Enhancing Prototype Development in GD&T Technology: Leveraging ChatGPT for Efficient Communication and Collaboration
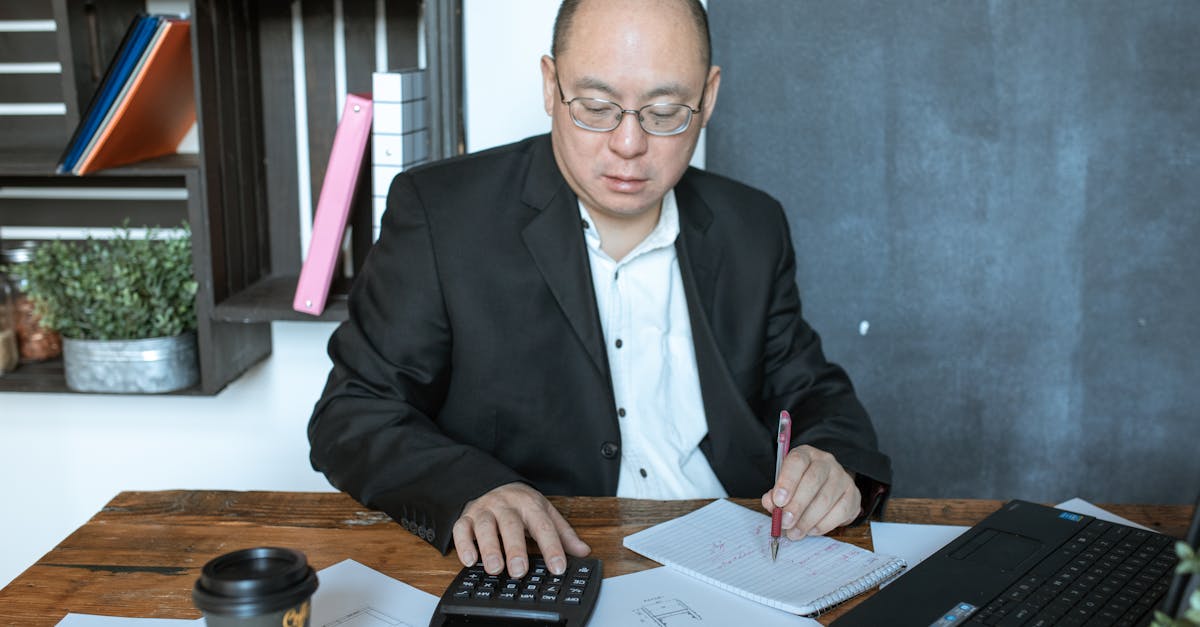
Geometric Dimensioning and Tolerancing (GD&T) is a system used to define and communicate engineering tolerances and specifications for the design and manufacturing of products. It provides a common language and set of rules for engineers, designers, and manufacturers to ensure that components and assemblies meet required specifications and can function as intended. GD&T plays a crucial role in various stages of product development, including prototype development.
Prototype Development and GD&T
Prototype development is a critical phase in the product design and development process, where initial designs are turned into physical prototypes for testing and evaluation. The goal of prototype development is to validate and refine the design, assess its functionality, identify potential issues, and make necessary improvements before moving into production.
GD&T principles can greatly assist in the process of developing prototypes. By applying the principles of GD&T, engineers and designers can ensure that the prototype components are manufactured to precise specifications, allowing them to fit together accurately and function properly. This eliminates any ambiguity in the design and manufacturing process, ultimately leading to improved product quality and performance.
Advantages of GD&T in Prototype Development
1. Enhanced Communication: GD&T provides a standardized language for communicating design intent, allowing engineers, designers, and manufacturers to have a clear understanding of the required tolerances and specifications. This eliminates confusion and interpretation errors, ensuring that the prototype is developed exactly as intended.
2. Design Optimization: GD&T allows for the optimization of product design by defining critical features and the allowable deviations. Engineers can use GD&T symbols and datum references to ensure that the prototype's critical dimensions are within the specified tolerances, leading to improved performance and functionality.
