Revolutionizing Product Design in Mechanical Technology with ChatGPT
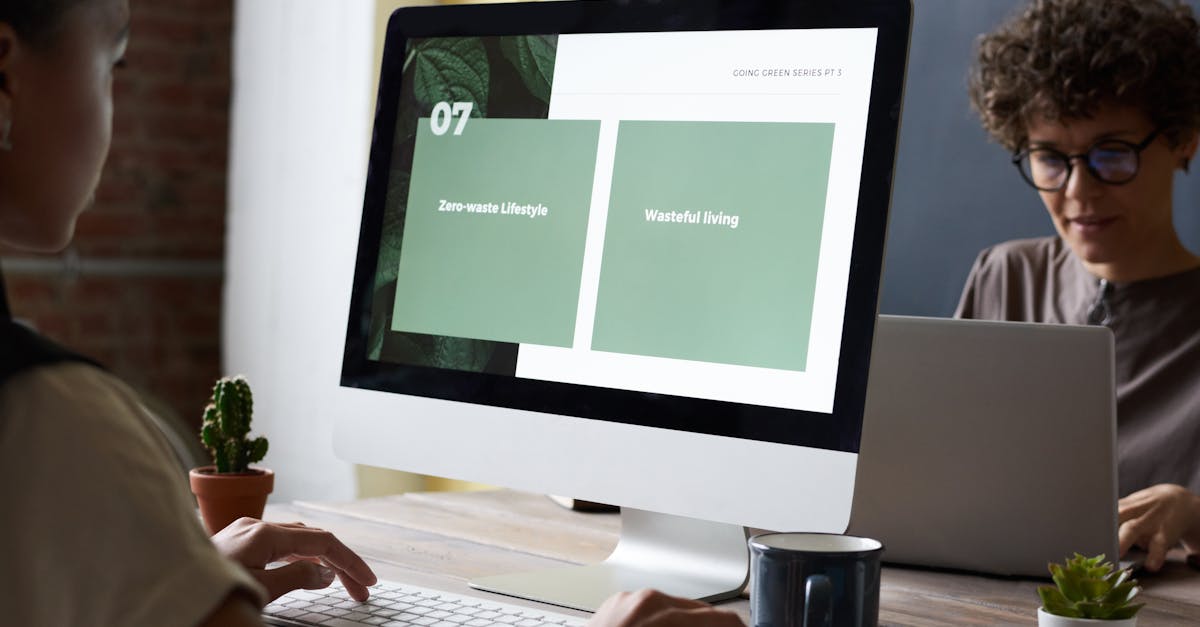
Simulating Part Reactions
Mechanical technology plays an integral role in the field of product design, with its scope expanding well beyond mere application to most of our contemporary modern era. Craftsmanship, meticulousness, and unparalleled technicality are the soul of mechanical technology which, when blended with product design, can yield extraordinary results.
The relationship between mechanical technology and product design is multi-faceted, shaping how products are drafted and redesigned, especially with a focus on mechanical parts. One of the key fields in which this interaction manifests is the simulation of how parts might react under certain conditions - an essential step in ascertaining a product's feasibility, durability, and safety.
The Role of Mechanical Technology in Product Design
Product design is an art that factors in aesthetics, functionality, and the user experience. The goal is to create products that not only look good but also work well - and that's where mechanical technology comes in. It provides the tools to envision, simulate, and test the functionality of a product, enabling designers to anticipate how mechanical parts will behave under different conditions. This is particularly crucial when designing complex products in industries such as automotive, aerospace, and robotics.
The advantages of employing mechanical technology in product design are numerous. It enables the understanding of how different materials behave and interact, and how design decisions impact a product's performance. It also helps in troubleshooting and rectifying design flaws early on in the process, saving costs and resources by reducing the need for physical prototypes and comprehensive testing stages.
Simulation: A New Approach to Designing Mechanical Parts
One of the most transformative advancements in mechanical technology is the ability to simulate how a part might react under specific conditions. Using computer-aided design (CAD) software, designers can build digital 3D models of a product or part and apply various forces or conditions to it. The software can then predict how the part will respond under those conditions, giving designers an accurate idea of what to expect from the real thing.
Simulating part reactions offers several benefits. It can significantly speed up the product design process by allowing flaws and weak points in a design to be identified early. It also aids in improving the efficiency of a product by refining part designs for optimal performance.
More importantly, using simulations could potentially overcome the limitations of traditional prototyping methods. Traditional methods primarily rely on physical replicas and manual testing, which are not only time-consuming but also costly. These costs only multiply when dealing with complex mechanical parts.
