improved Product Quality: Through virtual testing and analysis, manufacturers can ensure that the final product meets the desired performance standards.
- Enhanced Collaboration: Simulation and modeling technologies facilitate collaboration between designers, engineers, and other stakeholders by providing a shared platform for discussing and evaluating design choices.
- Efficient Resource Utilization: By optimizing manufacturing processes and material selection through simulation and modeling, manufacturers can minimize waste and maximize resource utilization.
The usage of simulation and modeling in DFM is widespread across various industries, including automotive, aerospace, electronics, and consumer goods. Manufacturers can leverage these technologies to deliver innovative products that meet customer expectations while maintaining cost-effectiveness.
Overall, the integration of simulation and modeling within the Design for Manufacturing framework empowers manufacturers to make informed decisions, optimize production processes, and ultimately improve product quality. By utilizing these technologies, manufacturers can save time, reduce costs, and drive innovation in today's competitive market.
References:
- https://www.sciencedirect.com/science/article/pii/S2212827114005008
- https://www.cadfamily.com/simulation-manufacturing-solutions-with-technology/
- https://www.researchgate.net/publication/287994361_Progress_in_Simulation_and_Modeling_for_Manufacturing_a_Review
Comments:
This article presents an interesting approach to enhancing design for manufacturing technology using ChatGPT. It seems like a promising idea!
I completely agree! ChatGPT has the potential to revolutionize the simulation and modeling process in manufacturing. Exciting times!
I'm curious about the practical implementation of ChatGPT in design for manufacturing. How would it integrate with existing software and simulation tools?
Great point, David! Sam Keefe, the author of the post, could you please shed some light on how ChatGPT can be seamlessly integrated into the existing workflow?
Thank you for your question, Emily. Integrating ChatGPT into the existing workflow involves developing an API that connects the simulation and modeling tools to the ChatGPT system. This allows users to interact with the AI model and leverage its capabilities within their familiar software environment.
I'm curious about the accuracy and reliability of the simulation results when using ChatGPT. How can we ensure that the AI model is providing accurate feedback?
That's a valid concern, Rachel. The accuracy of ChatGPT can be improved by training it on high-quality and reliable data. Additionally, regular validation and verification processes can be put in place to ensure the accuracy of the simulation results.
I'm interested to know if ChatGPT can handle complex manufacturing scenarios and provide valuable insights. Can it adapt to different industries?
Absolutely, Lisa! ChatGPT can adapt to different manufacturing scenarios across various industries. By training the model on a diverse range of simulation data, it can provide valuable insights and support decision-making in complex manufacturing processes.
I wonder if ChatGPT can automate repetitive tasks in the manufacturing design process. It could save a lot of time and effort.
That's a great point, Robert. With ChatGPT, repetitive tasks in the design process can be automated, freeing up time for engineers to focus on more critical and creative aspects of their work.
While ChatGPT seems promising, I am concerned about the potential biases and limitations of using AI in manufacturing design. How can we address these issues?
I share your concern, Michael. To address biases and limitations, it's important to carefully curate and diversify the training data for ChatGPT. Regular audits and human oversight can also help detect and mitigate any potential biases that may arise.
I'd like to know more about the learning process of ChatGPT. How is it trained to understand and respond to manufacturing-related queries?
Great question, David! ChatGPT is trained using a large dataset of manufacturing-related queries and corresponding responses. The model learns patterns and context from this data, allowing it to understand and generate relevant responses when queried about manufacturing-related topics.
Can ChatGPT handle real-time simulations and provide instant feedback during the design process?
Indeed, Rachel! ChatGPT can handle real-time simulations by leveraging its powerful language understanding capabilities. It can provide instant feedback and recommendations to engineers during the design process, enabling faster iteration cycles.
Is there any specific hardware or software requirement to use ChatGPT in the design for manufacturing process?
No, Lisa, there are no specific hardware or software requirements for using ChatGPT in the design for manufacturing process. It is designed to be flexible and can be integrated into existing software tools commonly used in the industry.
