Enhancing Mechanical Fastening in Mechanical Product Design: Harnessing the Power of ChatGPT Technology
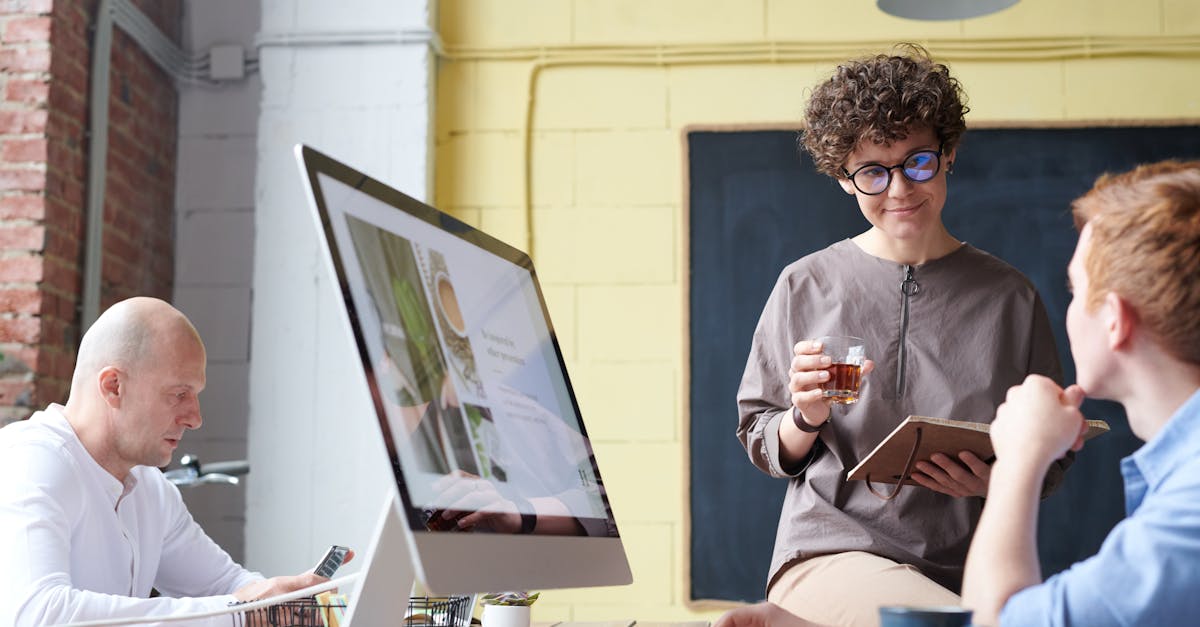
In the field of mechanical product design, selecting the appropriate mechanical fasteners is essential for ensuring the structural integrity and functionality of a product. Different types of fasteners are available for various applications, and it is crucial to understand their characteristics and usage to make informed decisions during the design process.
Introduction to Mechanical Fasteners
Mechanical fasteners are devices designed to secure two or more components together. They provide reliable connections that can withstand various forces such as tension, compression, and shear. Fasteners play a vital role in product design, as they ensure the stability and durability of assembled components.
When it comes to selecting mechanical fasteners, designers need to consider factors such as material compatibility, load-bearing capacity, ease of assembly, and disassembly. By understanding the available options, designers can make informed decisions that optimize the performance and functionality of their products.
Common Types of Mechanical Fasteners
1. Bolts and Nuts: Bolts and nuts offer a secure and versatile fastening solution. They come in various sizes and materials, making them suitable for a wide range of applications. Bolts are threaded cylindrical rods with a head, while nuts are components with an internally threaded hole. This combination allows for easy assembly, disassembly, and adjustment as required.
2. Screws: Screws are similar to bolts but typically smaller in size. They have external threading along their entire length and are commonly used for holding components together or securing objects to surfaces. Screws can be self-tapping, wood screws, or machine screws, each suited for specific applications.
3. Rivets: Rivets are permanent fasteners that are ideal for joining materials such as metal sheets or plates. They consist of a cylindrical shaft with a head that is inserted into pre-drilled holes. The tail end of the rivet is then deformed, creating a secure connection. Rivets offer high strength and reliability, making them suitable for applications where disassembly is not required.
4. Welding: Although not technically a fastener, welding is a widely used method to join metal components. It involves melting and fusing the materials together, creating a permanent bond. Welding offers excellent strength and is particularly suitable for applications subjected to high loads or extreme conditions. However, it requires specialized equipment and expertise.
5. Adhesive Bonding: Adhesive bonding involves using chemical adhesives to join components together. This method offers excellent aesthetics, uniform distribution of stress, and improved resistance to vibration. Adhesive bonding is suitable for a wide range of materials but may not provide the same level of strength as mechanical fasteners in certain applications.
Considerations for Choosing Mechanical Fasteners
When choosing the most appropriate mechanical fasteners for a specific product design, several key considerations must be taken into account:
1. Material Compatibility: Ensure that the chosen fastener material is compatible with the materials being joined. Factors such as corrosion resistance, thermal expansion coefficients, and electrical conductivity should be considered to avoid material degradation or performance issues.
