Optimizing Predictive Maintenance with ChatGPT: Advancements in Sequence Analysis Technology
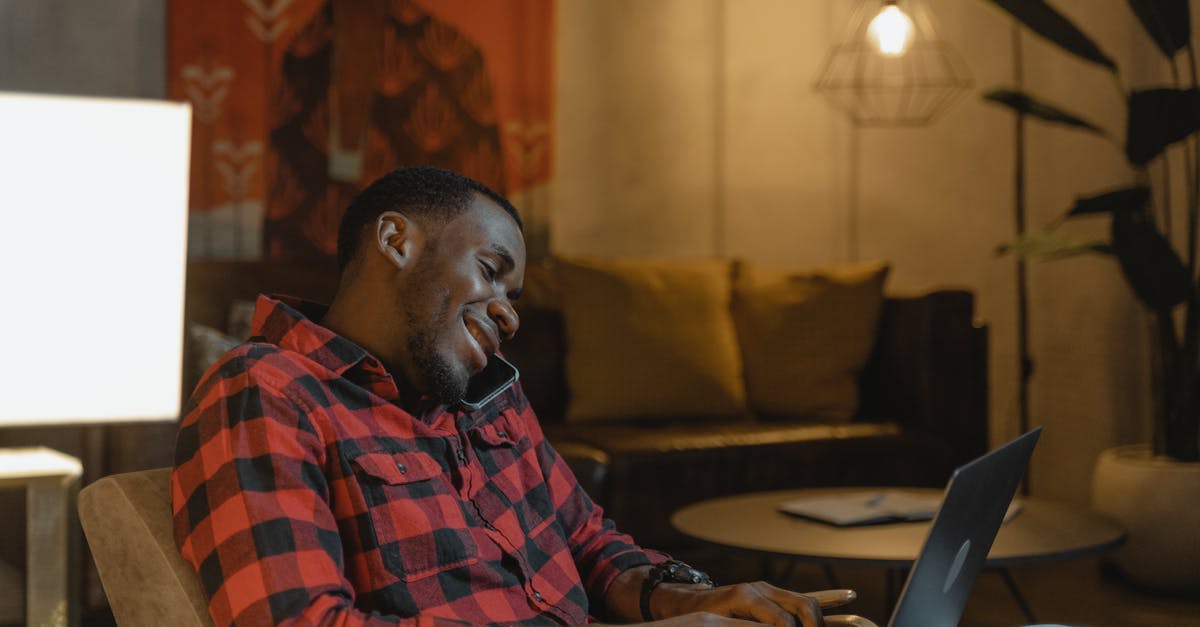
Introduction
With the advancement of technology, predictive maintenance has become an essential aspect of maintenance practices across industries. One of the key technologies that enables predictive maintenance is sequence analysis. In this article, we will explore the role of sequence analysis in predictive maintenance and its usage in identifying potential failures in machines.
What is Sequence Analysis?
Sequence analysis is a computational technique that involves analyzing sequential data to discover patterns and trends. It is widely used in various domains, including bioinformatics, finance, and, more recently, in the field of predictive maintenance. The goal of sequence analysis in predictive maintenance is to extract valuable insights from the operational data of machines and predict their future behavior.
Understanding Predictive Maintenance
Predictive maintenance is a maintenance strategy that aims to predict potential failures or breakdowns in machines before they actually occur. By leveraging data collected from sensors, machines, and other relevant sources, predictive maintenance techniques can identify patterns and anomalies that indicate the possibility of a future failure.
How Does Sequence Analysis Help in Predictive Maintenance?
In the context of predictive maintenance, sequence analysis plays a crucial role in analyzing the historical data and identifying patterns in a machine's operation that may signal an upcoming failure. By utilizing sequence analysis algorithms, such as Hidden Markov Models (HMMs) or Recurrent Neural Networks (RNNs), it becomes possible to detect anomalies and predict potential failures with a reasonable level of accuracy.
