Enhancing Performance Monitoring in Mining Engineering with ChatGPT: A Game-Changer in Technology Innovation
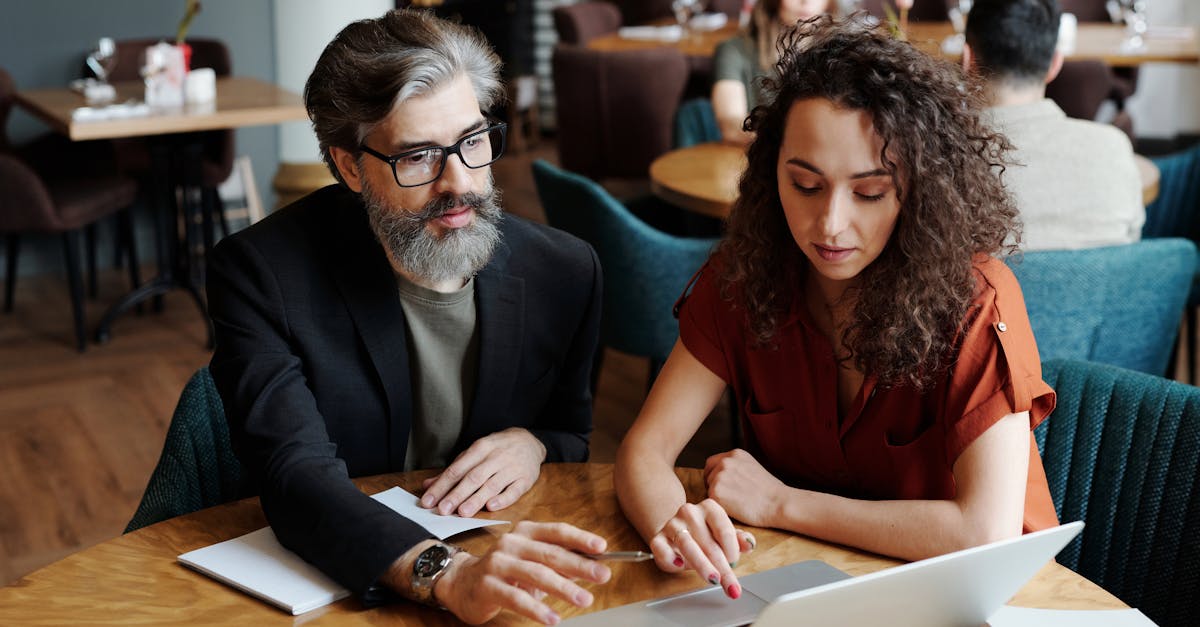
Introduction
In the field of mining engineering, performance monitoring plays a crucial role in ensuring efficient and productive mining operations. With advancements in technology, mining companies now have the ability to track the performance of both equipment and staff in real-time, enabling them to optimize their operations and maximize productivity. This article explores the technology, area, and usage of performance monitoring in mining engineering.
Technology
Performance monitoring in mining engineering relies on various technological advancements. The use of sensors, data analytics, and Internet of Things (IoT) devices have revolutionized the way mining operations are monitored. These technologies enable the collection of real-time data from equipment and staff, providing valuable insights into performance metrics such as productivity, downtime, and efficiency.
Area
Performance monitoring in mining engineering covers a wide range of areas within mining operations. It encompasses the monitoring of individual equipment, such as excavators, haul trucks, and drills, to ensure they are operating optimally. It also includes monitoring the performance of staff, tracking their productivity, adherence to safety protocols, and overall efficiency. Additionally, performance monitoring extends to monitoring the overall performance of the entire mining operation, allowing for identification of bottlenecks and areas of improvement.
Usage
The usage of performance monitoring in mining engineering is multifold. By tracking the performance of equipment in real-time, mining companies can identify potential issues or malfunctions before they lead to costly breakdowns or accidents. They can schedule preventive maintenance based on actual usage and performance data, reducing downtime and increasing overall equipment reliability.
