Optimizing Inventory Management with ChatGPT: Empowering KPI Reports Technology
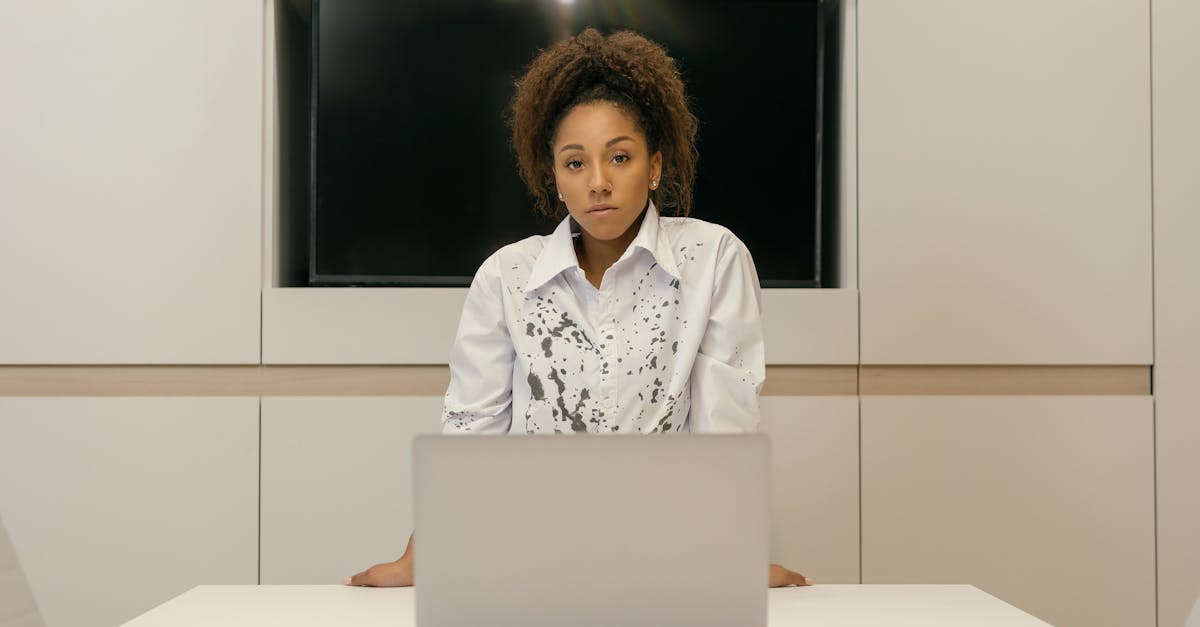
The use of Key Performance Indicators (KPIs) in inventory management has become increasingly important for businesses. KPIs provide valuable insights into the performance and efficiency of an organization's inventory control processes. One technology that enables businesses to leverage KPIs effectively is KPI reports.
What are KPI Reports?
KPI reports are tools that help businesses track and analyze Key Performance Indicators related to their inventory management. These reports are created using specialized software or systems that collect relevant data from various sources within the organization.
Why are KPI Reports important in Inventory Management?
Efficient inventory management is crucial for businesses to minimize costs, improve customer satisfaction, and optimize overall operations. KPI reports provide a visual representation of key metrics, allowing businesses to monitor their inventory performance in real-time.
Understanding the role of KPIs in Inventory Management
Key Performance Indicators in inventory management can vary depending on the nature of the business. However, common KPIs include:
- Inventory Turnover: Measures how quickly a company sells and replaces its inventory.
- Stockout Rate: Tracks the frequency of running out of stock for particular items.
- Order Fill Rate: Measures the percentage of complete orders shipped on time.
- Lead Time: Measures the time it takes from placing an order to receiving the items.
- Carrying Costs: Calculates the expenses associated with holding inventory, such as storage and insurance.
- Order Cycle Time: Measures the time between placing an order and receiving it.
How KPI Reports help in efficient stock control
KPI reports help businesses make informed decisions about their stock control processes by providing valuable insights. Here are some specific benefits:
- Identifying inefficiencies: KPI reports highlight areas where inventory management processes are inefficient, enabling businesses to take corrective actions. For example, if the stockout rate is consistently high, it may indicate a need for better demand forecasting or inventory replenishment methods.
