Enhancing Mechanical Systems Analysis in Mechanical Product Design with ChatGPT
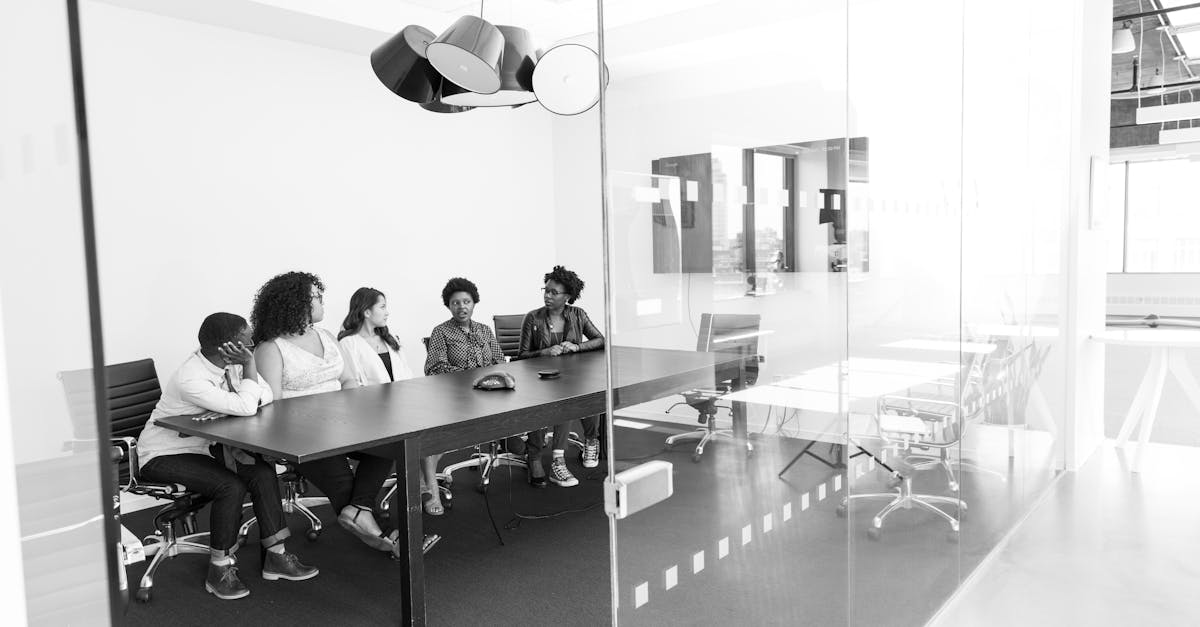
Introduction
Mechanical product design plays a critical role in various industries, including automotive, aerospace, and consumer electronics. It involves designing and developing mechanical systems that are efficient, reliable, and safe. In this article, we will focus on the area of mechanical systems analysis and its importance in analyzing designs as well as offering suggestions for improvement.
Importance of Mechanical Systems Analysis
Mechanical systems analysis involves examining the various components and subsystems of a mechanical design to ensure they function as intended and meet the desired performance requirements. By carefully analyzing these systems, engineers can identify potential issues, such as structural weaknesses, excessive vibrations, or inefficient energy usage.
One of the primary benefits of mechanical systems analysis is the ability to assess the design's overall performance before manufacturing. This analysis helps identify and address any design flaws or inefficiencies early on, thus saving time and resources during the development process. It also enables engineers to optimize the design for improved functionality, durability, and cost-effectiveness.
Process of Mechanical Systems Analysis
The process of analyzing mechanical systems involves several steps that ensure a comprehensive evaluation of the design.
- System Identification: The first step is to identify the key mechanical systems within the overall design. This includes understanding the intended functionality and performance requirements of each system.
- Data Collection: Once the systems are identified, relevant data such as component specifications, operating conditions, and constraints are collected.
- Modeling and Simulation: Using the collected data, engineers develop mathematical models and simulations to replicate the behavior of the mechanical systems. This allows for detailed analysis and prediction of performance.
- Analysis and Evaluation: The models and simulations are analyzed to assess the behavior of the mechanical systems under various conditions and stress factors. This step involves evaluating factors such as stress distribution, energy consumption, and dynamic response.
- Suggestions for Improvement: Based on the analysis results, engineers provide suggestions for improving the design of the mechanical systems. These suggestions may involve material changes, structural modifications, or optimizations in energy usage.