Performance monitoring also allows for the optimization of staff productivity. Real-time tracking of performance metrics enables supervisors to identify and address issues promptly, provide training where necessary, and incentivize high-performing individuals. This, in turn, boosts overall staff morale and operational efficiency.
Another crucial usage of performance monitoring is in improving overall operational efficiency. By analyzing real-time data from equipment and staff, mining companies can identify areas where performance can be optimized. For example, they can make data-driven decisions on equipment deployment, workflows, and process improvements, resulting in increased productivity and cost savings.
Conclusion
Performance monitoring in mining engineering is a powerful tool that enables mining companies to track the performance of both equipment and staff in real-time. By leveraging the advancements in technology, mining operations can achieve higher levels of efficiency, productivity, and cost-effectiveness. Real-time monitoring allows for proactive maintenance, staff optimization, and overall operational improvement, ensuring smooth and profitable mining operations.
Comments:
Great article! The use of ChatGPT in mining engineering sounds fascinating.
I agree, Michael! It's amazing how technology is revolutionizing different industries.
Indeed, Sophia. The advancements being made in performance monitoring are crucial for safety and efficiency in mining.
David, do you think the implementation of ChatGPT can reduce human error in mining operations?
Absolutely, Roger. ChatGPT can handle vast amounts of data and provide real-time insights, minimizing the chances of human error.
I agree with David. It can also alert mining engineers to potential risks and help prevent accidents.
Absolutely, David. I'm curious about how ChatGPT can specifically enhance performance monitoring in mining engineering.
I think ChatGPT can help by analyzing complex data and identifying patterns that may not be easily noticeable to humans, Emma.
This technology can definitely assist in early detection of potential issues and ultimately improve the overall performance of mining operations.
Oliver, can you give an example of how ChatGPT can detect issues in mining operations?
Sure, Emma. ChatGPT can analyze data from various sensors and equipment to detect anomalies like abnormal vibrations or temperature variations in real-time.
That's impressive, Oliver. It could help prevent equipment failures and potential accidents.
I agree, Oliver. It has the potential to save time and resources while ensuring safety.
Thank you all for your comments! I appreciate your interest in the topic.
Andrew, how do you envision the future of performance monitoring in mining with technologies like ChatGPT?
Michael, I believe the future will see mining operations embracing AI technologies like ChatGPT as standard practice for efficient and safe performance monitoring.
Andrew, do you think there might be any challenges during the implementation phase of ChatGPT in mining engineering?
Sophia, there might be challenges related to data integration, system compatibility, and training the workforce to effectively utilize the technology.
I agree, Andrew. Ensuring seamless integration and providing comprehensive training will be critical in the successful adoption of ChatGPT.
Andrew, how long do you think it will take for ChatGPT and similar technologies to become widely adopted in mining engineering?
Roger, the adoption rate will depend on factors like industry readiness, cost-benefit analysis, and successful case studies. It may take several years, but the potential is immense.
Andrew, it's always inspiring to engage in discussions where ideas are exchanged constructively. Thank you for facilitating this engaging conversation.
Sophia, thank you for your kind words. I'm glad I could provide a platform for this enriching dialogue. Your active participation contributed significantly to the quality of the discussion.
Andrew, thank you for sharing this informative article. It's exciting to envision a future where mining engineering incorporates these cutting-edge technologies.
You're welcome, Michael. I'm glad you found it interesting. The possibilities for technology-driven advancements in mining engineering are indeed fascinating.
Andrew, I'm excited to see how technology like ChatGPT will transform the mining industry in the coming years.
Michael, it's a thrilling time for mining engineering. The integration of AI technologies holds immense potential for enhanced performance monitoring and operational efficiency.
Andrew, your article sheds light on the promising integration of AI technology in mining engineering. Well done!
Andrew, the potential benefits and advancements that ChatGPT offers to the mining industry are truly game-changing.
Thank you, Michael. I believe that AI technologies like ChatGPT will drive a new era of efficiency and sustainability in mining engineering.
Michael, I'm excited to see how ChatGPT can revolutionize the field of mining engineering. The potential seems enormous.
