Enhancing Tolerance Analysis in Manufacturing Process Analysis: Leveraging ChatGPT Technology
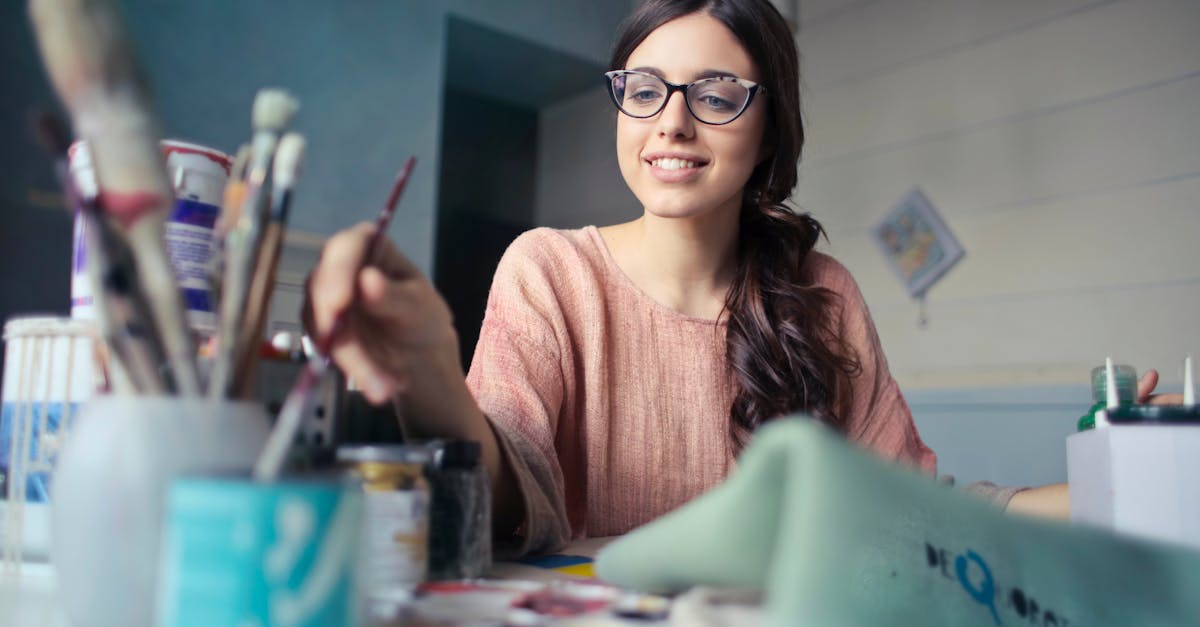
When it comes to manufacturing processes, it is important to ensure that the final product meets the required specifications and standards. One integral aspect of achieving this is through tolerance analysis. Tolerance analysis is a technology that is designed to explain how tolerances can be affected by specific methods or machinery in the manufacturing process.
Understanding Tolerances
In the context of manufacturing, tolerance refers to the allowable variation in a product's dimensions or properties. It is essential to consider tolerances during the design and production stages to ensure that the final product functions as intended. Tolerances can be influenced by various factors, including the manufacturing method, choice of materials, and the precision of the machinery used.
The Importance of Tolerance Analysis
Tolerance analysis plays a crucial role in the manufacturing process as it helps identify potential issues that may arise due to variations in tolerances. By analyzing and understanding tolerances thoroughly, manufacturers can determine the potential impact of these variations on the final product. This information allows them to make informed decisions and implement appropriate measures to ensure the desired quality of the product.
Methods and Machinery Influencing Tolerances
There are various methods and machinery that can affect tolerances in the manufacturing process. These include, but are not limited to, machining, injection molding, casting, and additive manufacturing techniques. Each method has its own set of considerations and limitations when it comes to achieving the desired tolerances.
For example, in machining processes, the choice of cutting tools, machine rigidity, and the type of machining operation can impact the final tolerance levels. Injection molding, on the other hand, requires careful control of process variables such as pressure, temperature, and cooling rates to ensure consistent and precise tolerances. Similarly, casting processes may be influenced by factors such as mold design, material properties, and casting temperature.
Benefits of Tolerance Analysis
The application of tolerance analysis in manufacturing process analysis offers several benefits. Firstly, it helps manufacturers optimize their processes by identifying critical areas where tolerances need to be closely controlled. This enables them to allocate resources more efficiently and reduce unnecessary costs associated with rework or rejection of non-compliant products.
