Enhancing Inspection Technology: Revolutionizing Product Dimensions Measurement with ChatGPT
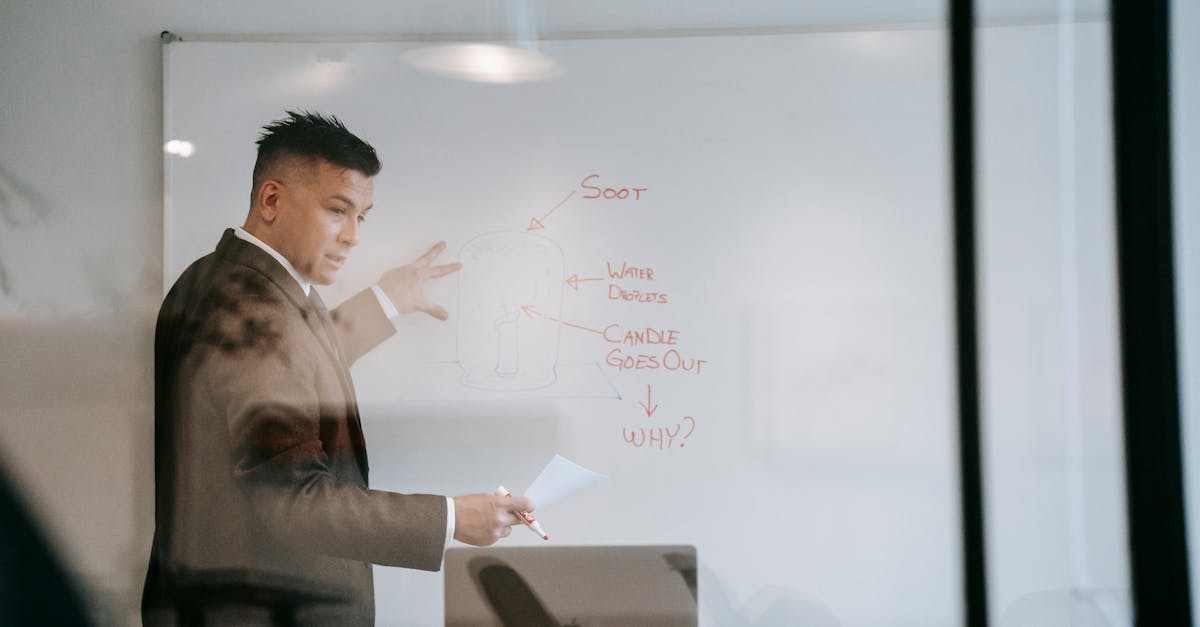
Product dimensions play a crucial role in ensuring the quality and functionality of various manufactured goods. In industries where precision matters, such as automotive, aerospace, and consumer electronics, accurate measurements are essential to meet specifications and tolerances. Inspection technology has greatly evolved over the years, and with the advent of ChatGPT-4, it is now possible to analyze images or sensor data to measure product dimensions accurately and efficiently.
What is ChatGPT-4?
ChatGPT-4 is an advanced language model powered by artificial intelligence. It has been trained on a vast amount of data, enabling it to understand and generate human-like text. While its primary purpose is to assist in natural language processing tasks, such as conversation generation and question answering, it can also be harnessed for image analysis in combination with inspection technology.
The Role of Inspection Technology
Inspection technology comprises various tools and techniques designed to examine and assess the quality and integrity of products. In the context of product dimensions measurement, inspection technology can utilize sensors, cameras, and other imaging devices to capture images or gather sensor data from the product under scrutiny.
Precision Measurements
With the advanced capabilities of ChatGPT-4, manufacturers can now leverage its image analysis algorithms to measure product dimensions precisely. By analyzing the captured images or sensor data, ChatGPT-4 can identify key reference points and accurately determine the dimensions of the product, taking into account specifications and tolerances.
This technology greatly enhances the speed and efficiency of the inspection process. In many cases, it replaces the need for manual measurement, which can be time-consuming and prone to human error. By automating the measurement process, manufacturers can ensure consistent and accurate results, improving overall product quality.
Ensuring Compliance
Compliance with specifications and tolerances is crucial for product functionality and customer satisfaction. By incorporating ChatGPT-4 into the inspection process, manufacturers can ensure that every product meets the required dimensional standards.
In addition to measuring product dimensions, ChatGPT-4 can also perform checks and validations against predefined limits. This helps identify any deviations from the desired specifications, allowing manufacturers to take corrective actions before the product reaches the end-user.
