Enhancing MIG Welding with Gemini: Revolutionizing Technology Integration
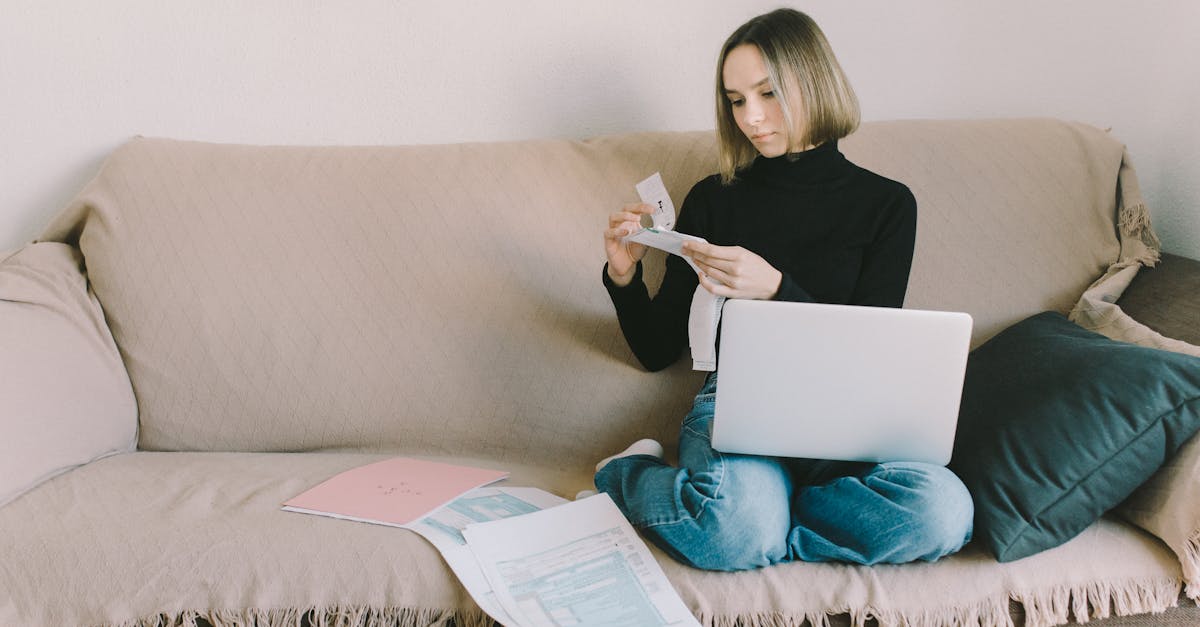
The world of technology is constantly evolving, and in recent years, we have seen significant advancements in various fields. One area that has witnessed remarkable growth is welding technology, particularly with the emergence of MIG (Metal Inert Gas) welding. MIG welding is widely used in industries such as construction, automotive, and manufacturing, given its versatility and efficiency in joining metal pieces together. With the continuous progress in artificial intelligence, specifically with natural language processing models like Gemini, there is immense potential to enhance MIG welding and revolutionize the way we integrate technology into this field.
The Role of MIG Welding in Industrial Applications
MIG welding, also known as Gas Metal Arc Welding (GMAW), utilizes a consumable electrode wire that continuously feeds into the welding gun. As the wire melts, it is deposited to form a weld joint, connecting the workpieces. The process employs an inert gas shield, typically argon or a mixture of argon and carbon dioxide, to protect the weld pool from atmospheric contamination. MIG welding is renowned for its speed, ease of use, and ability to weld different metals, making it a popular choice in various industrial applications.
The Potential of Gemini in MIG Welding
Gemini, developed by Google, is a state-of-the-art natural language processing model that has gained significant attention for its ability to generate human-like text responses. It is trained on a large corpus of text data, allowing it to understand and generate coherent text in response to written prompts. The transformative potential of Gemini lies in its ability to bridge the gap between humans and machines, enabling seamless communication and collaboration. When integrated into MIG welding processes, Gemini can bring numerous advantages and unlock new possibilities.
