Improving Quality Control in Countertops Technology with ChatGPT
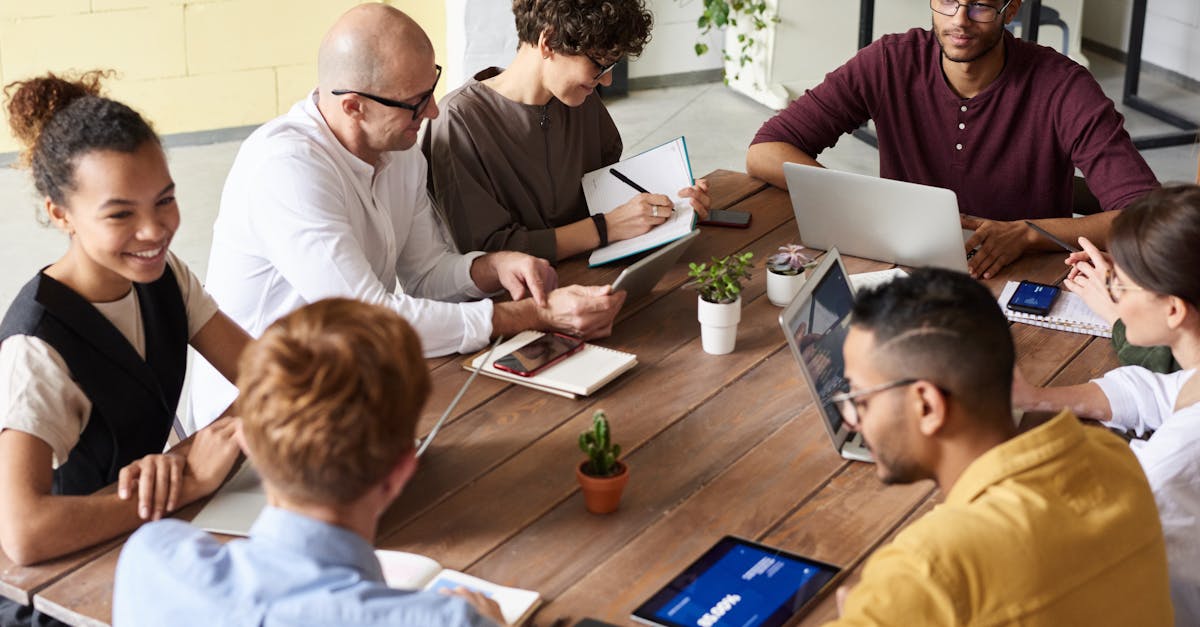
In today's fast-paced manufacturing industry, ensuring the highest quality standards is crucial. Quality control processes play a vital role in identifying defects, improving efficiency, and ensuring customer satisfaction. While quality control traditionally involved manual inspection and testing, advances in technology have brought forth innovative solutions to automate and streamline these processes.
Countertops and Quality Control
Countertops are a significant component in various industries such as kitchen and bathroom remodeling, hospitality, and healthcare. The quality of countertops is of utmost importance, as it directly impacts the overall aesthetics, durability, and functionality of the spaces they are installed in. Ensuring the highest quality standards for countertops is essential to meet customer expectations and maintain a good reputation.
The Role of Automation in Quality Control
Automation has revolutionized the manufacturing industry, and quality control is no exception. With the advent of artificial intelligence (AI), machine learning, and natural language processing, advanced chatbot technologies have emerged, offering an opportunity to automate and streamline quality control processes.
Introducing ChatGPT-4
ChatGPT-4 is an AI-powered chatbot developed by OpenAI. It is designed to understand and generate human-like text, making it an ideal tool for automating quality control processes. Leveraging ChatGPT-4's capabilities, manufacturers can build intelligent systems tailored to their specific quality control requirements.
Streamlining Defect Detection
One of the primary applications of ChatGPT-4 in quality control is streamlining defect detection. By training the chatbot on a vast dataset of known defects, it can efficiently analyze and identify potential issues in countertops. By automating this process, manufacturers can significantly reduce inspection time and improve overall efficiency.
