Enhancing Tolerance Analysis in Engineering Change Orders with ChatGPT
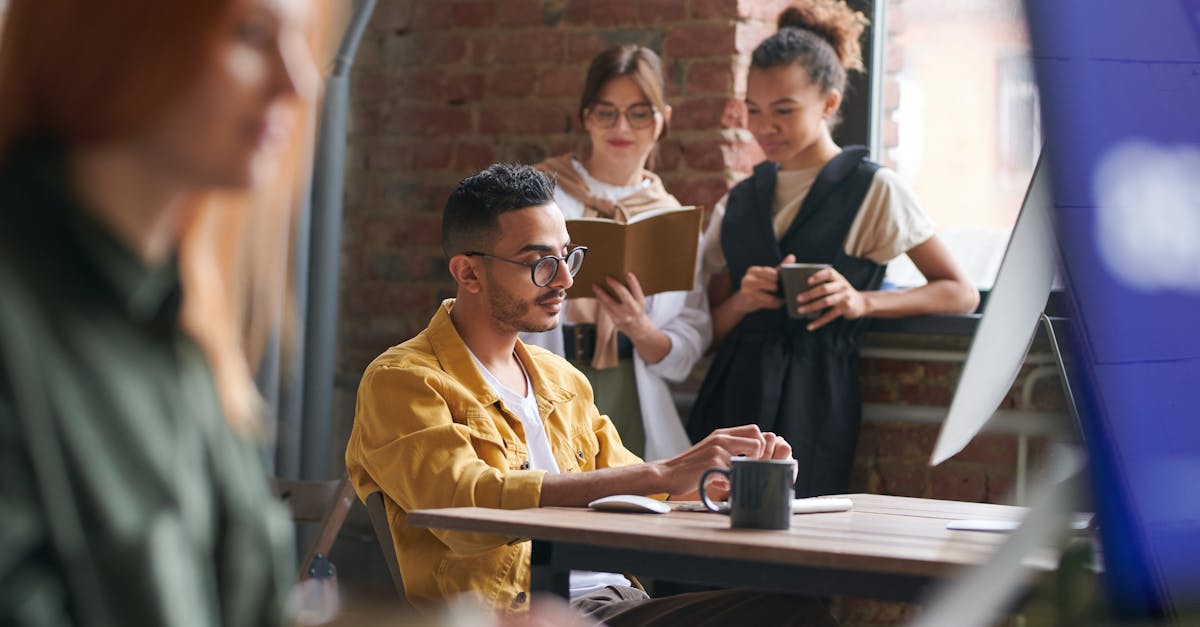
Tolerance analysis is a crucial aspect of engineering change orders (ECOs). When revisions to parts or assemblies are made, it is important to understand how these changes affect the overall tolerances of the design. Tolerance analysis helps in determining if the revised design meets the required specifications and if any additional adjustments are necessary.
What is Tolerance Analysis?
Tolerance analysis is a systematic process of examining the geometric variations in a design and evaluating their impact on product performance. It involves analyzing the dimensional and positional variations of the individual components and assemblies to ensure that they fall within acceptable limits.
Without proper tolerance analysis, even a minor deviation in the dimensions or positioning of parts can lead to issues in functionality, performance, and manufacturability. Therefore, it is essential to conduct tolerance analysis during the engineering change order process to avoid costly rework or production failures.
How Tolerance Analysis Helps in Engineering Change Orders
Engineering change orders often involve revising existing parts or assemblies due to design modifications, manufacturability improvements, or other factors. Tolerance analysis can assist in assessing how these revisions impact the overall tolerances of the design.
By conducting tolerance analysis, engineers can determine if the revised design still meets the required specifications. It allows them to evaluate the impact of the changes on the performance, functionality, and reliability of the product. If the revised design exceeds the specified tolerances, engineers can make further adjustments to bring it within acceptable limits.
Tolerance analysis also aids in identifying potential issues that may arise during manufacturing or assembly. It helps in identifying critical dimensions and features that require tighter tolerances to ensure proper fit, function, and manufacturability.
The Process of Tolerance Analysis in Engineering Change Orders
Tolerance analysis involves several steps to properly assess the impact of revisions on tolerances. These steps typically include:
- Identifying the revised parts or assemblies.
- Gathering the necessary geometric data such as dimensions, positions, and tolerances.
- Modeling the revised parts or assemblies in a CAD software.
- Conducting a tolerance stack-up analysis to calculate the cumulative effect of variations.
- Comparing the results with the specified tolerances and evaluating if they meet the requirements.
- If the tolerances are exceeded, making further adjustments to ensure compliance.
Once the tolerance analysis is complete, the revised design can be reviewed and approved for production. By incorporating tolerance analysis in the engineering change order process, companies can minimize the risk of manufacturing errors, improve product quality, and reduce time-to-market for revised designs.
Conclusion
Tolerance analysis plays a vital role in engineering change orders by assessing how revisions to parts or assemblies affect tolerances. It helps in ensuring that the revised design meets the required specifications and performs as intended. By conducting tolerance analysis, engineers can identify potential issues, make necessary adjustments, and minimize the risk of production failures.
It is essential for companies to incorporate tolerance analysis in their engineering change order process to optimize the design, improve manufacturability, and deliver high-quality products to the market.
Comments:
Thank you all for your comments! I appreciate the discussion.
