Revolutionizing Lean Initiatives with ChatGPT: Enhancing Predictive Maintenance in Tech
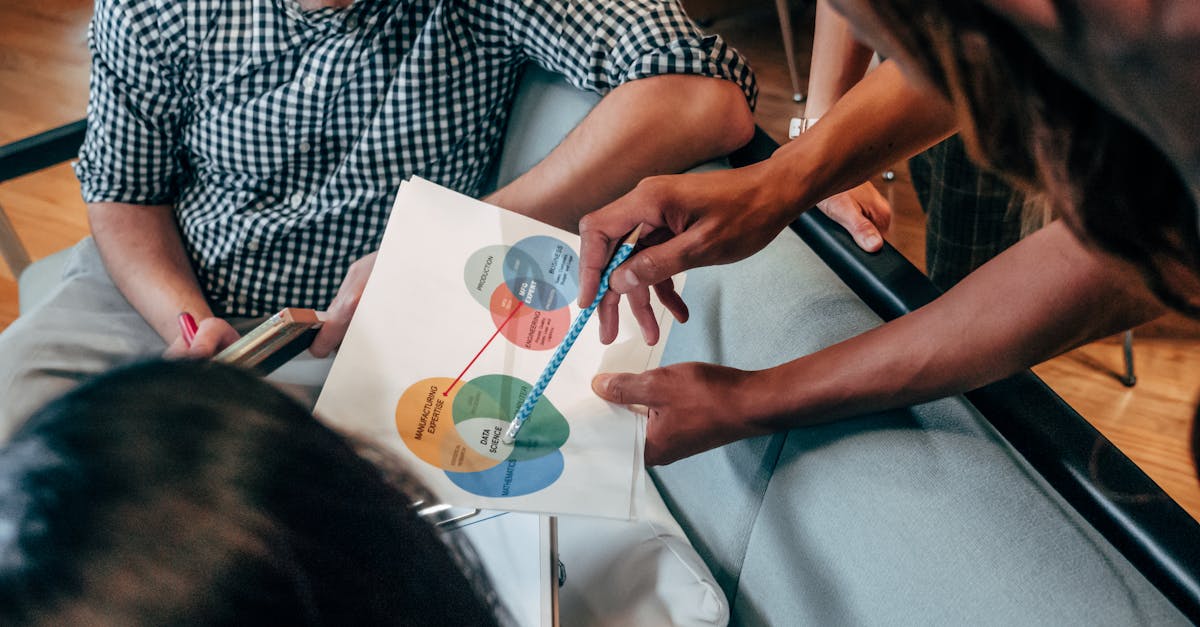
Predictive maintenance, a key aspect of lean initiatives, has revolutionized the way industries approach equipment maintenance. By utilizing advanced data analytics techniques, predictive maintenance allows organizations to predict and mitigate equipment failures before they occur. This proactive approach to maintenance helps reduce downtime, improve overall equipment efficiency, and minimize repair costs.
What is Predictive Maintenance?
Predictive maintenance is a technique that involves using historical usage and performance data to make accurate predictions about the health and condition of equipment. By analyzing this data, organizations can determine when and how equipment failures are likely to occur, enabling them to take preventive measures and avoid unexpected downtime and breakdowns.
The Role of Lean Initiatives
Lean initiatives, originally developed by Toyota, are focused on eliminating waste and improving operational efficiency. Predictive maintenance perfectly aligns with the principles of lean manufacturing by reducing waste in terms of time, resources, and costs associated with reactive maintenance practices. By adopting predictive maintenance strategies, organizations can shift from costly scheduled maintenance or reactive repairs to a more efficient and proactive approach.
Benefits of Predictive Maintenance
There are several benefits to implementing predictive maintenance as part of lean initiatives:
- Reduced Downtime: Predictive maintenance enables organizations to identify potential equipment failures before they occur, allowing for proactive repairs or replacements. This minimizes unscheduled downtime and ensures continuity of operations.
- Increased Equipment Lifetime: By identifying and addressing potential issues in advance, predictive maintenance helps extend the lifespan of equipment. This not only reduces replacement costs but also optimizes the return on investment (ROI) for organizations.