- Optimizing inventory levels: By analyzing KPIs such as inventory turnover and carrying costs, businesses can identify the optimal inventory levels needed to meet customer demand while minimizing costs. Maintaining excessive stock levels ties up capital and increases storage costs, while insufficient stock leads to stockouts and potential loss of sales.
- Forecasting demand: KPI reports allow businesses to track historical sales data, identify trends, and forecast future demand more accurately. This helps in avoiding stockouts, optimizing production planning, and ensuring sufficient inventory levels during peak periods.
- Supplier management: KPIs related to lead time and order cycle time enable businesses to evaluate the performance of their suppliers. By analyzing these metrics, organizations can make informed decisions when it comes to selecting or renegotiating contracts with suppliers.
Conclusion
KPI reports are essential tools for businesses engaged in inventory management. By providing insights into key performance indicators, these reports enable organizations to optimize their stock control processes, minimize costs, and meet customer demands effectively. Investing in technology that supports the generation and analysis of KPI reports is crucial for businesses looking to stay competitive in today's dynamic marketplace.
Comments:
Great article, Geri Vargas! I've been using ChatGPT for a while now, and it has definitely improved our inventory management. It helps us generate accurate KPI reports and gives us valuable insights into optimizing our inventory levels.
Thank you, Sheila! I'm glad to hear that ChatGPT has been helpful for your inventory management. If you have any specific examples or challenges you've overcome using ChatGPT, feel free to share!
I'm interested to know more about how ChatGPT integrates with existing inventory management systems. Are there any compatibility requirements or specific platforms it works best with?
Hi Marcus, I've used ChatGPT with various inventory management systems, and it seems to be agnostic to specific platforms. As long as you can feed it the relevant data, it can provide useful insights and help with KPI reporting.
Thanks, Julia! That's good to know. I'll definitely look into integrating ChatGPT with our current system.
This article raises an interesting point! How does ChatGPT handle demand forecasting? Can it predict future inventory needs effectively?
Hi Ethan! While ChatGPT is primarily used for optimizing inventory management and generating KPI reports, it can also assist with demand forecasting. By analyzing historical data and market trends, it can provide insights into potential future inventory needs.
That's impressive, Geri! Having a tool that can handle multiple aspects of inventory management is undoubtedly valuable.
I have reservations about using an AI-powered tool for inventory management. How can we ensure the accuracy and reliability of the data and recommendations provided by ChatGPT?
Hi David! Valid concern. ChatGPT's accuracy and reliability heavily depend on the quality and relevance of the data provided to it. It's essential to ensure data integrity and verify its correctness before relying on the insights provided by the system.
Thank you for the clarification, Geri. I agree that data quality plays a crucial role. Proper data management practices and validation processes will be necessary to ensure reliable results.
I'm wondering about the technical implementation of ChatGPT. Is it a cloud-based service or can it be deployed on-premises?
Hi Angela! ChatGPT is primarily offered as a cloud-based service, but it also provides options for on-premises deployment. The deployment method depends on your organization's specific requirements and preferences.
Thank you, Geri! Flexibility in deployment options is always beneficial. It allows organizations to choose what suits them best.
Have you faced any challenges or limitations when using ChatGPT for inventory management? I'd like to know both the advantages and the potential drawbacks of implementing it.
Hi Samuel! While ChatGPT can be highly useful, it's essential to mention that it heavily relies on the data provided and might not handle complex scenarios with extreme variability as well. It's best suited for assisting with optimization and generating reports rather than complete decision-making.
Thank you for the insights, Geri. Considering its strengths and limitations will be crucial in evaluating its implementation potential.
I've been hearing a lot about AI-powered inventory management systems lately. How does ChatGPT compare to other available solutions in the market?
Hi Rachel! ChatGPT is one of the leading AI-powered systems in the market when it comes to inventory management. Its natural language processing capabilities and ability to generate valuable insights make it a popular choice among businesses.
Thanks for the information, Geri! It's good to know that ChatGPT is well-regarded in the industry. I'll definitely consider it for our inventory management needs.
Does ChatGPT support real-time reporting of KPIs? Having up-to-date information on inventory performance is crucial for effective decision-making.
