Improving Quality Control and Process Efficiency in Statistics Technology with ChatGPT
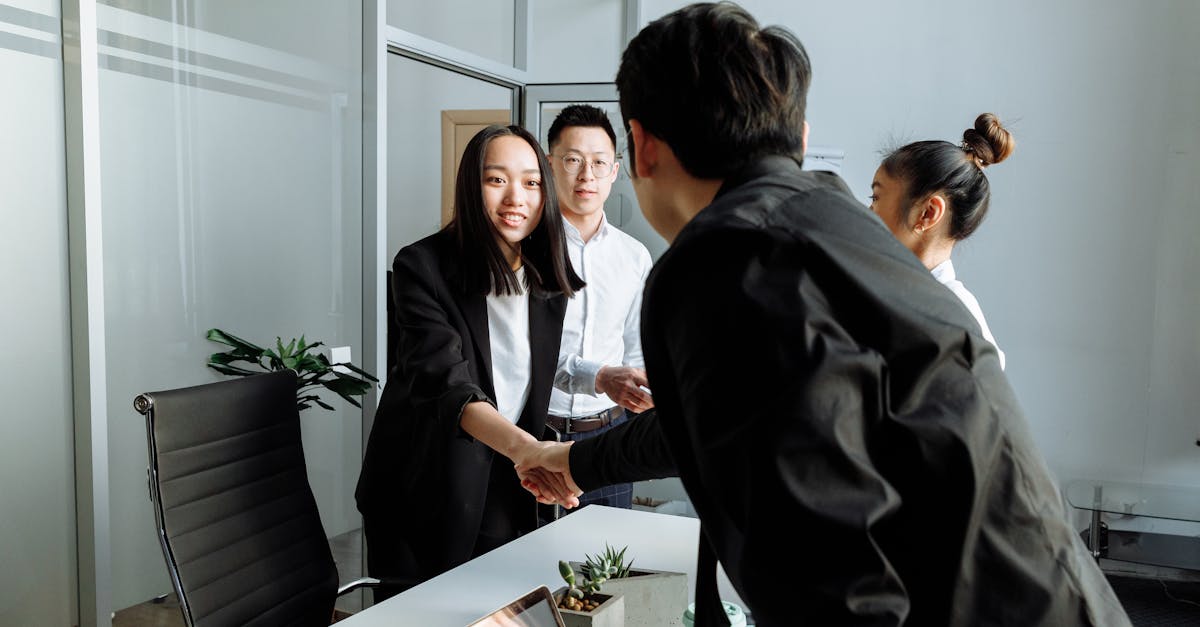
In today's modern world, businesses are constantly striving to enhance their operations and deliver high-quality products or services to their customers. This pursuit of excellence has given rise to various methodologies and techniques to ensure that processes are upheld to the highest standards. One such field that plays a critical role in this endeavor is statistics. By harnessing statistical analysis, businesses can effectively monitor and improve their processes, ultimately leading to enhanced quality control and process improvement.
Statistical Process Control (SPC)
Statistical Process Control (SPC) is a widely used method for monitoring and controlling processes to ensure that they operate within predefined limits. SPC involves collecting and analyzing data to understand and minimize process variation, identify potential issues, and implement corrective actions. This technique allows organizations to maintain process stability and ensure products or services consistently meet customer requirements.
Control Charts
In SPC, control charts are a vital tool for visualizing process data and identifying any trends or patterns that deviate from the desired performance. Control charts help organizations monitor process stability over time by plotting sample data points and control limits. By observing the control chart patterns, businesses can quickly spot any variations or anomalies in the process performance, enabling prompt corrective actions and preventive measures. Common types of control charts include the X-bar chart, R-chart, and individuals chart.
Process Capability Analysis
Process capability analysis is another statistical tool used in quality control to determine how well a process meets customer requirements. It involves assessing the inherent variability of a process and comparing it with specification limits. By calculating capability indices such as Cpk and Cp, organizations can gain insights into their process performance and identify areas for improvement. Process capability analysis helps businesses set realistic goals, optimize processes, and achieve desired levels of quality.
Six Sigma Methodologies
Six Sigma is a set of techniques and tools widely utilized in quality management to minimize process variation and achieve process improvement. It combines statistical analysis with a structured approach to identify and eliminate defects, reduce waste, and enhance customer satisfaction. Six Sigma methodologies embrace the DMAIC (Define, Measure, Analyze, Improve, Control) framework, which provides a systematic approach for problem-solving and process optimization. By integrating statistical tools and techniques within the Six Sigma framework, organizations can improve process performance and achieve near-perfect quality levels.
