Revolutionizing CNC Programming with Predictive Analytics: Harnessing the Power of ChatGPT
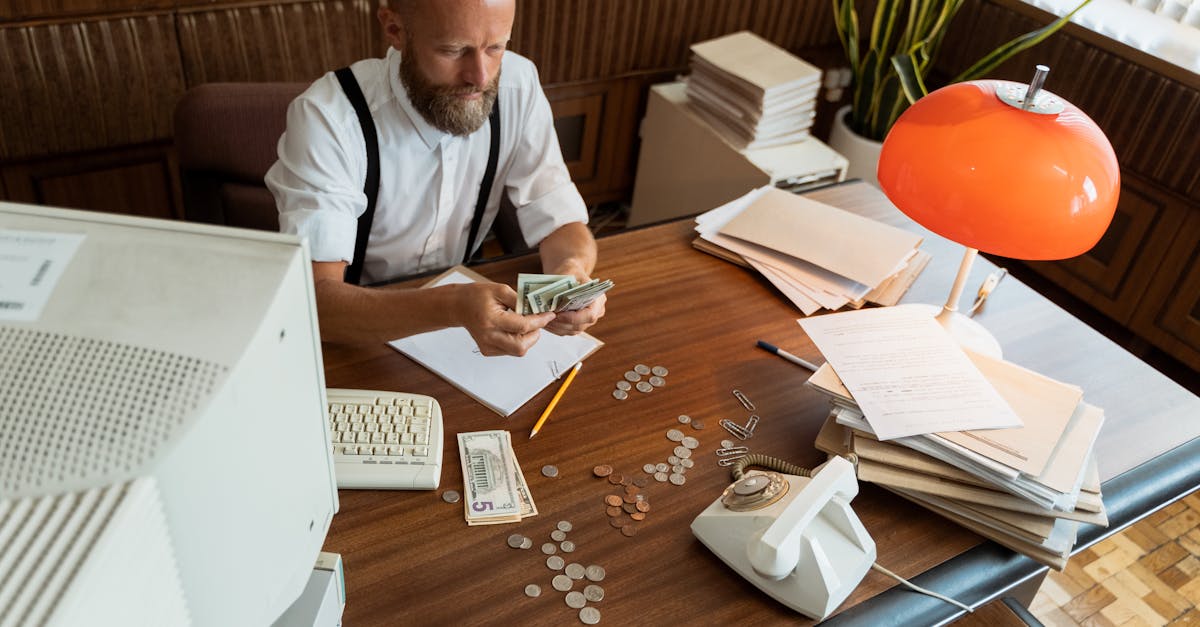
Introduction
CNC programming, short for Computer Numerical Control programming, is a technology that plays a crucial role in the manufacturing industry. It involves the use of computer software to control machine tools and automate the manufacturing process. By combining CNC programming with predictive analytics, it is possible to predict machine breakdowns and suggest preventive measures, improving productivity and reducing downtime significantly.
What is Predictive Analytics?
Predictive analytics is the use of historical data, statistical models, and machine learning techniques to make predictions about future events or outcomes. It involves analyzing past trends and patterns to identify potential issues or opportunities before they occur. In the context of CNC programming, predictive analytics can be applied to monitor the health of machines and foresee possible breakdowns, enabling proactive maintenance and minimizing costly repairs.
Utilizing CNC Programming for Predictive Analytics
CNC programming provides a wealth of data about machine operations, such as temperature, vibration, power consumption, and tool wear. By collecting and analyzing this data in real-time, it is possible to detect anomalies, deviations, or trends that may indicate impending machine failures. This data-driven approach allows manufacturers to take preventive actions before a breakdown occurs, thereby avoiding unexpected downtime and production losses.
Predictive Maintenance and Cost Savings
Implementing predictive analytics in CNC programming enables predictive maintenance, which involves scheduling maintenance based on the actual condition of the machine rather than a fixed schedule. By tracking machine performance and understanding the factors leading to breakdowns, maintenance can be carried out when necessary, optimizing both repair costs and the overall efficiency of the manufacturing process.
