Enhancing Kanban System Implementation with ChatGPT: Streamlining Lean Tools Utilization
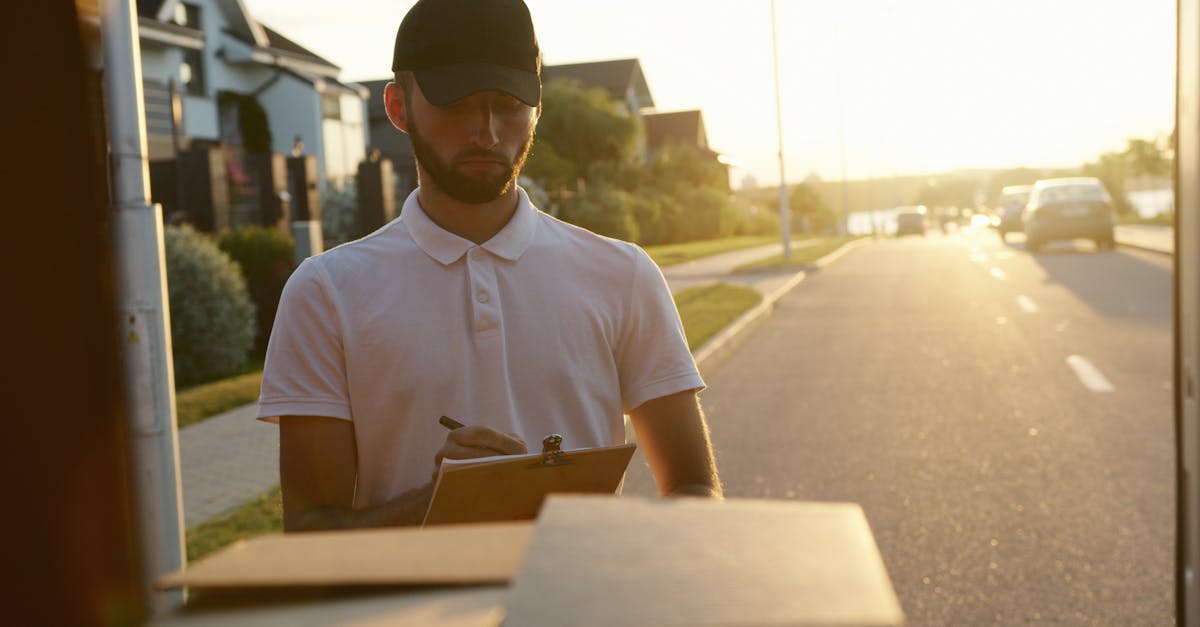
Kanban is a lean manufacturing methodology that originated from the Toyota Production System. It is a popular tool used to manage and optimize workflow efficiency in various industries. When implemented correctly, the Kanban system can greatly improve productivity, reduce waste, and help organizations achieve their goals effectively.
Understanding Kanban System
The Kanban system is built upon the principles of visualizing work, limiting work in progress (WIP), and enhancing flow. It uses visual signals, usually in the form of cards or sticky notes, to represent work items and their respective statuses. These visual signals are moved across the Kanban board, following a predefined workflow, to track the progress and ensure smooth flow of work.
The Benefits of Kanban System Implementation
Implementing a Kanban system provides several benefits to organizations. Firstly, it improves visibility and transparency, enabling team members to easily track the status of tasks and identify bottlenecks in the workflow. This visibility promotes effective collaboration and faster decision-making, as stakeholders have real-time access to the information.
Secondly, the Kanban system helps in managing and optimizing work in progress. By limiting the number of tasks in progress, teams can focus on completing existing work before moving on to the next task. This reduces multitasking and improves productivity by preventing overburdening of resources.
Furthermore, the Kanban system enhances flow by emphasizing the importance of completing work before starting new tasks. This workflow discipline reduces rework, promotes continuous improvement, and ultimately leads to faster delivery of high-quality products or services.
Managing and Optimizing Kanban Systems with Lean Tools
To effectively manage and optimize Kanban systems, organizations can leverage various Lean Tools. These tools provide additional insights and analytical capabilities for continuous improvement. Here are a few examples of Lean Tools commonly used in Kanban system implementation:
- Value Stream Mapping (VSM): VSM helps organizations identify and eliminate waste in their processes. When applied to Kanban systems, VSM can help in streamlining the workflow, reducing lead time, and improving overall efficiency.
- Pareto Analysis: Pareto Analysis is used to identify the most significant issues or bottlenecks that adversely affect the flow of work. By prioritizing these issues, organizations can focus their efforts on resolving them and achieving maximum efficiency.
- 5S Methodology: The 5S methodology focuses on organizing the workplace for improved productivity and morale. In the context of Kanban systems, implementing the 5S methodology ensures that workspaces are clean, organized, and conducive to efficient workflow.