Technques for Quality Improvement
In addition to SPC, control charts, process capability analysis, and Six Sigma methodologies, several other statistical techniques contribute to quality improvement. These techniques include hypothesis testing, designed experiments (such as Design of Experiments - DOE), regression analysis, and root cause analysis. Each technique plays a specific role in understanding and enhancing quality control processes. By leveraging these statistical techniques, businesses can identify areas of improvement, make data-driven decisions, and implement effective quality control measures.
Overall, the role of statistics in quality control and process improvement cannot be overstated. With the advent of advanced technologies like ChatGPT-4, organizations can now rely on virtual assistants to enhance their understanding of statistical tools and methodologies. ChatGPT-4 can provide real-time explanations and insights into statistical process control, control charts, process capability analysis, Six Sigma methodologies, and techniques for quality improvement. This invaluable tool enables businesses to make informed decisions, optimize processes, and ultimately deliver superior products or services to their customers.
Comments:
Thank you all for taking the time to read my article on improving quality control and process efficiency in statistics technology with ChatGPT. I would love to hear your thoughts and perspectives!
Great article, Virginia! I think ChatGPT has the potential to revolutionize quality control in statistics technology. The ability to automate processes and provide real-time assistance is game-changing.
I agree with you, Robert. ChatGPT can definitely enhance efficiency by reducing manual errors and providing immediate support. It allows researchers to focus more on analyzing data rather than troubleshooting technical issues.
While I see the benefits, I'm also concerned about potential biases in the data that ChatGPT relies on. How do we ensure that the training data is diverse enough to avoid reinforcing existing biases?
Valid point, Michael. Addressing biases is crucial. In the case of ChatGPT, OpenAI has implemented measures to improve data diversity during training, but ongoing efforts are required to ensure a balanced and unbiased system.
I appreciate the effort, Virginia. Diversity in training data is vital to avoid perpetuating biases. It's important for developers to remain vigilant and continuously fine-tune the system's algorithms to mitigate any biases that may emerge.
One concern I have is the potential overreliance on ChatGPT. It's a powerful tool, but we shouldn't neglect the importance of human expertise and critical thinking in quality control. It should complement, not replace, human judgment.
Absolutely, Emily. ChatGPT is designed to assist and augment human expertise, not replace it. It's important to strike a balance and leverage both machine intelligence and human judgment for optimal results in quality control.
ChatGPT sounds promising, but I'm concerned about potential security risks. How can we ensure that the system doesn't unintentionally expose sensitive data or vulnerabilities?
Valid concern, Daniel. OpenAI understands the importance of security. They are committed to implementing robust security protocols and regularly testing the system to identify and address any potential vulnerabilities.
In addition to OpenAI's efforts, it's also crucial for organizations implementing ChatGPT to have strong security measures in place. Training staff on data security and access controls can help minimize risks.
I find the idea of ChatGPT fascinating. How easy is it for someone with limited technical expertise to utilize and benefit from this technology?
Good question, Alice. OpenAI has made efforts to make ChatGPT as user-friendly as possible. While some technical understanding may be helpful, the aim is to provide a tool that can be used by individuals with various levels of expertise.
That's reassuring, Virginia. Accessibility and usability are key factors for widespread adoption. It would be great to see more organizations integrating ChatGPT into their quality control processes.
I agree, Thomas. Making ChatGPT user-friendly will encourage more users to embrace the technology. It has the potential to streamline processes and improve efficiency across a wide range of industries.
While ChatGPT can be a valuable tool, do you think there is a risk of over-reliance on AI in quality control? How do we maintain a balance?
That's a valid concern, Sarah. Over-reliance on AI can diminish human creativity and intuition, which are often crucial in quality control. It's important to use AI as a supporting tool while still valuing human insights.
Well said, Karen. Leveraging AI technology should augment human capabilities, not replace them. By maintaining a balance and combining the strengths of both AI and human expertise, we can achieve better quality control outcomes.
Another concern is the potential for ChatGPT to make errors or provide incorrect guidance, which could adversely impact the quality control process. How reliable is the system in practice?
Good point, Daniel. While ChatGPT is impressive, it's important to acknowledge that it's not infallible. Extensive testing, ongoing improvements, and regular human review are necessary to ensure the system's reliability.
