Revolutionizing Gemba Walks: Harnessing ChatGPT for Lean Thinking Technology
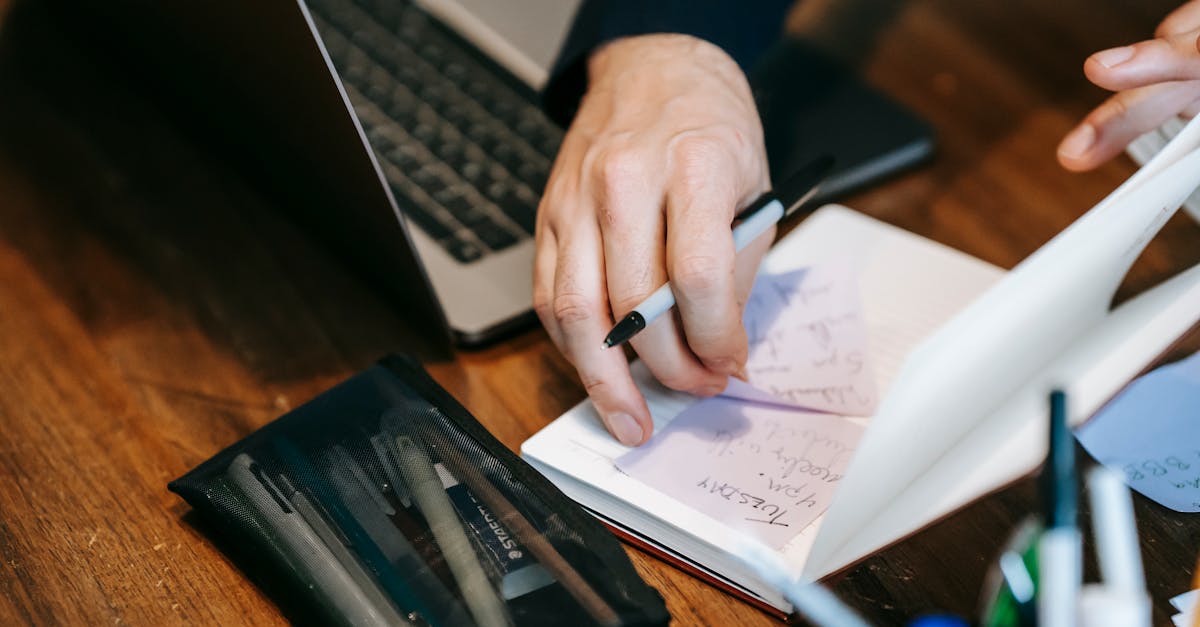
Introduction
Lean Thinking, a philosophy born out of the Toyota Production System (TPS), has become widely adopted by industries around the world. It focuses on continuously improving processes and eliminating waste to create value for customers. Gemba Walks, one of the core practices of Lean Thinking, involves going to the place where work is done to observe firsthand the processes, identify problems, and drive improvements.
The Role of Gemba Walks in Lean Thinking
Gemba, a Japanese term meaning "the real place," emphasizes the importance of observing work in its actual context. It provides an opportunity for leaders and team members to engage with the processes, better understand the challenges faced by the frontline workers, and find opportunities for optimization.
Gemba Walks promote a culture of continuous improvement, fostering collaboration and communication across different levels of the organization. By physically being in the work area, leaders can gain insights into the true state of operations, uncover bottlenecks, and identify areas where waste occurs.
Introducing ChatGPT-4 as a Digital Companion
With advancements in natural language processing and artificial intelligence, ChatGPT-4 now offers a unique opportunity to enhance Gemba Walks. Acting as a digital companion, ChatGPT-4 can accompany leaders during these walks, working as an intelligent assistant to record observations, suggest improvements, and identify areas of opportunity.