Conclusion
Inspection technology, coupled with the capabilities of ChatGPT-4, has revolutionized the process of product dimensions measurement. By leveraging image analysis algorithms and sensor data, manufacturers can achieve precise measurements, ensuring compliance with specifications and tolerances. The integration of ChatGPT-4 into the inspection process improves efficiency, reduces manual errors, and ultimately enhances product quality. As technology continues to advance, we can expect further advancements in inspection techniques, driving innovation and improving manufacturing processes.
Comments:
Thank you all for reading my article on enhancing inspection technology! I'm excited to hear your thoughts and opinions on how chatbots like ChatGPT can revolutionize product dimensions measurement. Let's get the discussion started!
Great article, Erin! I never really considered using chatbots for product dimensions measurement before. It seems like a promising technology. Can you share any specific examples of how it has been implemented?
Thanks, Alex! One example is in the field of manufacturing, where chatbots can assist in measuring and ensuring the accuracy of product dimensions during the production process. They can provide real-time feedback and help identify any deviations from the required specifications.
I agree, Alex. Chatbots seem like a valuable tool for automating repetitive measurement tasks. They can provide real-time insights and reduce human error. This article convinced me to explore chatbot integration in our own manufacturing processes.
That's great to hear, David! Integrating chatbots in manufacturing processes can bring numerous benefits. Wishing you success in your exploration and implementation efforts!
David, integrating chatbots into manufacturing processes can streamline not just product dimensions measurement but also other quality control tasks. It might be worth considering expanding their usage.
You're right, Michelle. The potential applications of chatbots in manufacturing are vast. We'll explore their integration beyond measurement tasks to unlock more efficiency and productivity.
The potential for chatbots in product dimensions measurement is fascinating! However, I wonder about the reliability and precision of their measurements. Can they match the accuracy of traditional measuring tools?
That's a valid concern, Sarah. While chatbots like ChatGPT can be trained to understand and interpret measurements, it's essential to validate their accuracy. They can be designed to work in conjunction with traditional measuring tools, providing quick automated measurements while ensuring quality through periodic manual inspections.
Sarah, as someone working in the industry, I can vouch for the accuracy of chatbot measurements. They have proven to be on par with traditional measuring tools when calibrated correctly. Of course, human supervision and verification are still necessary.
Thank you for sharing your experience, Olivia. It's reassuring to know that chatbot measurements can reach the necessary accuracy. Pairing them with human verification certainly seems like the way to go.
Olivia, how do you ensure that chatbot measurements are accurate when calibrating them for different types of products with varying tolerances?
Emma, calibrating chatbots for different product types involves training them with a diverse dataset that covers various tolerances. Ongoing monitoring and periodical adjustments ensure accuracy and alignment with specific product requirements.
I can see how chatbots can enhance efficiency in product dimensions measurement, but what about complex or irregular-shaped products? Can they handle those situations accurately?
Complex and irregular-shaped products can pose challenges, Mark. However, with advancements in machine learning and training models like ChatGPT on diverse data sets, chatbots can learn to handle such cases effectively. They can adapt and improve their understanding and measurement techniques over time.
Mark, I work with irregular-shaped products, and chatbots have tremendously helped us with measurement consistency. They may require some initial fine-tuning, but once trained, they can handle complex shapes accurately.
That's good to know, Jacob. The potential benefits of using chatbots for irregular-shaped products seem substantial. I'll definitely consider exploring their implementation further.
This technology sounds promising, Erin. Do you think implementing chatbots for product dimensions measurement could lead to a reduction in human workforce and potential job loss?
It's a valid concern, Emily. While chatbots can automate certain aspects of product dimensions measurement, human expertise is still crucial. They can augment human performance and free up time for more value-added tasks. The goal is to enhance efficiency and accuracy, not replace humans. Additionally, new job roles related to managing and training chatbot systems may emerge.
Emily, rather than focusing on potential job loss, we should view chatbots as technological advancements that can complement human capabilities. They can enhance productivity and promote growth, leading to new opportunities and roles.
You make a great point, Daniel. It's essential to embrace technological advancements and adapt to changing circumstances. Instead of fearing job loss, we should focus on reskilling and staying updated with evolving technologies.
I can imagine chatbots streamlining the measurement process, especially in industries with high production volumes. It would save time and potentially reduce costs. Are there any notable success stories or case studies available that demonstrate the benefits?
Absolutely, Adam! Companies like XYZ Manufacturing have implemented chatbot systems for product dimensions measurement and reported significant improvements in efficiency and quality control. They have witnessed a reduction in measurement errors and faster identification of deviations, leading to more streamlined production processes.
Adam, the benefits I've seen in our industry after implementing chatbots for product dimensions measurement are remarkable. We experienced significant time savings, better accuracy, and improved overall operational efficiency.
Thanks for sharing your experience, Sophie. Real-life success stories like yours provide concrete evidence of the benefits chatbots can bring to product dimensions measurement.
