Enhancing Lean Tools with ChatGPT: A Breakthrough Approach to Root Cause Analysis
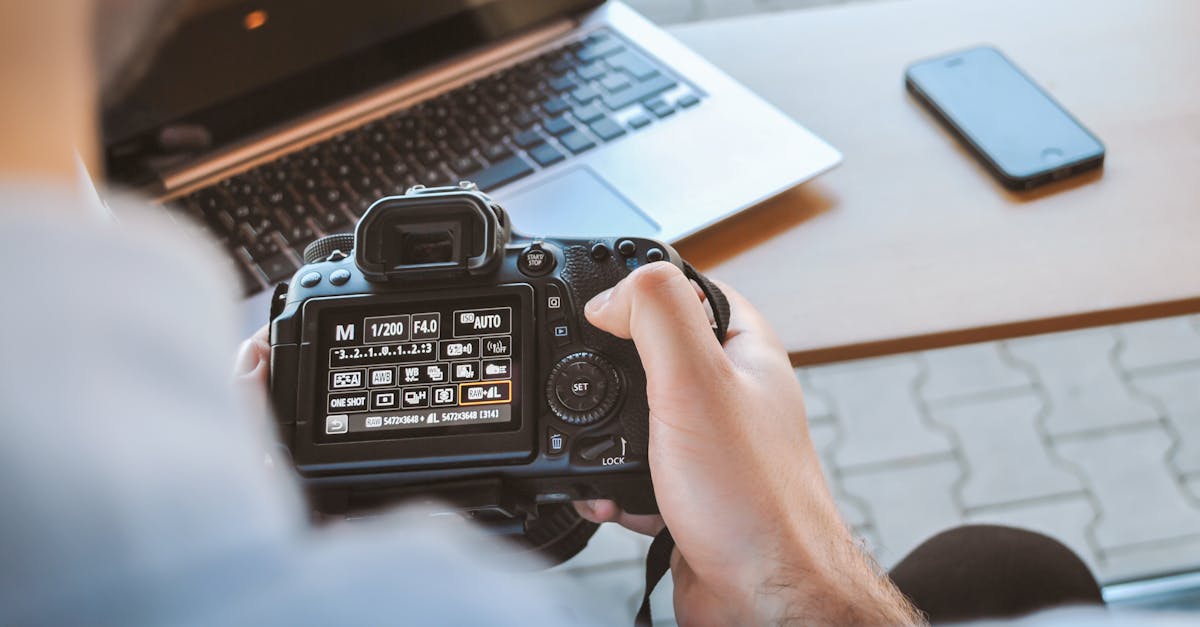
In today's fast-paced and complex business environment, identifying the root causes of problems is crucial for improving processes and achieving sustainable results. Root Cause Analysis (RCA) is a powerful technique used by teams to identify the underlying causes of problems and develop effective solutions. Lean Tools, with their data-driven approach, can greatly enhance the effectiveness of RCA.
Understanding Lean Tools
Lean Tools are a set of principles, methodologies, and practices derived from the Toyota Production System. They are widely used in various industries to eliminate waste, improve efficiency, and drive continuous improvement. Lean Tools emphasize the importance of using data and evidence to make informed decisions.
The Importance of Root Cause Analysis
Root Cause Analysis is a systematic approach to problem-solving that aims to identify and address the underlying root causes of problems, rather than merely treating their symptoms. By identifying the root causes, teams can develop targeted and effective countermeasures, leading to long-term solutions.
Using Lean Tools for Root Cause Analysis
Lean Tools provide a structured framework for conducting RCA, ensuring that teams follow a systematic and data-driven approach. Here are some key Lean Tools that can be utilized:
5 Whys
The 5 Whys is a simple but powerful technique used to identify the root cause of a problem by asking "why" repeatedly. By digging deep into the cause-and-effect relationship, teams can uncover the underlying reasons behind the problem.
Pareto Analysis
Pareto Analysis helps teams prioritize the most significant issues by focusing on the vital few rather than the trivial many. By identifying and addressing the most critical root causes first, teams can achieve quick wins and maximize their efforts.
Cause-and-Effect (Fishbone) Diagram
The Cause-and-Effect Diagram, also known as the Fishbone Diagram, is a visual tool used to explore the various potential root causes of a problem. By categorizing potential causes into specific dimensions such as people, process, equipment, and materials, teams can identify the most likely root causes.
Process Mapping
Process Mapping is a technique that helps teams visualize and understand the steps, inputs, and outputs of a process. By analyzing the process flow and identifying potential bottlenecks or areas of waste, teams can uncover root causes and make informed improvements.
The Benefits of Lean Tools for Root Cause Analysis
By leveraging Lean Tools for Root Cause Analysis, teams can experience several benefits:
- Improved Problem-Solving: Lean Tools encourage a structured and systematic approach to problem-solving, ensuring that teams address the root causes rather than just the symptoms.
- Data-Driven Insights: Lean Tools emphasize the use of data and evidence to drive decision-making. By analyzing the available data, teams can gain valuable insights into the root causes of problems and make informed decisions.
- Efficient Collaboration: Lean Tools provide a common language and framework for teams to collaborate effectively. By utilizing standardized Lean Tools, everyone can contribute to the RCA process, leading to better outcomes.
- Continuous Improvement: RCA is an iterative process that encourages continuous learning and improvement. By using Lean Tools, teams can identify and address root causes, implementing improvements that drive long-term success.
Conclusion
Root Cause Analysis is a critical activity for organizations aiming to improve their processes and achieve sustainable results. By combining the power of Lean Tools with RCA, teams can gain data-driven insights, optimize problem-solving, and drive continuous improvement. Leveraging Lean Tools in Root Cause Analysis can lead to more effective problem-solving, improved collaboration, and ultimately, enhanced organizational performance.