- Prototype Testing: Once the suggested improvements are implemented, prototype testing is conducted to validate the changes and ensure the desired performance improvements have been achieved.
Benefits and Applications
The benefits of mechanical systems analysis extend beyond design optimization. They include:
- Improved reliability and safety: By analyzing mechanical systems, engineers can identify potential failure points and address them before the product is manufactured, ensuring enhanced reliability and safety.
- Efficiency enhancements: Analysis helps identify energy-wasting components or subsystems, allowing engineers to suggest modifications that can maximize efficiency and reduce energy consumption.
- Cost savings: By catching design flaws early on, mechanical systems analysis prevents costly rework or recalls after product launch, saving both time and resources.
- Performance optimization: Analyzing and optimizing mechanical systems can result in improved overall performance, leading to increased customer satisfaction and market competitiveness.
The applications of mechanical systems analysis are far-reaching. It is utilized in industries such as automotive engineering, aerospace, industrial manufacturing, robotics, and consumer electronics, among others. Any field that involves mechanical design and development can benefit from implementing a thorough analysis process.
Comments:
Thank you everyone for reading my article on Enhancing Mechanical Systems Analysis in Mechanical Product Design with ChatGPT. I'm excited to engage in discussions and answer any questions you may have!
Great article, Jason! ChatGPT seems like a valuable tool for mechanical product designers. How exactly does it enhance the analysis process?
Thank you, Marcia! ChatGPT can enhance analysis by providing instant feedback and suggestions based on the input provided. It can help designers identify potential issues, optimize designs, and explore different possibilities more efficiently.
I'm curious about the accuracy of ChatGPT's analysis. How reliable is it in comparison to traditional methods?
That's a great question, Sarah! ChatGPT's analysis is based on pre-trained models that have been trained on vast amounts of data. While it can provide valuable insights, it's important to also consider traditional methods and use ChatGPT as a complementary tool rather than a replacement.
This technology sounds promising, but what are the limitations of ChatGPT in the context of mechanical product design?
Good question, Michael! ChatGPT's limitations include potential biases in the training data, sensitivity to input phrasing, and occasional production of incorrect or nonsensical responses. It's important to use critical thinking and human expertise alongside the tool.
So basically, it's important to use ChatGPT as a supplement and maintain a cautious approach while analyzing the results, right?
Exactly, Olivia! ChatGPT can be highly valuable, but using it alongside human expertise and critical thinking ensures a more accurate analysis in mechanical product design.
Is there a learning curve for designers to effectively utilize ChatGPT in their workflow?
Good question, David! There might be a learning curve in terms of understanding how to best utilize the tool and interpret its outputs. However, OpenAI is working on improving usability and providing clearer guidelines to facilitate a smoother learning process.
How user-friendly is ChatGPT for designers? Will it require technical expertise or coding skills?
Great question, Emma! OpenAI is aiming to make ChatGPT more accessible to users without technical expertise. While some technical understanding can be helpful, they are working towards providing intuitive interfaces that require minimal coding skills.
Are there any plans to integrate ChatGPT with existing design software or platforms?
Absolutely, Daniel! OpenAI is actively exploring partnerships with design software companies to integrate ChatGPT seamlessly into existing workflows. This would make it even more convenient for designers to use the tool.
Do you foresee any ethical concerns or potential misuse of ChatGPT in mechanical product design?
Ethical considerations are crucial, Joanna. While ChatGPT can be a powerful tool, it's essential to use it responsibly and be aware of potential biases in the training data. Organizations must establish guidelines and ensure proper usage to address these concerns.
What steps can organizations take to mitigate biases and ensure responsible use of ChatGPT?
Great question, Catherine! Organizations can implement diversity in training data, perform regular audits to identify and rectify biases, and promote ethical guidelines among designers using ChatGPT. Continuous evaluation and improvement are key.
Are there any specific industries or applications where ChatGPT has already shown significant benefits in mechanical product design?
Good question, Eric! ChatGPT has shown benefits in a range of industries, including automotive, aerospace, consumer electronics, and industrial machinery. Its capabilities make it applicable in diverse mechanical product design scenarios.
Does ChatGPT have any specific features or tools that cater to the unique requirements of mechanical product design?
