Improving Quality Control in Performance Consulting with ChatGPT
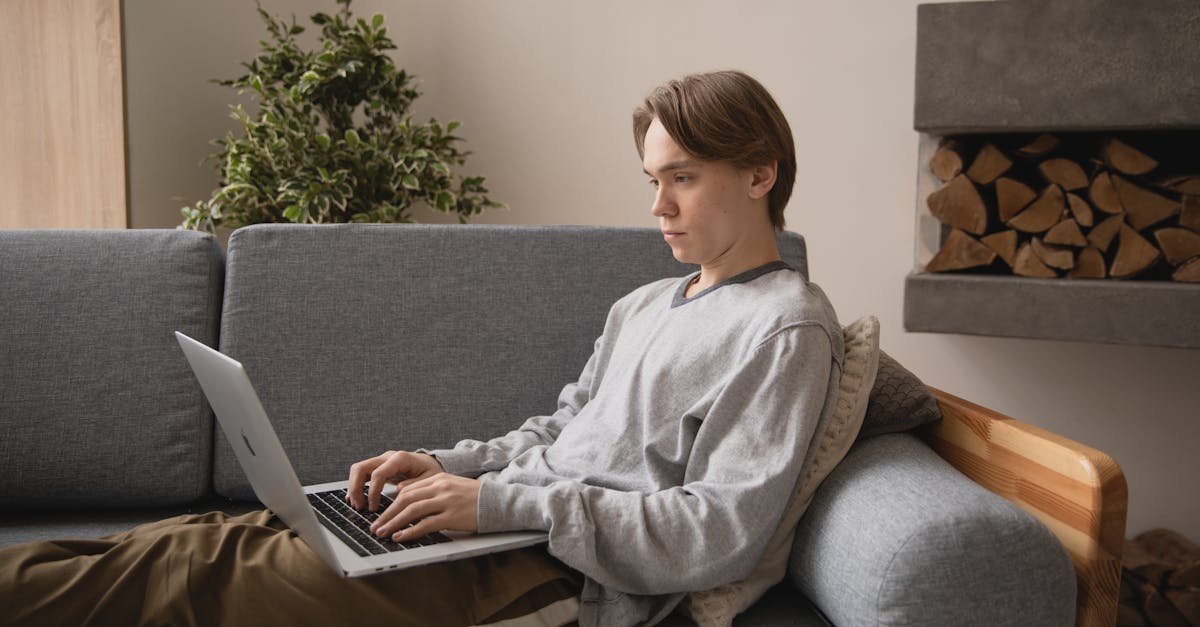
Quality control plays a critical role in ensuring that products meet the highest standards and customer expectations. To achieve this, companies can employ various methodologies, and one such approach gaining popularity is performance consulting. This article explores how performance consulting can revolutionize quality control, allowing businesses to monitor and analyze product quality, predict and prevent defects, and ultimately enhance overall efficiency and customer satisfaction.
What is Performance Consulting?
Performance consulting is a strategic process employed to identify and close the gap between desired and actual performance. In the context of quality control, performance consulting focuses on optimizing quality-related processes and outcomes to achieve organizational objectives. It involves analyzing the root causes of product defects, developing effective solutions, and implementing strategies to prevent recurrence.
Monitoring and Analyzing Product Quality
Performance consulting tools and techniques enable organizations to monitor and analyze product quality effectively. By collecting and analyzing data from various sources such as manufacturing processes, customer feedback, and quality control checkpoints, businesses can identify patterns and trends that impact product quality. This information can then be used to implement targeted improvements and ensure that products consistently meet or exceed customer expectations.
Predicting and Preventing Defects
One of the key advantages of performance consulting in quality control is its ability to predict and prevent defects before they occur. By employing advanced data analysis techniques, companies can identify potential issues and take proactive measures to eliminate them. For instance, by analyzing historical data, organizations can spot recurring defects and develop preventive measures to address the underlying causes. These measures may include process improvements, staff training, or technology upgrades, which can help prevent future defects and enhance product quality.
Enhancing Overall Efficiency and Customer Satisfaction
Performance consulting aims to improve overall efficiency by streamlining quality control processes and eliminating bottlenecks. By identifying performance gaps and implementing targeted improvements, businesses can optimize product quality and reduce waste, resulting in cost savings and increased productivity. Moreover, by focusing on continually improving product quality, organizations can enhance customer satisfaction, leading to increased customer loyalty and positive brand reputation.
Conclusion
In today's competitive business landscape, performance consulting has emerged as a critical tool for achieving quality control excellence. By monitoring and analyzing product quality, predicting and preventing defects, and enhancing overall efficiency and customer satisfaction, organizations can stay ahead of the competition and meet or exceed customer expectations consistently. Embracing performance consulting in quality control can lead to improved products, stronger customer relationships, and sustainable business success.
Comments:
Thank you all for your insightful comments on my article!
Great article, Pennee. I found ChatGPT to be a valuable tool in improving quality control for performance consulting. It helps in streamlining the communication process with clients.
I agree, Michael. ChatGPT is particularly useful in ensuring consistency and accuracy in the recommendations provided to clients.
Absolutely! ChatGPT has significantly improved our ability to address client queries and concerns promptly. It has been a game-changer for our team.
I have some concerns about the reliability of ChatGPT. It relies heavily on pre-existing data, which may limit its ability to consider new perspectives. How do you address this, Pennee?