I can imagine ChatGPT being a valuable tool for collaboration among engineers. It could facilitate knowledge sharing and bring interdisciplinary perspectives into the design process.
Absolutely, Robert! ChatGPT can foster collaboration by providing a platform for engineers from various disciplines to share their knowledge, ideas, and perspectives, leading to more innovative and optimized designs.
Are there any limitations or challenges we should consider when implementing ChatGPT in the manufacturing design workflow?
Certainly, Michael. Some limitations include the need for sufficient training data, potential biases, and the ongoing need for human oversight. Additionally, ensuring the privacy and security of sensitive manufacturing data is crucial when using AI models like ChatGPT.
I'm excited about the potential benefits of ChatGPT in enhancing the design for manufacturing technology. It could lead to more efficient and optimized manufacturing processes.
I agree, Sara! ChatGPT has the potential to revolutionize the manufacturing industry by streamlining the design process, improving collaboration, and unlocking innovative solutions.
The integration of AI technologies like ChatGPT into manufacturing design can truly be a game-changer. I'm excited to see how this approach evolves in the future!
I appreciate the article for shedding light on this promising use of AI in manufacturing design. It definitely sparks optimism for the future of the industry.
Kudos to Sam Keefe for sharing this insightful article. It's exciting to envision the potential impact of ChatGPT on manufacturing design!
Indeed, a thought-provoking article. The potential applications of ChatGPT in design for manufacturing are extensive, and it opens up new avenues for exploring innovative solutions.
I'm looking forward to seeing real-world implementations and case studies that showcase the benefits of incorporating ChatGPT into the manufacturing design process.
Absolutely, Michael! Real-world implementations will provide valuable insights and help us understand the full potential and limitations of using ChatGPT in manufacturing design.
I hope this article encourages further research and development in leveraging AI technologies for enhancing design for manufacturing.
Agreed, Emily! The future of manufacturing design looks promising with AI-driven tools like ChatGPT.
Thank you, Sam Keefe, for sharing your expertise on this topic. It's exciting to see how AI is transforming the manufacturing industry.
I appreciate the author's clear explanation of how ChatGPT can be integrated into the existing design workflow without major hardware or software changes.
This article has sparked my curiosity to explore the potential of AI in other areas of the manufacturing process, beyond just design.
Absolutely, David! AI technologies have the potential to transform various aspects of manufacturing, from supply chain management to quality control.
I'm glad to see that AI is being explored for its benefits in manufacturing design. It's a testament to the continuous innovation happening in the industry.
Thank you, Sara! Indeed, the manufacturing industry is continuously evolving, and AI technologies like ChatGPT can help drive innovation and optimize processes.
I'm excited to follow the progress of ChatGPT and see how it can be further refined for manufacturing design applications.
Me too, Emily! The potential advancements in AI-driven design tools for manufacturing are fascinating.
This article has certainly sparked my interest in exploring the possibilities of AI in manufacturing design. It could revolutionize the way we approach product development.
I'm excited about the potential cost savings and efficiency improvements that ChatGPT could bring to manufacturing design processes.
Cost savings and efficiency gains are indeed significant factors, Robert. It's exciting to think about the positive impact ChatGPT could have on the manufacturing industry.
Sam Keefe, thank you for sharing this well-written article. It has shed light on the exciting possibilities of ChatGPT in the design for manufacturing field.
I couldn't agree more, Michael. Sam Keefe's article has provided valuable insights into how ChatGPT can revolutionize manufacturing design.
I'm glad to see AI technologies being explored in the manufacturing industry. It's a clear indication of progress and innovation in the field.
Absolutely, Emily! The potential applications of AI in manufacturing are vast and can lead to improved productivity and streamlined processes.
Thank you, Sam Keefe, for sharing this thought-provoking article. It has sparked important discussions about the role of AI in design for manufacturing.
I agree, Lisa. Sam Keefe's article has initiated a much-needed conversation about the transformative potential of AI in the manufacturing industry.