Improving Quality Control with ChatGPT: A Lean Thinking Approach
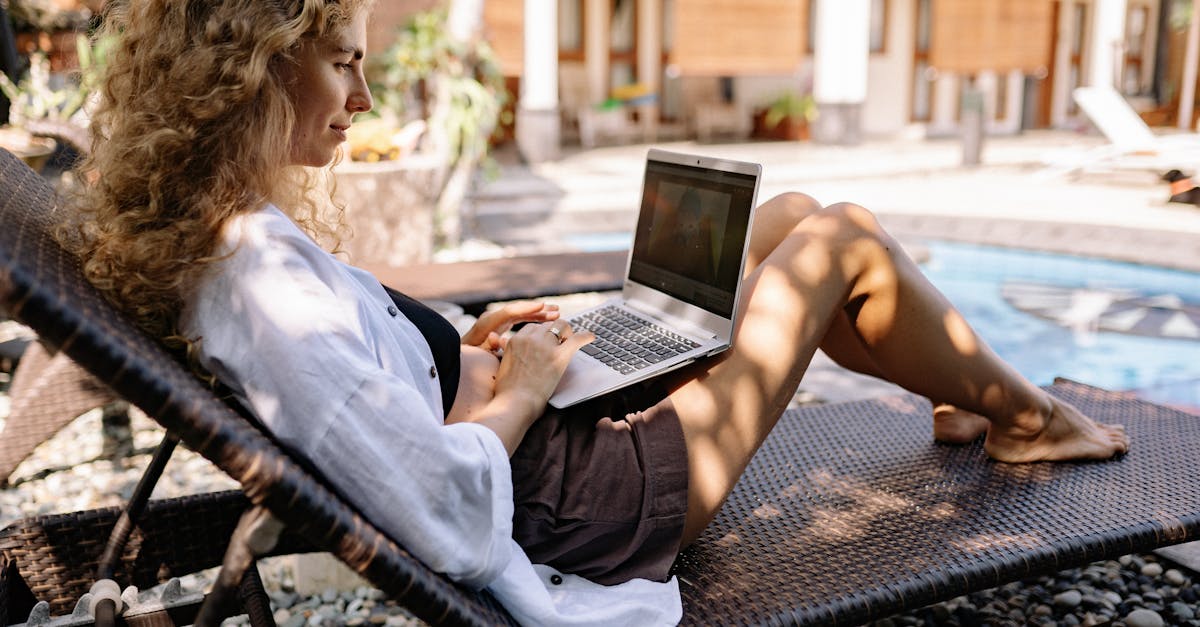
Lean thinking is a management philosophy that focuses on identifying and eliminating waste in order to increase efficiency and improve overall quality. It originated from the Toyota Production System and has since been adopted by various industries worldwide. In the realm of quality control, lean thinking can bring significant benefits, and with the advent of advanced technologies like ChatGPT-4, the possibilities are even greater.
What is Lean Thinking?
Lean thinking is based on the concept of continuously improving processes by reducing or eliminating non-value-added activities. It involves streamlining workflows, empowering employees, and fostering a culture of continuous improvement. By focusing on quality and efficiency, lean thinking aims to enhance customer satisfaction, reduce costs, and minimize waste.
Quality Control and Lean Thinking
In quality control, lean thinking emphasizes the need for error prevention rather than detection. By implementing lean principles, organizations can standardize processes, create clear quality standards, and provide ongoing training to employees. This approach ensures that potential defects and errors are identified and addressed early, reducing the need for costly rework or customer complaints.
Enter ChatGPT-4
ChatGPT-4, an advanced language model powered by artificial intelligence, can assist in managing and monitoring quality control processes. With its natural language processing capabilities, ChatGPT-4 can understand and respond to queries from quality control personnel, offering real-time guidance and solutions.
Here's how ChatGPT-4 can be effectively used in quality control:
- Process Standardization: ChatGPT-4 can help standardize quality control processes by providing step-by-step instructions and guidelines to ensure consistency in inspections and evaluations. It can also assist in developing and refining standard operating procedures (SOPs) for various quality control activities.