Comments:
This article presents an interesting approach to enhancing lean tools with ChatGPT. I can see how using AI could provide valuable insights for root cause analysis.
@Alice I agree, AI has the potential to revolutionize various aspects of problem-solving. It would be great to see more examples of how ChatGPT can be applied in different industries.
@Alice @Bob I think the combination of lean tools and AI could be really powerful. It could help businesses identify underlying causes more accurately and efficiently.
This article raises an interesting question: how does ChatGPT integrate with existing lean tools? Are there any challenges or limitations in implementing such an approach?
@David That's a great question! Integrating ChatGPT with existing lean tools can provide real-time suggestions and insights. One challenge could be ensuring the accuracy of AI-generated recommendations.
I'm curious about the training process for ChatGPT in root cause analysis. How is the AI model prepared to understand and identify the underlying causes of problems?
@Eve Training AI models like ChatGPT for root cause analysis typically involves feeding it with relevant data from various sources. It learns to identify patterns and make accurate recommendations based on the provided information.
The potential of AI in root cause analysis is tremendous. It can help organizations identify systemic issues and take proactive measures to prevent recurring problems.
@Grace Absolutely! Preventing problems before they occur can lead to long-term cost savings and improved efficiency.
What are the privacy implications of using ChatGPT for root cause analysis? Should companies be concerned about sharing sensitive data with AI models?
@Ivy Privacy is an important consideration when using AI tools. Companies should ensure that appropriate data security measures are in place, and sensitive information is handled responsibly to mitigate any risks.
I wonder if ChatGPT can handle complex scenarios where multiple root causes are interconnected. Sometimes, problems have multiple contributing factors that need to be addressed.
@Jack I believe ChatGPT's ability to process language and understand context can make it capable of handling complex scenarios. It can analyze relationships among various factors and provide actionable insights.
@Katie That's correct. ChatGPT's natural language processing capabilities enable it to identify connections between multiple root causes, facilitating a comprehensive analysis.
One potential drawback I see with relying heavily on AI for root cause analysis is the risk of overdependence. It's crucial to maintain a balance between human expertise and AI-powered insights.
@Alice I agree. AI should serve as a tool to support human decision-making rather than replacing human judgment entirely. Humans bring valuable experience and context to the table.
Would it be feasible to integrate ChatGPT into existing lean tools as a plugin or an additional module? This way, organizations could leverage the benefits without undergoing major system changes.
@David Integrating ChatGPT as a plugin or module is certainly feasible. It would allow organizations to enhance their existing lean tools while keeping their established processes intact.
Do you think ChatGPT has the potential to replace traditional root cause analysis methods? Or would it work more effectively in collaboration with humans?
@Eve While ChatGPT can provide valuable insights, it shouldn't replace traditional root cause analysis methods completely. Human involvement is crucial to verify, interpret, and implement the AI-generated recommendations.
I'm excited to see the practical applications of ChatGPT in root cause analysis. It has the potential to streamline problem-solving processes and drive continuous improvement.
@Grace Indeed! By leveraging AI, businesses can become more proactive in addressing underlying issues and optimizing their operations.
@Harry @Grace I agree with the potential benefits, but we must ensure that AI tools like ChatGPT are unbiased and free from algorithmic biases that could skew the root cause analysis results.
@Ivy You raise an important point. The development and deployment of AI models should prioritize fairness and inclusivity, and regular testing should be performed to detect and mitigate biases.
Are there any limitations to the ChatGPT approach for root cause analysis? What are the scenarios where it might not be as effective?
@Jack One limitation could be the quality of data available for training the AI model. Insufficient or biased data could impact the accuracy of the analysis. Additionally, extremely nuanced or novel scenarios might pose challenges for ChatGPT.
@Katie Agreed. The effectiveness of ChatGPT depends on the quality and relevance of the training data it receives. It's important to constantly monitor and update the model to enhance its performance.
I think one of the benefits of using ChatGPT is its ability to handle unstructured data effectively. Root cause analysis often involves analyzing text, transcripts, and other qualitative inputs.
@Alice That's a valid point. ChatGPT's language processing capabilities make it well-suited for extracting insights from unstructured data, which can be invaluable for root cause analysis.
It's fascinating to see how technology continues to advance problem-solving methodologies. ChatGPT seems like a promising addition to the lean tools repertoire.
@Charlie Indeed, technology has the potential to significantly enhance lean practices. It's exciting to see AI-enabled tools like ChatGPT making their way into various domains.
@David @Charlie I believe embracing technological advancements while keeping a human-centric approach can lead to the best results in problem-solving.
@Eve Well said! A balance between technology and human involvement ensures that we make the most of AI's capabilities while leveraging human expertise to drive meaningful change.
Root cause analysis is a critical process for businesses across industries. Introducing AI-powered tools like ChatGPT can help uncover hidden factors and address problems at their source.
@Frank I completely agree. Identifying and addressing root causes directly can have a significant impact on operational efficiency, quality, and customer satisfaction.
I wonder if ChatGPT has been tested extensively in real-world scenarios for root cause analysis. It would be interesting to see case studies showcasing its effectiveness.
@Harry I'm also interested in real-world examples. Seeing the practical applications of ChatGPT can provide a better understanding of its potential and limitations.
@Ivy @Harry Case studies demonstrating ChatGPT's effectiveness in different industries would indeed be beneficial. Real-world examples can highlight its value and inspire further adoption.
Overall, I'm optimistic about the integration of ChatGPT and lean tools for root cause analysis. It offers a fresh perspective and the potential for more efficient problem-solving.
@Jack I share your optimism. The combination of AI and lean methodologies can contribute to improved decision-making and continuous improvement in organizations.