Streamlining Manufacturing Processes with ChatGPT: Automation in the Industry
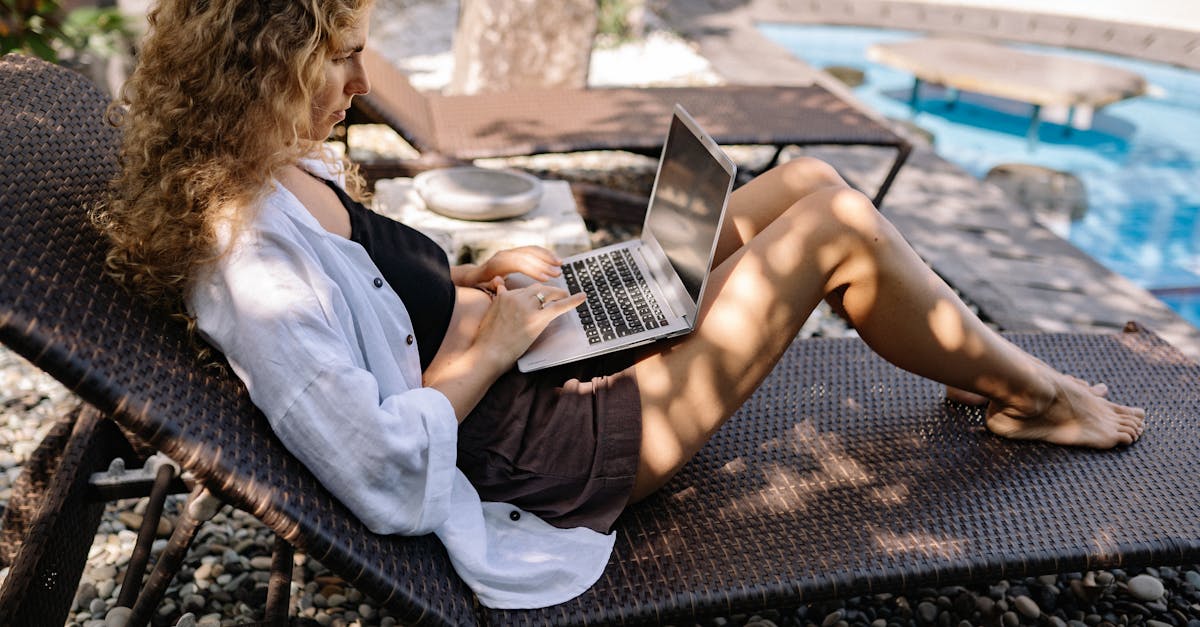
Introduction
In recent years, the advancement of artificial intelligence (AI) has revolutionized various industries, including manufacturing. With the emergence of ChatGPT-4, an advanced language model developed by OpenAI, manufacturers now have the opportunity to automate routine tasks and improve overall efficiency.
The Role of ChatGPT-4 in Manufacturing
ChatGPT-4 is a powerful AI model that has the ability to understand and generate human-like text. It can be trained on vast amounts of data, allowing it to acquire knowledge and respond to queries effectively. In manufacturing, this technology can be leveraged to automate several routine tasks.
Data Entry
Data entry is an integral part of any manufacturing process. It involves manually inputting data from various sources into computer systems. Traditionally, data entry tasks have been time-consuming and error-prone. However, ChatGPT-4 can help streamline this process by automating data entry tasks.
Using ChatGPT-4, manufacturers can build chatbots or virtual assistants that can extract information from documents, spreadsheets, or other sources and enter it into relevant databases or systems. This not only reduces the time and effort spent on manual data entry but also minimizes the chances of errors and inconsistencies.
Quality Control
Another important aspect of manufacturing is quality control. Inspecting products for defects or anomalies is crucial to ensure that only high-quality products reach the market. By training ChatGPT-4 to recognize common defects or anomalies, manufacturers can automate the quality control process.
ChatGPT-4 can analyze images or sensor data and identify potential issues with the products. It can provide real-time feedback and alerts, allowing manufacturers to address quality concerns promptly. This not only saves time but also improves overall product quality.
Inventory Management
Efficient inventory management is essential for manufacturing companies to optimize resources and meet customer demands. ChatGPT-4 can assist in automating inventory management tasks, such as forecasting demand and monitoring stock levels.