I completely agree, Michael. The utilization of ChatGPT can greatly benefit performance monitoring in mining engineering.
Emily, I'm particularly excited about the potential for real-time insights that ChatGPT can provide. It can revolutionize decision-making processes in mining.
Jane, I completely agree. ChatGPT has the potential to revolutionize mining engineering and pave the way for innovative practices.
Michael, the advancements in AI bring exciting possibilities for the mining industry. It's fascinating to imagine how ChatGPT will shape its future.
Michael, indeed. The potential for AI technologies like ChatGPT to revolutionize various industries, including mining, is truly remarkable.
Andrew, the integration of AI has the potential to create a paradigm shift in how we approach and optimize mining operations.
Andrew, I hope to see more advancements and successful implementations of ChatGPT in mining engineering in the near future.
Emily, as the technology continues to evolve, I'm confident that ChatGPT and similar AI tools will drive significant improvements in the mining industry.
Andrew, thank you for sharing such an insightful article. It has sparked an engaging discussion on the exciting possibilities of ChatGPT in mining engineering.
You're welcome, Emily. I'm thrilled to see the enthusiasm and thoughtful insights shared in this discussion. Thank you all for your contributions.
Andrew, we appreciate your article and the opportunity to discuss the potential impact of ChatGPT in the mining industry. It's been an excellent exchange of ideas.
Michael, I'm glad you found the article and discussion valuable. It's been a pleasure to witness such thoughtful contributions from everyone involved.
Andrew, thank you for initiating this insightful conversation. The collective knowledge and perspectives shared here have enriched our understanding of ChatGPT's potential in mining engineering.
David, I couldn't have asked for a more engaging and insightful discussion. I'm grateful for the participation of each person and their valuable contributions.
Michael, I wonder if ChatGPT can be combined with other AI technologies to further enhance performance monitoring.
Absolutely, Sophia. Integration with technologies like computer vision or predictive analytics can provide even more comprehensive insights.
That sounds promising, Michael. Combining different AI tools can unlock new possibilities for mining engineering.
I'm wondering how reliable the analysis of ChatGPT can be in such high-stakes environments.
That's a valid point, Erica. The reliability and accuracy of the technology should undergo rigorous testing and validation.
How user-friendly is ChatGPT for mining engineers who may not have extensive technical backgrounds?
Good question, Erica. The system can be designed with an intuitive interface and simple commands to ensure ease of use.
Erica, the analysis becomes more reliable as ChatGPT is trained on vast amounts of mining-specific data and validated for accurate performance.
That's reassuring, Emily and Sophia. Making it user-friendly is crucial for widespread adoption.
Additionally, mining engineers can be trained on how to effectively interpret and utilize the generated insights from ChatGPT.
Sophia is right. Adequate training and support are essential for mining engineers to leverage the potential of ChatGPT.
How cost-effective is the implementation of ChatGPT compared to traditional monitoring methods?
Good question, Roger. While the initial investment may be significant, the long-term benefits of enhanced performance monitoring with ChatGPT can outweigh the costs.
To add to Sophia's point, implementing ChatGPT can reduce downtime, improve productivity, and ultimately lead to better profitability.
That's a great advantage, Oliver. The return on investment (ROI) for implementing ChatGPT could be substantial.
I agree, Michael. It's crucial to consider the long-term benefits rather than just the initial costs.
Oliver, how customizable is ChatGPT to different mining engineering needs and requirements?
Emma, ChatGPT can be fine-tuned and customized to adapt to specific mining operations, considering factors like different types of equipment and environmental conditions.
That's fantastic, Oliver. A flexible and customizable system ensures optimal utilization across various mining sites.
Oliver, are there any ethical considerations to keep in mind when implementing ChatGPT in mining engineering?
Emma, ethical considerations include responsible data handling, ensuring unbiased algorithms, and addressing potential job displacement concerns.
That's an important point, Oliver. It's essential to strike a balance between technological advancement and ethical principles in mining operations.
