Enhancing Maintenance Management: A Breakthrough with ChatGPT in Manufacturing Operations Technology
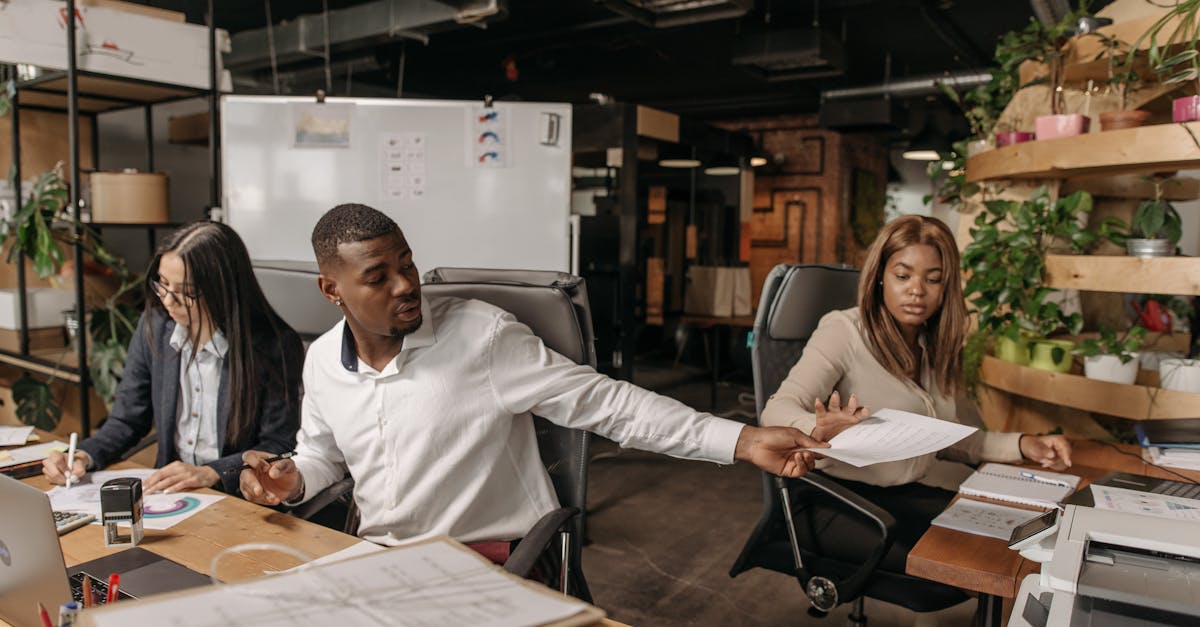
In the fast-paced world of manufacturing operations, downtime can have a significant impact on productivity and profitability. Equipment breakdowns and unscheduled maintenance can halt production lines, causing delays and increased costs. To mitigate the risk of unplanned downtime, manufacturers are turning to advanced technologies in maintenance management.
Manufacturing operations technology, specifically designed for maintenance management, leverages usage data to forecast equipment maintenance needs. By analyzing information on equipment usage patterns, such as running hours, performance data, and historical maintenance records, this technology enables manufacturers to predict and plan for maintenance requirements proactively.
One of the key advantages of using manufacturing operations technology in maintenance management is the ability to identify potential failures before they occur. By monitoring equipment performance in real-time and comparing it with predefined thresholds or historical data, the system can detect anomalies and alert maintenance teams to address the emerging issues promptly. This proactive approach minimizes the risk of unexpected failures, reducing downtime and associated costs.
Moreover, manufacturing operations technology enables manufacturers to optimize scheduled maintenance activities. Traditional maintenance practices often rely on fixed time intervals for servicing equipment, regardless of the actual usage. This approach may result in unnecessary maintenance, causing equipment downtime and not being cost-effective.
With the usage data-driven approach, manufacturers can align maintenance activities with the actual equipment usage. By considering factors such as runtime, load, and operational conditions, the system can determine the optimal timing for maintenance tasks. This lean and efficient approach avoids unnecessary disruptions to production and prevents over-maintenance, resulting in cost savings and improved productivity.
Furthermore, the usage data collected and analyzed by manufacturing operations technology can provide valuable insights into equipment performance and utilization trends. By tracking key performance indicators, manufacturers gain a deeper understanding of the health and efficiency of their assets. This knowledge helps in optimizing maintenance strategies, identifying opportunities for equipment upgrades or replacements, and making informed decisions regarding capital investments.