By analyzing historical data and market trends, ChatGPT-4 can predict future demand and recommend optimal stock levels. It can also generate automated reports, track inventory movement, and alert manufacturers when stock levels are running low or excess inventory needs to be cleared.
Benefits of Automating Routine Manufacturing Tasks
The automation of routine manufacturing tasks using ChatGPT-4 offers several benefits:
- Increased Efficiency: By automating tasks such as data entry, quality control, and inventory management, manufacturers can significantly improve operational efficiency. This frees up valuable human resources to focus on more complex tasks.
- Error Reduction: Manual data entry is prone to errors. By automating this process with the help of ChatGPT-4, the chances of human errors are minimized, leading to higher accuracy and lower rework.
- Cost Savings: Automating routine manufacturing tasks can lead to cost savings in the long run. With reduced labor hours and improved process efficiency, manufacturers can optimize their resources and cut down on operational costs.
- Real-time Insights: ChatGPT-4 provides real-time insights and alerts, enabling manufacturers to make informed decisions promptly. This enhances the agility and adaptability of manufacturing processes.
Conclusion
The integration of ChatGPT-4 technology into manufacturing processes has the potential to revolutionize the industry by automating routine tasks and increasing overall efficiency. By automating data entry, quality control, and inventory management, manufacturers can save time, reduce errors, cut costs, and make more informed decisions. It is crucial for manufacturers to explore the capabilities of ChatGPT-4 and leverage its potential for driving innovation and growth in the manufacturing sector.
Comments:
Great article, Lois! It's fascinating how automation is revolutionizing the manufacturing industry, and chatbots like ChatGPT have played a significant role in streamlining processes. Looking forward to seeing more use cases and success stories!
I totally agree, Michael! The integration of AI and automation in manufacturing has brought tremendous benefits. I believe it not only enhances productivity but also ensures higher accuracy and reduces human errors. Can't wait to hear more about the implementation challenges and best practices using ChatGPT!
Lois, your article is very informative! It's exciting to see how AI is transforming the manufacturing sector. I'm curious about the specific applications of ChatGPT in streamlining processes. Could you provide some real-life examples where it has made a significant impact?
Thank you, Michael, Emily, and Mark for your kind words! I'm glad you found the article helpful. Michael, I'll be sharing some interesting use cases in my next article. Emily, you're absolutely right about the benefits. AI-powered chatbots like ChatGPT have enhanced accuracy, reduced response times, and improved customer experience. Mark, sure! Let me give you an example - a manufacturing company implemented ChatGPT to automate the order tracking process, resulting in a significant reduction in manual effort and improved efficiency.
Lois, thank you for sharing the example! It's impressive to see how ChatGPT can streamline processes like order tracking. I'm curious, though, if there are any limitations to implementing AI chatbots in manufacturing. Are there any challenges or considerations that companies should be aware of?
You're welcome, Olivia! While AI chatbots like ChatGPT offer numerous benefits, there are indeed a few challenges to be aware of. One is the need for large and labeled datasets to train the model effectively. Additionally, ensuring data privacy, managing user expectations, and avoiding bias in responses are important considerations. I'll be discussing these challenges and providing best practices in my upcoming articles.
Lois, I appreciate your insight into the potential challenges. Data quality and biases in responses are critical aspects to address. I look forward to reading your upcoming articles for further guidance on effective implementation.
Thank you, Oliver! I'm glad you found the information valuable. Stay tuned for more insights on effective implementation strategies!
Hi Lois, great article! I wanted to know if there's a training period required for ChatGPT to learn a company's specific manufacturing processes, or can it be implemented with minimal setup and customization?
Thank you, Stella! ChatGPT requires training with domain-specific data and context to understand a company's manufacturing processes effectively. This training period allows it to learn and provide valuable responses. While it takes time and effort, the benefits outweigh the initial investment. Customization is vital to ensure accuracy and relevance to a specific industry.
Thank you, Lois! It's good to know that a strong IT infrastructure is necessary for successful implementation. I assume companies should also have a user-friendly interface to enable easy interaction with ChatGPT. Is that correct?
Absolutely, Stella! A user-friendly interface plays a significant role in ensuring a smooth user experience. Manufacturers should focus on designing intuitive interfaces that allow employees to interact with ChatGPT effortlessly. It enhances productivity and user adoption. Additionally, having features like natural language processing (NLP) and chat history retrieval further enrich the user interface.
