Enhancing Quality Control Through Process Automation: Leveraging ChatGPT's AI-powered Capabilities
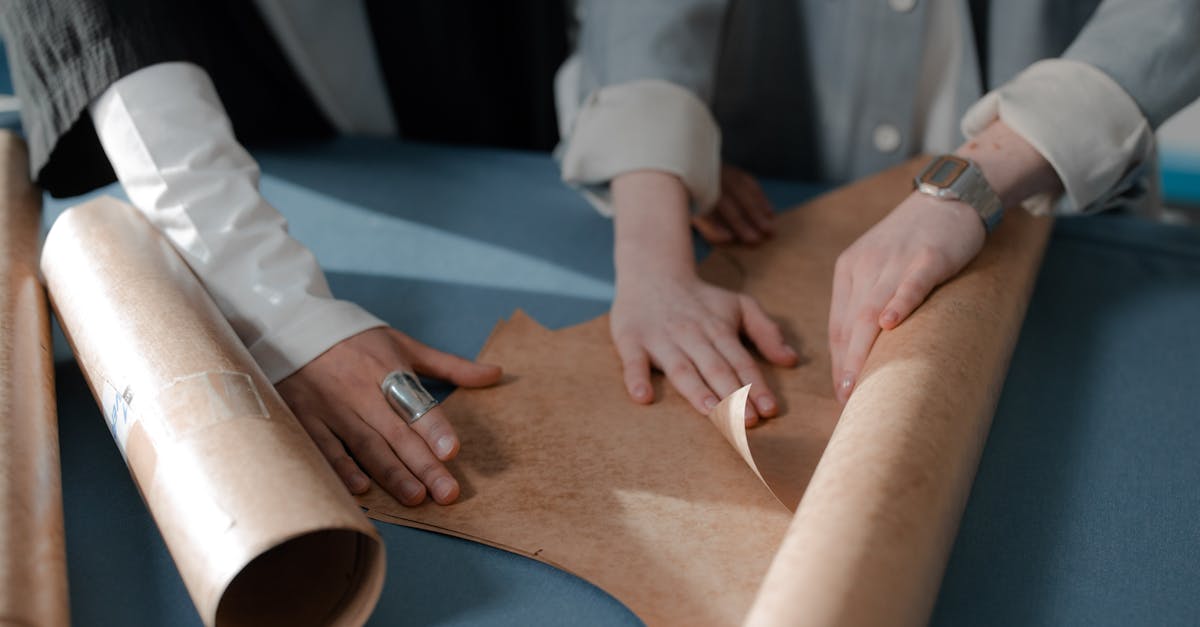
In today's fast-paced and highly competitive business landscape, process automation has become a crucial aspect of staying ahead. One area where automation has proven to be immensely beneficial is quality control. With the advent of ChatGPT-4, a state-of-the-art language model developed by OpenAI, automating routine quality control tasks has become easier than ever before.
The Role of Quality Control in Process Automation
Quality control plays a crucial role in ensuring that products or services meet the specified standards and customer expectations. Traditionally, quality control has been a manual process requiring extensive human intervention. This approach is not only time-consuming but also prone to errors and inconsistencies.
By leveraging ChatGPT-4's advanced natural language processing capabilities, organizations can automate a wide range of quality control tasks. By analyzing and interpreting large volumes of data, ChatGPT-4 can identify patterns, deviations, or potential issues with incredible accuracy.
Benefits of Automating Quality Control Tasks with ChatGPT-4
1. Increased Efficiency: Automation of routine quality control tasks can significantly improve operational efficiency. ChatGPT-4 can quickly analyze vast amounts of data, providing insights and identifying potential issues in real-time.
2. Cost Reduction: Automating quality control tasks reduces the dependency on manual labor, allowing organizations to save costs associated with human resources. By streamlining processes, organizations can allocate resources more efficiently.
3. Error Reduction: Human errors are inevitable, but automation can help minimize them. ChatGPT-4 consistently applies quality control protocols without fatigue or oversight, reducing the risk of errors that can impact product quality.
