Optimizing Inventory Management with ChatGPT: Harnessing the Power of Probability Technology
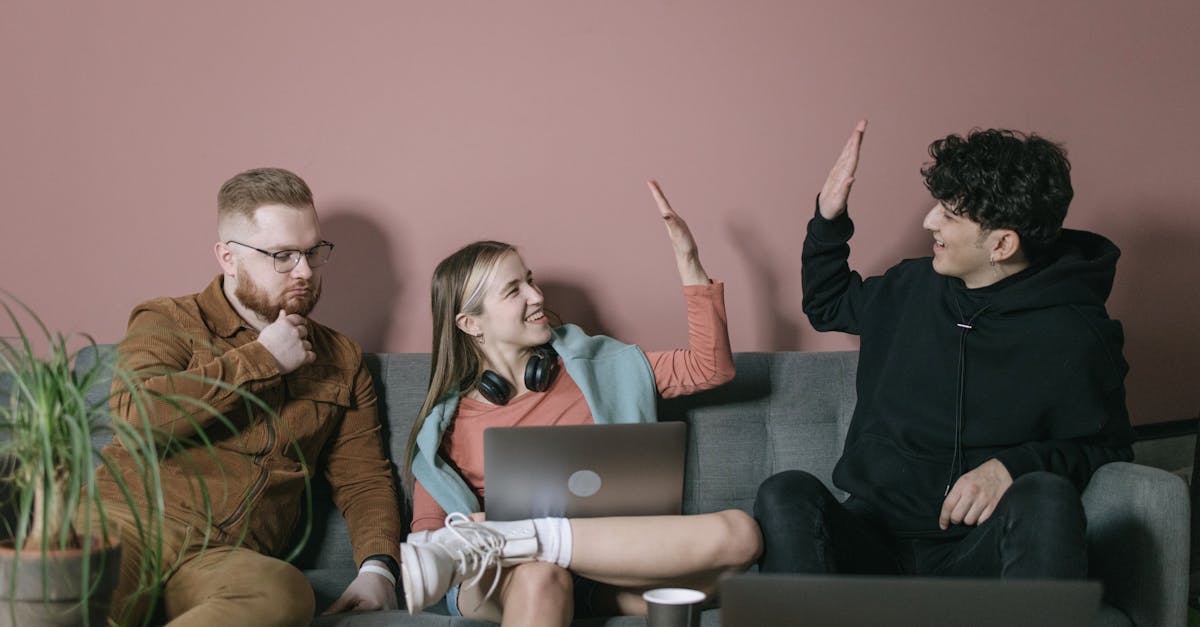
Inventory management is a critical process for any business that deals with physical products. Striking the right balance between having enough stock to meet customer demand and minimizing inventory costs is no easy task. However, with the help of probability, businesses can make informed decisions and optimize their stock levels effectively.
Understanding Probability
Probability is a mathematical concept that quantifies the likelihood of an event occurring. In the context of inventory management, probability can be used to predict future demand for a product. By analyzing historical sales data and other relevant factors, businesses can calculate the probability of different demand scenarios and adjust their stock levels accordingly.
Optimizing Stock Levels
Maintaining excessive stock levels can tie up valuable resources and increase holding costs. On the other hand, having inadequate inventory can lead to lost sales opportunities and dissatisfied customers. Using probability, businesses can determine the optimal stock levels that strike a balance between these two extremes.
Probability can help businesses answer important questions such as:
- What is the probability of encountering high-demand periods?
- What is the probability of encountering low-demand periods?
- How much safety stock should be maintained to cover uncertain demand?
By considering these probabilities, businesses can adjust their stock levels accordingly. For example, during high-demand periods, they may increase their inventory to meet the anticipated demand. Conversely, during low-demand periods, they can reduce stock levels to minimize holding costs.
Reducing Inventory Costs
One of the key benefits of using probability in inventory management is the ability to reduce inventory costs. By accurately predicting future demand and adjusting stock levels accordingly, businesses can minimize excess inventory and holding costs. This leads to improved cash flow and overall operational efficiency.
Additionally, probability analysis can help businesses identify trends and patterns in customer demand. This information can be utilized to optimize purchasing and production schedules, resulting in cost savings and reduced lead times.
Implementing Probability in Inventory Management
To leverage probability in inventory management, businesses need to collect and analyze relevant data. Historical sales data is crucial in understanding demand patterns and calculating probabilities. Statistical techniques, such as time series analysis and forecasting, can be used to make accurate predictions based on this data.
Inventory management software with built-in probability modeling capabilities can automate the analysis process and provide real-time insights. These tools use algorithms to calculate probabilities, recommend optimal stock levels, and generate demand forecasts. By integrating such software into their operations, businesses can streamline their inventory management processes and make data-driven decisions.
Conclusion
Probability is a powerful tool that can help businesses optimize their stock levels and reduce inventory costs. By accurately predicting future demand and adjusting inventory accordingly, businesses can strike the right balance between customer satisfaction and operational efficiency. Utilizing probability analysis and leveraging technology, businesses can embrace data-driven inventory management and gain a competitive advantage in today’s dynamic market.
Comments:
Great article, Joseph! I completely agree that optimizing inventory management is crucial for businesses.