Recording Observations and Suggestions
During Gemba Walks, it is crucial to capture relevant information accurately and efficiently. With ChatGPT-4, leaders can simply speak or type their observations, and the AI system will effortlessly record them. This minimizes the need for manual note-taking, allowing leaders to focus their attention on understanding the processes and engaging with the frontline staff.
Furthermore, ChatGPT-4 can analyze the data in real-time and offer immediate suggestions for improvement. By leveraging its vast knowledge base and analytical capabilities, it can provide insights into potential areas of waste, such as overproduction, waiting, transportation, and inventory handling.
Identifying Improvement Opportunities
Through its advanced algorithms, ChatGPT-4 can identify patterns and anomalies in the observed processes. It can compare current performance against best practices or predefined benchmarks, highlighting areas where the organization falls short. This helps leaders to prioritize improvement projects and allocate resources more effectively.
Additionally, ChatGPT-4 can facilitate a dialogue between the leader and the frontline workers. Its natural language processing capabilities enable it to understand and respond to questions, providing clarification, guidance, and knowledge transfer. It can foster an environment of open communication, encouraging employees to share their insights and suggestions for improvement.
Conclusion
Combining Gemba Walks with the power of ChatGPT-4 can unleash new possibilities for Lean Thinking and continuous improvement. The technology acts as a digital companion, recording observations, offering suggestions, and facilitating dialogue. By leveraging AI, organizations can enhance their ability to eliminate waste, improve processes, and ultimately deliver greater value for their customers.
References:
- Lean Enterprise Institute. (2021). What Is Lean? Retrieved from https://www.lean.org/whatslean
- Pokharel, S. (2020). Using AI Chatbots in Gemba Walks. Retrieved from https://www.linkedin.com/pulse/using-ai-chatbots-gemba-walks-shovit-pokharel
Comments:
Thank you all for taking the time to read my article on revolutionizing Gemba walks using ChatGPT for Lean Thinking technology. I'm excited to hear your thoughts and opinions!
Great article, Jody! Gemba walks are essential in lean thinking, and incorporating technology like ChatGPT can definitely revolutionize the process.
I agree, Mark! Leveraging technology can enhance the efficiency and effectiveness of Gemba walks. Jody, your article highlights some interesting possibilities.
Mark, do you have any insights on potential challenges organizations might face when adopting ChatGPT for Gemba walks?
Good question, Emily. Some challenges include initial resistance from employees, integrating the technology into existing processes, and ensuring data security and privacy. However, with proper planning and implementation, these challenges can be overcome.
Mark, your point about incorporating ChatGPT into Gemba walks is intriguing. How do you see it impacting cross-functional collaboration within organizations?
Good question, Laura. By enabling real-time communication and collaboration, ChatGPT can help break down silos and foster cross-functional teamwork. It creates opportunities for sharing insights, ideas, and problem-solving across departments.
Jody, your article inspired me to implement ChatGPT technology during our Gemba walks. It has increased communication and helped us identify improvement opportunities faster. Thank you!
Alice, that's fantastic to hear! How did you manage the initial resistance from team members when introducing ChatGPT during Gemba walks?
Good question, Grace. We conducted training sessions to familiarize everyone with ChatGPT and its benefits. Additionally, we emphasized that the technology enhances, rather than replaces, our Gemba walk practices.
Alice, did you face any challenges in terms of data accuracy or interpretation while using ChatGPT during Gemba walks?
Yes, Daniel, ensuring data accuracy was crucial. We initially faced some challenges with interpretation, as the technology is still evolving. However, with experience and periodic calibration, we were able to improve accuracy and enhance its value.
I have a question, Jody. How do you manage potential distractions caused by using technology during Gemba walks?
That's a great question, Adam. It's important to establish guidelines and boundaries when incorporating technology. Setting clear expectations and ensuring its use is in line with the purpose of Gemba walks can help minimize distractions.
Jody, your article got me thinking about how this technology could be applied in different industries beyond manufacturing. Are you aware of any examples or case studies?