Stella, I can share my experience with implementing ChatGPT. While setup and customization can require some initial effort, it's worth it. We conducted a training period where ChatGPT learned our specific processes, and over time, it became a valuable assistant in answering common queries and providing real-time guidance.
Thank you for sharing your experience, George! It's great to hear how ChatGPT has assisted you. The training period helps the model learn specific processes, making it a valuable tool in streamlining manufacturing operations.
Lois, you made an excellent point about collaborating with AI and cybersecurity experts. Companies need to have a holistic approach to security and risk management. By involving experts, they can identify vulnerabilities and proactively address potential threats in AI and automation systems.
Absolutely, Sophia! A holistic approach is crucial to ensure the safety and security of AI and automation systems. Collaboration with experts helps in identifying and mitigating vulnerabilities, enabling companies to build robust and reliable systems. Thank you for emphasizing that!
Absolutely, Lois. Collaboration with experts not only helps companies identify vulnerabilities but also ensures compliance with industry regulations and standards. With AI and automation systems becoming increasingly widespread, adherence to ethical considerations and legal requirements is of utmost importance.
Well said, Sophia! Compliance with ethical considerations, regulations, and standards is essential to build trust and ensure responsible use of AI and automation in manufacturing. Thank you for adding that point!
A user-friendly interface is crucial indeed, Lois. It not only enhances usability but also minimizes the learning curve for employees, ensuring an efficient and seamless interaction with ChatGPT.
Exactly, Sophia! Minimizing the learning curve and providing employees with an efficient tool for interaction enhances overall usability and adoption. It's an important aspect to consider during the implementation phase to ensure a positive user experience.
George, that's interesting! How long did the training period for ChatGPT take in your case? Did you face any challenges during that phase?
Emma, the training period took around three weeks. Initially, we faced challenges in fine-tuning the responses and maintaining accuracy. However, with continuous feedback and fine-tuning, we achieved the desired results. It's important to allocate enough time and resources during the training phase for optimal performance.
George, three weeks seems like a reasonable timeframe. How about the ongoing maintenance and updates? How frequently do you need to revisit and retrain ChatGPT to ensure it stays up to date with any process changes?
Oliver, maintaining ChatGPT is an ongoing process. We have a team dedicated to reviewing and updating the system periodically, especially when there are process changes or new product introductions. Continuous monitoring and regular updates are essential to keep the responses accurate and relevant, ensuring ChatGPT stays aligned with our current processes.
George, did you face any resistance or skepticism from the employees during the implementation of ChatGPT? If so, how did you address their concerns and ensure a smooth transition?
Olivia, there was indeed some initial hesitation among employees. Communication played a vital role in addressing their concerns. We organized training sessions to demonstrate how ChatGPT would assist them in their daily tasks rather than replace them. Involving employees in the implementation process and addressing their queries helped create a sense of ownership and ensured a smooth transition.
George, involving employees and addressing their concerns through training and communication is a great approach. It fosters a sense of collaboration and ownership, making them feel more comfortable with the new technology. Creating a positive attitude towards automation is crucial for successful implementation.
Absolutely, Emma. Employees are a valuable asset, and their involvement and support are vital for successfully integrating new technologies in the workplace. By fostering a positive attitude and addressing their concerns, we can create an environment where automation and AI are seen as tools that augment their capabilities.
I completely agree, George. Employing a collaborative approach and involving employees from the early stages of implementation fosters a sense of shared purpose and helps overcome resistance. It facilitates a smoother integration of new technologies and creates a win-win situation for both the employees and the organization.
George, Sophia, and Emma, your points are well-put. Employees are more likely to embrace automation when they feel valued and understand the positive impact it can have on their work. Open communication, training, and involving them in decision-making processes can create a culture that embraces change rather than resisting it.
Absolutely, Liam. Building trust, transparency, and involving employees in the transformation process are crucial for successful implementation. When they see the benefits and feel valued, the transition becomes smoother, and they become advocates for the technology.
I have mixed feelings about this. While automation brings efficiency, doesn't it also lead to job losses? How do companies address the potential impact on the workforce?