Benefits and Applications
1. Enhanced Training and Education: Gemini can be used as an interactive training tool for welders, providing them with real-time explanations, troubleshooting tips, and guidance during the welding process. Novice welders can learn from expert responses, improving their understanding and skill set.
2. Quality Control and Predictive Maintenance: By analyzing real-time welding data, Gemini can detect potential defects or irregularities in the process. It can provide insights and recommendations to ensure the weld quality meets the desired standards. Additionally, it can help predict maintenance requirements, reducing downtime and optimizing production efficiency.
3. Remote Support and Collaboration: With the ability to communicate with Gemini through text prompts, welders can access expert guidance remotely. This is particularly beneficial in situations where on-site experts are not readily available, facilitating real-time collaboration and problem-solving.
4. Process Optimization: Gemini can analyze vast amounts of welding data to identify patterns and optimize welding parameters. By suggesting parameter adjustments, it can improve welding efficiency, reduce material waste, and enhance overall productivity.
Challenges and Considerations
While integrating Gemini with MIG welding presents exciting possibilities, there are certain challenges that need to be addressed:
- Ensuring reliable and accurate responses: Gemini should be extensively trained and validated to provide accurate information and responses.
- Managing system integration: The seamless integration of Gemini with existing welding systems, sensors, and automation technologies requires careful implementation and coordination.
- Maintaining cybersecurity: As with any technology integration, robust cybersecurity measures need to be in place to protect against potential vulnerabilities and threats.
- Human-machine collaboration: While Gemini can enhance welding processes, striking the right balance between human expertise and the AI-driven system is crucial to ensure optimal outcomes.
Conclusion
MIG welding, already a highly efficient and versatile welding process, has the potential to benefit immensely from the integration of Gemini. From training and quality control to remote support and process optimization, this technology convergence can revolutionize how welding is approached in various industries. While challenges exist, careful implementation and collaboration can unlock the full potential of this innovative integration. As technology continues to advance, it is essential to explore and harness its capabilities to drive progress and efficiency in industrial processes.
Comments:
Thank you all for taking the time to read my article on 'Enhancing MIG Welding with Gemini'! I am excited to see what you think about the topic.
Great article, Russ! I never knew Gemini could revolutionize technology integration in MIG welding. It's fascinating to see how AI is transforming various industries.
I agree with you, Emily. The potential of AI in welding is immense. It would be interesting to know more about the specific applications of Gemini in enhancing MIG welding techniques.
Absolutely, Michael! Gemini can assist welders by providing real-time guidance, suggesting optimal parameters, and even identifying potential welding flaws. It acts as a virtual welding expert, making the process more efficient and accurate.
Wow, I never thought AI could play such a crucial role in welding. It seems like a game-changer for improving productivity and reducing errors.
I'm a professional welder, and I have my reservations about relying on AI for welding. It's important to maintain manual skills and not become overly dependent on technology.
Jeff, I understand your concerns. AI should be seen as a tool for assistance rather than a replacement for manual skills. It can aid welders by providing valuable insights and suggestions, but it cannot replicate the experience and expertise of a skilled professional.
I find it fascinating how AI is being integrated into so many industries. It's not just about automation; it's about enhancing human capabilities.
Indeed, Lisa. Gemini's ability to learn from vast amounts of welding data and offer customized recommendations can significantly improve the quality of welding projects.
Are there any limitations to using Gemini in MIG welding? It sounds promising, but I wonder if there are any challenges or drawbacks.
Good question, Jonas. While Gemini can be highly beneficial, its recommendations are based on patterns in the training data. In complex scenarios or unique situations, it may not provide the most optimal advice. Human judgment is still valuable in such cases.
I'm curious about the training process for Gemini in welding. How is the AI model trained to understand the nuances and intricacies of MIG welding?