- Continuous Improvement (Kaizen): Kanban systems are designed to promote continuous improvement. Implementing Kaizen principles and practices allows organizations to continually refine their Kanban systems, drive efficiency gains, and achieve operational excellence.
Conclusion
Implementing a Kanban system with the help of Lean Tools can significantly enhance workflow efficiency, improve collaboration, and reduce waste. By visualizing work, limiting WIP, and focusing on flow, organizations can achieve faster delivery of high-quality products or services. The Kanban system, when accompanied by Lean Tools, empowers organizations to continuously optimize their processes and achieve operational excellence.
Comments:
Thank you all for your interest in my article! I'm excited to discuss and answer any questions you may have.
Great article, Marcia! I've been considering implementing Kanban in my team, and your insights on using ChatGPT to enhance it are really helpful.
Thank you, Michael! I'm glad you found the article helpful. Let me know if you have any specific questions or if there's anything else I can assist you with.
I've been using Kanban for a while, but I haven't thought about using AI like ChatGPT to improve it. Interesting approach!
Hi Sarah! Integrating AI technologies like ChatGPT can indeed bring new possibilities and streamline Kanban implementation. Let me know if you need more information on how to get started with it.
I'm a bit skeptical about using AI for Kanban. Won't it add complexity and potentially slow down the process?
Hi Andrew! That's a valid concern. The key is to find the right balance. While integrating AI can bring additional complexity, it can also provide valuable assistance and streamline certain aspects. It's important to carefully evaluate if and how the benefits outweigh the potential drawbacks in each specific case.
I see the potential benefits, but what are the limitations of using AI in Kanban?
Good question, Elena. Some limitations can include AI's inability to handle unexpected or complex situations, lack of human intuition, and potential biases in the generated responses. It's important to critically evaluate and complement AI's suggestions with human judgment and oversight.
I'm interested in implementing Kanban, but I'm not sure how to start. Any suggestions?
Hi John! To get started with Kanban, it's important to define your workflow, identify the key steps, and visualize it on a Kanban board. You can then start with a few columns representing different stages and progressively refine and adapt the process as you gain experience. Don't hesitate to ask if you need more specific guidance.
I'm curious about the security implications of using ChatGPT in the context of Kanban. Is it safe to integrate AI in sensitive workflows?
Peter, security is indeed a critical aspect. When integrating AI like ChatGPT, it's important to assess and address potential security risks. Ensure you follow best practices for securing your systems, including user access controls, data encryption, and regular security audits. Consulting with security experts and adequately protecting sensitive information is essential.
I have a large team, and coordinating Kanban across different projects can be challenging. How can ChatGPT assist in such cases?
Hi Rebecca! ChatGPT can be useful in coordinating and aligning teams by providing real-time updates, assisting with task assignments, and facilitating communication. It can act as a virtual assistant, helping manage and track progress across different projects. It's important to tailor the implementation to suit your team's specific needs and workflows.
What are the key advantages of using Kanban in project management?
Hi Alex! Kanban offers several advantages in project management, including improved visualization of work, increased transparency, better flow management, enhanced collaboration, and the ability to adapt to changing priorities quickly. By limiting work in progress, it helps identify bottlenecks and optimize the overall process.
I'm concerned about the potential automation bias when using AI. How can we ensure balanced decision-making in Kanban with ChatGPT?
Brian, ensuring balanced decision-making is crucial. Counteracting automation bias involves a combination of techniques, such as validating AI-generated suggestions with human review, fostering a culture that encourages critical thinking, and continuously seeking diverse perspectives. Human input should always be considered for important decisions, especially in complex situations.
What are the key challenges organizations might face when implementing Kanban?
Hi Michelle! Some common challenges when implementing Kanban include resistance to change, ensuring team buy-in, defining clear policies and rules, managing dependencies between teams/projects, and continuously monitoring and improving the process based on feedback. It's important to address these challenges proactively and gradually foster a Kanban culture within the organization.
Can you provide some real-life examples where ChatGPT has successfully enhanced Kanban implementation?
Olivia, sure! ChatGPT has been used to assist with task prioritization, provide automatic status updates, offer suggestions for optimizing workflows, and facilitate cross-team collaboration by acting as a central communication hub. Implementations vary based on specific needs, but these examples showcase the versatility and value ChatGPT can bring to Kanban.
How can ChatGPT help with managing complex projects that involve multiple stakeholders?
Greg, ChatGPT can assist by centralizing communication, providing real-time updates, and facilitating collaboration among stakeholders. It can help streamline the communication process, ensure everyone is on the same page, and assist with coordinating actions and dependencies. For complex projects, it's important to adapt and configure ChatGPT to fit the specific collaboration needs.
What are the prerequisites for successfully implementing ChatGPT with Kanban?