Tolerance analysis also aids in improving product quality. By understanding the impact of tolerances on the functionality and performance of the final product, manufacturers can implement design modifications and process adjustments to achieve the desired level of quality. This can lead to increased customer satisfaction and a competitive advantage in the market.
Furthermore, tolerance analysis provides valuable insights into the capabilities and limitations of the manufacturing methods and machinery used. It allows manufacturers to assess the feasibility of producing complex products with tight tolerances and determine if additional investment in advanced machinery or processes is necessary.
Conclusion
Tolerance analysis is a critical technology in the domain of manufacturing process analysis. By understanding how tolerances can be affected by specific methods or machinery, manufacturers can take proactive steps to optimize their processes, improve product quality, and ensure compliance with required specifications. Incorporating tolerance analysis into the manufacturing workflow ultimately contributes to overall efficiency, cost-effectiveness, and customer satisfaction.
Comments:
Thank you all for taking the time to read my article on enhancing tolerance analysis in manufacturing process analysis using ChatGPT technology. I'd love to hear your thoughts and feedback on this topic!
Great article, Erik! I found your insights on leveraging ChatGPT technology for tolerance analysis really interesting. It seems like this technology has the potential to significantly improve accuracy and efficiency in manufacturing processes.
I agree, Robert! ChatGPT technology can definitely enhance tolerance analysis. It can analyze complex data and provide insightful recommendations, saving a lot of time and resources in the manufacturing process.
However, we should also consider potential limitations of relying solely on ChatGPT for tolerance analysis. AI models like this might not always capture all the nuances and variations in manufacturing processes. It's important to have a comprehensive approach that combines both AI and human expertise.
Absolutely, Paul! While ChatGPT technology is a powerful tool, human expertise is still crucial. It should be seen as a complement to human analysis rather than a replacement. Combining AI capabilities with human knowledge can yield the best results.
I'm intrigued by the idea of using AI for tolerance analysis in manufacturing. It has the potential to simplify complex calculations and provide valuable insights. Erik, do you have any specific examples of how ChatGPT has been successfully employed in this context?
Great question, Samuel! ChatGPT has been utilized in a variety of ways for tolerance analysis in manufacturing. For instance, it can analyze data from sensors and other monitoring devices to identify and predict potential deviations in the manufacturing process. It can also assist in optimizing manufacturing parameters to achieve better tolerance control.
One concern I have regarding ChatGPT technology is its susceptibility to biased training data. As we know, biased data can lead to biased recommendations. How can we ensure that the AI model is fair and unbiased in the context of tolerance analysis?
That's a valid concern, Jennifer. Ensuring fairness and minimizing bias is indeed crucial. It's important to have diverse and representative training data. Thorough validation and testing of the AI model can help address biases. Additionally, continuous monitoring and improvement of the data and model can help reduce biases over time.
Hi Erik, I enjoyed your article and the potential applications of ChatGPT in manufacturing. However, I wonder if the utilization of this technology would require a significant investment for companies? Is it cost-effective for small and medium-sized manufacturers?
Thank you, David! Cost is a crucial aspect to consider. While there may be initial investments required, the long-term benefits of improved accuracy, efficiency, and reduced errors can outweigh the costs. Small and medium-sized manufacturers might need a tailored solution to fit their budget, but the potential benefits make it worth exploring.
I can see the value of using ChatGPT technology in manufacturing, but what about the issue of data privacy and security? Manufacturing processes often involve sensitive data, so how can we ensure the confidentiality of the information analyzed by AI models?
An excellent point, Michelle! Data privacy and security are crucial considerations. Manufacturers should implement robust data protection measures, including encryption and access controls. Collaborating with trusted AI technology providers that prioritize data privacy can help ensure the confidentiality of sensitive information.
Erik, your article has sparked my interest in adopting ChatGPT technology for tolerance analysis. Do you have any recommendations for companies interested in implementing this technology? Any best practices or potential challenges to be aware of?
I'm glad to hear that, Sophie! When considering the implementation of ChatGPT technology, it's important to start with a clear understanding of the problem it aims to solve. Define evaluation metrics to assess its effectiveness. Collaborating with experts in both AI and manufacturing can help navigate challenges and identify the most suitable use cases for your specific needs.