- Real-time Troubleshooting: In situations where quality issues arise, ChatGPT-4 can be used as a troubleshooting tool. Quality control personnel can describe the problem to ChatGPT-4, which can then analyze the information and provide possible causes and solutions. This saves time in identifying and resolving quality-related issues.
- Training and Education: ChatGPT-4 can act as a virtual training assistant, providing on-demand training materials, quizzes, and interactive learning experiences. It can explain complex quality concepts, review relevant regulations, and offer practical examples to improve the knowledge and skills of quality control personnel.
- Continuous Improvement: Lean thinking emphasizes the importance of continuous improvement, and ChatGPT-4 can play a crucial role in this endeavor. It can analyze historical quality control data, identify trends and patterns, and suggest opportunities for improvement. By leveraging the insights provided by ChatGPT-4, organizations can constantly refine their quality control processes.
- Communication and Collaboration: ChatGPT-4 can facilitate effective communication and collaboration among quality control teams. It can serve as a knowledge-sharing platform, allowing personnel to ask questions, share best practices, and learn from each other's experiences. This promotes a culture of continuous learning and helps maintain consistent quality standards across the organization.
Conclusion
Lean thinking, combined with the capabilities of advanced technologies like ChatGPT-4, offers immense potential for improving quality control processes. By leveraging the power of AI, organizations can streamline workflows, enhance problem-solving, and foster a culture of continuous improvement.
As technology continues to advance, we can expect even greater integration of lean thinking principles with intelligent systems like ChatGPT-4. This synergy promises to revolutionize quality control practices and deliver higher levels of customer satisfaction in various industries.
Comments:
Thank you all for taking the time to read my article on improving quality control with ChatGPT. I'm excited to hear your thoughts and answer any questions you may have.
Great article, Jody! I found your perspective on applying lean thinking to quality control quite intriguing. Can you elaborate more on how ChatGPT can help streamline the process?
Thanks for your comment, Ken. ChatGPT can be used to automate quality control checks by analyzing data, identifying patterns, and signaling potential issues. By incorporating ChatGPT into the quality control workflow, companies can save time and improve their overall efficiency.
I agree with Ken, Jody. The application of ChatGPT in quality control seems promising. However, I wonder if there are any limitations or challenges we should be aware of when implementing it in real-life scenarios?
That's a valid concern, Sarah. Implementing ChatGPT in quality control does come with some challenges. One of the main limitations is that it requires a significant amount of training data to achieve accurate results. Additionally, it's important to carefully define the desired outputs and continuously monitor and update the system to adapt to evolving quality control needs.
Excellent article, Jody! I'm particularly interested in the potential impact of ChatGPT on reducing human errors in quality control processes. How effective has it been in practice?
Thank you, Chris! ChatGPT has shown promise in reducing human errors. By automating certain quality control checks, it minimizes the risk of oversight and enables faster identification of potential issues. However, it's essential to remember that ChatGPT is a tool to support quality control, not a replacement for human judgment. A combination of human expertise and AI capabilities can yield the best results.
Great article, Jody. I can see the benefits of ChatGPT in quality control, but what about industries or processes that require more complex analysis or decision-making? Can ChatGPT handle such scenarios effectively?
Thanks for raising that point, James. While ChatGPT can be valuable in automating certain quality control tasks, it may not be suitable for more complex analysis or decision-making that requires a deeper understanding of specific domains or intricate processes. In those cases, a combination of AI tools, domain expertise, and human judgment would be most effective.
Jody, I appreciate your article, and I believe ChatGPT can indeed enhance quality control efforts. However, I'm concerned about potential biases in AI systems. How can we ensure that ChatGPT doesn't introduce or perpetuate biases in quality control processes?
That's an important consideration, Emily. Bias in AI systems is a real concern. To mitigate this risk, it's crucial to train ChatGPT on diverse and representative datasets, involving stakeholders with diverse perspectives, and actively monitoring and auditing the system for potential biases. Transparency and accountability are key to ensuring the responsible and fair use of AI in quality control.
Interesting article, Jody! I'm curious about the potential cost implications of incorporating ChatGPT into existing quality control processes. How does it compare financially to traditional methods?
