Transforming Tolerance Analysis in Mechanical Product Design: Exploring the Power of ChatGPT
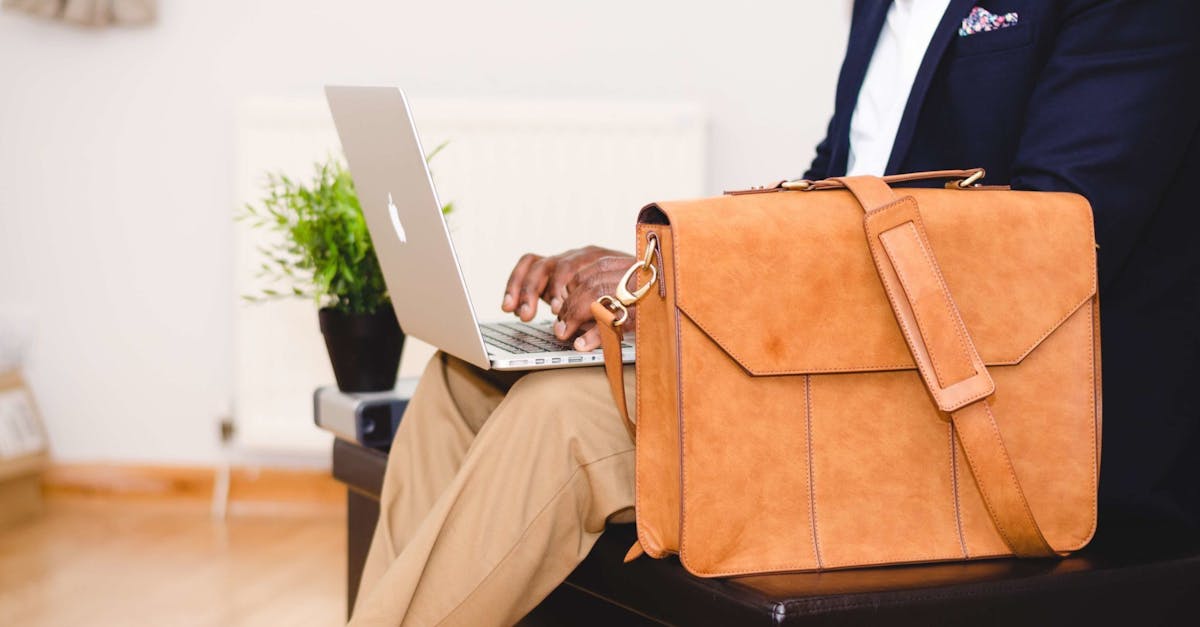
When it comes to mechanical product design, ensuring precise and accurate dimensions is crucial. This is where tolerance analysis plays a vital role in determining the permissible variations in dimensions and characteristics of a product. Tolerance analysis involves analyzing and providing advice on the tolerance aspects of a mechanical design to achieve maximum functionality and performance.
What is Tolerance Analysis?
Tolerance analysis refers to the process of evaluating and determining the acceptable range of variations in dimensions and geometrical features of a mechanical product. It involves assessing the impact of these variations on the product's functionality, manufacturability, and overall performance. Tolerance analysis helps designers understand how variations in dimensions can affect the function and overall quality of the product.
Importance of Tolerance Analysis
Tolerance analysis is crucial for several reasons:
- Functionality: Tolerances directly impact the functionality of a mechanical product. Understanding the permissible variations in dimensions and features helps ensure that the product functions as intended.
- Manufacturability: Tolerance analysis helps in determining the manufacturing process and feasibility of producing the part within the required tolerances. It aids in identifying potential manufacturing constraints and helps optimize the production process.
- Performance: Precise tolerances lead to improved performance and increased product lifespan. Tolerance analysis ensures that the product meets the required performance standards and expectations.
- Cost Optimization: Proper tolerance analysis helps reduce manufacturing costs by identifying areas where tolerances can be relaxed without compromising functionality or performance.
Tolerance Analysis Techniques
Tolerance analysis involves various techniques and methods to evaluate and quantify the impact of variations. Some commonly used techniques include:
- Statistical Analysis: Statistical analysis involves using statistical methods to assess the impact of variability on the overall performance of a mechanical product. It helps identify the probability of failures and deviations from desired specifications.
- Stack-Up Analysis: Stack-up analysis is a widely used technique that evaluates the accumulation of tolerances in an assembly. It helps in understanding the worst-case scenario and determining the impact on the final product's dimensions and fit.