Oliver, what kind of expertise is required to implement and manage ChatGPT in mining operations?
Erica, expertise in data science, mining engineering, and AI technology would be required for successful implementation and management of ChatGPT.
It seems like a multidisciplinary approach is necessary to fully leverage the potential of ChatGPT in mining engineering.
Sophia, I couldn't agree more. Collaboration between mining experts, data scientists, and AI specialists is key.
David, can ChatGPT also assist in identifying mineral deposits or optimizing mining processes?
Roger, indeed. With its ability to analyze geological and operational data, ChatGPT can contribute to identifying favorable mineral deposits and optimizing mining processes.
That's fantastic, David. It opens up new possibilities for efficient resource utilization in mining.
Roger, it can significantly reduce human error, but human expertise will still be necessary to interpret and act upon the insights provided by ChatGPT.
David, I feel the combination of human expertise and AI-driven insights will create a powerful synergy in mining operations.
Definitely, Sophia. Leveraging the strengths of multiple AI technologies can amplify their benefits and drive innovation in mining engineering.
Sophia, that synergy between humans and AI can pave the way for more efficient and sustainable mining practices.
Indeed, Roger. The future of mining engineering looks promising as we harness the potential of AI and human intelligence together.
Roger, there may also be additional cost savings in terms of preventive maintenance and optimized resource allocation through the use of ChatGPT.
Absolutely, David. It's crucial to consider the ethical implications of AI implementation in complex and high-stakes industries like mining.
Sophia, I agree with David. Collaboration and knowledge-sharing among experts will be vital in maximizing the benefits of ChatGPT in mining engineering.
Ethical considerations should be at the forefront while implementing any AI technology, including ChatGPT, in mining engineering.
I'm looking forward to seeing more case studies and real-world implementations of ChatGPT in mining engineering.
Erica, case studies can provide valuable insights into the practical applications and benefits of ChatGPT in mining engineering.
Absolutely, Emma. Real-world implementations and success stories will be essential for establishing confidence in the technology.
Erica, it would be ideal to have a team that combines domain knowledge with AI expertise to maximize the benefits of ChatGPT.
Oliver, responsible AI deployment ensures that the benefits of technologies like ChatGPT outweigh any potential negative consequences.
Emma, case studies indeed provide evidence for the practicality and effectiveness of ChatGPT in real-world mining scenarios.
Erica, making the interface intuitive and user-friendly will indeed facilitate the acceptance of ChatGPT by mining engineers.
Oliver, ethical considerations need to be at the forefront to ensure responsible and sustainable implementation of ChatGPT in mining engineering.
Oliver, the ability to detect potential issues in real-time can prevent costly downtime and ensure uninterrupted mining operations.
Michael, that's correct. Proactive detection and prevention can save significant resources and minimize the environmental impact of mining.
Oliver, the ability to customize ChatGPT to suit different mining engineering needs is crucial for its successful integration.
Sophia, indeed. Each mining site may have unique requirements, and adapting ChatGPT to those needs will maximize its effectiveness.
Oliver, having a multidisciplinary team with domain knowledge and technical expertise can ensure the successful implementation and management of ChatGPT.
Erica, user-friendliness will play a significant role in driving the adoption of ChatGPT among mining engineers.
Emily, a user-friendly interface can minimize the learning curve and make the technology accessible to a wider range of mining professionals.
Oliver, a cross-functional team approach can contribute to addressing potential implementation challenges and ensuring the success of ChatGPT in mining engineering.
Sophia, I absolutely agree. Collaboration and expertise across domains will be crucial for a smooth integration of ChatGPT.
Erica, reliability can be enhanced by combining ChatGPT with traditional monitoring methods to cross-validate the results.
Sophia, the synergy between technology and mining engineering can lead to remarkable advancements. ChatGPT is a remarkable innovation.
Oliver, a cross-functional team approach can also help in overcoming potential implementation challenges and ensuring successful integration of ChatGPT.
Sophia, collaboration and collective expertise will drive the successful implementation of ChatGPT and similar technologies in mining engineering.