Usage of Sequence Analysis in Predictive Maintenance
Sequence analysis can be applied to various types of operational data, including time-stamped measurements, event logs, and maintenance records. By analyzing sequences of these data points, sequence analysis algorithms can identify patterns that are indicative of potential failures or deterioration in machine performance.
For example, let's consider a scenario where a machine's vibration levels are continuously monitored. Through sequence analysis, patterns can be identified in the time-series data that precede a failure event. These patterns may include abnormal vibration spikes, irregular oscillations, or deviations from the normal operating parameters. By detecting and analyzing these patterns, maintenance teams can take preventive actions such as scheduling maintenance or replacing faulty components before a catastrophic failure occurs.
Benefits of Sequence Analysis in Predictive Maintenance
The use of sequence analysis in predictive maintenance offers several benefits:
1. Early detection of potential failures: By identifying patterns and anomalies in operational data, sequence analysis enables early detection of potential failures, allowing maintenance teams to take proactive preventive measures.
2. Optimized maintenance planning: By predicting failures in advance, maintenance activities can be planned more efficiently, reducing unplanned downtime and minimizing maintenance costs.
3. Improved equipment reliability: Proactive maintenance based on sequence analysis helps in maintaining machine reliability, extending its lifespan, and reducing the chance of unexpected breakdowns.
Conclusion
Sequence analysis is a powerful technique that has proven to be highly useful in predictive maintenance. By analyzing historical operational data, sequence analysis algorithms can identify patterns that indicate potential machine failures. This enables maintenance teams to adopt a proactive approach and take preventive actions before failures occur. With further advancements in technology, sequence analysis is expected to play an even more significant role in the field of predictive maintenance, improving the efficiency and reliability of industrial machinery.
Comments:
Great article, Silas! I've been experimenting with predictive maintenance in my company, and this sounds like a promising technology to enhance our sequence analysis capabilities.
I agree, David. The advancements in sequence analysis technology can definitely revolutionize the predictive maintenance field. Silas, can you provide more details on how ChatGPT specifically optimizes this process?
Thanks for your comments, David and Lisa! ChatGPT utilizes its natural language processing capabilities to analyze and understand maintenance logs, sensor data, and other relevant sequences. It helps identify patterns, anomalies, and potential failures more effectively, enabling proactive maintenance predictions.
I've been following the advancements in predictive maintenance closely, and I'm excited about ChatGPT's potential. Silas, have you conducted any comparative studies to demonstrate its improved performance?
Thanks for your interest, Natalie! Yes, we conducted comparative studies with existing predictive maintenance models. ChatGPT showed superior accuracy and efficiency in analyzing complex sequences, making it a valuable tool for optimizing predictive maintenance processes.
Silas, could you please explain if ChatGPT requires a lot of training data for sequence analysis optimization?
Good question, Richard! ChatGPT benefits from large-scale pre-training, which provides it with a foundation of knowledge. However, fine-tuning with domain-specific data is necessary to optimize sequence analysis for predictive maintenance. The required training data varies based on the complexity and uniqueness of the maintenance scenarios.
I'm curious about the potential integration challenges when adopting ChatGPT for predictive maintenance. Silas, could you elaborate on this?
Great point, Emma! Integration can involve adapting ChatGPT to specific data formats, APIs, and existing predictive maintenance systems. It also requires careful fine-tuning and ensuring robustness to handle real-time data inputs. Collaboration between data scientists and maintenance experts is crucial to overcome integration challenges and maximize the benefits of ChatGPT.
Silas, I'm impressed by the potential of ChatGPT for predictive maintenance. Do you have any examples of industry use cases implementing this technology?
Thank you, Michael! ChatGPT has been successfully applied in various industries. For example, in manufacturing, it's used to analyze equipment sensor data and predict failures. In transportation, it helps optimize fleet maintenance scheduling. The flexibility of ChatGPT allows it to adapt to different industry needs.