- Monte Carlo Simulation: Monte Carlo simulation involves generating random samples within specified tolerances and evaluating their impact on the performance. It helps in identifying the range of possible outcomes and assessing the risk of failure.
Best Practices for Tolerance Analysis
To ensure accurate and effective tolerance analysis, consider the following best practices:
- Collaboration: Involve all relevant stakeholders, including design engineers, manufacturing experts, and quality control professionals, in the tolerance analysis process. Effective collaboration leads to better decision-making and improved outcomes.
- Early Analysis: Perform tolerance analysis as early as possible in the design process to identify potential issues and make necessary adjustments before the product reaches the manufacturing stage.
- Consider Design for Manufacturing (DFM) Principles: Design products with manufacturability in mind. Consider the capabilities and limitations of the manufacturing process and incorporate necessary design changes to achieve desired tolerances.
- Verification and Validation: Validate the tolerance analysis results through physical testing or simulation to ensure that the product meets the required specifications and performance standards.
- Continuous Improvement: Incorporate feedback and lessons learned from previous projects to continually improve tolerance analysis processes and outcomes.
Conclusion
Tolerance analysis is an integral aspect of mechanical product design. Accurate and effective tolerance analysis ensures that a product functions as intended, is manufacturable, and performs optimally. By utilizing various techniques and following best practices, engineers can mitigate potential risks, optimize costs, and deliver high-quality products that meet the expectations of stakeholders.
Incorporating tolerance analysis in the design process is essential for achieving precision and accuracy in mechanical product design, ultimately leading to improved functionality and customer satisfaction.
Comments:
Thank you all for your comments! I appreciate your engagement with the article.
I found the article quite informative. ChatGPT could definitely enhance tolerance analysis in mechanical product design. It could streamline the process and improve efficiency.
Absolutely, Abigail! The power of AI technologies like ChatGPT lies in their ability to automate complex tasks and provide valuable insights. It's exciting to witness their potential in mechanical product design.
While I see the potential benefits, I'm concerned about the accuracy of ChatGPT. How reliable is it in providing accurate tolerance analysis?
Liam, that's a valid concern. The accuracy of AI models like ChatGPT depends on the quality and quantity of data they are trained on. It's crucial to have a robust dataset for reliable results.
Exactly, Sophia. Training AI models on a diverse range of mechanical products and their corresponding tolerance analysis data can help improve accuracy. It's an ongoing challenge, but with proper training, we can overcome it.
Do you think incorporating ChatGPT into mechanical product design will reduce the need for human expertise?
Ethan, I believe AI can augment human expertise, but it won't replace it entirely. While ChatGPT can automate certain tasks, human engineers will still be needed to interpret and apply the generated analysis.
Well said, Olivia. AI is a powerful tool that can assist engineers, but their domain knowledge and expertise will always be essential in the design process.
I worry that relying too much on AI could reduce creativity and innovation in mechanical product design. How do we strike the right balance?
Evelyn, striking the right balance is indeed crucial. AI should be seen as a tool to enhance creativity and innovation, rather than replacing human input. Engineers can use ChatGPT's insights as a starting point, allowing them to explore new ideas and push the boundaries of design.
I'm curious about the computational resources required to implement ChatGPT in tolerance analysis. Are there any limitations or potential challenges?
That's a good point, Thomas. AI models like ChatGPT can be computationally demanding. It's essential to assess the hardware and resources required to ensure efficient implementation.
Indeed, Liam. Implementing AI in real-world applications often requires careful consideration of computational resources, such as processing power, memory, and scalability. However, with advancements in technology, these challenges can be managed effectively.
I'm concerned about the potential biases in AI models like ChatGPT. How can we ensure fairness and avoid perpetuating any existing biases in tolerance analysis?
Great question, Natalie. Bias mitigation in AI models is crucial. Proper data preprocessing, diverse training datasets, and ongoing evaluation can help in identifying and addressing biases.
Absolutely, Sophia. Ensuring fairness in AI models is a priority. Regular monitoring and auditing can help identify and rectify any biases, while continual improvement in training practices can lead to more unbiased analysis.
The potential of ChatGPT in transforming tolerance analysis is fascinating. It opens up new possibilities and can save valuable time in the design process.
Indeed, David. The time-saving aspect is one of the significant advantages of AI applications like ChatGPT. It enables engineers to focus more on other critical aspects of product design and innovation.
I believe incorporating AI into tolerance analysis will require engineers to upskill and adapt to new technologies. How can companies facilitate this transition?
