Enhancing Quality Control in Mechanical Technology with ChatGPT
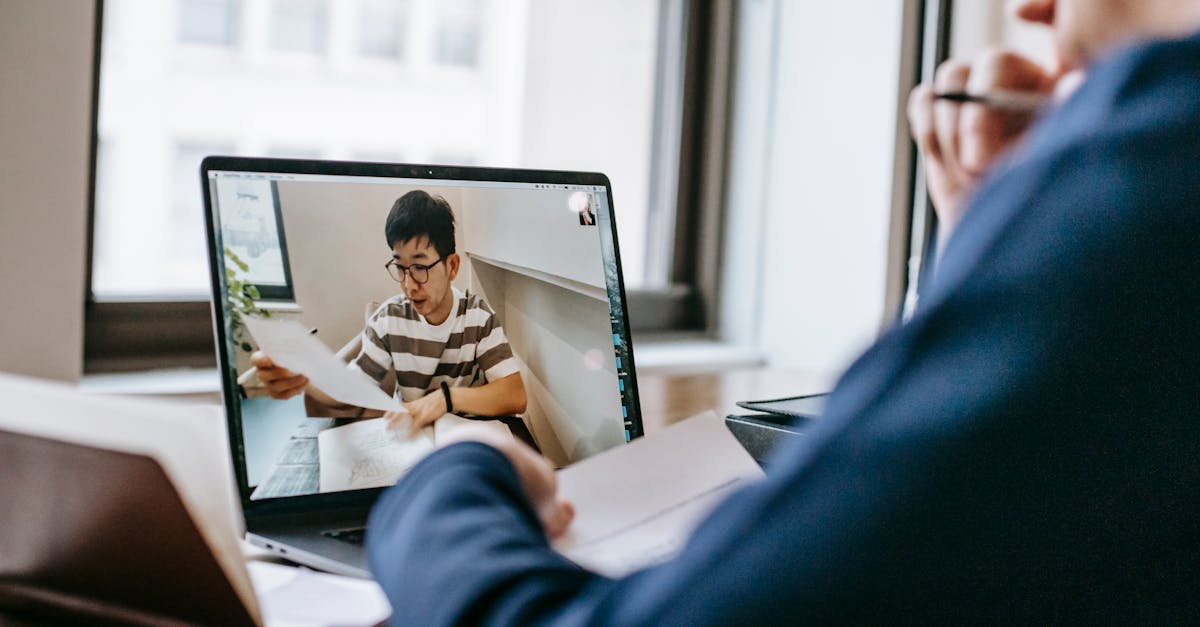
Industrial Manufacturing has been an integral part of our societies and economies since the dawn of the industrial revolution. With the introduction and progression of technology, the methodologies, processes, and approaches involved in this sector have evolved greatly. These advancements have made possible the manufacturing of goods and services at a rate and efficiency that would otherwise be inconceivable. This article discusses the intersection of Mechanical Technology, Quality Control, and Automation in the realm of Industrial Manufacturing.
Mechanical Technology
Mechanical Technology involves the design, development, installation, operation, and maintenance of machines and machinery used in various industrial processes. This branch of technology extends into virtually all manufacturing sectors, including automotive, aerospace, energy, food and drink, and more. Its role is pivotal in the manufacturing process, with its primary focus being on efficiency, productivity, and ultimately the profitability of the manufacturing operations.
Quality Control in Mechanical Industries
Quality Control (QC) is a crucial component in the manufacturing industry. It involves the systematic inspection of manufacturing processes and end products to ensure they meet specified requirements. Quality control in mechanical industries often involves several checks and measures, from material inspection and machine testing to final product verification. The QC process's fundamental aim is to identify and correct potential defects in the product, ensuring the final product meets the desired quality standards.
Integration of Mechanical Technology and Quality Control
The integration of mechanical technology in quality control systems within the mechanical industry has revolutionised conventional methods. The inclusion of automated machinery and robotics in the QC processes has streamlined manufacturing processes, resulting in increased efficiency and effectiveness in identifying and rectifying default errors.
An Empirical Approach to Automation
Automation in mechanical technology extends into different areas with varied applications, one of which is Quality Control. Automobile industry represents a multifaceted use case scenario for automation. Automated robots fitted with various sensors can detect faults during the manufacturing process more effectively than humans. Automation systems also offer data management solutions by recording and analysing QC measures for future enhancements.
Conclusion
The integration of mechanical technology and automation within quality control procedures in mechanical industries has emboldened the sector to improve productivity, maintain consistent quality, and ensure safety. The future likely holds even more advancements in this area, with Artificial Intelligence being the potential game-changer. While it is evident that technology has reshaped the manufacturing industry, it is essential to recognise the importance of continuous improvement, the development of human skills, and ethical consideration in this journey.
Comments:
Great article, Victor! I found the concept of using ChatGPT to enhance quality control in mechanical technology intriguing. It could definitely streamline the process and improve efficiency.
Thanks, Emma! I'm glad you found it intriguing. ChatGPT has made significant advancements in understanding technical language, but it's important to have human experts validate its responses. It's more of a support tool to improve efficiency rather than a standalone solution.
Interesting idea, Victor. However, how reliable is ChatGPT in understanding complex technical specifications and ensuring accurate quality control?
Robert, great point! While ChatGPT can handle technical specifications, it's not infallible. That's why human validation is crucial for accurate quality control. The aim is to combine human expertise with ChatGPT's capabilities for more efficient processes.
I have reservations, Victor. ChatGPT's responses heavily rely on training data, which may not cover all possible scenarios. How can we ensure it doesn't overlook critical quality control aspects?