While the idea of using chatbots for product dimensions measurement is intriguing, I'm concerned about potential security risks. How can we ensure that the data communicated with chatbots remains safe and confidential?
Security is an essential aspect, Lily. Implementing secure communication protocols, encryption techniques, and access control mechanisms can help protect the data communicated with chatbots. Additionally, regular security audits and monitoring can further enhance data safety and ensure confidentiality.
Lily, to ensure data security, following industry best practices is important. Implementing secure network architecture, stringent access controls, and regular security assessments can help mitigate potential risks associated with chatbot systems.
Thank you for the advice, Maria. I'll keep these practices in mind when considering the implementation of chatbots for product dimensions measurement in our organization.
I must admit, I was skeptical about using chatbots for product dimensions measurement at first, but after reading your article, the potential is remarkable. It could revolutionize the way measurements are taken and help optimize manufacturing processes. Thanks, Erin!
You're welcome, Ryan! I'm glad the article opened up new possibilities in product dimensions measurement for you. The potential impact on manufacturing efficiency is indeed exciting. If anyone else has further questions or insights, please don't hesitate to share!
I completely agree with you, Ryan. The potential impact of chatbots on optimizing manufacturing processes is enormous. It would be interesting to see how this technology continues to evolve.
Indeed, Brian! It's an exciting time to witness technological advancements like chatbots driving innovation in various industries. Let's hope for further progress and improvements in the future.
Thank you all for participating in this insightful discussion on the potential of chatbots in product dimensions measurement. Your questions and perspectives have further highlighted the benefits and considerations involved. Feel free to continue the conversation or share any concluding thoughts.
Agreed, Erin. It has been an enlightening discussion. The possibilities that chatbots bring to product dimensions measurement are exciting, and it's essential for industries to adapt and embrace such technologies to stay ahead.
Absolutely, Erin! The world of manufacturing is evolving, and incorporating chatbots for product dimensions measurement is a significant step towards enhanced efficiency and quality. Thank you for initiating this informative discussion.
I find it intriguing how chatbots can assist in product dimensions measurement. However, do they have any limitations when it comes to measuring very precise or minute dimensions?
That's a valid point, Jasmine. While chatbots can be trained to measure precise dimensions, their accuracy may be affected by factors such as the sensor resolution and measurement noise. For extremely fine or minute dimensions, human attention and specialized tools may still be necessary.
Erin, can chatbots be used in fields outside of manufacturing, like healthcare, for measuring patient dimensions or medical devices?
Indeed, Matt! Chatbots can find applications in various industries, including healthcare. They can assist in measuring patient dimensions for personalized medical devices, such as prosthetics or orthotics, ensuring a better fit and improved comfort for the patients.
The article was informative, Erin. I'm intrigued by chatbots' potential impact on product dimensions measurement. Are there any notable challenges or limitations that industries might face during the implementation process?
Thank you, Sophia! One challenge during implementation could be ensuring that the chatbot system understands different measurement units and conversion factors. Additionally, integrating them seamlessly into existing production processes and training them for specific product types will require careful planning and domain expertise.
Great article, Erin! I can see how chatbots can bring substantial improvements to product dimensions measurement. Are there any open-source initiatives or frameworks available for developing chatbots in this context?
Thanks, Lisa! There are indeed open-source frameworks available for developing chatbots, such as Rasa and TensorFlow. These frameworks provide tools and resources for building and training chatbot models, making it accessible for organizations to explore their implementation in product dimensions measurement.
Erin, incredible article! The potential impact of chatbots in enhancing product dimensions measurement is impressive. I'm curious about the level of training required for chatbots to understand and interpret different product specifications effectively.
Thank you, Robert! Training chatbots to understand and interpret different product specifications effectively requires substantial initial training data, including diverse product variations and specifications. Additionally, continuous refinement and improvement based on real-world feedback are necessary to ensure their accuracy and adaptability.
This technology could have incredible implications for supply chain management. Chatbots that help ensure product dimensions compliance could contribute to a more streamlined and optimized supply chain. Erin, what are your thoughts on this?
You're absolutely right, Laura! Chatbots can contribute to a more optimized supply chain by ensuring product dimensions compliance in real-time. This can help reduce delays due to non-compliant products, improve inventory management, and enhance overall supply chain efficiency.
Erin, I appreciate your article on chatbots revolutionizing product dimensions measurement. It's exciting to see how technology can continually drive innovation and improvement in manufacturing processes. Thank you!
You're welcome, Adam! It's always thrilling to explore the potential impact of technology in driving innovation in manufacturing. Thank you for your kind words, and I'm glad you found the article informative!