Chloe, you're right. Companies can arrange training programs and workshops to help engineers upskill in AI technologies. Collaboration with experts and encouraging a learning culture can also ensure a smooth transition.
Absolutely, Olivia. Companies play a crucial role in supporting engineers during this transition. Providing the necessary resources, training opportunities, and fostering a culture of continuous learning will help engineers embrace AI in their work.
What potential challenges might arise when implementing ChatGPT in tolerance analysis? Are there any specific drawbacks we should consider?
That's an important question, Michael. One drawback could be overreliance on AI-generated analysis without proper validation, leading to potential errors. It's crucial to have a balance between human expertise and AI insights.
Well said, Evelyn. Validating AI-generated analysis and cross-referencing it with domain knowledge is essential to avoid any misleading or erroneous results.
I'm excited about the possibilities AI brings to tolerance analysis. It can revolutionize product design and improve overall quality.
I share your excitement, Isabella. AI has the potential to transform various industries, including mechanical product design. It's an exciting time to be at the forefront of this technological advancement.
What industries other than mechanical product design can benefit from AI-powered tolerance analysis?
Andrew, AI-powered tolerance analysis can be beneficial in industries like automotive manufacturing, aerospace, consumer electronics, and even medical device manufacturing. Any industry that involves intricate mechanical designs can benefit from it.
Exactly, Sophia. AI-powered tolerance analysis can have widespread applications across industries, where precision and reliability of mechanical designs are paramount.
How can we address the skepticism around AI in mechanical product design, especially regarding its ability to replace human engineers in the long run?
Jessica, it's essential to foster open communication and education about AI's role in mechanical product design. Highlighting the collaboration between AI and human engineers, and emphasizing the value it adds rather than focusing on replacement can help alleviate skepticism.
Well put, Olivia. Demonstrating how AI tools like ChatGPT can enhance engineering capabilities and positively impact product design can address the skepticism and establish trust in the technology.
I'm impressed with the potential of ChatGPT. The ability to simulate different scenarios and analyze tolerances in real-time can be a game-changer for engineers.
Indeed, Daniel. Real-time analysis and simulation capabilities can significantly accelerate the mechanical design process and allow engineers to make timely decisions based on accurate insights.
In the future, do you think AI models like ChatGPT will become even more advanced and outperform traditional tolerance analysis techniques?
Sophia, AI is continually advancing, and it's likely that future AI models will become more advanced. However, it's important to remember that AI should complement and enhance existing techniques rather than render them obsolete.
Well said, Evelyn. AI should be seen as a tool to augment human expertise, providing valuable insights and efficiency gains, but not as a replacement for traditional analysis techniques.
With the potential benefits of ChatGPT, what are the main barriers to its widespread adoption in the industry?
Liam, widespread adoption faces challenges such as maintaining data privacy, addressing security concerns, ensuring reliability, and standardizing the integration of AI tools. Overcoming these barriers will be key to realizing the full potential of ChatGPT in the industry.
Spot on, Olivia. Addressing these challenges requires collaborative efforts between AI developers, industry professionals, and policymakers to establish robust frameworks for the safe and efficient adoption of AI in mechanical product design.
I'm curious about the scalability of ChatGPT. Can it handle large-scale tolerance analysis projects efficiently?
Michael, achieving scalability can be a challenge, but with proper architectural design and optimizations, ChatGPT can handle large-scale projects. Continuous research and development in AI infrastructure are crucial in this regard.
Absolutely, Chloe. Scalability is a priority, and as the demand for AI-powered tolerance analysis grows, advancements in hardware and algorithms will ensure efficient handling of large-scale projects.
Are there any ethical considerations we need to keep in mind while integrating AI like ChatGPT into mechanical product design?
Ethical considerations are indeed crucial, Jessica. Transparency, accountability, and ensuring the responsible use of AI are paramount. We must avoid bias and ensure the generated analyses align with ethical standards.
Well said, Sophia. Ethical considerations should be at the forefront of AI integration. Adhering to ethical guidelines and ongoing evaluation can help us mitigate risks and ensure AI is used as a force for good in mechanical product design.
The potential collaboration between ChatGPT and human engineers is exciting. It can lead to innovative solutions and push the boundaries of mechanical product design.
Indeed, Daniel. When AI and human expertise converge, remarkable advancements become possible. The collaboration between ChatGPT and engineers can unlock new dimensions of creativity and efficiency in mechanical product design.
I can't wait to see ChatGPT and similar AI technologies being implemented in mechanical product design. It's an exciting time for innovation!