Improving Operational Efficiency in CNC Programming with ChatGPT
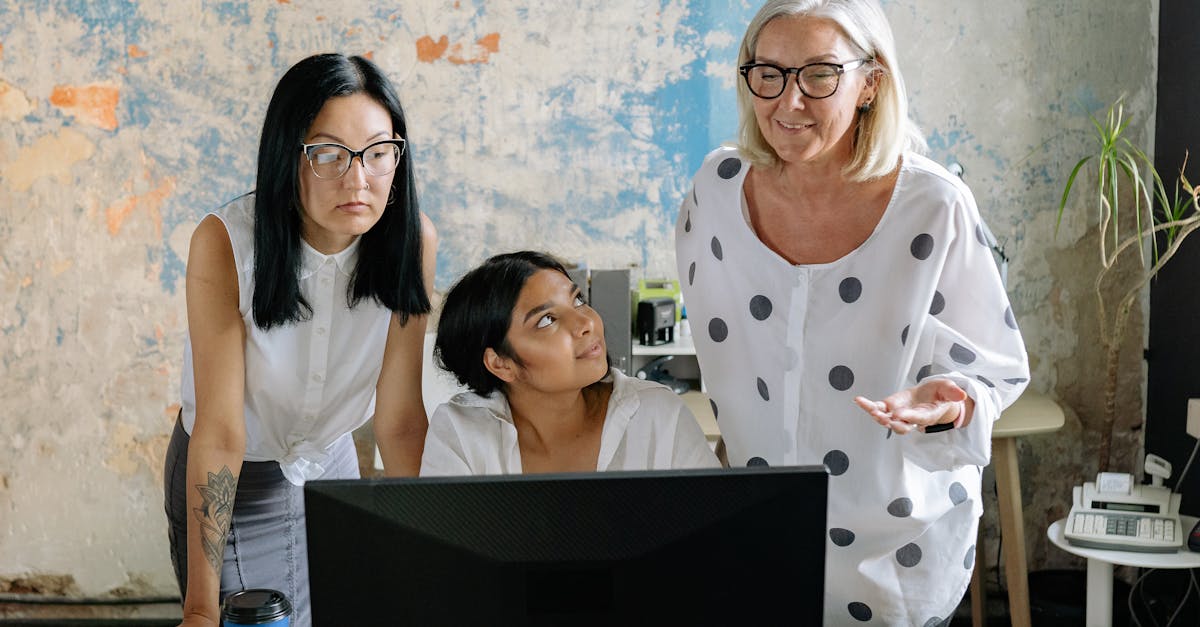
In today's increasingly competitive manufacturing landscape, operational efficiency has become a critical factor for success. Businesses are constantly seeking ways to optimize their processes and maximize productivity. One technology that has proven to be instrumental in achieving these goals is Computer Numerical Control (CNC) programming. By providing data-driven insights, CNC programming can greatly enhance overall operational efficiency.
What is CNC Programming?
CNC programming involves the use of computer software to control complex machinery, primarily CNC machines. These machines use predefined instructions and algorithms to carry out specific tasks with precision and accuracy. CNC programming allows for the creation of detailed instructions that facilitate the manufacturing of intricate parts and components, often with minimal human intervention.
The Role of CNC Programming in Operational Efficiency
CNC programming plays a crucial role in enhancing operational efficiency in several ways:
- Automation: CNC machines can be programmed to automate repetitive tasks, reducing the reliance on manual labor. This eliminates human error, reduces production time, and improves overall product quality.
- Precision: CNC machines consistently produce parts with exceptional accuracy, minimizing the possibility of errors or rework. This precision translates into improved quality control and reduced scrap rates.
- Speed: With CNC programming, manufacturers can significantly reduce cycle times, allowing for faster production and quicker turnaround times. This increased speed enables businesses to meet tight deadlines and satisfy customer demands more efficiently.
- Flexibility: CNC programming allows for easy modifications and adjustments to manufacturing processes. This flexibility enables businesses to adapt to changing production requirements quickly, without incurring significant downtime or additional costs.
- Optimization: By analyzing production data gathered by CNC machines, businesses can identify inefficiencies and areas for improvement. This data-driven approach empowers manufacturers to optimize their processes, minimize wastage, and enhance resource utilization.
Industry Applications
CNC programming has found extensive application across various industries. Some notable examples include:
- Automotive Manufacturing: CNC programming is widely used in the production of automotive components, such as engine parts, transmission systems, and chassis components.
- Aerospace Industry: CNC machines are instrumental in manufacturing critical aerospace components that demand high precision, including turbine blades and structural parts.
- Medical Device Manufacturing: The medical industry extensively relies on CNC programming to produce precise and intricate medical devices and implants.
- Consumer Electronics: CNC programming enables the production of intricate electronic components, ensuring high-quality standards and fast production.
Conclusion
In conclusion, CNC programming has emerged as a vital technology for enhancing operational efficiency in the manufacturing sector. By automating processes, ensuring precision, speeding up production, allowing for flexibility, and enabling optimization, CNC programming drives significant improvements in overall efficiency. Its wide-ranging applications across industries further highlight its versatility and value. Businesses that embrace CNC programming are well-positioned to streamline operations, reduce costs, and gain a competitive edge in today's fast-paced market.
Comments:
This article is very insightful! ChatGPT seems like a great tool for improving operational efficiency in CNC programming.
I agree, James! The ability to use natural language instructions with ChatGPT can make CNC programming more accessible and efficient.
I have some reservations about relying too much on AI for CNC programming. It's a complex field that requires human expertise and understanding of materials and machine capabilities.
I understand your concerns, Paul. However, I think ChatGPT can be a valuable tool when used in conjunction with human expertise. It can help streamline processes and reduce errors.