Absolutely, Ralph! ChatGPT has features like interactive prompts, which allow designers to have guided conversations to get feedback and suggestions. It can also assist in generating CAD models, simulating designs, and optimizing parameters for mechanical systems.
How does ChatGPT handle proprietary or sensitive information related to mechanical product designs?
Great question, Sophia! OpenAI takes privacy and data security seriously. They are actively working on updates to allow users to customize and control ChatGPT's behavior, enabling designers to use it while preserving the privacy of sensitive information.
Considering the potential inaccuracies in ChatGPT's analysis, how do we ensure that errors don't lead to design flaws or failures?
Valid concern, Emily! It's crucial to validate and cross-check ChatGPT's outputs using traditional methods, perform rigorous testing, and have expert human reviews before finalizing designs. Human expertise acts as an important safeguard against design flaws or failures caused by inaccuracies.
In your experience, Jason, could you share any specific success stories where ChatGPT contributed significantly to the design process?
Certainly, Henry! We had a case where ChatGPT assisted in identifying potential fatigue issues in an automotive component, leading to design modifications that significantly improved the product's lifespan. It saved time and resources compared to traditional analysis methods.
Does ChatGPT support multi-disciplinary design analysis, or is it focused on specific areas within mechanical product design?
Good question, Robert! ChatGPT can assist in multi-disciplinary design analysis to a certain extent. While it may not replace domain-specific tools for in-depth analysis, it can certainly provide valuable insights that integrate different perspectives.
As a designer using ChatGPT, how can I ensure that I'm effectively using the tool's capabilities without getting overwhelmed by options?
That's a great concern, Oliver. Developing a clear objective for using ChatGPT and focusing on specific aspects of analysis can help you avoid being overwhelmed. Start with small use cases, gradually exploring additional functionalities as you gain confidence and experience with the tool.
Are there any risks associated with over-reliance on ChatGPT's analysis in mechanical product design?
Absolutely, Gregory! Over-reliance on ChatGPT without cross-checking or validating its outputs using traditional methods can lead to design flaws, suboptimal solutions, or overlooking critical factors. Therefore, it's vital to leverage ChatGPT as a supportive tool instead of relying solely on its analysis.
So, using ChatGPT as an aid rather than a decision-making authority is the way to go?
Exactly, Sophie! ChatGPT empowers designers with valuable insights, but it should be used in conjunction with domain expertise and critical thinking. It's an aid in decision-making but not the sole authority.
Is ChatGPT available for individual designers, or is it more geared towards larger organizations?
Good question, Alex! ChatGPT aims to be accessible to both individual designers and larger organizations. OpenAI is actively working on pricing plans that cater to different user needs, ensuring wide availability and usability.
That's great to hear! I'm an independent designer, and having access to such technology would be a game-changer for my workflow.
Absolutely, Lucy! ChatGPT can indeed revolutionize the design workflow for independent designers like you, offering new possibilities and augmenting your expertise.
Has there been any research exploring the potential impact of ChatGPT on design iteration time?
Good question, Matthew! Research has shown that ChatGPT can significantly reduce design iteration time by facilitating quick feedback and providing alternative suggestions. This can lead to faster design convergence and overall efficiency improvements.
Can ChatGPT be used in real-time simulations or virtual prototyping to enhance the accuracy of predictions?
Definitely, Ryan! ChatGPT's capabilities can be utilized in real-time simulations or virtual prototyping to enhance the accuracy of predictions. By incorporating its analysis, designers can refine their models and simulate optimized mechanical systems more effectively.
Are there any specific requirements in terms of hardware or computing resources to effectively use ChatGPT for mechanical systems analysis?
Great question, Isabella! OpenAI is working towards providing different deployment options to suit a range of hardware and computing resources. While the specifics may vary, they aim to make it accessible without large infrastructure requirements.
That's reassuring! It would be excellent to have flexibility in using ChatGPT without needing extensive hardware upgrades.
Absolutely, Mason! OpenAI wants to ensure accessibility to a wide range of users, keeping hardware requirements as flexible as possible.
In your opinion, what are the most exciting future possibilities for AI-assisted mechanical product design beyond ChatGPT?
Great question, Kevin! AI-assisted design holds immense potential beyond ChatGPT. Machine Learning and AI algorithms can further optimize designs, improve predictive simulations, automate repetitive tasks, and enable collaborative design ecosystems. The future possibilities are truly exciting!