The Future of Mechanical Technology in Product Design
We are at a juncture where the fusion of technology and creativity is redefining the product design landscape. As we continue to embrace mechanical technology, expectations are high for even more sophisticated simulations that can provide detailed insights into a part's potential behavior. This includes not just force-based conditions, but also the impact of temperature variations, material stresses, and even the wear and tear that a part may experience over time.
As we continue to advance, we can anticipate further integration of mechanical technology within the product design sector. It fosters a more efficient and streamlined design process, offering an excellent scope for innovation, reducing waste, and promoting sustainable practices. With the ability to simulate part reactions, we are not only making more reliable products but also paving the way for the future.
Comments:
Great article, Victor! ChatGPT seems like a game-changer in revolutionizing product design. I'm excited to see how it will enhance mechanical technology.
Thank you, Michael! I believe ChatGPT has the potential to greatly impact the field. It can expedite the design process and improve collaboration between engineers and designers.
As a mechanical engineer, I'm curious to know how ChatGPT can assist in complex design challenges. Can it handle intricate simulations and calculations?
That's a valid point, Linda. While ChatGPT can provide suggestions and generate ideas, it may not be suitable for in-depth simulations or calculations. However, it can complement the design process and assist in generating innovative concepts.
I'm concerned about the potential limitations of using ChatGPT in product design. Human intuition and creativity play a vital role, and relying solely on AI may hinder that aspect.
I understand your concern, Daniel. ChatGPT is designed to augment human creativity, not replace it. It can generate ideas and provide insights, allowing designers and engineers to explore new possibilities more efficiently.
I'm impressed with the potential of ChatGPT, but what about the ethical considerations? Who takes responsibility if an AI-generated design fails?
Ethical considerations are indeed crucial, Emily. Ultimately, the responsibility lies with the engineers and designers who make the final decisions. ChatGPT can be a valuable tool, but human expertise and accountability should always prevail.
I wonder if using ChatGPT in product design will eventually reduce job opportunities for mechanical designers. Could it potentially replace human designers?
Valid concern, Marcos. While ChatGPT can automate certain design aspects, it cannot replace the expertise and creativity of human designers. Rather than eliminating jobs, it has the potential to enhance their work and enable them to focus on more complex and innovative tasks.
I believe collaboration between humans and AI is the future. ChatGPT, when integrated correctly, can greatly enhance creativity, problem-solving, and efficiency in product design.
Well said, Sarah! The partnership between humans and AI can lead to remarkable advancements in various fields, including product design. I share your optimism in the future of collaborative innovation.
While the potential of ChatGPT in product design is exciting, we must also address potential biases in AI-generated designs. How can we ensure inclusivity and avoid perpetuating existing biases?
An important aspect to consider, Robert. It is crucial to train ChatGPT using diverse datasets and actively involve a multidisciplinary team in the design process. By promoting inclusivity and diversity, we can minimize biases and create more equitable solutions.
I'm interested to know if ChatGPT has been implemented in any real-world mechanical design projects. Are there any success stories or case studies available?
Good question, Grace. While ChatGPT is still relatively new, there have been some pilot projects where it has shown promise. However, it's essential to establish a robust evaluation framework and continue refining the model before widespread adoption.
Will using ChatGPT in product design require significant computational resources? Small design teams or individual designers may face challenges with hardware requirements.
Valid concern, Mark. While using ChatGPT can benefit from computational resources, efforts are being made to make it more accessible. There are cloud platforms available that can provide the necessary computational power, even to smaller design teams and individual designers.
Apart from mechanical design, do you see ChatGPT being useful in other areas of engineering, such as civil or electrical engineering?
Absolutely, Rachel! While the initial focus may be on mechanical design, the underlying principles of ChatGPT can be applied to various engineering disciplines. It has the potential to assist in generating innovative solutions and optimizing designs across multiple fields.
What are the limitations of ChatGPT in terms of language understanding and context? Can it effectively understand complex design requirements and constraints?
Good question, Jonathan. While ChatGPT has made significant strides in natural language understanding, it may occasionally struggle with certain nuances and complex design requirements. It's essential to provide clear instructions and verify the output to ensure it aligns with the intended design context.
How user-friendly is ChatGPT for non-technical users? Would an engineer with minimal AI experience be able to utilize it effectively?
That's a legitimate concern, Olivia. While ChatGPT is designed to be user-friendly and accessible, it may still require some familiarity with AI and design concepts. However, efforts are being made to create intuitive interfaces to facilitate its usage for non-technical users.
