Enhancing Lean Tools: Leveraging ChatGPT for Effective 5S Implementation
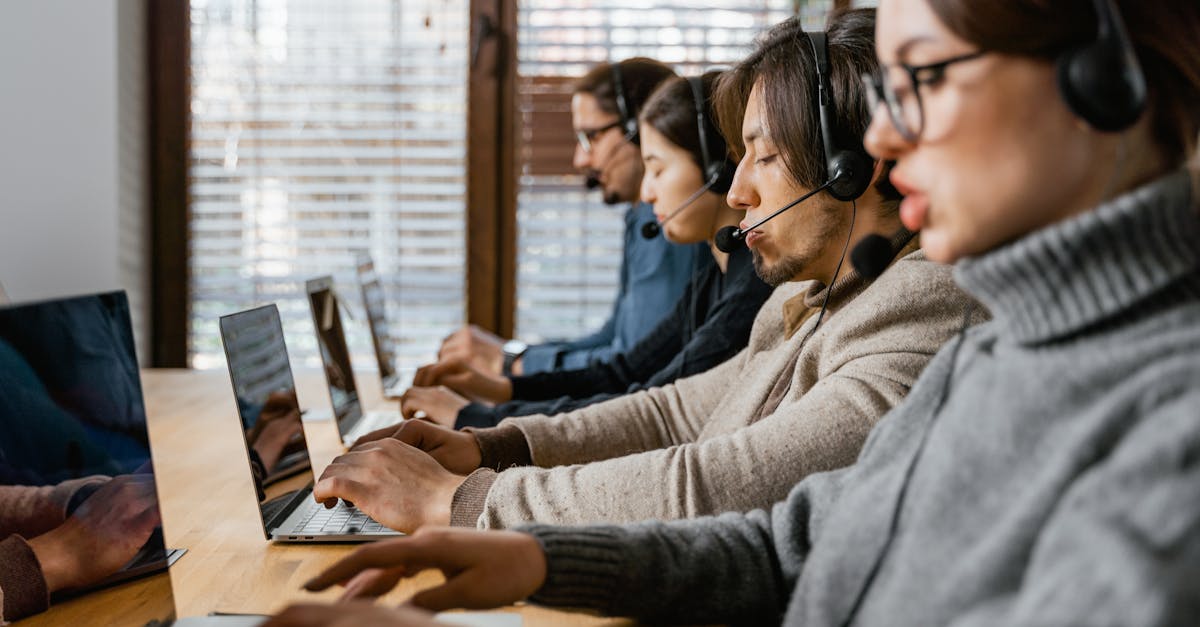
Lean Tools are a set of techniques and principles used in process improvement to eliminate waste and optimize efficiency. One of the most important lean tools is the 5S methodology, which focuses on organizing the workplace for improved productivity and safety. In this article, we will explore how the 5S implementation can assist in managing workplace organization and efficiency.
What is 5S?
The 5S methodology consists of five steps: Sort, Set in Order, Shine, Standardize, and Sustain. Each step represents a specific activity that contributes to the overall goal of achieving a well-organized and efficient workplace.
1. Sort (Seiri)
The first step in 5S implementation is to sort through all items in the workplace and separate what is necessary from what is unnecessary. Unnecessary items are either discarded, recycled, or relocated to a designated storage area. By eliminating clutter and excess inventory, the workspace becomes less chaotic and easier to navigate.
2. Set in Order (Seiton)
Once unnecessary items have been removed, the next step is to organize the remaining items in a logical and efficient manner. Everything should have a designated place and be easily accessible. Clear labels, signage, and visual indicators can be used to make it clear where each item belongs. This reduces wasted time spent searching for tools or materials and improves overall efficiency.
3. Shine (Seiso)
Cleaning and maintenance are essential to ensure a safe and productive work environment. Regular cleaning schedules should be established to keep workstations, tools, and equipment clean and in good working order. By regularly removing dirt, dust, and debris, potential hazards are reduced, and the overall quality of the workplace is improved.
4. Standardize (Seiketsu)
To ensure the sustainability of the first three steps, standardization is crucial. This involves developing and implementing standard operating procedures, visual management systems, and training programs. Standardized processes help maintain organization, promote a consistent work culture, and allow for easier identification and resolution of issues.
5. Sustain (Shitsuke)
The final step in the 5S methodology is to sustain the achieved improvements. This requires ongoing commitment and discipline from all employees. Regular audits and inspections should be conducted to address deviations and reinforce the importance of maintaining a clean and organized workspace.
Benefits of 5S Implementation
Implementing 5S in the workplace offers numerous benefits, including:
- Improved efficiency: By eliminating waste and optimizing workflows, 5S helps streamline processes, leading to increased productivity.
- Enhanced safety: A well-organized workplace reduces the risk of accidents, improves ergonomics, and promotes a safer working environment.
- Cost savings: By eliminating excess inventory and reducing downtime, 5S implementation can result in cost savings for the organization.