While ChatGPT technology can be valuable for tolerance analysis, what are the potential risks associated with relying too heavily on AI models? How can we maintain human oversight and prevent over-reliance on AI-generated recommendations?
A great question, Daniel! Over-reliance on AI-generated recommendations can be risky. Having human oversight throughout the analysis process is essential. Regular human reviews, verification, and validation of recommendations can help prevent errors and ensure the suitability of AI-generated decisions in the manufacturing process.
Hi Erik, your article highlights the potential benefits of integrating ChatGPT technology into manufacturing processes. I'm curious about the scalability of such solutions. Can ChatGPT handle large-scale manufacturing operations effectively?
Good question, Karen! ChatGPT technology has shown promise in handling large-scale manufacturing operations. However, scalability can depend on factors like the complexity of the manufacturing process and the amount of data involved. It's crucial to evaluate and optimize the AI model's performance to ensure efficiency in large-scale manufacturing scenarios.
Erik, I'm intrigued by the potential of ChatGPT for tolerance analysis. However, I'm concerned about the learning curve that might be involved for manufacturing personnel who are not familiar with AI technologies. How can we address this issue effectively?
Valid concern, Jason! The learning curve can be managed through proper training and education initiatives. Manufacturers should invest in providing comprehensive training programs to familiarize their personnel with the AI technology being implemented. Explaining the benefits and offering ongoing support can help employees embrace and effectively utilize ChatGPT for tolerance analysis.
Erik, your article shed light on a fascinating application of AI in manufacturing. However, are there any specific industries or sectors where ChatGPT technology might be particularly well-suited for tolerance analysis?
Great question, Emily! ChatGPT technology can be applicable across various industries, including automotive, aerospace, electronics, and consumer goods manufacturing. Any industry that requires precise control over manufacturing tolerances and can benefit from accurate analysis and recommendations can potentially leverage this technology effectively.
Erik, I'm curious about the potential challenges or limitations of ChatGPT technology in manufacturing. Are there any situations where it might not be the most suitable approach for tolerance analysis?
Excellent question, Michael! While ChatGPT technology has its strengths, there may be situations where it's not the most suitable approach. For instance, if a manufacturing process involves extremely specialized knowledge or unique constraints that are not effectively captured by the AI model, a different approach might be more suitable. It's crucial to evaluate and tailor the technology to the specific requirements of the manufacturing process.
Erik, your article has convinced me of the potential benefits of leveraging AI for tolerance analysis in manufacturing. However, what kind of computational resources would be required to implement ChatGPT effectively?
I appreciate your enthusiasm, Brian! The computational resources required can vary depending on factors like the complexity of the manufacturing process and the size of the data being analyzed. Cloud-based solutions can be advantageous as they offer scalability and flexibility. Assessing the specific needs of the manufacturing process and consulting with AI experts can help determine the appropriate computational resources for effective implementation.
Erik, I thoroughly enjoyed reading your article. However, do you foresee any potential ethical concerns emerging from the use of ChatGPT technology for tolerance analysis in manufacturing?
Thank you for your kind words, Richard. Ethical concerns should indeed be considered when implementing AI technologies. Transparency, fairness, and accountability throughout the AI model lifecycle are crucial. Manufacturers must ensure that the AI system operates within ethical guidelines, respects privacy, and does not discriminate against certain groups. Responsible AI development and continuous monitoring can help mitigate potential ethical concerns.
Erik, I appreciate the insights provided in your article. In terms of implementation, what kind of data would be required for ChatGPT to perform accurate tolerance analysis?
Thank you, Grace! For accurate tolerance analysis, ChatGPT would require relevant data related to the manufacturing process. This can include sensor data, historical records, specifications, and any other data that captures the variations and deviations in the process. The AI model learns from this data to provide insights and recommendations for improving tolerance control.
Erik, fascinating article! I'm curious about the integration of ChatGPT technology with existing manufacturing systems. How can companies seamlessly incorporate this technology into their processes?
Great question, Lisa! Integrating ChatGPT technology with existing manufacturing systems can be achieved through proper planning and collaboration. Manufacturers should work closely with technology providers to ensure compatibility and establish smooth data exchange and integration processes. Conducting pilot tests and gradually scaling the implementation can help minimize disruptions and ensure a seamless integration.