Emily, before implementing ChatGPT, it's vital to have a solid Kanban foundation in place. This includes defining a clear workflow, establishing effective team communication, and ensuring a good understanding of the overall process. Once you have that, integrating ChatGPT becomes an iterative process of evaluating its benefits, refining its usage, and continuously improving its integration with Kanban.
What are the privacy considerations when integrating ChatGPT into Kanban systems?
David, privacy is vital when using AI systems. Ensure you comply with relevant data protection and privacy regulations. Minimize the collection and storage of unnecessary data, use encryption for sensitive information, and regularly assess and address potential privacy risks. Protecting user privacy and sensitive data should be a priority when integrating ChatGPT with Kanban systems.
What are the main use cases for ChatGPT in the context of Kanban?
Jason, ChatGPT has several use cases in the context of Kanban. It can assist with automating repetitive tasks, providing updates, answering common questions, suggesting improvements or alternative approaches, facilitating communication and coordination, and even acting as a personal productivity assistant. It's versatile and can be tailored to support various aspects of the Kanban process.
Is there any risk of the AI making incorrect interpretations or generating inaccurate suggestions in a Kanban system?
Amy, there is always a risk of AI making incorrect interpretations or generating inaccurate suggestions. It's important to validate and evaluate the AI-generated outputs, apply common sense, and leverage human judgment. Combining AI with human expertise ensures a comprehensive and well-informed decision-making process, minimizing the risk of errors or inaccurate suggestions in a Kanban system.
Are there any alternatives to ChatGPT that can be used to enhance Kanban implementation?
Laura, there are various AI tools and technologies available that can be used to enhance Kanban implementation besides ChatGPT. Some alternatives include other natural language processing (NLP) models, workflow automation software, task management platforms, and collaboration tools. The choice of technology depends on specific requirements, available resources, and the desired level of automation and assistance.
How do you ensure user acceptance and adoption of ChatGPT in a Kanban system?
Sophia, user acceptance and adoption are crucial for successful integration. It's important to involve users from the start, provide clear communication about the benefits, address any concerns or doubts they may have, and offer training and support throughout the adoption process. Incorporating user feedback and continuously improving and fine-tuning ChatGPT can also increase acceptance and usage in a Kanban system.
What are the potential cost implications of integrating ChatGPT in a Kanban system?
Daniel, the cost implications involve various factors, including licensing or subscription fees for AI services, potential development or customization costs, infrastructure requirements, and ongoing maintenance and support. It's important to evaluate the cost-benefit ratio, considering the potential efficiency gains and improvements in productivity that ChatGPT can bring to the Kanban system.
Can ChatGPT be used to analyze Kanban metrics and provide insights for process improvement?
Angela, ChatGPT can be used to analyze Kanban metrics and provide insights for process improvement. By processing and analyzing historical data, it can identify bottlenecks, recommend changes to the workflow, suggest performance enhancements, and assist with continuous improvement efforts. Leveraging AI's ability to analyze large datasets can lead to valuable insights that contribute to optimizing the Kanban process.
What are the scalability considerations when using ChatGPT in a large-scale Kanban implementation?
Christopher, scalability is an important aspect. When scaling a Kanban implementation that includes ChatGPT, it's important to ensure the underlying infrastructure can handle the increased workload and user base. This includes considering factors like computational resources, response times, and overall system performance. Adequate capacity planning and monitoring are vital to maintain a smooth user experience.
What are the risks associated with over-reliance on ChatGPT in a Kanban system?
Nathan, over-reliance on ChatGPT can present risks. If users become too dependent on AI-generated suggestions, they might neglect critical thinking or overlook important aspects. It's crucial to maintain a balance, encourage human judgment, and regularly assess the effectiveness and accuracy of ChatGPT's suggestions. Humans should retain the ultimate decision-making authority in a Kanban system.
What training or resources are needed for teams to effectively use ChatGPT in a Kanban system?
Sophie, effective training and resources are essential. Teams need to understand the capabilities, limitations, and potential use cases of ChatGPT. Providing relevant documentation, training materials, and tutorials is important. Additionally, ongoing support, access to experts, and sharing best practices within the team can help maximize the value teams derive from ChatGPT in a Kanban system.
Are there any known challenges with change management when introducing ChatGPT in an established Kanban process?
Kevin, change management is crucial when introducing ChatGPT to an established Kanban process. Some challenges might include resistance from team members, uncertainty about new roles and responsibilities, and potential disruptions during the transition. Effective change management involves clear communication, involving relevant stakeholders, addressing concerns, providing training, and gradually integrating ChatGPT into the established process.
Thank you all for your valuable questions and discussions! I hope this article and our conversation here help you leverage the power of ChatGPT to enhance your Kanban system implementation. If you have any further queries or need assistance, feel free to reach out.