Enhancing Real-time Diagnostics in Mechanical Technology: Harnessing the Power of ChatGPT
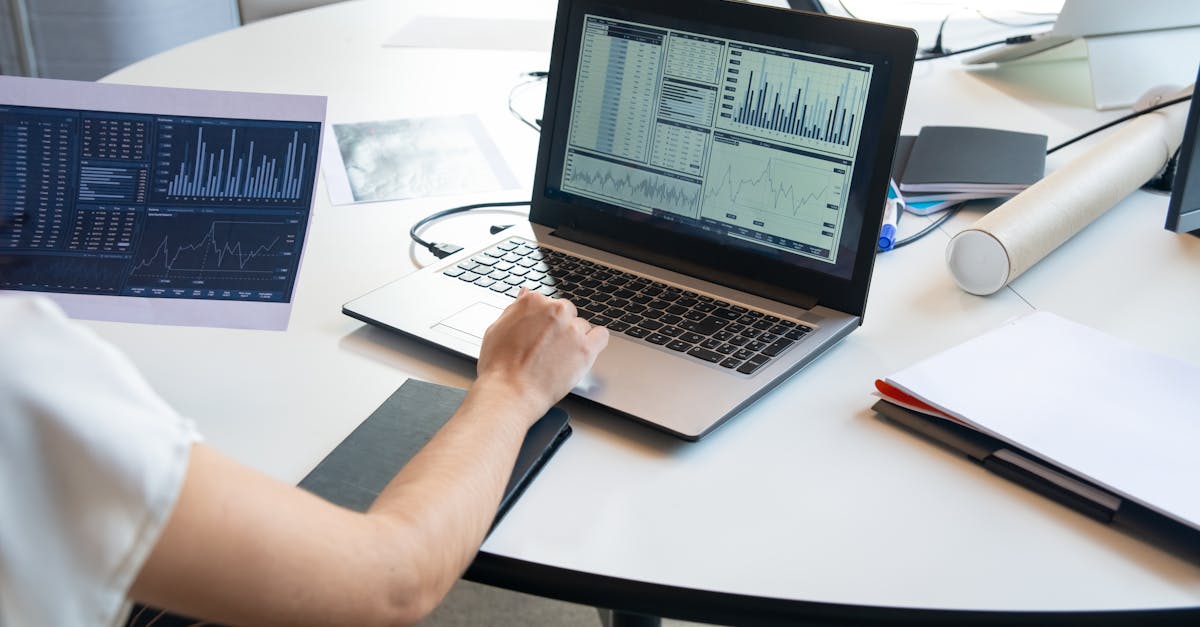
Mechanical technology has, for years, revolutionized the world in various fields and industries. Indeed, it has proven especially pivotal in facilitating the creation of everyday devices and complex machinery, offering practical solutions and driving the progress of civilization. This article aims to delve deeper into a specific aspect of mechanical technology: real-time diagnostics.
What is Real-time Diagnostics?
Real-time diagnostics is, in essence, a method that allows automated, immediate analysis and monitoring of systems. It is also a subtle embodiment of predictive maintenance, as it enables prompt detection of faults and potential machine failures thereby promoting a proactive rather than reactive approach to system maintenance.
Real-time Diagnostics in Mechanical Systems
When it comes to mechanical systems, real-time diagnostics plays a crucial role. Mechanical systems are structured and functioning assemblies of mechanical components. The role of real-time diagnostics in such systems is to continuously monitor these individual components and the overall system performance.
How it Works
Real-time diagnostics in mechanical technology works by creating a consistent stream of data, continuously monitoring system performance for signs of declining performance or imminent machine failure. It involves setting up sensors that collect data related to performance parameters such as temperature, pressure, vibration, and rotational speed. This data is then processed instantly, and actionable results are produced, often with the help of modern digital solutions like machine learning algorithms or artificial intelligence.
Benefits
The benefits of real-time diagnostics are manifold. First, it promotes operational efficiency. With real-time diagnostics, maintenance can be planned ahead, downtime can be minimized, and the overall operational efficiency can be improved. A second major benefit is cost-saving. Real-time diagnostics helps to prevent critical system failures, thus avoiding expensive repair or replacement costs. Lastly, the use of real-time diagnostics improves the safety of systems. Potential system failures can be detected before they occur, avoiding catastrophic system failures and maintaining the safety of both the machinery and its operators.