2. Load-Bearing Capacity: Evaluate the expected loads and forces acting on the fasteners to ensure they are capable of withstanding the required strength and durability. Consider factors such as shear strength, tensile strength, and fatigue resistance.
3. Ease of Assembly and Disassembly: Consider the ease of assembly during the manufacturing process and potential disassembly for maintenance, repairs, or upgrades. Quick-release fasteners or those designed for easy installation can save time and effort in the production and maintenance stages.
4. Environmental Factors: Assess the environmental conditions that the product will be subjected to, such as temperature fluctuations, moisture, and exposure to chemicals. Choose fasteners that can withstand these conditions without degradation or undesirable reactions.
Conclusion
Choosing the best mechanical fasteners for product design is a critical aspect of ensuring the structural integrity and functionality of a product. By considering factors such as material compatibility, load-bearing capacity, ease of assembly and disassembly, and environmental factors, designers can make informed decisions that optimize the performance and durability of their designs.
Remember, different mechanical fasteners serve different purposes and offer unique advantages. Therefore, it is important to consult with experts or refer to industry guidelines to select the most appropriate fasteners for specific product designs.
Comments:
Thank you for reading my blog post about enhancing mechanical fastening with ChatGPT technology. I hope you find it informative and engaging. Feel free to share your thoughts and ask questions!
Great article, Jason! The concept of applying ChatGPT technology to mechanical fastening is intriguing. Can you provide more details on how it improves the process?
Michael, ChatGPT technology improves mechanical fastening by quickly generating various design alternatives, optimizing joint configurations, analyzing potential failure modes, and suggesting improvements based on past design knowledge. It helps explore a wider design space efficiently.
Hi Michael, I'm also interested in learning more about the practical implementation of ChatGPT technology. Will it require specialized software or integration with existing CAD tools?
Stephanie, great question! While it depends on the implementation, integrating ChatGPT technology into existing CAD tools is ideal. This allows seamless interaction between the AI system and the designer's workflow, making it more user-friendly and efficient.
Thank you for the clarification, Michael. It's great to hear that ChatGPT can seamlessly integrate with existing CAD tools, making it accessible to a wide range of designers.
I never would have thought to combine AI chat technology with mechanical design. This is really innovative, Jason! Are there any limitations or challenges in implementing it?
Samantha, while ChatGPT technology offers numerous benefits, like any AI system, it has limitations. One challenge is the interpretation of rare or extreme edge cases where the system may provide less accurate results. It's important to have engineering expertise to review and validate the suggestions provided.
Samantha, I wonder if ChatGPT technology could adapt to industry-specific requirements and design standards. Flexibility is crucial for its success. What are your thoughts, Jason?
Christopher, you're absolutely right. Flexibility is vital for ChatGPT technology to adapt to different design standards and industry-specific requirements. Customization and training the AI model on relevant datasets can help achieve this flexibility.
Flexibility and adapting to industry standards are indeed crucial. Thanks for your response, Jason. Exciting times ahead for mechanical design!
Impressive article, Jason. I can see the potential of ChatGPT in mechanical product design. How do you ensure that the technology provides accurate and reliable information?
Ryan, ensuring accuracy and reliability is crucial. A careful evaluation of the AI model, training data, and continuous feedback from domain experts is necessary to minimize errors. Verification and validation processes in the design phase are also essential to verify the reliability of ChatGPT technology.
Ryan, I'm also curious about the potential biases in an AI system like ChatGPT. How do you address the issue of biases and ensure fair and unbiased suggestions?
David, addressing biases is critical in any AI system. By carefully curating training data, maintaining diversity in the dataset, and continuously monitoring and refining the AI model, we strive to minimize biases and ensure the suggestions provided are fair, unbiased, and compliant with industry standards.
I appreciate your thorough approach, Jason. Addressing biases is certainly important to ensure the technology benefits everyone, regardless of their background.
Ryan, besides verification and validation processes, do you perform any post-implementation assessment to further ensure the reliability and accuracy of ChatGPT technology?
Brenda, post-implementation assessment is indeed crucial. It involves monitoring the performance of ChatGPT in real-world usage, collecting user feedback, and continuously refining the AI model based on the observations and feedback received. This iterative process helps to enhance reliability and accuracy over time.
Jason, can ChatGPT technology also assist in identifying potential design flaws or weaknesses in mechanical products? Having early insights could save a lot of effort and costs in the long run.
Kyle, absolutely! ChatGPT technology can analyze the design and provide insights regarding potential flaws or weaknesses, helping designers identify and rectify issues earlier in the process. This can save significant effort and costs, as you mentioned.
That's excellent, Jason. Catching design flaws early in the process could prevent costly mistakes and ultimately lead to better, more reliable products. The potential impact is substantial.