Alexandra, training Gemini involves feeding it massive amounts of welding data, including input sensor readings, output parameters, and expert guidelines. The model learns patterns and correlations, enabling it to provide knowledgeable suggestions in welding scenarios.
I can see how AI integration in welding can improve safety too. Can Gemini identify potential hazards or issues during welding?
Absolutely, John! Gemini can analyze sensor data and real-time feedback to detect anomalies, such as overheating, inconsistent arc length, or improper shielding. Early identification of these hazards can prevent accidents and improve overall welding safety.
As an AI enthusiast, I'm thrilled to see how AI technology like Gemini is making a positive impact in different industries. It's definitely a step toward the future.
I'm concerned about the potential job loss for welders due to AI integration. Could Gemini eventually replace human welders altogether?
George, while AI can bring changes to job roles and tasks, it is unlikely that Gemini or similar technology will replace human welders completely. AI integration should be seen as a tool to enhance skills and improve efficiency, rather than a threat to job security.
I think the combination of human expertise and AI assistance can lead to superior results. Like any technology, it's a matter of how we utilize it.
This article opened my eyes to the potential of AI in welding. It seems to be a win-win situation for both welders and the quality of welding projects.
I'm curious if Gemini can be used for other welding processes besides MIG welding. Can it adapt to different welding techniques?
Great question, Sophia! While the initial focus has been on MIG welding, the potential breadth of Gemini's application in other welding processes, such as TIG and stick welding, is being explored. It can definitely be adapted to different techniques with proper training.
Russ, do you have any insights about the cost implications of integrating Gemini into welding processes?
Jeff, while there might be upfront costs involved in adopting AI technology like Gemini, the long-term benefits outweigh them. Improved productivity, reduced errors, and enhanced welding quality can lead to cost savings and competitive advantages for businesses in the welding industry.
I'm glad to see AI being utilized to enhance existing skills rather than replace them. It addresses many concerns people have about automation taking over jobs.
Are there any ethical considerations that need to be taken into account when using AI in welding or other industrial applications?
Sarah, ethical considerations are crucial when integrating AI. Ensuring AI models are trained on diverse datasets, avoiding bias, and maintaining transparency in decision-making processes are essential. It's important to responsibly develop and use AI technologies.
I wonder if Gemini can be used as a training tool for aspiring welders? Having an AI mentor to provide guidance and feedback would be really helpful.
That's an interesting idea, Laura! Gemini can indeed be used as a training tool to assist new welders, offering real-time suggestions, highlighting potential mistakes, and guiding skill development. It can be a valuable tool in welding education.
I'm curious about the future advancements in AI for welding. What other possibilities do you see beyond Gemini?
Michael, the future holds exciting possibilities. We can explore AI models that can dynamically adapt welding techniques to changing conditions, robots controlled by AI for automated precision welding, and integration of augmented reality (AR) technology to provide real-time guidance during welding processes.
The potential advancements in AI for welding are limitless. It's fascinating to think about the future of this technology and its impact on industries.
Thank you, Russ, for shedding light on the integration of AI in welding. It's an exciting development that has the potential to bring numerous benefits to the industry.
This article left me inspired. It's amazing to witness how AI can transform traditional industries and bring about revolutionary changes.
As an engineer, I'm always looking for innovative ways to improve processes. AI integration in welding seems like a promising avenue for enhancing efficiency and quality.
I imagine AI could also aid in welding research and development, allowing for faster prototyping and testing of new welding techniques.
Absolutely, Sophia! AI can accelerate research and development in welding by simulating different welding scenarios, optimizing parameters, and analyzing the impact of variations. It can significantly speed up the innovation process.
It's fascinating to witness the evolution of welding technology. AI integration holds tremendous promise, and I'm excited to see its widespread adoption in the industry.
AI's ability to continuously learn and improve itself makes it an invaluable tool in welding, where precision and accuracy are critical.