What are the potential risks of relying extensively on AI for product design? Can it undermine critical thinking and problem-solving skills?
Valid concern, Ryan. While AI can enhance the design process, excessive reliance without critical thinking can be detrimental. It's crucial for designers and engineers to maintain their problem-solving skills and engage in a balanced partnership with AI to ensure innovative and effective solutions.
I'm fascinated by the idea of ChatGPT assisting designers, but how secure is the intellectual property when using such AI models? Are there any privacy concerns?
An important point, Sophia. Intellectual property and privacy are vital considerations. When utilizing AI models like ChatGPT, it's crucial to establish appropriate security measures, data protection protocols, and legal agreements to safeguard confidential information and maintain privacy.
What are the current limitations of ChatGPT in terms of scalability? Can it handle large-scale design projects?
Scalability is an essential aspect, Jason. While ChatGPT has shown promise in various domains, including product design, there are technical challenges when it comes to handling extremely large-scale projects. However, ongoing research and advancements aim to address these limitations and improve scalability.
Considering the rapid advancements in AI, what future developments do you envision for ChatGPT specifically in the field of mechanical technology?
Exciting possibilities, Alexis! In the future, ChatGPT could become more proficient in understanding complex design constraints, handling simulations, and suggesting optimized solutions. It may even contribute to the automation of repetitive design tasks, freeing up time for designers to focus on innovation.
Are there any known limitations in terms of bias when using ChatGPT? How can we ensure the system remains unbiased in its design suggestions?
Excellent question, Adrian. Bias is a critical concern, and continuous efforts are being made to address it. By employing diverse datasets and engaging a multidisciplinary team during the training and validation stages, we can mitigate bias and ensure the system remains unbiased in its design suggestions.
I'd like to know more about the integration process of ChatGPT into existing product design workflows. Are there any specific requirements or challenges to consider?
Great question, Jordan. Integrating ChatGPT into existing workflows can bring about various considerations such as data compatibility, data preprocessing, and training time. Additionally, ensuring a seamless integration with the existing tools and processes can be a challenge that requires close collaboration between AI experts and domain specialists.
How can we validate the designs suggested by ChatGPT? Are there any evaluation methods or frameworks for assessing the effectiveness of its suggestions?
Validation is indeed crucial, Michelle. Developing evaluation methods and frameworks specific to ChatGPT's design suggestions is an ongoing effort. It involves iterative testing, comparing outcomes with human-designed solutions, and receiving continuous feedback from domain experts to refine the model's effectiveness and reliability.
What are the key differences between ChatGPT and other AI models or design software available in the market? What sets it apart?
Great question, Eric. ChatGPT's key differentiator lies in its ability to understand and generate human-like text, facilitating seamless communication between designers and the AI system. It aims to bridge the gap between designers and engineers, promoting collaboration, and utilizing AI to spark innovation.
I'm curious about the learning curve for using ChatGPT effectively. Would designers and engineers need extensive training to make the most out of this technology?
Learning how to effectively leverage ChatGPT may require some initial training and familiarization, Kimberly. However, efforts are being made to design intuitive user interfaces and provide comprehensive documentation to minimize the learning curve and enable designers and engineers to quickly integrate it into their workflows.
Are there any cost implications associated with using ChatGPT in product design? How does it compare to existing design software in terms of affordability?
Cost considerations are important, Kevin. While AI technology often incurs certain expenses, the overall affordability of ChatGPT depends on factors like usage demands, computational resources, and implementation requirements. However, as the technology matures and becomes more widespread, it can be expected that cost-effective solutions will emerge.
Could using ChatGPT potentially speed up the product design process? Can it assist in reducing time-to-market for new products?
Absolutely, Monica! ChatGPT has the potential to expedite the design process. By offering quick suggestions, generating ideas, and enhancing collaboration, it can assist in reducing the time-to-market for new products, giving companies a competitive edge in the industry.
How does ChatGPT handle conflicting design requirements or constraints? Can it analyze trade-offs and provide effective solutions in complex situations?
Great question, Connor. ChatGPT can offer suggestions based on user inputs and generate a variety of design possibilities. However, when it comes to analyzing trade-offs and providing effective solutions in complex situations, it may require collaboration with domain experts to ensure the final design aligns with all requirements and constraints.
How does ChatGPT handle real-time collaboration? Can multiple users actively communicate and work together with the AI system?
Real-time collaboration is an exciting aspect, Rebecca. While current systems may have limitations, there are ongoing advancements towards enabling multiple users to actively communicate and collaborate with ChatGPT simultaneously. This can enhance teamwork and foster synergy between designers, engineers, and the AI system.