- Improved Safety: Equipment failures can pose significant safety risks to operators and employees. Predictive maintenance helps mitigate these risks by identifying and preventing potential failures, ensuring a safer working environment.
- Optimized Maintenance Costs: Reactive maintenance practices can be expensive, as they involve unplanned repairs and replacements. Predictive maintenance allows organizations to plan maintenance activities in advance, reducing overall maintenance costs and optimizing resource allocation.
- Enhanced Operational Efficiency: By minimizing unexpected downtime and optimizing maintenance activities, predictive maintenance helps improve overall operational efficiency. Organizations can better plan production schedules, ensuring uninterrupted workflow and customer satisfaction.
Implementing Predictive Maintenance
To implement predictive maintenance, organizations need access to relevant usage and performance data. This can be collected through various means, including Internet of Things (IoT) devices, machine sensors, and existing equipment monitoring systems. Once the data is collected, advanced analytics techniques, such as machine learning algorithms, can be used to detect patterns, identify anomalies, and predict equipment failures with a high degree of accuracy.
Organizations should also establish a maintenance strategy that outlines the steps to be taken based on the predictions made through the analysis of data. This strategy may include preventive maintenance tasks, scheduled repairs, or replacement plans, depending on the severity of the predicted failure. By combining data analysis with a well-defined maintenance strategy, organizations can effectively implement predictive maintenance and realize its full benefits.
Conclusion
Predictive maintenance is a powerful tool that can significantly improve equipment reliability, reduce downtime, and optimize maintenance costs. By leveraging lean initiatives and analyzing usage and performance data, organizations can proactively predict and mitigate equipment failures before they occur. Implementing predictive maintenance not only improves operational efficiency but also enhances safety, extends equipment lifetime, and provides a competitive advantage in today's fast-paced industries.
Comments:
Thank you all for reading my article 'Revolutionizing Lean Initiatives with ChatGPT: Enhancing Predictive Maintenance in Tech'! I'm excited to hear your thoughts and opinions.
Cindy, excellent article! I believe AI-driven predictive maintenance can enhance productivity by minimizing unplanned downtimes and optimizing maintenance schedules.
Sarah, I couldn't agree more. AI can enable companies to move from reactive to proactive maintenance, resulting in improved efficiency and reduced costs.
Great article, Cindy! I completely agree that incorporating AI like ChatGPT can improve predictive maintenance in tech. It has the potential to revolutionize the way we manage maintenance tasks.
Scott, I agree with you. AI can definitely play a significant role in predictive maintenance. It can assist in detecting potential problems early and preventing costly downtimes.
Emma, I agree with your point about AI detecting potential problems early. It can save a lot of time and resources by enabling proactive maintenance.
Scott, do you think there are any limitations or challenges when it comes to implementing ChatGPT in the context of predictive maintenance?
Daniel, one challenge I can think of is the interpretability of AI-generated predictions. It's crucial to understand how the AI arrives at its conclusions to gain trust and make informed decisions.
I disagree with the idea that AI can enhance predictive maintenance. While it may be useful for certain tasks, relying too heavily on AI can lead to unforeseen issues and less human oversight.
I see your point, Emily. But I think AI can complement human efforts, not replace them entirely. It can help identify patterns and anomalies that humans might miss, leading to more effective maintenance strategies.
Emily, I understand your concerns, but AI can actually increase human oversight. By providing data-driven insights, it allows technicians to make more informed decisions.
I'm skeptical about the effectiveness of AI in predictive maintenance. It requires a massive amount of accurate data for accurate predictions, and that can be a challenge.
David, you're right that data quality is crucial for accurate predictions. However, with advances in data collection and analysis, obtaining the required data is becoming more feasible.
Mike, I agree with your point that AI can help identify patterns and anomalies. It can alleviate the burden of manual analysis and enable technicians to focus on more critical tasks.
Mike, I agree that advancements in technology make obtaining accurate data more feasible. Companies should also focus on data quality control to ensure better predictions.
Absolutely, David. Data quality control is crucial for the success of any predictive maintenance program that incorporates AI.
David and Mike, I believe data accuracy, relevancy, and timeliness are critical in achieving reliable predictive maintenance results. The right data inputs are key.