You raise a valid concern, Liam. However, it's worth mentioning that automation often augments human capabilities instead of completely replacing them. While some low-skill jobs may be automated, new opportunities arise in managing and maintaining automation systems. It's important for businesses to find a balance and ensure a smooth transition while providing support for employees during such changes.
Absolutely, Michael. Automation can free up time and resources, allowing employees to focus on higher-value tasks that require human intelligence and creativity. The key lies in adapting and evolving skill sets to remain relevant in an increasingly automated world.
That's a valid concern, Liam. Automation can indeed disrupt job roles. However, it's important to note that it also creates new opportunities. Companies should focus on workforce reskilling and upskilling programs to ensure a smooth transition. The collaboration of AI and humans can yield even better results. What are your thoughts, Michael and Emily?
I agree, Sophia. Job roles may evolve, and the nature of work may change with automation, but it also leads to the emergence of new job prospects that require human skills like critical thinking, problem-solving, and creativity. It's crucial for companies to invest in retraining programs to equip employees with the skills needed to thrive in an automated environment.
Indeed, Sophia and Emily, upskilling programs are crucial. Companies should proactively invest in retraining and smooth career transitions to alleviate concerns and ensure a positive impact on the workforce. It's also important for employees to embrace lifelong learning and stay adaptable to changes in the workplace.
Lois, your article raises an interesting point about streamlining processes. However, I'm concerned about potential risks like system failures or malicious attacks. How can companies mitigate these risks when implementing AI and automation in manufacturing?
Valid concern, Ryan! Implementing AI and automation indeed brings certain risks. To mitigate system failures, redundancy and fail-safe mechanisms can be employed. Regarding security, it's crucial to follow best practices like regular updates, data encryption, and strong access controls. Collaborating with experts in AI and cybersecurity can help companies understand and address these risks effectively.
Ryan, you bring up an important consideration. Companies should also conduct regular risk assessments and robust testing of AI systems to identify vulnerabilities and ensure their resilience to attacks. It's a constantly evolving field, and staying updated with security measures is crucial.
Absolutely, Jackson! Continuous evaluation, testing, and staying updated with evolving security measures are vital to ensure the safety and integrity of AI systems in manufacturing. Thank you for adding that point!
Jackson, you're absolutely right. Regular risk assessments are crucial for identifying potential vulnerabilities and taking proactive measures to address them. In an evolving technological landscape, staying vigilant is key to protect manufacturing systems from any security threats.
Indeed, Jackson and Emily. Manufacturing companies should establish strong cybersecurity practices and ensure that risk assessments are conducted periodically. This will help in identifying vulnerabilities and implementing necessary measures to safeguard critical infrastructure from potential attacks.
Ryan, as companies adopt AI and automation, it's vital to have strong backup systems in place to mitigate the risk of system failures. Redundancy measures and proper disaster recovery planning can help minimize downtime and ensure continuity in manufacturing operations.
Oliver, you're absolutely right. Redundancy measures and robust disaster recovery planning are crucial to minimize the impact of system failures. It's essential to have backup systems, resilient infrastructure, and proper contingency plans to ensure smooth manufacturing operations, especially in critical environments.
Great point, Oliver and Ryan! Having backup systems, redundancy measures, and well-defined disaster recovery plans are essential to ensure uninterrupted operations and minimize the negative impact of system failures. Thank you for highlighting that aspect!
Lois, your article was such an insightful read! It's incredible how automation in manufacturing has evolved with AI-powered chatbots like ChatGPT. I'd love to know more about the potential future developments in this field and how it can further optimize the manufacturing processes.
Thank you, David! I'm glad you found the article insightful. Future developments in AI and automation hold immense potential for further optimizing manufacturing processes. Increased personalization, predictive maintenance, and enhanced supply chain management are some areas that have promising prospects. I'll be covering these in detail in my future articles. Stay tuned!
Lois, can you elaborate on the implementation process of ChatGPT in manufacturing? Are there any specific requirements or infrastructure changes that companies need to consider?
Certainly, Emma! Implementing ChatGPT in manufacturing requires a few considerations. Companies should ensure they have a secure and reliable IT infrastructure to support the chatbot. Additionally, the availability of well-labeled training data, domain expertise, and a clear understanding of the manufacturing processes are important requirements. Infrastructure changes may vary depending on the specific implementation, but having a robust IT foundation is crucial for a smooth integration.