Indeed, Robert. OpenAI is dedicated to continuously refining ChatGPT's accuracy and reliability. Human oversight and feedback play a crucial role in identifying and rectifying any errors or shortcomings.
Continuous improvement is key. It's important for organizations utilizing ChatGPT to maintain a feedback loop and provide regular updates to the system based on real-world experiences. This iterative approach helps build trust in the technology.
I can see ChatGPT being incredibly helpful for repetitive and time-consuming tasks. It has the potential to significantly boost process efficiency in statistics technology.
Absolutely, Lucas. By automating mundane tasks, ChatGPT allows researchers and statisticians to focus on more complex and intellectually stimulating aspects of their work.
ChatGPT's ability to provide real-time assistance also contributes to process efficiency. Researchers can obtain immediate support, reducing their reliance on lengthy troubleshooting or waiting for assistance.
That's true, Sarah. Time is a valuable resource, and ChatGPT can help save significant amounts of it by speeding up problem-solving and reducing downtime.
I think maintaining human oversight is critical, especially when dealing with complex statistical analyses. AI can provide assistance, but human judgment and expertise should be the ultimate decision-making factor.
Well said, Jeanne. AI should be seen as a valuable aid in the decision-making process, but human judgment and experience play an irreplaceable role in understanding complex statistical nuances.
Are there any potential limitations or challenges we should be aware of when implementing ChatGPT in quality control processes?
Certainly, Alice. One challenge is the potential for ChatGPT to generate plausible but incorrect answers. Human review is essential to catch such errors and prevent misleading guidance.
You're absolutely right, Robert. Careful human review is necessary to double-check ChatGPT's responses and ensure the accuracy and validity of the guidance it provides.
Another limitation may be the inability of ChatGPT to understand highly specialized or domain-specific statistical concepts. How can this be addressed?
Excellent point, Daniel. While ChatGPT is designed to be versatile, it may struggle with extremely specialized domains. Providing supplementary resources and knowledge bases tailored to specific fields can help overcome this limitation.
Including domain experts in the development and training phases can also help fine-tune ChatGPT for specialized statistical concepts. Collaboration between AI developers and human experts is crucial for optimal results.
Agreed, Michael. Involving domain experts ensures that ChatGPT becomes more adept at handling specific statistical challenges, improving its overall usability and accuracy in specialized fields.
Some users might also find it challenging to adapt to a new tool like ChatGPT, particularly if they are accustomed to traditional quality control processes. Proper training and support can help address this concern.
Absolutely, Lucas. Organizations should invest in adequate training programs, workshops, and user support to ensure a smooth transition and successful integration of ChatGPT into existing quality control processes.
I'm curious to know if there are any significant cost implications associated with implementing ChatGPT for quality control. Could it become a prohibitive factor for smaller organizations?
That's a valid concern, Jennifer. While some costs may be involved in implementing and maintaining ChatGPT, OpenAI aims to provide affordable and accessible options to cater to organizations of various sizes and budgets.
Another factor to consider is the potential long-term cost savings that ChatGPT can bring by reducing manual work and improving efficiency. It's important to evaluate the overall cost-benefit analysis.
Are there any privacy concerns associated with ChatGPT? How can organizations ensure the privacy of sensitive data during interactions with the system?
Privacy is crucial, Sarah. OpenAI takes privacy seriously and has implemented measures to protect sensitive data. Organizations must also adhere to best practices in data privacy and implement appropriate security measures when integrating ChatGPT.
Data encryption and secure data handling protocols play an important role in ensuring privacy. Organizations must be diligent in maintaining a secure environment when using ChatGPT.
It's worth considering whether sensitive data should be anonymized or masked before interacting with ChatGPT to provide an additional layer of protection.
How customizable is ChatGPT? Can organizations tailor it to fit their specific quality control requirements?
Good question, Alice. While ChatGPT has certain customization options, organizations may need to work closely with AI developers to ensure that it aligns with their specific quality control needs.
Having the ability to customize ChatGPT for specific quality control requirements would greatly enhance its usefulness. It would allow organizations to tailor the tool to their unique workflows and processes.
Care should be taken to balance customization with maintaining the integrity of the underlying system. Striking the right balance ensures that organizations benefit from flexibility while still leveraging the power of ChatGPT's core capabilities.
Customizability is important, but it's also crucial to consider the potential limitations and biases that can arise from excessive customization. Finding the right balance is key.
Indeed, Jennifer. A balance must be struck to ensure that customization complements the system's capabilities without compromising the integrity and accuracy of the guidance it provides.