Developing Tools for Real-time Diagnostics
Developing tools for real-time diagnostics in mechanical systems demands expert knowledge in mechanical systems and advanced technology. These tools need to efficiently collect, process, and analyze data. Moreover, they need to offer actionable insights that can be readily implemented. This necessitates sophisticated tools that are equipped with state-of-the-art technology such as machine learning and artificial intelligence.
Conclusion
In conclusion, real-time diagnostics in mechanical systems offers a myriad of opportunities as it propels advancements in mechanical technology. While its implementation asks for expert knowledge and advanced technologies, the benefits it brings regarding operational efficiency, cost-saving, and safety are exceptional. Thus, the importance of real-life diagnostics cannot be overstated, and further research and development in this area are paramount for industrial growth and development.
Comments:
Thank you all for taking the time to read my article on harnessing the power of ChatGPT in real-time diagnostics for mechanical technology. I hope you found it informative and thought-provoking. I'm here to answer any questions or engage in discussions!
Great article, Victor! I'm impressed by the potential of ChatGPT in enhancing real-time diagnostics in mechanical technology. It can really revolutionize the field. Have you come across any practical applications of this technology?
Thank you, Michael! Absolutely, there are several practical applications of ChatGPT in mechanical technology. For example, it can assist in troubleshooting equipment issues remotely or guide technicians through complex repair procedures. Its versatility makes it a valuable tool in various industries.
I enjoyed reading your article, Victor! ChatGPT seems like a powerful tool, but how accurate is it in real-time diagnostics? Are there any limitations or challenges that need to be addressed?
Thank you, Sophia! Accuracy is a crucial aspect, and while ChatGPT has shown promising results, it's not without limitations. One challenge is its reliance on training data, which may not cover all possible scenarios. Moreover, in complex situations, it may struggle to provide precise diagnoses. However, continual refinement can help mitigate these challenges.
I find the idea of using ChatGPT in real-time diagnostics fascinating. It could greatly reduce downtime and improve overall efficiency. However, do you think there could be any potential risks or ethical considerations in relying solely on AI for critical tasks?
Good point, David! Relying solely on AI does pose ethical considerations and potential risks. It's essential to maintain a balance and have human oversight in critical tasks. AI can assist and provide insights, but the final decision should be made by trained professionals. Regular audits and human collaboration can help mitigate risks and ensure accountability.
Great article, Victor! ChatGPT certainly has the potential to streamline diagnostics in mechanical technology. As with any AI system, how can we ensure that ChatGPT remains unbiased and does not perpetuate any pre-existing biases?
Thank you, Jennifer! Addressing bias is crucial to ensure fairness in AI systems like ChatGPT. It requires careful curation of training data and continuous evaluation to identify and rectify any biases that may emerge. Involving a diverse range of stakeholders in the development process can also help mitigate biases and create more inclusive technology.
Victor, great article! While ChatGPT sounds promising, what are the computational requirements for implementing it in real-time diagnostics systems? Can it be resource-intensive?
Thank you, Eric! ChatGPT can be resource-intensive, especially during training and inference stages. However, there are ways to optimize its deployment, such as using hardware acceleration or edge computing. Balancing computational requirements with the benefits obtained is crucial to ensure its practicality in real-time diagnostics systems.
Victor, your article was an interesting read! Do you think ChatGPT will completely replace human experts in diagnostics, or is it more of a complementary tool?
Thank you, Sara! I believe ChatGPT is more of a complementary tool rather than a replacement for human experts. It can augment their capabilities and provide valuable insights, but human expertise, critical thinking, and experience are vital for accurate diagnostics. The goal is to create a symbiotic relationship between AI and human professionals.
Great study, Victor! It's fascinating to see ChatGPT's potential in real-time diagnostics. How do you envision its role evolving in the future? Are there any exciting developments on the horizon?