Kyle, you're absolutely right. Identifying and rectifying design flaws early can save both time and resources while enhancing product reliability. The impact of AI technology in this regard is indeed substantial.
Absolutely, Jason. This technology has the potential to disrupt the entire design process, revolutionizing how products are conceived, developed, and commercialized. The future looks promising!
Kyle, I couldn't agree more. The impact of AI technology, including ChatGPT in mechanical product design, is revolutionizing the industry and opening up new avenues for exploration and innovation. Exciting times lie ahead!
Your approach sounds comprehensive, Jason. Continuous refinement based on user feedback is important to keep the technology up-to-date with evolving design needs.
Continuous refinement is essential to keep pace with evolving design needs and ensure the technology remains relevant and useful for designers. Your approach demonstrates a commitment to excellence, Jason.
Thanks for sharing this, Jason. I'm curious to know if ChatGPT can assist in reducing the development time for mechanical products. Is it applicable across different industries?
Emily, ChatGPT technology can indeed help reduce development time by automating certain aspects of the design process, generating design alternatives rapidly, and assisting with simulations and optimizations. It has potential applications across various industries, from automotive to aerospace, and beyond.
Emily, I'm excited about the potential time-saving capabilities of ChatGPT. Do you have any specific examples of how it has improved mechanical product development time in real-life scenarios?
Emma, in real-life scenarios, ChatGPT has been used to assist in generating optimized joint configurations, reducing the number of physical prototypes needed, and providing insightful recommendations for improving the overall design. These capabilities have led to significant time savings in the development process.
That's impressive, Jason. Having fewer physical prototypes can significantly speed up development cycles and save costs. It's exciting to see AI technology revolutionizing mechanical product design.
Emma, ChatGPT's time-saving capabilities are truly remarkable. It's incredible how AI technology is reshaping traditional design processes to make them more efficient and dynamic.
Zoe, you're absolutely right. AI technology, like ChatGPT, is unlocking new possibilities in design processes, enabling more efficient exploration of design alternatives and fostering creativity. It's an exciting time for mechanical product design!
Jason, apart from the limitations, what kind of training or knowledge is required to effectively use ChatGPT technology in mechanical product design?
Andrea, to effectively use ChatGPT technology in mechanical product design, basic knowledge of mechanical engineering principles and design concepts is essential. Familiarity with CAD software and understanding the principles of AI can also help in maximizing the benefits of the technology.
Thank you, Jason. It's good to know that having a basic knowledge of mechanical engineering principles is sufficient for utilizing ChatGPT technology effectively. It seems like an accessible and user-friendly tool.
The time-saving aspects of ChatGPT are fascinating. In terms of the generated joint configurations, how accurate are the suggestions provided by the technology?
Oliver, the accuracy of the generated joint configurations by ChatGPT technology can vary depending on factors like the quality of training data, the model's training and fine-tuning, and the specific design requirements. It's crucial to balance the generated suggestions with engineering expertise and domain knowledge during the design review process.
Jason, regarding biases, can you shed some light on the efforts put into ensuring diverse representation in the training data? Inclusivity is key!
Barbara, ensuring diverse representation in the training data is indeed crucial to avoid biases. Efforts are made to include data from various sources, diverse industries, and different design cultures. Regular monitoring and evaluation are conducted to address biases and promote inclusivity in ChatGPT technology.
The benefits of AI in mechanical product design are immense, Jason. Can ChatGPT technology also help inexperienced designers improve their design skills by providing intelligent suggestions?
Melissa, yes, ChatGPT technology can provide intelligent suggestions to inexperienced designers, helping them learn and improve their design skills. By offering alternative configurations and insights, it serves as a valuable tool for enhancing design capabilities and broadening the designers' knowledge.
That's wonderful, Jason. By empowering inexperienced designers and guiding them towards better design choices, the technology has the potential to foster innovation across the industry.
Melissa, indeed! Empowering inexperienced designers to make informed design choices is one of the key objectives of ChatGPT technology. By democratizing access to design expertise, we can drive innovation and push boundaries in mechanical product design.
Well said, Jason. Breaking down barriers and empowering designers is crucial for continuous innovation. AI technologies like ChatGPT enable designers to explore new horizons and achieve groundbreaking results.
Jason, I appreciate your commitment to ensuring diverse representation in the training data. Promoting inclusivity is commendable and shows responsible AI development.
Promoting inclusivity and diversity in AI development benefits not only the design community but also society as a whole. It encourages unbiased and equitable design practices. Kudos to your efforts, Jason!
Thanks for clarifying, Jason. It's crucial to strike the right balance between AI-generated suggestions and human expertise to ensure that the joint configurations are not only optimized but also reliable.
Balancing AI-generated suggestions with human expertise is crucial, as it ensures the optimization of joint configurations without compromising the reliability and safety of the overall design. Thanks for emphasizing that point, Jason.
Indeed, ChatGPT's accessibility and user-friendliness make it a valuable tool for designers at all levels of expertise. Lowering the entry barrier can lead to more inclusive and diverse design solutions.