Hi Liam! ChatGPT can provide real-time reporting of KPIs as long as the data feeding into the system is up-to-date. It analyzes the data and generates insights based on the current information available.
That's great to hear, Geri! Real-time reporting will definitely add value to our inventory management processes.
Could you please elaborate on the potential cost savings by implementing ChatGPT for inventory management? Is it a significant factor to consider?
Hi Sophia! Implementing ChatGPT for inventory management can lead to cost savings by providing more accurate insights, optimizing inventory levels, and reducing excess or obsolete inventory. It's essential to assess the potential savings against the cost of implementing and maintaining the system.
Thank you for the explanation, Geri. Factoring in both the potential benefits and implementation costs is crucial for making an informed decision.
Geri, what kind of training or expertise does a team need to effectively use ChatGPT for inventory management? Are there any specific skills or knowledge areas that are particularly valuable?
Hi Oliver! While no specific training or expertise is required to start using ChatGPT, having a basic understanding of inventory management principles and familiarity with KPI reporting can certainly enhance the effectiveness of implementing the system.
Thanks, Geri! It's good to know that existing knowledge in the field can supplement the usage of ChatGPT for better outcomes.
Can ChatGPT handle multiple warehouses or locations? We have a distributed inventory setup, and it would be valuable to have insights across all our facilities.
Hi Natalie! Yes, ChatGPT can handle multiple warehouses or locations. By aggregating and analyzing inventory data from different facilities, it can provide comprehensive insights across your distributed inventory setup.
That's great to hear, Geri! Having a centralized view of our distributed inventory will greatly help us make informed decisions. Thanks!
I'm curious about the scalability of ChatGPT. Can it handle large datasets and still provide quick responses?
Hi Simon! ChatGPT can handle large datasets and provide reasonably quick responses. However, the response time may vary depending on factors like dataset size, system resources, and complexity of queries. It's essential to assess the specific requirements of your inventory management system and evaluate ChatGPT's performance accordingly.
Thank you for the clarification, Geri. We'll keep the possible response time variation in mind when considering the implementation of ChatGPT.
Are there any privacy concerns related to using ChatGPT for inventory management? We deal with sensitive information, and it's crucial to ensure data security.
Hi Isabella! Privacy and data security are indeed important considerations. OpenAI, the organization behind ChatGPT, has implemented measures to protect user data. It's advisable to review their privacy policy and ensure compliance with your organization's data security requirements.
Thank you for addressing the privacy concern, Geri. It's reassuring to know that steps have been taken to protect sensitive information.
Can ChatGPT generate custom reports tailored to specific business needs? We have unique KPIs and reporting requirements in our industry.
Hi Daniel! Yes, ChatGPT can generate custom reports tailored to specific business needs. By defining the relevant KPIs and reporting requirements, it can provide insightful reports based on your industry and organizational context.
That's great to hear, Geri! Customized reports will help us address the unique demands of our industry effectively. Thank you!
You're welcome, Daniel! If you have any further questions or need assistance with implementing ChatGPT for your business, feel free to reach out. I'm here to help!
What are the key performance indicators (KPIs) that ChatGPT focuses on for optimizing inventory management? Are there any common ones that it highlights?
Hi Madison! ChatGPT can help optimize various inventory-related KPIs, including but not limited to stock turnover ratio, carrying cost of inventory, lead time, service level, and demand forecasting accuracy. It can analyze these indicators to provide insights for better inventory management.
Thank you for your response, Geri. It's helpful to know the specific KPIs that ChatGPT focuses on. It will guide us in aligning its usage with our inventory management goals.
Is ChatGPT compatible with different data formats? We have data in various file formats, and it would be convenient if we can use them without much conversion.
Hi Gavin! ChatGPT is designed to be compatible with multiple data formats. It supports popular file formats like CSV, Excel, and JSON, making it easier to utilize different types of data without significant conversion efforts.
That's great! Having flexible compatibility with multiple data formats will definitely simplify the integration process. Thank you, Geri!
You're welcome, Gavin! If you have any more questions or need further guidance as you explore ChatGPT for your inventory management needs, feel free to ask. I'm here to assist you!
Thank you all for your valuable comments and questions! I appreciate your engagement. If you have any more thoughts or need further information, feel free to continue the discussion. I'll be happy to help!