David, reducing human error is crucial in mining operations. ChatGPT sounds like an important step towards achieving that.
David and Roger, combining the strengths of humans and AI can create safer and more efficient mining environments with reduced operational risks.
Collaboration and knowledge-sharing between experts is crucial to fully embrace the possibilities of ChatGPT in mining engineering, as you mentioned, David.
Sophia, leveraging AI can alleviate human error, allowing mining engineers to focus on more complex tasks and critical decision-making.
David, exactly! By reducing human error, ChatGPT can help mining experts allocate their time and efforts more efficiently.
Sophia, indeed. The collaboration between humans and AI systems can lead to more sustainable and responsible mining practices.
David, the potential for ChatGPT to optimize mining processes and identify mineral deposits makes it an invaluable tool for the industry.
David, interdisciplinary collaboration is key to unlocking the full potential of AI technologies like ChatGPT in mining engineering.
Sophia, combining human expertise with the analytical power of ChatGPT can lead to effective decision-making for mining operations.
Absolutely, Emma. Augmenting human intelligence with AI capabilities can result in safer, more efficient, and sustainable mining practices.
Emma, showcasing successful implementations can be a catalyst for wider adoption, driving innovation and progress in mining engineering.
Emily, real-world case studies will not only demonstrate the technology's benefits but also address any concerns and skepticism surrounding its implementation.
Emma, case studies and practical examples can go a long way in building confidence and encouraging mining industry leaders to embrace ChatGPT.
Exactly, Erica. Real-world implementations will help dissolve any doubts and pave the way for further advancements in mining engineering.
Emily, real-world case studies that showcase the practical benefits of ChatGPT will be instrumental in overcoming any initial skepticism.
Indeed, Emma. Demonstrating tangible results with ChatGPT in mining operations will gain industry-wide attention and drive adoption.
Emily, real-world implementations coupled with ongoing research and development will be crucial in shaping the future of mining engineering with ChatGPT.
Absolutely, Erica. A continuous focus on innovation and improvement will ensure the technology's continuing relevance and effectiveness.
Emma, combining the analytical capabilities of ChatGPT with human intuition and domain expertise can lead to informed decisions and better outcomes in mining operations.
David, the integration of human judgment with AI-driven insights can strike a balance between technological capabilities and the specific needs of mining engineering.
Emma, showcasing successful implementations can inspire other mining industry leaders to explore the potential of ChatGPT and accelerate its widespread adoption.
Exactly, Sophia. Success stories inspire confidence and help overcome initial skepticism about the capabilities of ChatGPT in mining engineering.
Sophia, responsible AI deployment should also address potential biases in data and algorithms to ensure fairness and inclusivity in mining engineering.
Oliver, absolutely. Ethical considerations should encompass transparency, fairness, and ensuring unbiased outcomes in the deployment of AI technologies like ChatGPT.
Sophia, addressing biases is key to building trust and ensuring the equitable utilization of AI technologies in the mining industry.
David, I completely agree. Responsible AI development should actively combat biases and promote fairness in decision-making processes.
David, ensuring diversity in data collection and continuous monitoring of algorithmic biases are crucial steps towards responsible AI implementation in mining engineering.
Oliver, excellent point. By proactively addressing biases and continuously monitoring AI algorithms, we can mitigate potential social and ethical risks.
Oliver, diversity in data collection is indeed crucial. It helps avoid reinforcement of biases and leads to more balanced and inclusive decision-making.
Sophia, exactly. Ensuring diversity in data collection is a means to promote fairness, accuracy, and encompass the interests of various stakeholders in mining engineering.
Sophia, with diverse and representative data, ChatGPT can better identify and address potential biases, contributing to responsible and unbiased decision-making.
David, absolutely. Diverse data ensures that AI technologies like ChatGPT provide fair and unbiased insights, fostering trust in their usage.
Sophia, collaboration and cooperation between multiple stakeholders, including mining companies, AI researchers, and policymakers, will be pivotal in ensuring ethical AI development and deployment.