Jessica, I agree with you. The quality and relevance of data inputs are indeed crucial for obtaining reliable predictive maintenance results.
David and Jessica, I completely agree that data quality is paramount. Having accurate and relevant data increases the reliability and effectiveness of AI-powered predictive maintenance.
Maria, absolutely! Organizations need to ensure that their data collection methods and storage systems are robust enough to handle the demands of AI-driven predictive maintenance.
Jessica, I completely agree. Proper data management is vital to ensure the accuracy and integrity of AI-driven predictive maintenance systems.
David, indeed. Organizations need to have robust data governance practices in place to maintain the quality and security of their data.
Jessica, I couldn't agree more. Data governance is crucial not only for predictive maintenance but for all AI applications.
In my experience, implementing AI for predictive maintenance has shown a noticeable improvement in detecting and preventing equipment failures. It's a game-changer!
Absolutely, Robert! The ability of AI to analyze vast amounts of data in real-time and generate actionable insights is a significant advantage.
The cost of implementing advanced AI systems like ChatGPT can be high. Small and medium-sized enterprises may find it challenging to invest in such technologies.
Karen, that's a valid concern. However, as AI technology continues to evolve, we may see more affordable solutions tailored to the needs of smaller businesses.
Julia, affordability is indeed a challenge for some businesses. However, the long-term benefits and cost savings resulting from fewer equipment failures may outweigh the initial investment.
Robert, you're right about the long-term benefits outweighing the initial investment. The key is to develop a well-thought-out implementation strategy.
Agreed, Julia. Proper planning and stakeholder involvement are vital for successful AI implementation in predictive maintenance.
Exactly, Sarah. It's crucial to have a clear understanding of the organizational and operational challenges before implementing AI-driven predictive maintenance.
Mark, you've highlighted an essential point. A comprehensive understanding of the challenges allows us to develop effective mitigation strategies.
Absolutely, Daniel. Proactive planning and collaboration with stakeholders can significantly increase the chances of successful AI implementation.
Mark and Sarah, I couldn't agree more. Understanding the specific challenges and requirements of each organization is crucial for a successful implementation.
Robert, you're spot on. Each organization's unique context should inform the approach and priorities when implementing AI for predictive maintenance.
Robert, I agree with you. Smaller businesses should seek guidance or collaborate with industry experts to overcome the affordability challenge in adopting AI for predictive maintenance.
Karen, collaborating with industry experts is an excellent suggestion. It can help smaller businesses gain insights and develop cost-effective AI strategies.
Absolutely, Jessica. Collaboration and knowledge sharing among industry peers can significantly expedite the adoption and enhancement of AI for predictive maintenance.
David, Jessica, and Sarah, you all touched on a critical point - proper planning and data governance are key pillars for successful AI implementation.
Mark, well said. Organizations should approach AI implementation in predictive maintenance as part of a broader, well-executed digital transformation strategy.
Scott and Julia, thanks for sharing your insights. It's fascinating to see the potential benefits and challenges of AI in the context of predictive maintenance.
Absolutely, Daniel! The continuous advancements in AI technologies provide both opportunities and obstacles that we need to navigate.
Thank you all for the engaging discussion and valuable insights! I appreciate the different perspectives shared here.
Indeed, Cindy has written a thought-provoking article that encourages us to explore the potential of AI in maintenance operations.
Cindy, thank you for shedding light on how ChatGPT can revolutionize lean initiatives and enhance predictive maintenance. It's an exciting time for the industry!
Thank you, William! I'm glad you found the article enlightening. Exciting times lie ahead as AI continues to transform the field of maintenance and reliability.
Thank you all for sharing your insights and experiences. It's been a valuable learning experience discussing the potential of AI in predictive maintenance.
Thank you all once again for your active participation and valuable contributions! Let's continue exploring the transformative potential of AI in maintenance.
Thank you all for the incredible discussion on the potential of AI in predictive maintenance. Your insights have been invaluable, and it's been a pleasure engaging with each of you.
With that, let's bring this discussion to a close. Feel free to reach out if you have any further questions or would like to continue the conversation. Thank you!