Thanks for your question, Alex. Incorporating ChatGPT into quality control processes may have upfront costs related to training the model and integrating it into existing systems. However, in the long run, it can lead to cost savings by reducing manual labor, minimizing errors, and improving overall process efficiency. It's important to conduct a thorough cost-benefit analysis to understand the specific financial implications for each organization.
Great article, Jody! I have a question regarding the scalability of ChatGPT. Can it handle large-scale quality control operations?
Thank you, Lily! ChatGPT is designed to handle large-scale operations. With the right infrastructure and resources in place, it can be scaled up to analyze and process vast amounts of data, making it suitable for a variety of quality control scenarios. However, it's important to ensure that the system is adequately trained and continuously improved to maintain its effectiveness.
Interesting read, Jody! In your opinion, what are the main advantages of using ChatGPT over traditional quality control methods?
Thanks, Michael! One of the main advantages of using ChatGPT in quality control is its ability to automate repetitive and time-consuming tasks, saving valuable human resources. Additionally, ChatGPT can help identify patterns and potential issues that may be overlooked by manual inspections, leading to more accurate and efficient quality control processes.
Jody, thank you for sharing your insights on using ChatGPT for quality control. I'm curious if ChatGPT can adapt to evolving quality standards and changing requirements over time.
You're welcome, Ethan! ChatGPT can adapt to evolving quality standards by regularly updating and retraining the model based on new data and feedback. By fine-tuning the system, it can align with changing requirements and maintain its effectiveness in improving quality control.
Jody, thanks for the informative article! I wonder if there are any privacy concerns when using ChatGPT for quality control, especially if it involves sensitive data.
That's an important point, Sophia. When using ChatGPT for quality control, organizations must ensure appropriate data security and privacy measures. It's essential to handle sensitive data responsibly, comply with regulations, and implement safeguards to protect confidential information. Privacy considerations should be an integral part of the implementation and usage of AI systems in quality control.
Interesting perspective, Jody! I'm curious if there are any specific industries or sectors where you see ChatGPT being particularly beneficial for quality control.
Thanks, Mark! ChatGPT can be beneficial for quality control in industries such as manufacturing, software development, customer support, and content moderation, where repetitive tasks and pattern recognition are essential. However, its potential applications extend beyond these sectors, and it can be adapted to various quality control scenarios depending on the organization's needs.
Great article, Jody! I'm curious if ChatGPT can assist in root cause analysis, or is it primarily focused on identifying potential issues?
Thank you, Olivia! ChatGPT can assist in root cause analysis by identifying patterns and anomalies that may contribute to quality issues. While it may not fully replace the human-driven root cause analysis process, it can provide valuable insights and help prioritize areas for further investigation.
Jody, your article was thought-provoking! How long does it typically take to integrate ChatGPT into existing quality control workflows?
I appreciate your kind words, Laura. The time required to integrate ChatGPT into existing quality control workflows can vary depending on factors such as the complexity of the processes, data availability, and the organization's existing infrastructure. It typically involves data preparation, model training, testing, and deployment, which may take several weeks to a few months, considering the necessary iterations and refinements.
Great read, Jody! You mentioned AI tools, including ChatGPT, as part of the quality control process. Are there any other AI technologies that can complement ChatGPT in this context?
Thanks, David! Absolutely, ChatGPT can be complemented with other AI technologies to enhance quality control. For instance, computer vision systems can be used alongside ChatGPT to detect visual defects, while machine learning algorithms can help predict potential quality issues based on historical data. The choice of complementary AI technologies depends on the specific requirements and nature of the quality control tasks.
Jody, thanks for sharing your insights. I'm curious if there are any ongoing research efforts to improve the capabilities of ChatGPT in quality control.
You're welcome, Emma! Ongoing research efforts are focused on improving ChatGPT's ability to understand and analyze context-specific quality control requirements, addressing biases and fairness concerns, and enhancing interpretability and transparency of the automated quality control process. Continuous innovation and refinement are essential to unlocking the full potential of AI in quality control.
Interesting article, Jody! How can organizations ensure that employees are comfortable working alongside ChatGPT in their quality control roles?