Enhancing Communication and Collaboration
Quality control often involves multiple stakeholders, including product designers, engineers, quality assurance teams, and production managers. ChatGPT-4 can facilitate seamless communication and collaboration among these stakeholders by offering real-time feedback and suggestions. This helps in resolving quality-related issues promptly, ensuring continuous improvement in the manufacturing process.
Providing Customer Support
Countertop manufacturers often receive inquiries and support requests from customers regarding product specifications, installation guidelines, and warranty information. ChatGPT-4 can act as a virtual customer support assistant, handling customer queries and providing accurate information. This reduces the burden on human customer support teams and improves response times.
Real-Time Analytics and Insights
ChatGPT-4 can be integrated with quality control systems to collect real-time data and generate valuable insights for manufacturers. By analyzing data captured during the quality control process, it can identify patterns, trends, and areas of improvement. These insights enable manufacturers to make data-driven decisions, optimize production processes, and enhance product quality.
Conclusion
The integration of ChatGPT-4 in quality control processes for countertops offers immense benefits to manufacturers. By automating defect detection, enhancing communication and collaboration, providing customer support, and generating real-time analytics, ChatGPT-4 streamlines quality control processes, improves efficiency, and elevates customer satisfaction. Embracing AI-powered solutions like ChatGPT-4 is a step forward in the pursuit of excellence in the manufacturing industry.
Comments:
Great article, Jane! I never thought about how AI can improve quality control in countertop technology. It's fascinating to see how ChatGPT is being utilized in different industries.
Samantha, do you think the implementation of AI in quality control will replace human inspectors, or will it rather augment their capabilities?
Andrew, I believe AI will augment human capabilities rather than replacing inspectors entirely. While AI systems can detect certain defects efficiently, human judgment and decision-making are still essential in complex quality control processes.
Exactly, Samantha! AI can assist inspectors but can't replace their expertise and critical thinking. It's a powerful tool to enhance their work.
Oliver, you're right! AI can help automate the identification of defects, but it still requires human validation and decision-making.
I completely agree, Jessica! Human validation is crucial to ensure that any identified defects are accurately classified and appropriate actions are taken.
Samantha, you're absolutely right. Human expertise ensures that AI-driven quality control remains accurate and reliable.
Agreed, Samantha! Human judgment is invaluable in maintaining the overall quality and ensuring customer satisfaction.
That's a great point, Samantha and Oliver. A combination of AI and human expertise can lead to more accurate and efficient quality control processes.
I agree, Samantha. The application of AI in improving quality control is impressive. It can help streamline processes and reduce errors. Looking forward to seeing more advancements in this area.
Jane, your article provided valuable insights into the potential benefits of using ChatGPT in the countertop industry. I appreciate how you explained the advantages it brings. Well done!
Interesting read, Jane. I wonder how widely ChatGPT is currently used in the countertop industry. Are there any practical examples you can share?
Robert, while I'm not sure about specific examples, I've heard of companies using ChatGPT to identify small imperfections in countertops during the manufacturing process.
Thank you all for your positive feedback! Samantha, Michael, Emily, and Robert, I'm glad you found the article informative. Robert, ChatGPT is still in the early stages of adoption in the countertop industry, but there are a few companies experimenting with its use for quality control. Exciting times ahead!
I enjoyed reading your article, Jane. It's impressive how AI technology is making its way into various industries. It opens up new possibilities.
Jane, could you please elaborate on how ChatGPT improves quality control in countertops? I'd like to know more about the specifics.
Marcus, ChatGPT can improve quality control by analyzing images of countertops and identifying any defects or inconsistencies. It enhances the efficiency of inspections and enables faster detection of issues that might be missed by manual inspections alone.
Jane, do you foresee any challenges in implementing ChatGPT or similar AI systems in quality control for countertops?
Christine, one challenge in implementing ChatGPT is ensuring that the AI system is trained on a diverse and representative set of countertop images to avoid biases. Additionally, adapting the technology to accommodate various countertop materials and finishes can be a complex task.