I've been using ChatGPT for CNC programming and it has saved me a lot of time. It quickly generates code snippets based on my instructions, and I can fine-tune it afterwards.
That's great to hear, Emily! How accurate is the code generated by ChatGPT? Have you encountered any issues with it so far?
The code is usually quite accurate, Sophia. However, sometimes it requires some manual tweaking to ensure optimal performance. Overall, it has been a huge time-saver for me.
Thank you all for your comments and feedback! I appreciate the different perspectives shared.
I'm new to CNC programming. Can someone explain how ChatGPT helps improve operational efficiency?
Certainly, Maria! ChatGPT can help by generating CNC code based on natural language instructions, reducing the time and effort required to write complex code manually.
In addition, Maria, ChatGPT can aid in error reduction and increase productivity by providing quick feedback and suggesting optimizations based on its AI capabilities.
I've seen AI used in other industries, and it has revolutionized efficiency. I'm excited to see how it can benefit CNC programming. Can ChatGPT handle specific industrial requirements well?
ChatGPT is trained on a wide range of sources, including CNC programming domain knowledge. While it may not be perfect, it does a good job of understanding and generating CNC code that meets specific industrial requirements.
That's reassuring, Michael! It's essential to have a tool that understands the unique needs of CNC programming.
I wonder if ChatGPT can also assist in identifying potential issues or conflicts in CNC programs before they are executed.
That's an interesting point, Oliver. Collaborating with AI systems like ChatGPT could help catch potential errors or conflicts that humans might overlook.
While ChatGPT sounds promising, I believe it's important for CNC programmers to still have a deep understanding of the underlying principles. AI should be seen as a tool, not a replacement.
I agree with you, Thomas. AI can never fully replace the expertise and intuition of a skilled CNC programmer.
Absolutely, Thomas and Paul. ChatGPT should complement human knowledge and experience, enhancing the overall efficiency and quality of CNC programming.
I believe that using AI in CNC programming will become increasingly important as the industry evolves. It can be a game-changer for both seasoned professionals and newcomers.
As someone who has been in the industry for years, I'm excited to see how ChatGPT can help us optimize and automate CNC programming processes.
I'm concerned about potential job losses in CNC programming due to AI advancements. How do you see this affecting the industry in the long run?
While AI can streamline certain aspects of CNC programming, Sarah, it's unlikely to replace human programmers entirely. The industry will likely adapt, with professionals focusing more on higher-level tasks.
That makes sense, Michael. It's reassuring to know that AI will likely augment, rather than replace, human expertise in CNC programming.
Can ChatGPT also assist in optimizing toolpaths and reducing material waste?
Absolutely, John! ChatGPT can analyze designs and suggest improvements in toolpaths, helping to reduce material waste and optimize manufacturing processes.
That's fantastic! It would be a significant benefit in terms of cost savings and environmental impact.
I'm curious about the limitations of ChatGPT. Are there any programming scenarios where it may struggle or require significant manual intervention?
Great question, Liam. ChatGPT may struggle with complex or highly customized CNC programming scenarios that require intricate knowledge of specific machines and materials. In such cases, manual intervention would likely be necessary.
Thanks for the clarification, Paul. It's crucial to understand the limitations of any AI tool to make informed decisions while utilizing it.
I'm impressed by how AI is being integrated into various industries. ChatGPT seems like an exciting development for CNC programming.
The potential of AI in CNC programming is vast, but it's essential to embrace it cautiously. Continuous human oversight is necessary.
AI has transformed several fields, and I believe it will do the same in CNC programming. It's exciting to see the possibilities it offers.
ChatGPT shows promise, but we must remember that AI systems are only as good as the data they are trained on. Comprehensive training and ongoing improvements are crucial for its success.
I completely agree, David. Regular updates and improvements to the AI models will ensure that ChatGPT remains valuable and aligns with industry requirements.
Thank you all for the engaging discussion! It's evident that there are both excitement and valid concerns about using AI in CNC programming. Moving forward, collaboration between AI and human expertise will shape the future of the industry.
What training data has been used to fine-tune ChatGPT for CNC programming? Is it specific to certain machine types or materials?
ChatGPT has been trained on a diverse dataset that includes general programming knowledge and specific CNC programming domain information. While it covers a wide range of machine types and materials, some customization may still be required for unique scenarios.
Thank you for the clarification, Michael. It's good to know that ChatGPT has been trained on a broad dataset to handle different aspects of CNC programming.
Are there any privacy concerns related to using AI tools like ChatGPT for CNC programming?
That's an important question, Sarah. When using AI tools, it's crucial to ensure that sensitive information and proprietary designs are appropriately protected.
Absolutely, Linda. Data security and privacy measures should be a top priority when adopting AI solutions.
Overall, ChatGPT seems like a powerful tool that can greatly benefit CNC programming. It's exciting to see how AI continues to enhance different industries.
I agree, Daniel! Advancements in AI have the potential to revolutionize CNC programming and unlock new levels of efficiency and productivity.
Thank you all for your insights! As someone new to CNC programming, this article and discussion have given me a better understanding of the possibilities and considerations when using AI tools like ChatGPT.
Indeed, Maria! Don't hesitate to reach out if you have any questions or need further guidance. The CNC programming community is supportive.
You're welcome, Maria! Feel free to ask any further questions you may have as you dive deeper into the world of CNC programming.
We're here to help, Maria! CNC programming can be complex, but with the right tools and knowledge, you'll be able to excel.
Best of luck with your CNC programming journey, Maria! Remember to mix AI tools like ChatGPT with your expanding expertise to achieve optimal results.
Thank you all once again. I appreciate your active participation in this discussion. Let's continue to explore the possibilities and advancements in CNC programming with AI!