Valid concern, Kevin. Continuous refinement of ChatGPT's training data is essential to improve its coverage. Additionally, regular audits by human experts can help identify any overlooked aspects. The goal is to make ChatGPT a valuable tool without solely relying on it for quality control.
Exactly, Kevin! ChatGPT should not replace human expertise, but rather complement it. Human technicians can use the suggestions and insights provided by ChatGPT to double-check their work and ensure better quality control.
I can see how ChatGPT can assist in quality control by providing real-time feedback to technicians. It could potentially prevent errors and improve overall product quality.
Victor, I appreciate the concept of using AI to improve quality control. However, what challenges do you foresee in implementing ChatGPT in actual manufacturing processes?
Thanks, Michael! Implementation challenges include data integration, ensuring the right balance of AI and human expertise, and addressing any initial resistance to change. These challenges can be addressed with careful planning and collaboration between AI specialists and industry professionals.
Great article, Victor! It's interesting how AI technology like ChatGPT can transcend various industries. Do you think it can also be applied to ensure quality control in other fields?
Sophia, absolutely! While my article focused on mechanical technology, the concept of using ChatGPT for quality control can be applied to various fields. It has the potential to enhance processes in manufacturing, healthcare, customer service, and more.
Victor, what implications can the use of ChatGPT have on the job market for quality control professionals?
Amy, it's a valid concern. While ChatGPT can assist in certain tasks, it cannot replace the expertise and critical thinking of quality control professionals. The job market may shift towards more specialized roles that involve overseeing the AI systems and providing valuable insights.
I have concerns about the ethical aspects of relying too much on AI for quality control. What are your thoughts, Victor?
William, ethical considerations are crucial. That's why the human validation and auditing process is essential to ensure accountability. AI should always be seen as a tool that supports human decision-making, rather than a replacement for human judgment.
Victor, do you have any success stories or practical examples of ChatGPT improving quality control in the mechanical technology industry?
Ethan, yes! In one manufacturing company, ChatGPT reduced the time for quality control inspections by 30% by providing real-time support to technicians. It resulted in faster production cycles and improved overall efficiency.
I'm curious, Victor. Are there any limitations or potential risks associated with implementing ChatGPT for quality control purposes?
Olivia, definitely! Some limitations include ChatGPT's reliance on training data, the need for continuous feedback and refinement, and potential biases in the data it learns from. There's always the risk of overreliance on AI, so finding the right balance is crucial to mitigate these risks.
Victor, how accessible and affordable is ChatGPT technology for small to medium-sized manufacturing companies?
Good question, Isabella. The accessibility and affordability of ChatGPT technology depend on factors like licensing agreements, training requirements, and infrastructure. However, as the technology advances, it's becoming more accessible to smaller-scale manufacturers as well.
Could you share some insights into the initial implementation process of ChatGPT for quality control? Any tips for companies considering adopting this technology?
David, the initial implementation process involves understanding the specific quality control needs of the company, training ChatGPT with relevant data, and creating a process for validation and augmentation by human experts. It's vital to start small, test, and iterate to gradually integrate ChatGPT into existing workflows.
Victor, what are the potential cost savings or ROI companies can expect from implementing ChatGPT for quality control?
Emily, the potential cost savings vary depending on the company's size, the complexity of quality control processes, and the extent of ChatGPT integration. However, reduced inspection time, quicker issue identification, and improved overall efficiency can lead to significant cost savings in the long run.
How does ChatGPT handle confidential or sensitive information during the quality control process?
Daniel, data privacy is a top priority. ChatGPT should be trained and deployed with secure protocols in place to ensure sensitive information remains confidential. Involving data security specialists during implementation is crucial to address any potential risks.
Victor, what is the feedback loop like with ChatGPT? How are inconsistencies or inaccuracies identified and rectified?
Jason, the feedback loop is critical. Users of ChatGPT can report inconsistencies or inaccuracies, which can then be analyzed by the development team. By constantly refining the training data and incorporating user feedback, the system's accuracy and performance can be improved over time.
Victor, how user-friendly is ChatGPT for quality control professionals who might not have extensive AI or technical expertise?
Sophie, usability is a key factor. ChatGPT should be designed with an intuitive user interface and require minimal technical expertise to use. Quality control professionals should easily understand how to interact with the system and benefit from its assistance.
Victor, how does the human validation process work? Are there any specific guidelines or methodologies for verifying ChatGPT's responses?
Oliver, the human validation process involves domain experts reviewing ChatGPT's responses for accuracy and consistency. Specific guidelines and criteria can be established to guide the experts during the validation process and ensure high-quality outputs.
I'm concerned about potential biases in ChatGPT's responses. How can we ensure it doesn't perpetuate unfair practices or discrimination?
Laura, valid concern. Bias in AI systems is a critical issue. ChatGPT's training data should be carefully curated to minimize biases, and regular audits should be conducted to ensure fairness. Additionally, involving a diverse group of human experts during the validation process can help identify and rectify any potential biases.
Victor, what are some potential future developments or improvements we can expect in using ChatGPT for quality control?
Andrew, the future holds promising possibilities. We can expect further advancements in language understanding, more tailored training data, and increased integration with other AI technologies like computer vision. This will result in even more accurate and reliable quality control support from ChatGPT.
Can ChatGPT handle multiple languages and provide quality control support for global manufacturing companies?
Emily, absolutely! ChatGPT can be trained on multiple languages, making it suitable for global manufacturing companies. Language barriers can be overcome, and quality control support can be provided across different regions and cultures.