Good point, Jane. Overcoming biases and ensuring AI systems can handle different countertop variations will be important for widespread adoption.
Another challenge to consider, Jane, is the need to establish trust in the AI system's decisions. How can companies address potential concerns about the reliability of AI-driven quality control?
Christine, ensuring transparency and interpretability of AI systems' decisions is crucial for establishing trust. By providing explanations for the AI's outputs and regularly validating and auditing the system's performance, companies can address concerns and build confidence in the reliability of AI-driven quality control.
I couldn't agree more, Jane. AI's impact goes beyond efficiency. It contributes to enhanced quality and customer satisfaction, ultimately driving business success.
Thank you, Jane. Establishing transparency around AI decision-making and building a clear feedback loop with human experts can indeed address concerns and enhance trust in AI-driven quality control.
Thank you, Jane. It's impressive how AI can enhance traditional quality control methods, saving time and resources.
Jane, do you think AI-driven quality control will become a standard practice in the countertop industry in the near future?
Marcus, while it may take time to become a standard practice, I believe AI-driven quality control has immense potential in the countertop industry. As the technology matures and adoption increases, it could become an essential component of quality assurance processes.
That's fascinating, Jane. The efficiency gains and improved accuracy in inspections can potentially lead to significant cost savings in countertop production.
Exactly, Jane. Companies can benefit not only from improved quality but also from reduced resources spent on rework and potential customer complaints.
I totally agree with the potential of AI in quality control. It can help detect defects that might be hard to notice with the naked eye.
Great article, Jane! It's exciting to see AI being used to enhance quality control. I can envision a future where AI systems like ChatGPT play a crucial role in ensuring product excellence.
Jane, your article shed light on an innovative use of AI. It's fascinating to see how technology continues to revolutionize different industries.
Great article, Jane. AI applications continue to amaze me. It's exciting to think about the possibilities in improving quality control across different industries.
Jane, I'm curious about the potential cost savings of using ChatGPT in quality control. Are there any estimates on how much it can reduce inspection costs?
Jennifer, the potential cost savings can vary depending on the scale of operations and the quality control processes in place. While it's hard to provide precise estimates, ChatGPT has the potential to reduce inspection costs by automating certain aspects and making the process more efficient.
Great article, Jane! It's impressive to see how AI-powered technology like ChatGPT is transforming traditional industries.
This article highlights the importance of embracing AI in quality control. It has the potential to revolutionize various sectors, including the countertop industry.
Jane, I found your article very informative. AI's role in quality control can ensure consistent standards and improved customer satisfaction. Well done!
Great job on the article, Jane. AI can definitely help raise the bar in the quality control processes of the countertop industry.
Jane, your article beautifully explains the practical implications of incorporating AI in quality control. It's impressive how technology continues to transform industries for the better.
It's interesting to see how AI can elevate quality control measures in the countertop industry. Jane, your article provides a comprehensive overview of the subject.
Jane, your article showcases the exciting advancements happening in quality control. It's inspiring to see how AI can positively impact industries across the board.
The use of AI in quality control can help ensure consistency and minimize human error. Your article, Jane, highlights the potential benefits of AI in the countertop industry.
Jane, your article is a great example of how AI can be harnessed to improve quality control processes in traditional industries. Well-written and insightful!
Jane, your article provides an interesting perspective on the potential of AI in quality control. It's great to see technology making a positive difference in traditional industries.
The application of AI in quality control opens up new possibilities for improving product quality and reducing defects. Well-explained, Jane!
Jane, your article highlights the transformative power of AI in quality control. It's a fascinating area where technology can make a significant impact.
Well done, Jane! Your article emphasizes the importance of embracing AI for improving quality control in countertop technology.
Jane, I found your article both informative and thought-provoking. AI's role in quality control is promising, and it's exciting to see these advancements.
Jane, your article demonstrates the potential of AI in enhancing quality control processes. It's fascinating to see how technology is shaping different industries for the better.