I'm glad that AI technologies like Gemini are being developed to assist, not replace, human welders. It's a great balance between utilizing technology and maintaining manual craftsmanship.
Thank you all for reading my article on enhancing MIG welding with Gemini! I'm excited to hear your thoughts and answer any questions you may have.
Great article, Russ! It's fascinating to see how AI technology like Gemini is being integrated into welding. Can you share some specific examples of how this integration has improved MIG welding processes?
Thank you, Sara! One example is the real-time feedback provided by Gemini. It can analyze welding parameters and alert the welder of any deviations, ensuring optimal weld quality and reducing errors.
This is groundbreaking! I can imagine how helpful it would be to have an AI assistant like Gemini during welding projects. Are there any limitations to its capabilities?
Indeed, Chris! While Gemini is highly advanced, it does have limitations. For example, it may struggle to provide accurate recommendations for complex welding scenarios that involve unique materials or unconventional techniques.
I'm curious about the learning process of Gemini. How does it acquire the knowledge necessary for assisting in MIG welding?
Good question, Lisa! Gemini is trained on a large dataset that includes welding best practices, industry standards, and accumulated welding expertise. It learns to provide assistance by recognizing patterns and finding relevant information within its training data.
I'm wondering about the integration process. Is it complicated to set up Gemini for MIG welding applications?
Setting up Gemini for MIG welding applications involves customizing it to understand welding-specific language and parameters. While it requires some technical expertise, there are guides available to assist in the integration process.
I can see how AI integration can enhance welding efficiency, but does it also have any benefits in terms of safety?
Absolutely, Mark! Gemini can provide real-time safety warnings and reminders. For instance, it can alert welders about potential hazards, remind them to use protective equipment, and promote adherence to safety protocols.
As an experienced welder, I'm curious if Gemini can offer insights and suggestions beyond basic welding techniques. Can it assist with troubleshooting complex welding issues?
Absolutely, Emily! Gemini can help with troubleshooting complex welding issues by analyzing the given problem description and offering potential solutions based on its training. It can also provide references to relevant resources for further assistance.
This is mind-blowing! How widely is Gemini being adopted in the welding industry, and what are the potential future applications?
Gemini is gaining acceptance in the welding industry, James. Many companies are exploring its usage for training new welders, improving productivity, and ensuring high welding standards. Future applications could include automated welding systems with built-in AI assistants.
This article is quite insightful! I wonder if Gemini's assistance can extend to other welding processes like TIG or stick welding?
Thank you, Sophia! While my article focuses on MIG welding, Gemini's assistance can indeed be extended to other welding processes like TIG and stick welding. Its capabilities can be trained and customized to various welding techniques and applications.
I'm curious about the potential cost implications of integrating Gemini into welding setups. Could it be expensive for smaller businesses?
Valid point, Daniel. The cost of integrating Gemini can vary depending on the scale of implementation and customization required. While it might be more challenging for smaller businesses, there could be affordable options tailored to their needs as AI technology advances.
I find it fascinating how AI is transforming various industries. Are there any ethical considerations associated with the use of Gemini in welding or AI integration overall?
Ethical considerations are crucial, Karen. When integrating AI like Gemini, it's essential to ensure data privacy, prevent bias in the training data, and maintain human oversight to avoid reliance solely on AI. Responsible AI integration is key to leveraging its benefits ethically.
Do you think Gemini could eventually replace human welders, or is it designed to work alongside them?
Good question, Ethan. Gemini is designed to complement human welders, not replace them. It enhances their capabilities, provides guidance, and acts as a knowledgeable assistant. Human expertise and experience in welding remain invaluable.
I'm curious if Gemini's suggestions are always accurate, or are there instances where its recommendations may be incorrect?
Gemini strives for accuracy, Linda, but there can be instances where its recommendations may not be entirely correct or optimal for a given situation. Therefore, it's always advisable for welders to validate Gemini's suggestions and use their expertise when making decisions.