3. Cost Reduction: GD&T helps in minimizing manufacturing and assembly costs by precisely defining tolerance zones. By providing clear guidelines on allowable variations, GD&T reduces the need for unnecessary rework, adjustments, and assembly issues, resulting in cost savings during the prototype development phase.
4. Improved Fit and Functionality: GD&T ensures that the prototype components fit together accurately, reducing the risk of misalignment or improper functionality. This is particularly important when testing the functionality and usability of the prototype, as any misfit or improper function can lead to design changes and delays in the development process.
Conclusion
GD&T is an invaluable tool in prototype development. By using GD&T principles, engineers and designers can effectively communicate design intent, optimize product design, reduce manufacturing costs, and improve fit and functionality. The application of GD&T in prototype development ensures that the prototypes meet the required specifications, allowing for successful testing and evaluation before moving into production. Overall, GD&T plays a crucial role in enhancing the efficiency and effectiveness of the prototype development process.
Comments:
Thank you all for joining this discussion on enhancing prototype development in GD&T technology using ChatGPT. I am excited to hear your thoughts and opinions!
Great article, Aditi! I really enjoyed reading it. I completely agree that leveraging ChatGPT can greatly improve communication and collaboration during prototype development.
Hi Aditi, thanks for sharing this article. I found the application of ChatGPT in GD&T technology to be intriguing. It can definitely streamline the communication process and reduce errors.
Aditi, excellent write-up! ChatGPT can undoubtedly facilitate effective communication, especially for remote teams working on prototype development.
I appreciate you shedding light on this topic, Aditi. I'm curious about the potential challenges of using ChatGPT in GD&T technology. Anyone have any thoughts?
Elizabeth, I think one challenge could be the accuracy of interpreting complex GD&T requirements through text-based communication. It might require additional effort to ensure crystal clear understanding.
Maria, I agree with you. It can be challenging to convey precise technical specifications solely through text-based communication. Visual aids or additional platforms might be necessary to complement ChatGPT.
Aditi, fantastic article! I think one of the major benefits of ChatGPT could be its ability to save time in prototype development. It allows for quick interaction and clarification, reducing delays.
Indeed, Karen! Real-time collaboration facilitated by ChatGPT can significantly accelerate prototype development and decision-making processes.
Aditi, thank you for sharing your insights. I wonder if there are any limitations or potential biases in the use of ChatGPT for GD&T technology. Any thoughts?
Linda, one limitation could be that ChatGPT might not grasp the contextual nuances and industry-specific jargon accurately. It could lead to misinterpretations or miscommunications.
Roger raises a valid concern. The training data for ChatGPT may not cover all the GD&T intricacies, which might impact the accuracy of its interpretations.
Aditi, your article brings up an interesting point. I can see how ChatGPT's collaboration features can enhance communication among cross-functional teams working on GD&T prototypes.
I agree with you, Michael. ChatGPT can ensure a seamless flow of information between different teams, leading to increased efficiency and reduced rework.
Aditi, your article is enlightening. I believe implementing ChatGPT for GD&T technology can empower engineers with a more dynamic and interactive collaboration experience.
Great article, Aditi! I think ChatGPT can foster better communication by bridging the gap between technical experts and non-technical stakeholders during prototype development.
Aditi, the potential of leveraging ChatGPT in GD&T technology is indeed promising. It can help reduce miscommunication, which is vital for successful prototype outcomes.
Thank you all for your valuable comments and insights. I appreciate your engagement and perspectives on ChatGPT in GD&T technology. It's great to see the positive reception.
Aditi, thanks for writing this article. I think ChatGPT could also assist in knowledge sharing and documentation of prototype development processes.
That's a great point, Nathan. By using ChatGPT, discussions and decisions made during prototype development can be recorded and easily accessible for future reference.
Aditi, I found your article very informative. I think ChatGPT can help bridge communication gaps that often occur between design and manufacturing departments.
Yes, Jeffrey! ChatGPT can facilitate smoother communication, reducing iterations and improving alignment between design intent and manufacturing feasibility.