Implementing manufacturing operations technology in maintenance management requires careful planning and integration with existing infrastructure. The technology often involves sensor-based monitoring devices, data analytics software, and integration with enterprise resource planning (ERP) systems. This ensures seamless data flow, consolidation, and analysis for accurate forecasting and maintenance planning.
In conclusion, the use of manufacturing operations technology in maintenance management revolutionizes traditional approaches by leveraging usage data for proactive maintenance forecasting. By predicting equipment maintenance needs based on usage patterns and performance data, manufacturers can minimize downtime, optimize maintenance activities, and gain valuable insights for strategic decision-making. Embracing this technology empowers manufacturers to enhance productivity, reduce costs, and stay ahead in the competitive manufacturing landscape.
Comments:
Great article! I can see how ChatGPT can revolutionize maintenance management in manufacturing.
Indeed, John! The ability of ChatGPT to assist in real-time decision making seems quite valuable.
I agree, John! The potential of AI in optimizing operations is immense.
Exactly, Jane! AI can help identify patterns and anomalies that may be missed by human operators.
Interesting read! I wonder how ChatGPT compares to other AI solutions in the market.
Mark, from what I've seen, ChatGPT offers a more interactive and conversational approach compared to other solutions.
Michael, have you come across any specific use cases where ChatGPT has outperformed other AI solutions?
Emily, in my experience, ChatGPT has excelled in assisting technicians during complex troubleshooting scenarios.
That's interesting, Michael! It seems like ChatGPT can act like a virtual expert in those situations.
Emily, I've heard of cases where ChatGPT helped reduce average response time for equipment maintenance.
John, a reduced response time can have a significant impact on minimizing equipment downtime.
Emily, definitely! This leads to improved productivity and customer satisfaction.
John, that's a great aspect of ChatGPT that shouldn't be overlooked.
John, improved customer satisfaction through reduced downtime is a significant benefit.
Max, AI-driven maintenance solutions can elevate overall operational performance.
Sarah, operational excellence is indeed a key advantage brought by AI in maintenance management.
Mark, I've seen ChatGPT being used effectively in identifying optimal maintenance schedules based on real-time data.
Alex, I think ChatGPT's ability to adapt and learn from user feedback contributes to its effectiveness.
That's a crucial aspect, Daniel. AI systems must continuously improve to provide accurate insights.
Alex, optimizing maintenance schedules based on real-time data can reduce equipment failures.
Emily, the ability of ChatGPT to provide insights based on historical data is remarkable.
Thank you all for your comments! I appreciate your interest in the topic.
I can imagine ChatGPT reducing downtime and enhancing overall operational efficiency.
That's a good point, Emily! It can be really beneficial for predictive maintenance applications.
AI has so much potential in transforming various industries, and manufacturing is no exception.
I wonder if ChatGPT can be integrated with existing maintenance management software.
I think integration would be possible via APIs, David. It could provide a seamless user experience.
Agreed, ChatGPT's integration potential is crucial in making it a practical solution.
Manufacturing processes can be hectic, and AI can help streamline operations and reduce errors.
AI can provide valuable insights into equipment health, allowing preventive maintenance measures.
Absolutely, Laura! Predictive maintenance can prevent costly breakdowns and save resources.
Karen, AI-powered anomaly detection can indeed boost operational reliability.
Michael, with the sheer volume of data generated in manufacturing, AI becomes indispensable.
Karen, absolutely! AI can enable faster, data-driven decision-making processes.
Mark, AI algorithms can help uncover hidden patterns and correlations in manufacturing data.
Laura, precisely! It empowers manufacturers to make data-driven, informed decisions.
Michael, AI solutions like ChatGPT can contribute to overall operational excellence.
Sarah, having a virtual expert that can provide guidance anytime would indeed be revolutionary.
Emma, indeed! It can enhance troubleshooting capabilities in real-time scenarios.
ChatGPT assisting technicians in real-time troubleshooting sounds really promising!
Indeed, being able to tap into the experiential knowledge of a virtual expert is a game-changer.
Sarah, AI can assist in root cause analysis and help identify unforeseen issues.
Daniel, root cause analysis can help mitigate recurring issues and optimize maintenance efforts.
Karen, predictive maintenance can optimize the use of resources and minimize costs.
John, exactly! Early detection of equipment anomalies can prevent catastrophic failures.
Michael, preventing critical failures can save significant costs and protect worker safety.
Karen, precisely! AI can provide valuable insights for continuous improvement.
Daniel, indeed! AI offers opportunities for continuous improvement and efficiency gains.
Manufacturers can gain a competitive advantage by embracing AI-driven maintenance solutions.
Laura, companies must embrace AI technologies or risk falling behind in the market.