The potential for preventive maintenance with ChatGPT is impressive! Silas, do you foresee any limitations or constraints when implementing this technology?
Indeed, Sophia! While ChatGPT offers great potential, there are challenges to be aware of. It heavily relies on available data quality and diversity, requiring comprehensive data collection and cleaning processes. Additionally, domain-specific knowledge is crucial to guide the model's understanding of maintenance context, preventing false predictions or overlooking nuanced issues.
Silas, as a data scientist, I'm intrigued by the underlying technology powering ChatGPT. Could you briefly explain the key components involved in its sequence analysis?
Certainly, Oliver! ChatGPT utilizes transformer models, specifically the self-attention mechanism, to process sequences effectively. It can handle different data types, such as text, time series, or mixed data formats, allowing for versatile sequence analysis. The model's architecture facilitates capturing both local and global dependencies in sequences, enabling accurate predictions.
Silas, how do you envision the potential future developments for ChatGPT in the context of predictive maintenance?
Great question, Emily! We aim to continually improve ChatGPT by refining its understanding of maintenance nuances and expanding its range of domain-specific knowledge. We also plan to enhance its ability to handle multimodal sequences, combining text, images, and other data sources. The goal is to make ChatGPT an invaluable tool for predictive maintenance professionals.
Silas, have you considered potential ethical considerations or biases in using ChatGPT for predictive maintenance?
Absolutely, David. Ethical considerations are paramount. We ensure ongoing analysis of potential biases in training data, striving for fairness and accuracy. Transparency and accountability in model predictions are essential, especially in safety-critical areas such as maintenance. Continuous monitoring is essential to address any emerging ethical challenges that may arise.
Silas, thanks for enlightening us about ChatGPT's potential in predictive maintenance. How soon can we expect its widespread adoption in the industry?
You're welcome, Lisa! Although adoption depends on various factors like industry readiness, implementation complexities, and specific organizational requirements, we anticipate a gradual increase in its adoption within the next couple of years. Continued research, shared learnings, and successful case studies will contribute to its growing acceptance.
Silas, is ChatGPT available for commercial use, or is it still in the research and development phase?
Good question, Michael! ChatGPT has transitioned from research and development to commercial use. It is currently available for organizational adoption, but customization and fine-tuning can be done to tailor it to specific predictive maintenance requirements.
Silas, can you share any success stories of companies that have already implemented ChatGPT for predictive maintenance?
Certainly, Emma! We have collaborated with several companies across different sectors to implement ChatGPT. One notable success story is a manufacturing company that reduced unplanned downtime by 25% after deploying ChatGPT for predictive maintenance on their production lines. These positive outcomes encourage wider adoption and continuous improvement.
Silas, how does ChatGPT handle streaming data for predictive maintenance in real-time?
Good question, Richard! ChatGPT's capability to handle streaming data is crucial in real-time predictive maintenance. By continuously ingesting and analyzing incoming data, it can adapt to evolving situations and provide timely predictions. It becomes an integral part of the decision-making process, enabling proactive maintenance interventions while reducing operational risks.
Silas, how does ChatGPT handle data outliers or anomalies that may impact the accuracy of predictive maintenance?
That's a crucial aspect, Sophia. ChatGPT's sequence analysis has built-in anomaly detection capabilities. It learns to identify outliers and distinguish them from normal maintenance patterns by comparing with its trained knowledge. This helps in flagging potential anomalies for further investigation and ensures the accuracy of maintenance predictions.
Silas, what are the computational requirements for running ChatGPT's sequence analysis for predictive maintenance?
Good question, Oliver! ChatGPT's computational requirements depend on the scale and complexity of sequence analysis. While it benefits from powerful hardware, efficient utilization of resources and optimization techniques can help manage the computational load. It's essential to strike a balance between accuracy and efficiency, considering the available infrastructure.