Benefits of CNC Programming for Predictive Analytics
- Reduced downtime: By predicting machine breakdowns, time-consuming repairs can be avoided, leading to reduced downtime and increased productivity.
- Improved safety: Preventive maintenance helps to ensure that machines are in optimal condition, reducing the risk of accidents and injuries.
- Cost savings: By avoiding costly emergency repairs and optimizing maintenance schedules, significant cost savings can be achieved.
- Increased efficiency: Proactive maintenance allows manufacturers to plan production schedules more effectively, maximizing efficiency.
- Enhanced product quality: By minimizing machine failures, manufacturers can deliver products of consistent quality, leading to customer satisfaction and loyalty.
Conclusion
CNC programming combined with predictive analytics is revolutionizing the manufacturing industry. By leveraging data-driven insights, manufacturers can predict machine breakdowns and implement preventive measures. This approach not only optimizes maintenance schedules but also improves productivity, reduces costs, and enhances product quality. As technology continues to advance, CNC programming for predictive analytics will become an essential tool for manufacturers in maintaining a competitive edge.
Comments:
This article on revolutionizing CNC programming with predictive analytics is really interesting! The advancements in technology are truly amazing.
@Emily I agree! The power of predictive analytics in CNC programming can greatly improve efficiency and accuracy in manufacturing processes. It's exciting to see how far we've come.
@Marcus Absolutely! It opens up new possibilities for optimizing CNC operations and reducing errors. Do you have any experience implementing predictive analytics in CNC programming?
As someone who works in the CNC industry, I find this article really helpful. Predictive analytics could be a game-changer in improving productivity and reducing downtime. Can anyone share their implementation experiences?
@Brandon I've tried implementing predictive analytics in our CNC programming department, and it has made a significant impact. We can anticipate maintenance needs and adjust programming accordingly. It has saved us a lot of time and resources.
@Sophie That's impressive! How did you initially introduce predictive analytics into your CNC programming processes?
This article is an eye-opener! I never realized the potential of harnessing the power of ChatGPT in revolutionizing CNC programming. Exciting times ahead!
@Rachel Thank you for your feedback! I'm glad you found the article informative. The integration of ChatGPT with CNC programming indeed opens up new possibilities for automation and optimization.
I'm curious about the potential limitations of using predictive analytics in CNC programming. Are there any risks or challenges that need to be addressed?
@Alex Good question! While predictive analytics can greatly benefit CNC programming, there are certainly challenges. One of them is ensuring data accuracy and reliability for accurate predictions. Also, proper training and understanding of the technology are crucial to leverage its full potential.
The article mentions the power of ChatGPT. Can anyone elaborate on how exactly ChatGPT is integrated into CNC programming?
@Daniel ChatGPT can be used to generate CNC program code based on given parameters or issues described in plain English. It helps with automation and streamlining the programming process, making it more efficient.
@Sophie That sounds intriguing! How accurate and reliable is the code generated by ChatGPT? Are there any validation steps required?
@Marcus Validating the code is essential. We have a team of CNC experts who review and refine the code generated by ChatGPT to ensure accuracy before implementation. It's a collaborative effort to maintain quality standards.
Predictive analytics in CNC programming could also have implications for supply chain management. It can help better forecast material needs and optimize inventory levels.
@Natalie That's a great point! By integrating predictive analytics throughout the manufacturing process, from CNC programming to supply chain management, the overall efficiency can be significantly improved.
This article made me realize how vital it is to stay updated with advancements in technology, especially in CNC programming. It can give businesses a competitive edge!
@Emily Absolutely! Embracing the power of predictive analytics and technologies like ChatGPT can help businesses enhance their operations, increase productivity, and stay ahead in the industry.
I believe exploring the potential of predictive analytics in CNC programming is essential for long-term success. It's an exciting time for the manufacturing industry!
@Sophie I agree! Embracing technological advancements and leveraging AI can be a game-changer. It will be interesting to see how predictive analytics continues to evolve in CNC programming.
Predictive analytics in CNC programming offers endless possibilities for optimizations. Equipment monitoring, preventive maintenance, and real-time adjustments are just a few areas that can benefit.