Thank you, Michael! I'm glad you agree on the importance of optimizing inventory management.
Joseph, what are the potential risks or limitations of relying on ChatGPT for inventory management?
Emily, some potential risks of relying on ChatGPT for inventory management include biases in training data and overconfidence in predictions.
I enjoyed reading this article, Joseph. The concept of using ChatGPT for inventory management is interesting.
Thanks, Sarah! Yes, the application of ChatGPT in inventory management offers exciting possibilities.
Joseph, you've made a compelling case for using probability technology in inventory management. Can't wait to see more businesses adopt this.
Jason, I hope more businesses will recognize the benefits and adopt probability technology for inventory optimization.
This is a well-written article, Joseph. I appreciate how you explained the benefits of using ChatGPT for inventory optimization.
I'm glad you found it well-written, Rebecca. The potential of ChatGPT for inventory optimization is indeed remarkable.
Joseph, thank you for shedding light on the potential of probability technology in improving inventory management. Really informative article.
You're welcome, Andrew! It's really exciting to see the impact probability technology can have on inventory management.
I've been looking into inventory management systems, and this article has certainly piqued my interest in considering ChatGPT.
Jessica, if you have any more questions about ChatGPT or its integration, feel free to ask.
Interesting article, Joseph! Do you think ChatGPT can be effectively integrated with existing inventory management software?
Mark, ChatGPT can be integrated with existing inventory management software for enhanced decision-making and optimization.
I wonder if ChatGPT can truly analyze and predict demand patterns accurately, considering the intricacies of inventory management.
Michelle, ChatGPT's ability to analyze demand patterns relies on the quality and diversity of training data and continuous fine-tuning.
Joseph, how can ChatGPT handle the dynamic nature of inventory, particularly in fast-paced industries?
Daniel, ChatGPT can handle the dynamic nature of inventory by learning from historical data, real-time inputs, and adapting its models.
The potential of using ChatGPT for optimizing inventory management is exciting, but what are the implementation challenges?
Olivia, some implementation challenges include data integration, model customization, and ensuring user trust in automated inventory decisions.
Joseph, what would be the key factors to consider when implementing ChatGPT for inventory optimization?
Sophia, when implementing ChatGPT for inventory optimization, key factors to consider include data quality, scalability, and integration with existing processes.
This article has inspired me to explore the potential of ChatGPT in optimizing inventory management. Well done, Joseph!
Thank you, Lauren! I'm glad the article has sparked your interest in ChatGPT's potential for optimizing inventory management.
Joseph, do you have any recommendations for businesses that are considering implementing ChatGPT for inventory management?
Michael, businesses considering ChatGPT for inventory management should start with a pilot project and gradually scale up while monitoring performance and user feedback.
I'm curious how ChatGPT would handle different inventory models, such as just-in-time or economic order quantity?
Sarah, ChatGPT's flexibility allows it to adapt to different inventory models by considering historical data, business rules, and specific constraints.
What would be the potential cost implications of adopting ChatGPT for inventory optimization?
Jake, the cost implications of adopting ChatGPT for inventory optimization would vary depending on factors like data size, computational resources, and customizations.
Joseph, can ChatGPT handle demand forecasting for seasonal products with fluctuating demand patterns?
Sophie, ChatGPT can handle demand forecasting for seasonal products by learning from historical patterns and adapting to changing demand dynamics.
I'm intrigued by the concept of using probability technology for inventory optimization. Great article, Joseph!
Thank you, Julia! Probability technology indeed holds great promise for driving advancements in inventory optimization.
Do you have any success stories or case studies where ChatGPT has been used effectively in improving inventory management?
Nathan, there are success stories where ChatGPT has been used to improve inventory management, but I suggest looking into relevant industry case studies for more details.
Joseph, have there been any ethical considerations in using ChatGPT for automated inventory decisions?
Amy, ethical considerations arise when using ChatGPT for automated inventory decisions, such as potential biases and the need for human oversight to ensure fairness and accountability.
How can businesses ensure a smooth transition when implementing ChatGPT for inventory optimization?
Erica, a smooth transition when implementing ChatGPT for inventory optimization is ensured through proper planning, gradual adoption, change management, and ongoing training.
Joseph, what are the potential risks of relying solely on automated inventory decisions without human intervention?
Lisa, potential risks of relying solely on automated inventory decisions include system errors, biases, unforeseen data patterns, and disregarding contextual nuances.
Joseph, what are the key performance indicators or metrics to evaluate the effectiveness of ChatGPT in inventory optimization?
Oliver, key performance indicators (KPIs) for evaluating the effectiveness of ChatGPT in inventory optimization might include inventory turnover, stockouts, fill rate, and forecast accuracy.
Joseph, how can businesses address potential concerns or skepticism among employees when adopting ChatGPT for inventory management?
Gemma, addressing concerns or skepticism among employees when adopting ChatGPT for inventory management can be done through communication, training, involving them in the process, and emphasizing the benefits.
What role can human intuition and judgment play alongside ChatGPT in inventory optimization?
Lucas, human intuition and judgment play a valuable role alongside ChatGPT in inventory optimization by providing subjective insights, considering external factors, and ensuring ethical decision-making.