- Employee engagement: Involving employees in the 5S implementation process fosters a sense of ownership, empowerment, and accountability.
- Continuous improvement: The 5S methodology provides a solid foundation for further process improvement initiatives, enabling organizations to achieve higher levels of efficiency and quality.
Conclusion
Effective workplace organization and management are critical to achieving operational excellence. The 5S methodology, as a powerful lean tool, offers a systematic approach to implement and sustain workplace organization and efficiency. By utilizing the steps of Sort, Set in Order, Shine, Standardize, and Sustain, organizations can unlock the benefits of a well-organized and productive workplace.
Comments:
Great article, Marcia! I've been using 5S in my workplace, and leveraging ChatGPT sounds like an interesting approach to enhance the implementation process. I'm curious to know more about how it can be integrated into the workflow.
I agree with you, Michael. Integrating ChatGPT into the 5S workflow seems promising. I can envision it helping with organizing and visualizing data during the sorting phase. It could provide suggestions and help maintain consistency throughout the process.
Absolutely, Rachel! ChatGPT's ability to analyze and process data could be a valuable asset during the sorting phase of 5S. It could help identify patterns, recommend optimal item placement, and ensure efficient organization. The possibilities are exciting!
I agree, Michael! The idea of combining Lean tools with AI technology is fascinating. Marcia, could you provide some examples of how ChatGPT can be utilized to improve the 5S implementation? I'd love to learn more!
Thank you, Michael and Rebecca, for your kind words! ChatGPT can be employed in various ways to enhance 5S implementation. For instance, it can assist in generating standardized work instructions, providing real-time guidance in conducting audits, and even help train employees on the principles of 5S. Its natural language processing capabilities make it a valuable tool for streamlining processes and improving efficiency.
I'm still not fully convinced about the effectiveness of using AI in Lean methodologies like 5S. While it may have its advantages, I fear that it could potentially undermine the human aspect of the process. What are your thoughts on this, Marcia?
That's a valid concern, James. AI should never replace human involvement in Lean methodologies. Instead, it should be seen as a supportive tool that complements the efforts of people. ChatGPT, in this context, serves as an assistant that aids in the implementation process, providing guidance and automation where applicable while engaging employees in meaningful ways. The human aspect remains crucial for successful 5S implementation.
I understand your concern, James. However, I believe the human aspect is still crucial in the implementation. ChatGPT can act as an aid, but it's the people who will ultimately execute and maintain the 5S principles. It's all about finding the right balance!
This article has definitely piqued my interest! As someone who works in a manufacturing environment, I can see the potential benefits of leveraging ChatGPT for 5S implementation. It could help us standardize procedures and improve training efficiency. I'm excited to explore this further!
I'm glad to hear that, Emily! The manufacturing industry can greatly benefit from the integration of ChatGPT into 5S practices. It has the capability to streamline processes, reduce waste, and enhance overall productivity. If you have any specific questions or need guidance on implementation, feel free to ask!
I can see how ChatGPT can be valuable in providing real-time guidance during audits. The ability to answer queries and provide suggestions on the spot could speed up the audit process and ensure accuracy. Marcia, have you come across any case studies or practical examples showcasing the successful integration of ChatGPT with 5S?
Absolutely, Sophia! Several organizations have started incorporating AI technologies like ChatGPT into their Lean methodologies, and their success stories are increasingly becoming available. I can share some case studies with you that demonstrate the positive impact of leveraging ChatGPT in 5S implementation. It's encouraging to see the tangible benefits they have achieved!
That would be great, Marcia! Case studies could provide valuable insights into the practical benefits and challenges of implementing ChatGPT for 5S. I'd love to explore those examples and learn from real-world experiences.
Thank you, Marcia! Looking forward to exploring those case studies. Real-world examples can provide valuable insights and help in understanding the practical application of ChatGPT in different industries and organizational contexts.
I'm a bit concerned about the potential cost involved in implementing ChatGPT for 5S. Marcia, in your experience, how feasible is it for small and medium-sized businesses to adopt this technology without breaking the bank?
Cost is indeed an important consideration, Liam. While ChatGPT and other AI tools may have associated expenses, it's worth noting that the cost has been decreasing over time as the technology matures. Cloud-based solutions and subscription models make it more accessible, particularly for smaller businesses. Furthermore, the potential benefits, such as improved efficiency and reduced waste, can often outweigh the initial investment!
I can see the benefits of utilizing ChatGPT for 5S implementation, but I'm also concerned about the learning curve for employees. How user-friendly is ChatGPT, and would extensive training be required to onboard the workforce?
That's a valid concern, Nathan. User-friendliness is vital when integrating new technologies into the workplace. While every organization's experience may vary, modern ChatGPT implementations focus on simplicity and ease of use. The advanced natural language processing capabilities make the interaction more conversational and intuitive, reducing the need for extensive training. Of course, providing some initial guidance and support during the transition would still be beneficial!