Thank you, Amy! In the future, the role of ChatGPT is likely to expand further. Improvements in language models and training methodologies can boost its diagnostic accuracy. Additionally, integrating it with other technologies like IoT and augmented reality can provide more comprehensive real-time diagnostics solutions. Exciting developments are on the horizon, and I'm eager to see how it unfolds!
Victor, excellent article on ChatGPT! Can you shed some light on the challenges of implementing ChatGPT in real-time diagnostics, particularly in high-risk environments?
Thank you, Robert! Implementing ChatGPT in high-risk environments brings additional challenges. Ensuring system reliability, addressing security concerns, and real-time response requirements are crucial aspects that need attention. Verification and validation processes are essential to guarantee accurate diagnostic recommendations in such critical environments.
Victor, fascinating topic! Can you elaborate on how ChatGPT handles uncertainty in real-time diagnostics? Is it able to provide probabilities or confidence levels in its diagnoses?
Thank you, Rachel! Handling uncertainty is an important aspect of real-time diagnostics. ChatGPT, by leveraging probabilistic approaches, can indeed provide confidence levels or probabilities in its diagnoses. These can help users gauge the level of certainty and make informed decisions based on the recommendations provided.
Great article, Victor! Do you think ChatGPT can be effectively used for predictive maintenance in mechanical systems or is it more suited for diagnostic purposes?
Thank you, Daniel! While ChatGPT can contribute to predictive maintenance by analyzing system data and identifying potential issues, its strength lies in diagnostic purposes. By providing real-time insights during system operation, it can help analyze and rectify existing problems effectively.
Victor, your article was thought-provoking! How can we address the potential limitations of ChatGPT's training data, particularly in scenarios where there is limited data available?
Thank you, Emma! Limited training data can be a challenge for ChatGPT. Techniques like transfer learning or synthetic data generation can be used to compensate for the scarcity of real-world or specific domain data. Additionally, collaborations between experts and AI researchers can help address this limitation by providing domain-specific insights.
Victor, I thoroughly enjoyed your article on ChatGPT! What kind of computational resources are required to train and fine-tune ChatGPT models specifically for mechanical diagnostics?
Thank you, Oliver! The computational resources required for training and fine-tuning ChatGPT models for mechanical diagnostics can vary depending on the size of the model and complexity of the problem. Training large-scale models typically requires high-performance hardware like GPUs or TPUs along with substantial memory capacity. The availability of cloud computing services can also help alleviate the resource requirements.
Victor, great insights into ChatGPT! As the technology continues to evolve, how do you think it will impact the job roles of mechanical technicians and engineers?
Thank you, Liam! ChatGPT, while augmenting diagnostics, is unlikely to replace mechanical technicians and engineers. Instead, it will impact their job roles by allowing them to focus more on complex problem-solving, decision-making, and overseeing AI-powered diagnostic systems. It can enhance their capabilities and make them more efficient in their roles.
Victor, your article was informative! How can businesses and industries embrace ChatGPT in real-time diagnostics without disrupting their existing infrastructure or processes?
Thank you, Emily! The integration of ChatGPT into existing infrastructure and processes should be done gradually and thoughtfully. Pilot projects, training programs, and phased implementation can help businesses adapt without disruption. Close collaboration between AI experts and industry professionals is vital to ensure a seamless transition and maximize the benefits of real-time diagnostics using ChatGPT.
Victor, fascinating article! Considering the fast-paced advancements in AI, how do you stay up-to-date with the latest developments in this field?
Thank you, Nathan! Staying up-to-date with the latest developments in AI requires continuous learning and engagement. Following academic research, attending conferences, workshops, and being part of online AI communities are essential. Collaboration with fellow researchers and professionals also provides opportunities to discuss and explore new ideas in the field.
Victor, your article on ChatGPT was insightful! Are there any specific applications or industries where ChatGPT has already shown exceptional results in real-time diagnostics?
Thank you, Grace! ChatGPT has shown exceptional results in various industries such as automotive, manufacturing, energy, and healthcare. It has been used for tasks like equipment troubleshooting, quality control, anomaly detection, and assisting with medical diagnoses. Its versatility allows for widespread adoption in different sectors and domains.