4. Enhanced Productivity: By automating routine quality control tasks, employees can focus on strategic and higher-value activities that require critical thinking and problem-solving skills. This allows businesses to harness the full potential of their human resources, leading to increased productivity.
Applications of ChatGPT-4 in Quality Control
The applications of ChatGPT-4 in quality control are widespread across various industries:
1. Manufacturing: ChatGPT-4 can analyze sensor data, ensuring compliance with quality parameters in real-time. It can identify potential defects or anomalies, enabling proactive maintenance and reducing downtime.
2. Software Development: ChatGPT-4 can review code and identify possible bugs and vulnerabilities. By automating code quality checks, organizations can reduce the risk of software failures and security breaches.
3. Customer Support: With its natural language processing capabilities, ChatGPT-4 can analyze customer feedback and identify recurring issues or patterns. This helps organizations proactively address customer concerns and improve overall customer satisfaction.
4. Data Analysis: ChatGPT-4 can analyze large sets of data, helping organizations identify trends, correlations, and anomalies. This enables data-driven decision-making and optimization of processes for improved quality control.
Conclusion
Automation of quality control tasks with ChatGPT-4 opens up new possibilities for businesses by streamlining processes, reducing costs, and enhancing overall productivity. By leveraging this advanced language model, organizations can improve their products and services, stay competitive, and focus their resources on strategic activities that drive growth. As automation continues to evolve, ChatGPT-4 demonstrates its potential to revolutionize quality control in various industries.
Comments:
Thank you for taking the time to read my article on enhancing quality control through process automation. I'm excited to hear your thoughts and opinions!
Great article, Michele! Automation has really revolutionized quality control processes in many industries. It helps in reducing errors and enhancing efficiency.
I agree with Sarah. Automation can greatly improve quality control by eliminating human error. However, it's important to find the right balance between automation and human intervention.
Fantastic article, Michele! I particularly enjoyed reading about how ChatGPT's AI-powered capabilities can be leveraged in quality control. It's amazing what AI can do!
Thank you, Emily! I'm glad you found the article enjoyable. AI has indeed opened up new possibilities in quality control, and ChatGPT's capabilities can be a game-changer.
While automation provides numerous benefits, I worry about potential job losses in quality control due to increased reliance on machines. What are your thoughts on this, Michele?
That's a valid concern, Mark. As automation becomes more prevalent, some job roles may change or become redundant. However, it also opens up new opportunities for reskilling and focusing on more strategic tasks.
Great article, Michele! One aspect I'd like to explore further is the potential challenges in implementing process automation for quality control. Are there any specific obstacles that organizations may face?
Thank you, Michael! Implementing process automation for quality control can indeed have its challenges. Some common obstacles include integrating automation with existing systems, ensuring data accuracy, and addressing potential resistance to change.
In addition to what Michele mentioned, organizations may also face challenges in selecting the right automation tools that align with their specific quality control processes and requirements.
Great article, Michele! I have seen how automation has improved quality control in our organization. It has reduced errors and improved overall efficiency.
Thank you, Karen! I'm glad to hear that automation has had a positive impact on quality control in your organization. It demonstrates the immense potential it holds.
Hi Michele, excellent article! Are there any specific industries where process automation has been particularly successful in enhancing quality control?
Thank you, Frank! Process automation has been successful in various industries, including manufacturing, healthcare, banking, and customer service. Its potential extends across different sectors.
Michele, great article! I would love to learn more about the potential risks associated with process automation for quality control. Are there any risks that organizations need to be cautious about?
Thank you, David! When it comes to process automation for quality control, some potential risks include over-reliance on automation, lack of human oversight, and susceptibility to technical glitches or data breaches.
I completely agree, Michele. It's crucial to strike a balance between automation and human judgment to mitigate these risks and ensure optimal quality control.
Great article, Michele! I have a question regarding the scalability of automation in quality control processes. How easily can automation accommodate changing business needs and scale up?