@Marcus Indeed! The potential for improving efficiency, reducing downtime, and optimizing CNC operations through predictive analytics is immense. It's exciting to think about the future possibilities.
I appreciate all the insights shared here. It's valuable to hear real-life experiences with implementing predictive analytics in CNC programming. It motivates me to explore its potential further.
@Brandon Absolutely! Learning from others' experiences can provide valuable insights and inspiration. Best of luck in your explorations of predictive analytics in CNC programming!
Are there any specific industries where the application of predictive analytics in CNC programming has shown significant benefits?
@Alex Predictive analytics can benefit various industries, including automotive, aerospace, electronics, and medical device manufacturing. It helps optimize production processes across different sectors.
@Marcus In addition to those industries, I've also seen great potential for predictive analytics in the furniture manufacturing sector. It helps optimize material usage and production planning.
This article has definitely sparked my interest in exploring the possibilities of predictive analytics in CNC programming. The potential benefits are enormous!
@Daniel That's fantastic! Exploring new technologies and advancements can lead to exciting discoveries and opportunities. Good luck in your exploration!
It's fascinating to witness how technology continues to reshape the manufacturing industry. Predictive analytics in CNC programming is another step towards a more efficient and optimized future.
@Rachel Indeed! The continuous advancements in technology pave the way for a smarter and more automated manufacturing industry. Predictive analytics is just one of the many promising tools.
I appreciate the reminder to stay updated with technological advancements. It's essential not to overlook the potential benefits they can bring to our CNC programming processes.
@Brandon Absolutely! Continuous learning and adaptation are crucial in staying competitive. Embracing technological advancements can significantly impact the success of our CNC operations.
What are some key factors to consider before implementing predictive analytics in CNC programming? Any challenges to be aware of?
@Alex Some key factors to consider include data quality and accuracy, technological infrastructure, security measures, and training for the team. Challenges can arise in data integration and ensuring the reliability of predictions.
Another challenge is managing expectations and understanding that predictive analytics is a tool to enhance decision-making rather than a guaranteed solution. It requires continuous monitoring and refinement.
@Emily That's an important point! Implementing predictive analytics successfully requires a holistic approach, involving both technological and human aspects of the CNC programming process.
The potential for predictive analytics in CNC programming is enormous, but it's important to approach it with a clear strategy. Aligning the technology with specific business goals is crucial for success.
Understanding the limitations and challenges of predictive analytics in CNC programming is equally important. It helps set realistic expectations and plan for necessary resources and expertise.
@Daniel You're absolutely right. Proper planning and understanding of the technology, along with addressing challenges, are key to successfully harnessing the power of predictive analytics.
I've always been fascinated by CNC programming, and this article has made me even more excited about the possibilities of leveraging predictive analytics. It's a compelling combination!
@Sarah I'm glad this article has sparked your interest! The combination of CNC programming and predictive analytics indeed holds immense potential for optimizing manufacturing processes.
The use of predictive analytics in CNC programming not only improves efficiency but also reduces costs in the long run. It's a win-win situation for manufacturers.
@Natalie I completely agree! The ability to optimize processes, minimize wastage, and reduce errors through predictive analytics directly translates into cost savings and improved profitability.
Predictive analytics in CNC programming can also help in identifying patterns and trends that aid in process optimization and decision-making. It's like having an intelligent assistant!
@Sophie Well said! Predictive analytics acts as a valuable assistant, providing insights and recommendations to improve CNC programming and drive better results.
Thank you to everyone who shared their experiences and insights. This discussion has been really helpful in understanding the potential of predictive analytics in CNC programming. Great article!
@Brandon Thank you for your kind words! I'm grateful for all the insightful contributions here. It's amazing to see the engagement and interest in this topic.
@Brandon You're welcome! It was a pleasure discussing the topic with everyone. Glad to hear you found it helpful. Feel free to ask if you have further questions.
Indeed, this discussion has been enlightening. Thank you, @Michael Hoteling, for sharing this informative article with us and actively participating in the conversation.