Victor, your article on ChatGPT was an interesting read! Are there any privacy concerns associated with using ChatGPT in real-time diagnostics?
Thank you, Jason! Privacy concerns are indeed a crucial aspect of implementing ChatGPT in real-time diagnostics. It's important to handle user data securely and follow privacy regulations. Implementing measures like data anonymization, secure communication protocols, and user consent mechanisms can help address privacy concerns and ensure the responsible use of AI technology.
Victor, your article on implementing ChatGPT in real-time diagnostics was insightful! How can we ensure that such AI systems are accessible to users with disabilities or language barriers?
Thank you, Maria! Ensuring accessibility is imperative in AI system deployments. Providing multi-modal interfaces, support for assistive technologies, and multilingual capabilities can enhance accessibility for users with disabilities or language barriers. Emphasizing inclusivity during the development process and gathering feedback from diverse user groups is vital to address their specific needs.
Victor, your article gave a detailed perspective on ChatGPT! How do you think this technology will evolve in terms of scalability and customization for specific industries?
Thank you, Jack! Scalability and customization are important considerations for ChatGPT in specific industries. With advancements in computing power and training techniques, scaling AI models to handle larger volumes of data and complex problems will become more feasible. Moreover, domain-specific fine-tuning and collaboration between researchers and industry professionals can enhance customization for better industry-specific applications.
Victor, great insights into ChatGPT! Do you have any recommendations for individuals interested in exploring this technology further for real-time diagnostics?
Thank you, Sophie! Individuals interested in exploring ChatGPT for real-time diagnostics can start by familiarizing themselves with natural language processing techniques and machine learning fundamentals. Hands-on experience with AI model development, training, and evaluation can be gained through online courses and practical projects. Staying updated with the latest research and actively participating in AI communities are also beneficial.
Great article, Victor! What are the key factors to consider when selecting or developing a ChatGPT model for real-time diagnostics?
Thank you, Benjamin! When selecting or developing a ChatGPT model, several factors need consideration. Model architecture, scalability, computational requirements, fine-tuning capabilities, and compatibility with the specific domain are crucial. Additionally, availability of quality training data, handling of uncertainties, privacy concerns, and ethical considerations should be factored in during the selection or development process.
Victor, your article was very informative! How can businesses assess the cost-effectiveness of implementing ChatGPT for real-time diagnostics?
Thank you, Claire! Assessing the cost-effectiveness of implementing ChatGPT for real-time diagnostics requires careful analysis. Factors like initial setup costs, infrastructure requirements, training and maintenance costs, potential reduction in downtime, and overall efficiency improvements should be considered. Conducting cost-benefit analyses, comparison with existing systems, and evaluating long-term ROI can help businesses make informed decisions.
Victor, your article provided great insights into ChatGPT for real-time diagnostics! What are some potential future use cases of this technology?
Thank you, Lucas! The potential future use cases of ChatGPT for real-time diagnostics are vast. It can be applied in fields like aviation, telecommunications, robotics, and more. Enhancing predictive maintenance systems, remote troubleshooting, intelligent virtual assistants, and continuous performance monitoring are some exciting directions where this technology could be utilized.
Victor, your article was enlightening! Can ChatGPT assist with data visualization and presenting diagnostic results to users?
Thank you, Lucy! ChatGPT can indeed assist with data visualization and presenting diagnostic results to users. It can analyze and interpret data, provide insights, and generate visual representations or reports for better understanding. Integrating it with visualization tools or incorporating adaptive interfaces can enhance the user experience and facilitate effective communication of diagnostic results.
Victor, great article on ChatGPT's potential in real-time diagnostics! In your opinion, what are the key challenges that need to be overcome for widespread adoption of this technology?
Thank you, Peter! Widespread adoption of ChatGPT in real-time diagnostics requires overcoming certain challenges. Improving accuracy and addressing biases, ensuring system reliability and security, handling privacy concerns, and establishing industry-specific standards are some key areas that need attention. Moreover, educating stakeholders, fostering trust, and maintaining a balance between AI and human expertise are vital for successful adoption.