Thank you, William! Employee comfort and confidence are crucial for successful integration of ChatGPT into quality control roles. Organizations can ensure this by providing proper training and education to employees on the capabilities and limitations of ChatGPT, involving them in the implementation process, and emphasizing the collaborative nature of humans and AI working together to achieve better quality control outcomes.
Jody, I found your article quite informative and inspiring. What steps can organizations take to evaluate the effectiveness of ChatGPT in their quality control processes?
Thank you, Sophie! Evaluating the effectiveness of ChatGPT in quality control processes requires defining relevant metrics and KPIs to measure its impact accurately. Organizations can conduct pilots or A/B tests, comparing the outcomes of quality control tasks performed with and without ChatGPT's assistance. Analyzing the results, gathering feedback from employees, and continuous monitoring are essential to evaluate and iterate upon the effectiveness of ChatGPT implementation.
Great insights, Jody! Are there any ethical considerations organizations should keep in mind when using ChatGPT for quality control?
Thanks, Robert! Ethical considerations are crucial when using AI systems like ChatGPT in quality control. It's important to ensure fairness, accountability, and transparency in decision-making processes. Organizations should actively address potential biases, consider the impact on employees and affected stakeholders, and establish governance mechanisms to guide the responsible use of AI in quality control.
Jody, great article! I'm curious if ChatGPT can assist in real-time quality control scenarios where immediate actions are required.
Thank you, Daniel! ChatGPT can be utilized in real-time quality control scenarios to provide near-instant analysis and flag potential issues as they occur. Its ability to process data and generate insights rapidly makes it well-suited for time-sensitive quality control tasks, helping organizations take immediate actions when necessary.
Jody, I appreciate your perspective on leveraging AI for quality control. Is there any specific expertise required to implement and maintain ChatGPT effectively?
Thanks, Ava. Implementing and maintaining ChatGPT effectively does require some expertise. Organizations would benefit from having professionals with knowledge in machine learning, natural language processing, and data engineering. It's important to collaborate with domain experts who understand the quality control processes and data intricacies to ensure ChatGPT's successful integration and ongoing refinement.
Jody, your article shed light on an innovative approach to quality control. Can ChatGPT handle multiple languages or is it limited to English?
Thank you, Grace! ChatGPT has been primarily trained on English text, but it can handle multiple languages to some extent. However, its performance may vary depending on the language and the availability of training data. Continuous improvements are being made to enhance ChatGPT's multilingual capabilities, but for optimal results, organizations should consider language-specific models or adaptations if their quality control processes involve non-English content.
Insightful article, Jody! Considering the rapid advancements in AI, how do you envision the future of quality control with ChatGPT or similar technologies?
Thanks, Sophia! In the future, quality control with technologies like ChatGPT is likely to become more sophisticated and intuitive.AI systems will continue to improve in their ability to understand and adapt to specific quality control requirements. We can expect more seamless integration of AI tools into existing workflows, enabling real-time decision-making and proactive quality control measures. The potential for enhanced productivity, accuracy, and innovation in quality control is significant.
Jody, I appreciate the insights you shared. How can organizations ensure the ethical use of AI in quality control and prevent unintended consequences?
You're welcome, Elijah. Organizations need to establish clear ethical guidelines and governance frameworks for the use of AI in quality control. This includes promoting transparency, ensuring accountability, conducting ongoing monitoring for biases and unintended consequences, actively involving stakeholders, and fostering a culture of responsible AI use. By proactively addressing ethical considerations, organizations can mitigate risks and maximize the positive impact of AI in quality control.
Great article, Jody! Do you foresee any specific challenges in implementing ChatGPT in highly regulated industries like healthcare or finance?
Thank you, Joshua! Implementing ChatGPT in highly regulated industries may pose additional challenges. Compliance with strict regulations regarding privacy, security, and data handling becomes vital. Additionally, organizations must navigate potential legal and ethical considerations specific to these industries. Collaborating with experts well-versed in the regulatory landscape and adopting a robust governance framework is crucial for successful implementation of ChatGPT in healthcare, finance, or any other highly regulated sector.
That wraps up our discussion on improving quality control with ChatGPT. Thank you all for your engagement and valuable input! If you have any further questions or would like to continue the conversation, feel free to reach out. Have a great day!