Oliver, I agree. Engaging all stakeholders in the conversation will help shape responsible deployment guidelines for AI technologies like ChatGPT in mining engineering.
Sophia, collaborative efforts will not only result in responsible AI development but also help address concerns and build public trust towards AI applications in mining engineering.
David, I couldn't agree more. Collaboration is the key to ensuring that AI technologies are beneficial for everyone and address societal needs.
David, building public trust in AI technologies requires open dialogue, transparency, and actively involving stakeholders in decision-making processes.
Oliver, you're absolutely right. Openness and transparency are fundamental to ensure AI technologies are developed and deployed responsibly, with the best interests of all in mind.
Oliver, involving stakeholders early on in the development and deployment of AI technologies can address potential concerns and ensure a responsible and inclusive approach.
Sophia, exactly. Engaging stakeholders fosters trust, ensures diverse perspectives are considered, and promotes the responsible implementation of AI in mining engineering.
Oliver, involving stakeholders also allows for checks and balances, ensuring AI technologies remain aligned with the societal, ethical, and environmental goals of the mining industry.
David, absolutely. Collaborative decision-making involving stakeholders helps address potential risks and ensures responsible AI implementation in mining engineering.
Sophia, building public trust necessitates proactive efforts to educate stakeholders about AI technologies, their benefits, and ethical considerations in the mining industry.
Oliver, educating stakeholders about AI technologies and engaging in responsible practices will foster positive perception and acceptance of such tools in mining engineering.
Oliver, responsible implementation of AI technologies must include transparency, accountability, and continuous evaluation to adapt to changing societal needs and concerns.
Sophia, I completely agree. Responsible AI deployment requires an ongoing commitment to ensure that technologies like ChatGPT align with evolving ethical standards.
Oliver, alongside ethics, the transparency of ChatGPT's decision-making process is crucial to build trust among mining engineers and stakeholders.
Emily, transparency enables mining engineers to understand how ChatGPT reached its conclusions and builds trust in the technology's reliability and fairness.
Sophia, showcasing practical examples will enable companies to evaluate ChatGPT's potential and make informed decisions about its implementation in mining engineering.
Erica, real-world implementations are crucial for companies to witness the actual benefits of ChatGPT in improving their mining efficiency and decision-making processes.
Sophia, diversity in data collection is essential to avoid the perpetuation or amplification of underlying biases, ensuring fairness and accuracy in AI systems such as ChatGPT.
Oliver, absolutely. Incorporating diverse perspectives and inclusive datasets is fundamental to ensuring AI systems like ChatGPT are free from biases and produce reliable results in mining engineering.
Sophia, as mining operations impact various stakeholders, ensuring unbiased decision-making through diverse data collection is fundamental for responsible and inclusive AI implementation.
David, exactly. The inclusion of diverse data sets reduces the risk of AI technologies perpetuating biases and safeguards against unintended consequences in mining engineering.
David, involving policymakers in discussions around responsible AI deployment will help create regulations that balance innovation and societal interests in the mining industry.
Oliver, a collaborative approach that includes policymakers is essential to ensure that the adoption of AI technologies is aligned with legal and ethical considerations in mining engineering.
David, involving policymakers will help shape responsible AI regulations and ensure that the benefits of ChatGPT are realized while mitigating potential risks.
Sophia, policymakers play a crucial role in maintaining a balanced and inclusive approach to AI implementation, fostering trust and advancing responsible practices in the mining industry.
Sophia, educating stakeholders about the potential and limitations of AI technologies in mining engineering can promote realistic expectations and informed decision-making.
Oliver, exactly. Education and awareness will enable mining industry professionals to adopt AI technologies like ChatGPT with an understanding of their capabilities and limitations.
Sophia, educating stakeholders about the capabilities and limitations of ChatGPT will help manage expectations and promote responsible utilization of the technology within mining engineering.
David, raising awareness about AI technologies fosters a more knowledgeable and receptive environment, where the true potential of ChatGPT in mining engineering can be realized.
Oliver, transparency in ChatGPT's decision-making process will be crucial in building trust among mining engineers when interpreting generated insights.