Thank you, Sophia! Automation can be highly scalable when implemented correctly. By designing flexible and adaptable automation workflows, businesses can ensure efficient scaling to accommodate changing needs.
That's reassuring to know, Michele. It's important for organizations to invest in automation solutions that can grow alongside their evolving quality control requirements.
I agree with you, Michael. Implementing automation can be complex, especially when it involves integrating with legacy systems. It requires careful planning and strategic execution.
I understand the concern, Mark, but it's important to keep in mind that automation also creates new jobs and skill requirements. It's a matter of adapting to the changing landscape.
I can vouch for automation in the customer service sector. It has improved response times, reduced errors, and enhanced the overall quality of interactions.
I agree, Alice. Automation in customer service has transformed the way organizations interact with their customers, leading to better customer experiences.
Manufacturing is another industry where automation has made a significant impact on quality control. It has enhanced precision, reduced defects, and improved production efficiency.
Another risk that organizations need to consider is the need for continuous monitoring and updating of automated systems to adapt to changing requirements and technologies.
The concept of leveraging AI-powered capabilities in quality control is fascinating. How do you foresee AI further shaping the future of quality control processes?
Great question, Adam! AI will likely play a pivotal role in quality control processes. It will enable more advanced predictive analytics, real-time monitoring, and continuous improvement based on intelligent insights.
I think AI can also help in identifying patterns and anomalies in vast amounts of data, allowing organizations to proactively address quality issues before they escalate.
AI can also assist in optimizing resource allocation, identifying bottlenecks, and streamlining quality control processes, leading to better productivity and cost savings.
Automation has undoubtedly transformed quality control processes. However, it's important to remember that not all aspects of quality control can be automated. Human expertise and judgment still play a crucial role.
I completely agree with you, Grace. Automation should support and augment human capabilities in quality control, rather than replace them entirely.
The potential benefits of automation in quality control are immense. Improved accuracy, productivity, and efficiency are just a few examples of how it can revolutionize processes.
Absolutely, Ava! Automation can free up human resources to focus on more complex tasks, innovation, and strategic decision-making, ultimately driving business growth.
As with any technological advancement, it's important to carefully plan and implement automation in quality control. Organizations should prioritize training, change management, and constant evaluation.
I couldn't agree more, Lucy. Successful implementation of automation requires a holistic approach that considers not only the technology but also the people and processes involved.
Automation can contribute to standardization and consistency in quality control processes, ensuring that products and services meet the expected standards consistently.
I think the combination of automation and human expertise can create a powerful quality control system that leverages the strengths of both.
It's fascinating to see how technology like ChatGPT's AI-powered capabilities is transforming not only quality control but various aspects of our personal and professional lives.
Indeed, Daniel! Technology continues to shape our world in remarkable ways, and AI-powered tools are at the forefront of this transformation.
Automation and AI-powered capabilities in quality control have the potential to enhance customer satisfaction and loyalty by ensuring consistent high-quality products and services.
Absolutely, Joshua! Quality control is integral to building trust with customers, and automation can significantly contribute to maintaining and improving that trust.
As technology continues to advance, it's crucial for organizations to embrace automation in quality control to stay competitive and meet evolving market demands.
You're absolutely right, Aiden. Adapting to technological advancements is essential for organizations to thrive in this fast-paced and ever-changing business landscape.
Thank you, Michele, for sharing such an informative article! It's evident that automation and AI-powered capabilities hold immense potential in enhancing quality control processes.
Indeed, Grace! It's exciting to see how technology continues to shape the way we approach quality control, paving the way for more efficient and effective processes.
I thoroughly enjoyed reading this article, Michele. It provided valuable insights into the role of automation in quality control and its future implications.
Thank you, Olivia! I'm glad you found the article insightful. The potential of automation in quality control is indeed exciting, with many possibilities yet to be explored.
Automation and AI-powered capabilities have come a long way in enhancing quality control, and I look forward to seeing further advancements and innovations in this field.
Absolutely, Emma! The future of quality control is intertwined with automation and AI, and the journey ahead holds great promise.