Valid point, Rachel. While ChatGPT does have its limitations, one way to address this is through continuous training and updating of its datasets. This helps in incorporating new perspectives and ensuring more reliable responses.
I also think it's important to have human oversight and review when using ChatGPT. It helps in catching any inaccuracies or biases that may arise.
Absolutely, Roger. Human oversight is crucial in maintaining quality control and addressing any concerns that arise from using automated tools like ChatGPT. It's necessary for a balanced approach.
Pennee, how do you ensure data security when using ChatGPT? As consultants, handling client data is a top priority.
Data security is indeed a major concern. We use secure servers and follow strict protocols to ensure the confidentiality of client data. We make sure ChatGPT is only accessible to authorized personnel.
I'm curious about how ChatGPT handles complex queries. Can it effectively analyze intricate performance-related questions?
Great question, Daniel. ChatGPT has shown promising results in handling complex queries. It can effectively analyze intricate performance-related questions and provide insightful recommendations. However, for highly specialized or domain-specific queries, human expertise may still be required for accurate guidance.
While ChatGPT offers many benefits, do you think it will replace the need for human performance consultants in the future?
That's an interesting question, Sophia. While ChatGPT is a powerful tool, I believe human performance consultants will always be necessary. They bring domain expertise, empathy, and a deeper understanding of client needs, which automated tools alone cannot fully replace.
I've used ChatGPT in my performance consulting work and have found it to be quite efficient. It saves me a lot of time in communication with clients. Highly recommended!
I have reservations about the potential biases in ChatGPT's responses. How are ethical considerations addressed to ensure fair and unbiased consulting advice?
Ethical considerations are critical, Jennifer. We review and validate the training datasets to mitigate biases as much as possible. Additionally, we encourage feedback from clients to identify any potential biases and improve the system's fairness.
I believe it's essential to have a diverse team of consultants to address biases in ChatGPT's responses effectively. Different perspectives help in ensuring a more balanced and fair consulting approach.
Does ChatGPT provide multilingual support? As a consultant working with clients globally, language capabilities are crucial.
Indeed, David. ChatGPT does offer multilingual support, which is beneficial for consultants working with diverse clients across different languages. It helps in improving the accessibility and effectiveness of our consulting services.
It's fascinating how AI technology like ChatGPT is transforming the consulting industry. Thanks for sharing your insights, Pennee!
I'm wondering about the integration process of ChatGPT into existing performance consulting workflows. Are there any challenges or considerations to keep in mind?
Integration can indeed pose challenges, Samuel. It requires adapting existing workflows to incorporate ChatGPT effectively. Ensuring proper training for consultants, addressing potential resistance to change, and conducting periodic evaluations are crucial to successful integration.
I believe providing comprehensive training and guidance to consultants during the integration process is paramount. It helps in smooth adoption and utilization of ChatGPT in performance consulting.
How does ChatGPT handle context-specific information? Can it capture the intricacies of various industries and tailor recommendations accordingly?
Great question, Olivia. ChatGPT's ability to provide context-specific information relies on the training it receives. While it can capture industry-specific nuances to an extent, human expertise is crucial for highly specialized or unique industry requirements.
I agree with Pennee. While ChatGPT is a powerful tool, the tailored expertise of human performance consultants is vital to truly understand the intricacies of different industries and provide the best possible recommendations.
Are there any potential risks in relying heavily on ChatGPT for performance consulting? What are the key precautions to consider?
Risks can exist, Eric. Key precautions include proper training of consultants to effectively utilize ChatGPT, maintaining human oversight for quality control, addressing biases, and acknowledging its limitations. It's important to strike a balance between automation and human expertise.
Regularly assessing the performance and accuracy of ChatGPT is crucial to mitigate any potential risks in relying on it. Continuously improving the system helps maintain its effectiveness in performance consulting.
Has ChatGPT been implemented in performance consulting extensively, or is it still in the early stages of adoption?
ChatGPT's implementation in performance consulting is gaining momentum, Sophie. Though it's still relatively new, many consultants and organizations have recognized its potential and started incorporating it into their workflows. The widespread adoption is growing steadily.
What kind of accuracy levels can be expected from ChatGPT in providing performance consulting advice?
ChatGPT's accuracy levels depend on the quality and relevancy of the training data it receives. While it can provide helpful recommendations, it's important to validate its outputs and leverage human expertise to ensure the highest possible accuracy for performance consulting advice.
I'd like to know more about the user interface and user experience of ChatGPT. How intuitive is it for consultants to use in their daily work?
The user interface and experience of ChatGPT are designed to be intuitive and user-friendly, Samantha. Consultants can interact with it through text inputs and receive responses that are easy to understand and work with. It aims to enhance productivity and streamline communications in performance consulting.
Have there been any notable success stories or case studies of using ChatGPT in performance consulting? I'd love to hear some examples.
Absolutely, William. Several success stories have emerged with ChatGPT in performance consulting. One notable example is a consulting firm that reduced response times to client queries by 40% and improved overall client satisfaction through streamlined communication using ChatGPT.
I have seen an organization effectively leverage ChatGPT to provide consistent, high-quality recommendations to their performance consulting clients across different regions. It has significantly enhanced their consulting capabilities.
Thank you all for your valuable comments and questions. Your engagement is greatly appreciated!