This technology sounds amazing! How intuitive is Gemini's user interface, and is it easy for welders to interact with during their work?
Thanks, Michael! Gemini's user interface is designed to be intuitive and user-friendly. It can be accessed via devices like tablets or mobile phones with a clean and simple user interface, allowing welders to interact with it conveniently while working.
I'm intrigued by the potential of AI to revolutionize welding. Are there any research initiatives or ongoing projects in this field that you're aware of?
Absolutely, Olivia! Several research initiatives are exploring AI integration in welding. Advanced robotic welding systems, augmented reality interfaces, and improved welding quality assessment using AI are among the ongoing projects aimed at enhancing welding processes.
It's impressive how AI technologies continue to advance. What are the main factors that led to the successful integration of Gemini into MIG welding?
Great question, Brian! The successful integration of Gemini into MIG welding is primarily attributed to advancements in natural language processing, access to large training datasets, and the collaboration between AI experts and welding industry professionals.
I'm curious about the training and learning time required for Gemini to become efficient in assisting with MIG welding. Could you shed some light on that?
Certainly, Michelle! The training and learning time for Gemini depend on the complexity of the welding domain and the size of the training dataset. It typically requires several weeks to train the model and continuously refine its performance with feedback from welding experts.
I can see how Gemini's real-time feedback can be beneficial, but can it also capture and analyze historical welding data for performance evaluation or predictive maintenance purposes?
Absolutely, Daniel! Gemini can capture and analyze historical welding data for performance evaluation and predictive maintenance. By analyzing patterns, it can identify potential issues, provide insights for process improvement, and help optimize maintenance schedules.
With the continuous advancements in AI, do you envision Gemini evolving into a more comprehensive welding expert system in the future?
Definitely, Jennifer! As AI technology progresses, Gemini has the potential to evolve into a more comprehensive welding expert system. It will continue to learn from user interactions, improve its capabilities, and offer even more valuable insights and assistance in the welding domain.
I'm impressed by the potential benefits of integrating Gemini into MIG welding, but are there any concerns about job security for welders?
Valid concern, Rachel. While Gemini can enhance welding processes, it's important to remember that it complements welders' skills rather than replacing them. Human welders bring expertise, adaptability, and creativity that are essential for complex projects, ensuring their continuous role in the industry.
Thank you for sharing this insightful article, Russ! It's exciting to see how AI like Gemini can revolutionize various industries, including welding.
You're welcome, Alexis! I appreciate your kind words. Indeed, AI integration has the potential to transform industries, and the welding field is no exception. Exciting times ahead!
This shows how technology is driving innovation in unexpected fields. Great read, Russ!
Thank you, Eric! Technology advancements continue to push the boundaries, unlocking possibilities in various domains. I'm glad you found the article informative.
I can imagine how Gemini would benefit both experienced welders and those new to the field. It's like having a welding expert accessible at any time.
Exactly, Laura! Gemini's accessibility and knowledge can be incredibly valuable for welders across experience levels. It empowers newcomers with guidance and provides a quick reference for experienced welders, aiding them in tackling challenges effectively.
Incredible how AI integration keeps expanding, Russ! Can Gemini learn from user welding experiences to improve its assistance over time?
Absolutely, Mike! Gemini can learn from user welding experiences to continually improve its assistance. User feedback, interaction data, and continuous refinement can enhance its knowledge base, making it more effective and attuned to welder's needs over time.
As technology advances, the need for upskilling in the welding industry becomes even more important. Does Gemini also provide educational resources for welders?
Absolutely, Katie! Gemini can provide educational resources for welders, including training materials, best practices, and references. It can contribute to upskilling efforts, supporting welders in their professional growth and knowledge development.
I'm excited about the possibilities Gemini brings to the welding industry. Thank you for sharing this enlightening article, Russ!
You're welcome, Samuel! I share your excitement about the potential of Gemini in welding. It has been my pleasure to share this information and discuss it with all of you.