Aditi, great insights! ChatGPT can enhance collaboration not only within teams but also between different organizations involved in prototype development.
Sara, you're right! ChatGPT's ability to enable efficient communication and collaboration across organizations can lead to better outcomes and reduced development cycles.
Thank you, everyone, for sharing your thoughts and insights. It's been a pleasure discussing the potential benefits and considerations of using ChatGPT in GD&T technology.
Aditi, I thoroughly enjoyed reading your article. It's inspiring to see how AI technologies like ChatGPT can revolutionize the way we collaborate in engineering fields.
Carol, I couldn't agree more! Incorporating AI in communications can unlock immense potential for efficiency, accuracy, and streamlined decision-making.
Aditi, thank you for the insightful article. ChatGPT can provide a valuable platform for brainstorming and ideation during prototype development.
Absolutely, Adrian! ChatGPT can serve as a virtual collaborative whiteboard, enabling real-time idea sharing and creation for better prototype outcomes.
Aditi, I found your article thought-provoking. ChatGPT could assist in capturing tacit knowledge and expertise during prototype development, paving the way for continuous improvement.
Mark, that's an interesting perspective. By using ChatGPT, organizations can build a repository of valuable information for future reference and knowledge retention.
Aditi, I appreciate you highlighting the potential benefits of leveraging ChatGPT in GD&T technology. It surely holds immense promise for the engineering field.
Aiden, I completely agree. The application of AI technologies like ChatGPT can redefine collaboration and communication norms in engineering and prototyping.
Thank you all for your engaging comments. Your perspectives provide valuable insights into the potential of ChatGPT in prototype development. Keep the conversation going!
Aditi, your article inspires me to explore how AI can amplify engineering efforts further. ChatGPT can truly revolutionize the way we collaborate and innovate.
I agree, Victoria. The integration of AI in engineering processes can unlock new possibilities and enhance the overall efficiency of prototype development.
Aditi, great insights on the role of ChatGPT. I believe it can contribute to reducing errors and increasing precision during GD&T prototype development.
Absolutely, Richard. ChatGPT can help enhance the quality of prototypes by facilitating clearer communication and minimizing misunderstandings.
Thank you once again for your valuable contributions. It's inspiring to see your enthusiasm for the potential of ChatGPT in GD&T prototype development. Let's continue the discussion!
Aditi, your article really got me thinking about the future of collaboration in engineering. I believe ChatGPT can lead to breakthroughs in prototype development.
I share your excitement, Jacob. The possibilities seem endless when it comes to leveraging AI technologies like ChatGPT in engineering and design fields.
Aditi, thank you for shedding light on this fascinating topic. ChatGPT's integration into GD&T technology can revolutionize collaboration and efficiency in prototyping.
Nora, I couldn't agree more. The potential impact of AI-driven communication tools like ChatGPT on prototype development is truly exciting.
Thank you, Jacob, Emma, Nora, and Timothy, for your insightful comments. Let's embrace the possibilities of AI in prototype development and continue exploring its potential.
Aditi, I found your article to be thought-provoking. ChatGPT can bridge the gap between design intent and practical implementation during GD&T prototype development.
Julia, I couldn't agree more. The real-time collaboration and communication features of ChatGPT can facilitate a better understanding of design requirements for successful prototypes.
Aditi, thank you for presenting the potential benefits of ChatGPT in GD&T technology. It's exciting to think about the advances we can achieve through AI-driven collaboration.
Olivia, I share your excitement. With AI technologies like ChatGPT, the engineering field can unlock new levels of efficiency, accuracy, and innovation.
Thank you, Julia, Benjamin, Olivia, and William, for your engaging comments. Your thoughts demonstrate the immense potential of ChatGPT in GD&T prototype development. Let's keep pushing boundaries!
Thank you all once again for your wonderful comments and insights. Your engagement in this discussion has been instrumental in exploring the possibilities of ChatGPT in GD&T technology. Keep innovating and collaborating!