Hi Erik, your article provided valuable insights into leveraging ChatGPT for tolerance analysis. Can you elaborate on the potential impact of using this technology on product quality in manufacturing?
Hi Oliver! Utilizing ChatGPT for tolerance analysis can have a significant impact on product quality. By providing accurate recommendations for tolerance control, it helps manufacturers identify potential deviations and take corrective actions, improving overall product quality. The technology can reduce errors, improve consistency, and ensure that products meet the desired precision requirements, ultimately enhancing customer satisfaction.
Erik, your article has sparked my interest. Are there any notable real-world case studies or success stories where ChatGPT has been implemented for tolerance analysis in manufacturing?
Absolutely, Megan! Several real-world case studies demonstrate the successful implementation of ChatGPT for tolerance analysis. One example is an automotive manufacturing company that utilized ChatGPT to optimize their manufacturing parameters, resulting in tighter tolerance control and higher product consistency. Another case involves an electronics manufacturer that improved product quality by using ChatGPT technology to identify potential deviations and take timely corrective actions. These success stories highlight the potential benefits of this technology.
Erik, your article provides valuable insights into leveraging ChatGPT technology. Can you elaborate on the potential challenges or limitations of integrating this technology into existing manufacturing workflows?
Certainly, Sara! Integrating ChatGPT technology into existing manufacturing workflows can present challenges. Ensuring compatibility with existing systems, handling data integration, and addressing any initial resistance from employees are some potential hurdles. It's important to plan for these challenges and address them through proper training, change management, and collaboration with experts to ensure smooth integration and maximum effectiveness.
Erik, your article highlights the potential benefits of ChatGPT for tolerance analysis. However, how do we handle situations where the AI model fails to provide satisfactory results or encounter unforeseen scenarios?
That's a valid concern, Peter. In situations where the AI model fails to provide satisfactory results or encounters unforeseen scenarios, it's important to have a fallback plan. This can involve a human-in-the-loop approach, where human experts review and validate the recommendations. Continuous monitoring, feedback loops, and learning from failures can help improve the AI model's performance over time and ensure its adaptability to various scenarios.
Erik, your article is thought-provoking. I'm curious about the potential time and cost savings that can be achieved by leveraging ChatGPT technology for tolerance analysis. Can you provide any insights on this?
Certainly, Anna! ChatGPT technology can significantly reduce the time and cost associated with tolerance analysis. By automating complex calculations and providing accurate recommendations, it eliminates the need for manual analysis, reducing human effort and potential errors. The ability to predict deviations and optimize manufacturing parameters can also streamline the manufacturing process, saving time and minimizing material waste. Overall, it can lead to improved operational efficiency and cost savings.
Erik, your article convinced me of the potential benefits of ChatGPT for tolerance analysis. However, how does this technology handle dynamic changes in manufacturing processes?
Excellent question, Brian! ChatGPT technology can handle dynamic changes in manufacturing processes by continuously analyzing real-time data. It can adapt to evolving conditions and provide timely recommendations based on the latest information. In cases where significant process changes occur, a reevaluation and retraining of the AI model might be necessary to ensure accuracy and relevance in the new manufacturing context.
Erik, your article provided valuable insights into the potential applications of ChatGPT for tolerance analysis. Are there any regulatory considerations that manufacturers need to be aware of when implementing AI technologies in this context?
Regulatory considerations are indeed important, Sophia. When implementing AI technologies, such as ChatGPT, manufacturers must ensure compliance with applicable regulations related to data protection, security, and industry-specific standards. Collaborating with legal experts and staying informed about evolving regulatory frameworks can help manufacturers navigate these considerations effectively.
Erik, your article shed light on the potential benefits of leveraging ChatGPT technology for tolerance analysis. How can manufacturers evaluate the return on investment (ROI) of implementing this technology?
A valid concern, Liam. Evaluating the ROI of implementing ChatGPT technology involves considering factors like the reduction in errors, time savings, improved product quality, and overall cost savings. Comparing the costs of implementing the technology with the identified benefits can help manufacturers assess the return on investment. Conducting pilot studies and monitoring key performance indicators can provide valuable insights into the effectiveness of the technology in meeting the desired goals.
Thank you all for your valuable comments and questions! I appreciate your engagement and interest in leveraging ChatGPT technology for tolerance analysis in manufacturing. If you have any further questions, feel free to ask. Let's continue the discussion!