Sophia, transparency and explainability are indeed pivotal aspects that need to be prioritized to foster trust and acceptance of AI technologies like ChatGPT in mining engineering.
Sophia, enabling mining engineers to understand and interpret ChatGPT's decision-making process will empower them to make well-informed decisions based on the generated insights.
David, precise interpretation of ChatGPT's insights is crucial in the mining industry. Empowering engineers to understand its decision-making process enhances their utilization of the technology.
David and Sophia, precise interpretation of ChatGPT-generated insights coupled with an understanding of its underlying mechanisms will enable mining engineers to leverage its full potential effectively.
Oliver, I agree. By ensuring that mining engineers have a clear understanding of ChatGPT's decision-making process, they can make informed judgments and actionable decisions based on the insights provided.
Erica, the reliability of ChatGPT's analysis will likely improve further as the technology evolves and undergoes continuous refinement in mining engineering.
Michael, I agree. The iterative nature of technology development will surely enhance the reliability and accuracy of ChatGPT in monitoring mining operations.
Michael and Sophia, you both make valid points. As AI technologies evolve, they can overcome limitations and become even more robust and reliable.
Erica, that's absolutely true. Continuous improvement and refinement are inherent in the development of AI, providing prospects for enhanced reliability in mining engineering.
David, optimizing resource allocation and preventive maintenance through ChatGPT's insights can lead to substantial cost savings for mining companies.
Emma, indeed. By leveraging ChatGPT's capabilities, mining companies can optimize their operations, reduce expenses, and enhance profitability.
David, optimizing mining practices through AI-driven insights not only improves operational efficiency but also minimizes environmental impacts. It's a win-win.
Roger, exactly. By adopting technologies like ChatGPT, the mining industry can strive towards more sustainable and responsible resource extraction.
David, adopting sustainable practices is becoming increasingly important in the mining industry. ChatGPT can help in striking a balance between resource extraction and environmental concerns.
Roger, that's so true. Responsible resource extraction is a shared responsibility, and advanced technologies like ChatGPT can contribute to achieving that.
David, the ability of ChatGPT to identify mineral deposits could facilitate more efficient and sustainable mining practices, benefiting both the industry and the environment.
David, proper training and support can empower mining engineers to make the best use of ChatGPT's insights for improved performance monitoring.
Sophia, training programs can help bridge the gap between technical expertise and mining engineering requirements, maximizing the potential of ChatGPT.
Sophia, cross-validation with traditional monitoring methods is a great way to enhance the reliability of ChatGPT's analysis in mining engineering.
Erica, combining the strengths of AI and traditional methods can provide a comprehensive and robust performance monitoring framework for the mining industry.
Sophia, interdisciplinary collaboration and knowledge-sharing will lead to innovative solutions and drive the future of mining engineering.
Absolutely, Emily. Collaboration allows us to leverage collective expertise and push the boundaries of what is possible in mining engineering.
Emily, practical examples can provide concrete evidence and illustrate the tangible benefits of ChatGPT in the challenging mining environment.
Erica, concrete examples can help mining industry leaders envision the possibilities and understand the specific advantages ChatGPT can bring to their operations.
Erica, user-friendly interfaces and comprehensive training programs can make the adoption of ChatGPT a smoother transition for mining engineers.
Emily, showcasing successful and practical implementations of ChatGPT will play a vital role in encouraging its widespread adoption.
Emma, hearing real-world success stories with ChatGPT in mining engineering will surely spur industry-wide adoption and advancements.
Ensuring ethical practices and addressing potential job displacement are essential considerations when implementing AI technologies like ChatGPT.
Ensuring ethical practices and responsible deployment of ChatGPT will be critical to gain trust and acceptance from the mining industry and broader society.
Oliver, responsible AI deployment is crucial so that ChatGPT can contribute to a more sustainable and responsible mining industry.
Oliver, the responsible deployment of ChatGPT in mining engineering will play a vital role in maximizing its benefits and minimizing potential drawbacks.