Absolutely, Catherine! While most examples focus on manufacturing, I've come across case studies where ChatGPT has been successfully utilized in healthcare, logistics, and service industries as well.
Jody, what are your thoughts on the future of Gemba walks with the integration of AI and other advanced technologies?
Great question, David! I believe AI and advanced technologies will play an increasingly significant role in Gemba walks. They can provide real-time insights, predictive analytics, and assist in decision-making, ultimately driving continuous improvement efforts.
Jody, I would love to explore the application of ChatGPT in the service industry. Are there any specific use cases or success stories you could share?
Certainly, John! In the service industry, ChatGPT has been successfully used in customer service interactions, improving response times, and enhancing the quality of support provided. It has also been deployed in call centers to assist agents in resolving customer queries efficiently.
That's interesting, Jody! Have you come across any challenges or limitations when implementing ChatGPT in non-manufacturing sectors like healthcare?
Absolutely, Ethan! Challenges include the need for customization to specific healthcare settings, ensuring patient data privacy, and the need for ongoing training to improve accuracy in medical terminology and context. However, it has shown promise in tasks like automating patient history documentation and aiding diagnoses.
Jody, do you think AI-enabled Gemba walks might bring about a shift in the role of lean practitioners?
Great question, Sophia! I believe AI-enabled Gemba walks will indeed shift the role of lean practitioners. Instead of spending significant time on data collection, they can focus more on analysis, strategy, and leading improvement initiatives based on the insights provided by AI. It will require evolving skill sets and adapting to technological advancements.
Jody, I really enjoyed your article. I can see the potential benefits of ChatGPT in Gemba walks. It's a fascinating area of development!
Jody, I believe incorporating AI and advanced technologies will require organizations to ensure proper change management and provide training to employees to embrace and maximize their benefits.
Absolutely, Karen! Change management, training, and creating a culture of continuous improvement will be crucial in effectively leveraging AI and advanced technologies in Gemba walks.
Catherine, I can envision ChatGPT being used in retail environments, especially for analyzing customer behavior and making data-driven decisions to optimize store layouts and product placements.
Adam, to minimize distractions, establishing clear goals for Gemba walks and ensuring technology usage aligns with those goals is important. It's crucial to strike the right balance!
I have mixed feelings about this. While technology can be useful, I worry that it might undermine the human connection and observation aspect of Gemba walks.
I understand your concern, Samuel. However, I think incorporating technology can provide additional insights and data that may otherwise be missed during traditional Gemba walks.
I see both sides of the argument. Technology can be valuable, but we should also ensure that we don't lose the human touch and direct engagement that Gemba walks provide.
Jennifer, I agree with your concern about maintaining human engagement. Technology should complement, not replace, the personal connection between teams during Gemba walks.
Jennifer, you raised an essential point. While technology aids Gemba walks, we shouldn't overlook the importance of face-to-face interactions and observing physical processes directly.
Thank you, everyone, for your valuable comments and questions! It's been a pleasure discussing the potential of ChatGPT in revolutionizing Gemba walks. Your insights and perspectives have been enlightening!
Jody, I'm curious if ChatGPT can help in identifying trends or patterns in customer feedback to drive improvements in the service industry.
Certainly, Rhonda! ChatGPT can analyze a large volume of customer feedback, detect patterns, and identify areas for improvement. It enables organizations to prioritize their efforts and address customer concerns more effectively.
Jody, the use of ChatGPT in automating patient history documentation sounds promising. Do you have any insights into its accuracy and reliability?
Great question, Liam! While ChatGPT shows promise in automating patient history documentation, it is crucial to validate the accuracy and reliability of the generated content. Human oversight and periodic review are essential to ensure the quality and integrity of the patients' records.
Thank you all for your participation and insightful comments! It's been an engaging discussion. If you have any further questions or ideas, feel free to reach out. Together, we can continue improving Gemba walks with technology.