This article on enhancing tolerance analysis with ChatGPT sounds interesting! Can you provide more details on how it works?
I agree, Michael. I'm curious to learn more about the specifics.
Yes, the concept is intriguing, but I wonder how reliable this approach is in comparison to established methods?
Great questions, Michael and Lisa! ChatGPT is a language model that leverages natural language processing capabilities to help engineers perform tolerance analysis in change orders.
The model can interpret engineering change orders described in plain English and generate detailed insights, reducing the need for manual analysis.
Keep in mind that while ChatGPT can provide valuable insights, it should be used in conjunction with established analysis methods for robust results.
I think incorporating AI into engineering change orders has the potential to improve efficiency and accuracy. However, it's important to ensure the model is trained on reliable data.
True, David. The quality of the training data and the model's ability to understand engineering terminology are crucial for reliable analysis.
Absolutely, David and Richard. Training the model with domain-specific engineering data and incorporating feedback from experts can enhance its understanding of technical terms.
I see the potential benefits, but I'm concerned about errors and biases that could arise in the AI analysis. How can we address those concerns?
Valid point, Emily. Bias mitigation in AI analysis is crucial. Continuous evaluation, refining the training data, and involving diverse perspectives in model development can help address those concerns.
Given that engineering change orders often involve complex technical details, how well does the model handle nuanced scenarios?
Good question, Sam. While ChatGPT performs well in many scenarios, it's important to validate the model's output with engineering expertise, especially in complex and nuanced situations.
I can see the value in using ChatGPT as a supportive tool for tolerance analysis, but wouldn't it be more practical to develop a specialized software designed solely for this purpose?
That's a valid perspective, Michael. Developing specialized software can offer a dedicated solution. However, ChatGPT's adaptability and its potential to assist in various engineering tasks make it an attractive option.
As an engineer, I'm excited about the possibilities ChatGPT brings. It could save a lot of time spent on manual analysis.
I understand the time-saving potential, but how does ChatGPT handle uncertainties and provide accurate analysis?
Good question, Lisa. ChatGPT uses probabilistic approaches to handle uncertainties. It provides an analysis based on the given inputs, indicating probabilities rather than absolute certainties.
Thanks for the clarification, Erik. It's good to know that ChatGPT takes uncertainties into account.
While the idea of using AI in engineering change orders is fascinating, there might still be resistance from professionals who prefer traditional methods. How can you address this concern?
I understand the concern, David. It's crucial to demonstrate the value of AI-enhanced analysis through case studies, comparisons, and highlighting the complementary nature of AI and traditional methods.
Erik, are there any limitations or challenges in implementing ChatGPT for engineering change orders that we should be aware of?
Certainly, Emily. Some challenges include domain adaptation, data quality, and the need for continuous improvement as engineering practices evolve. These aspects should be carefully considered during implementation.
Are there any plans to develop ChatGPT further to handle other engineering tasks beyond tolerance analysis?
Absolutely, Sam. The potential applications of ChatGPT in engineering are vast. Expanding its capabilities to handle other tasks and domains is a future direction we are actively exploring.
I believe that embracing AI in engineering can lead to exciting innovations. However, we should also stay vigilant and ensure human expertise remains at the core of the decision-making process.
I completely agree with you, Julia. AI should act as a supportive tool rather than a replacement for human expertise.
Thank you, Erik, for sharing insights into the application of ChatGPT in engineering change orders. It's an intriguing concept.
You're welcome, Lisa! I'm glad you found it intriguing.
I appreciate the open discussion here. It helps to address both the potential and concerns regarding AI in engineering.
I agree, Alex. Open discussions like this facilitate a better understanding and enable us to collectively explore new possibilities.
Indeed, it's great to hear diverse perspectives on AI in engineering. Thank you all for sharing your thoughts.
Thank you, Richard. It's been a pleasure to hear and engage with everyone's perspectives.
This discussion highlights the importance of striking the right balance between AI and human expertise in engineering change orders.
Well said, David. A harmonious integration of AI and human expertise is crucial for successful deployment.
Thank you, Erik, for taking the time to address our questions and concerns. It has been an insightful discussion.
You're welcome, Emily. I'm glad you found it insightful.
Thanks, Erik, for clarifying various aspects of implementing ChatGPT in engineering change orders. It has increased my understanding.
I'm happy to hear that, Sam. Increasing understanding is the goal of such discussions.
I appreciate the opportunity to participate in this discussion. It has broadened my perspective on AI in engineering.
Thank you, Julia. Hearing different perspectives is invaluable in broadening our horizons.
I've really enjoyed this discussion. It's great to connect with fellow engineers and learn from each other.
I'm glad you enjoyed it, Michael. Connecting and learning are essential aspects of professional growth.
Indeed, this discussion has shed light on the potential benefits and considerations of integrating AI into engineering change orders.
Absolutely, Lisa. Exploring the potential benefits and considerations is crucial for informed decision-making.
Thank you, Erik, for sharing your expertise. It has been a thought-provoking discussion.
You're welcome, Richard. I'm glad you found it thought-provoking.
This discussion reflects the importance of continuous learning and adaptation in the engineering field.
Absolutely, David. Continuous learning and adaptation are essential as engineering practices evolve.
Thank you all once again for your valuable participation in this discussion. Your insights contribute to a holistic perspective on the role of AI in engineering.