Thank you for addressing my concern, Marcia. It's reassuring to know that user-friendliness is a focus in modern AI implementations. The conversational nature of ChatGPT could indeed help facilitate smoother adoption and minimize disruption during the transition.
This article was an eye-opener! I had never considered the potential of AI in Lean methodologies. It makes me wonder, Marcia, do you think ChatGPT or similar AI tools could be integrated into other Lean tools?
Indeed, Olivia! AI technologies hold immense potential to enhance various Lean tools beyond 5S. For example, they can assist in value stream mapping, root cause analysis, and even predictive maintenance. The key lies in identifying areas where AI can augment human efforts and optimize processes. It's an exciting time for Lean practitioners!
Exactly, Marcia! AI could revolutionize how we approach Lean methodologies as a whole. Integrating AI into various tools could lead to more efficient and effective problem-solving, decision-making, and continuous improvement.
I'm intrigued by the potential of AI in Lean methodologies as well. Marcia, do you think there will be any challenges in integrating AI tools like ChatGPT into existing Lean frameworks?
Good question, William! Integrating AI tools into existing Lean frameworks can pose certain challenges. It requires thoughtful planning, proper change management, and ensuring alignment with the organization's goals. Additionally, data access, system integration, and potential resistance to change might be areas to address. However, with thorough planning and engagement of employees, these challenges can be overcome successfully.
Thank you for addressing my question, Marcia! Indeed, careful planning and alignment are essential when integrating AI tools into existing Lean frameworks. Engaging employees and providing proper training and support can ensure a smooth transition and successful integration of ChatGPT or similar tools.
I'm curious to know what kind of support and resources are needed for implementing ChatGPT. Does it require a dedicated IT team or external consultants, or can it be managed within the organization?
Great question, Linda! The level of support and resources required for implementing ChatGPT can vary depending on the organization's size, capabilities, and existing infrastructure. While larger organizations might have dedicated IT teams or consultants to assist with integration, smaller businesses can leverage cloud-based solutions that provide support and training resources. The involvement of employees throughout the process is crucial to ensure successful implementation!
Marcia, I'm curious to know if there are any specific industries where ChatGPT has shown exceptional results when combined with 5S.
Certainly, David! While ChatGPT can be beneficial across various industries, some sectors where it has shown exceptional results in combination with 5S include manufacturing, logistics, healthcare, and service industries. The ability to standardize processes, improve efficiency, and ensure compliance with standardized work instructions proves valuable in these domains.
As an avid proponent of Lean methodologies, I'm excited about the potential of ChatGPT in 5S implementation. Marcia, do you think AI tools like ChatGPT will eventually become a standard part of Lean practices?
Sarah, I share your excitement! While predicting the future is challenging, the current trends suggest that AI tools will play an increasingly significant role in Lean practices. The potential they offer to streamline processes, enhance decision-making, and improve overall efficiency aligns well with the objectives of Lean methodologies. However, it's essential to adapt and integrate these tools thoughtfully based on individual organizational needs.
Marcia, do you have any recommendations on how organizations can approach the integration of ChatGPT into their existing 5S practices? Any specific steps or best practices to keep in mind?
Certainly, Sophie! When integrating ChatGPT into existing 5S practices, it's essential to first define clear objectives and identify areas where AI can enhance the process. Engaging employees from the start and addressing any concerns or questions they may have is crucial. Thorough testing and piloting can ensure a smooth transition, and continuous evaluation of the tool's impact can help refine its implementation. Remember, it's an iterative process!
It's great to see a growing interest in AI's role in Lean methodologies. Marcia, what do you think the future holds for other AI applications in Lean beyond ChatGPT?
Andrew, the future of AI applications in Lean is promising! We can expect to see further integration of AI in areas such as predictive analytics, autonomous systems, virtual assistants, and more. The key lies in leveraging AI's capabilities to augment human efforts, improve decision-making, and drive continuous improvement. As technology evolves, Lean methodologies will evolve with it, benefiting organizations in numerous ways!
Thanks for the response, Marcia! It's interesting to see the wide range of industries where ChatGPT has shown promise. I can see how its capabilities can be leveraged to improve various processes within these sectors. Exciting possibilities!
Thank you for the insight, Marcia! It's good to know that there are different options available based on the organization's resources and capabilities. Involving employees throughout the process will certainly help in fostering acceptance and maximizing the benefits of implementing ChatGPT.
The sorting phase is indeed a critical part of the 5S process, and ChatGPT's assistance could be invaluable. It could quickly analyze items, suggest categorizations, and help maintain consistency in the sorting process. This could save significant time and effort!
I'm glad you see the potential, Julia! ChatGPT can leverage its ability to understand and process natural language to facilitate the sorting phase of 5S. It could help eliminate ambiguity, ensure correct placements, and assist in maintaining an organized workspace. The benefits are indeed promising!
Absolutely! The potential of AI extends beyond just making processes more efficient. It can contribute to better decision-making, continuous improvement, and ultimately, the success of Lean initiatives. Exciting times lie ahead!