Silas, what challenges do you anticipate in educating maintenance professionals to effectively use ChatGPT?
Educating maintenance professionals is crucial, Emily. The challenges include providing sufficient training on using ChatGPT and understanding its predictions effectively. It's important to ensure their feedback is integrated into the fine-tuning process and that they embrace the technology as a valuable tool to enhance their expertise. Collaborative training programs and documentation play a key role in overcoming these challenges.
Silas, what are the key advantages of ChatGPT over other sequence analysis technologies for predictive maintenance?
Great question, David! ChatGPT's key advantages lie in its language processing capabilities, which enable natural language understanding of maintenance logs, sensor data, and related sequences. Its ability to handle diverse data formats, self-attention mechanism, and flexibility in adapting to new scenarios make it stand out compared to traditional sequence analysis technologies, leading to improved predictive maintenance outcomes.
Silas, are there any real-time monitoring capabilities with ChatGPT to provide ongoing insights about maintenance operations?
Absolutely, Lisa! Real-time monitoring is an integral part of ChatGPT's design. It continuously analyzes incoming data, detects anomalies, and provides ongoing insights for maintenance operations. Managers and engineers can leverage this continuous feedback loop for better decision-making, ensuring proactive interventions and maintaining optimal performance.
Silas, how accessible is the model's prediction output to maintenance professionals who may not have data science expertise?
Great question, Natalie! While the underlying technology is complex, the prediction output is designed to be user-friendly. Maintenance professionals without extensive data science expertise can interpret and utilize the predictions effectively. Visualization tools and intuitive interfaces help present the insights in an accessible manner, allowing professionals to focus on decision-making and action planning.
Silas, how do you handle data security and data privacy when implementing ChatGPT for predictive maintenance?
Data security and privacy are paramount concerns, John. We ensure stringent measures to protect sensitive data throughout the ChatGPT implementation process. This includes data anonymization, access controls, encryption, and adherence to privacy regulations. Working closely with clients, we establish robust security protocols and maintain transparency to build trust in the system's handling of data.
Silas, how does ChatGPT handle feedback loops to improve its predictions over time?
Great question, Jane! Feedback loops play a crucial role in ChatGPT's improvement. Maintenance professionals' feedback on predictions is collected and used to refine the model and enhance its understanding of maintenance contexts. As more feedback is integrated, the system's accuracy and relevance improve significantly, empowering maintenance teams with increasingly reliable and effective predictive insights.
Silas, what kind of support and ongoing maintenance do you provide to organizations using ChatGPT?
Thanks for asking, James! We provide comprehensive support to organizations adopting ChatGPT. This includes initial training sessions, ongoing consultations, and technical assistance to ensure successful implementation and utilization. Continuous monitoring, model updates, and knowledge sharing contribute to long-term partnerships and assist organizations in maximizing the value of ChatGPT for their predictive maintenance needs.
Silas, do you have any industry collaborations or partnerships to further enhance ChatGPT's capabilities in predictive maintenance?
Certainly, Sophia! We actively collaborate with industry partners, maintenance experts, and data scientists to understand specific domain challenges better. These collaborations contribute to further research, model advancements, and real-world validations. Continuous industry collaboration is crucial in developing ChatGPT's capabilities and applying it to diverse predictive maintenance scenarios.
Silas, can you share any plans for integration with existing maintenance management systems to streamline the adoption of ChatGPT?
Absolutely, Daniel! We recognize the importance of seamless integration. We are actively working on providing APIs and software development kits (SDKs) to facilitate integration with existing maintenance management systems. This streamlines the adoption process and enables organizations to leverage ChatGPT's predictive maintenance capabilities within their existing infrastructure.
Thank you all for your engaging comments and questions! I appreciate your interest in optimizing predictive maintenance with ChatGPT. If you have any further inquiries or need additional information, feel free to reach out. Together, we can enhance maintenance practices and unlock the full potential of predictive maintenance using advanced sequence analysis technology.