Unlocking Standard Compliance: Leveraging ChatGPT for GD&T Technology
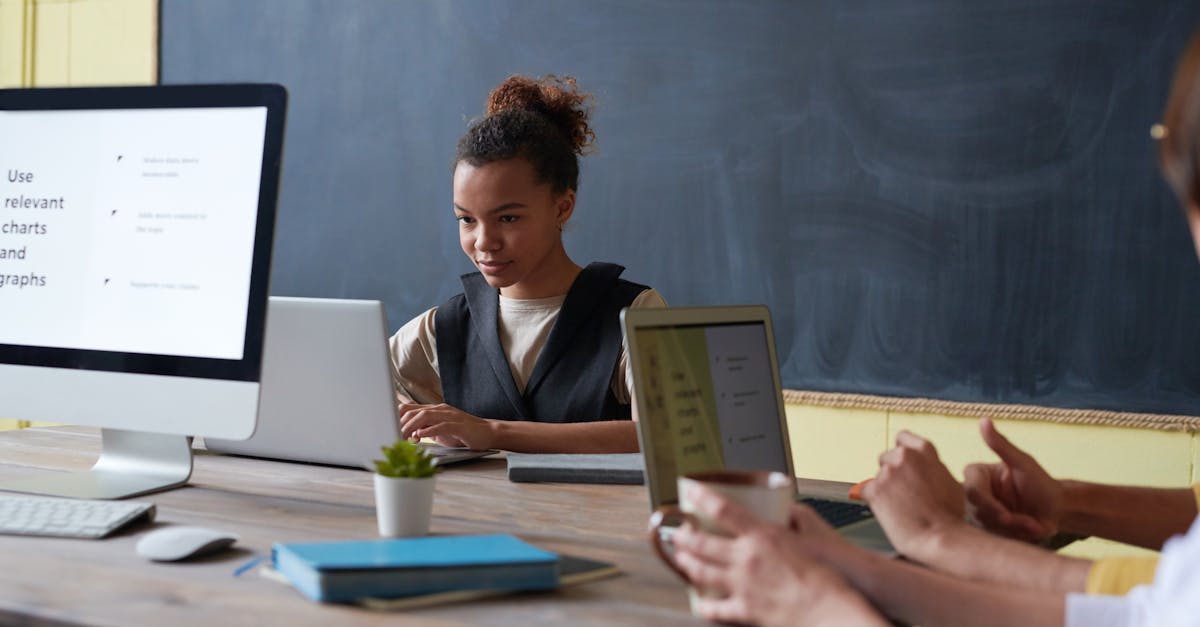
In the field of engineering and manufacturing, Geometric Dimensioning and Tolerancing (GD&T) plays a crucial role in ensuring the accuracy and interchangeability of parts and components. GD&T is a symbolic language used to communicate design intent and define the allowable variation in form, size, orientation, and location of features on a part or assembly. It provides a precise and clear set of rules that helps in achieving the desired functionality and quality while also enhancing manufacturing efficiency.
What is GD&T Standard Compliance?
GD&T Standard Compliance refers to the assessment of a design's adherence to the GD&T standards established by the American Society of Mechanical Engineers (ASME). Compliance with these standards ensures that the design is within the specified limits and meets the required functional requirements. It involves verifying the dimensional, form, and geometric requirements of a part or assembly based on the GD&T symbols, datums, and tolerances specified in the engineering drawings.
Importance of GD&T Standard Compliance
GD&T Standard Compliance is crucial in various stages of the product development process. Here are some key reasons why it is important:
- Quality Assurance: Verifying compliance with GD&T standards ensures that the design meets the required quality standards. It helps in identifying and rectifying any potential manufacturing or functionality issues early in the design phase, reducing the risk of errors and costly rework.
- Interchangeability: GD&T ensures that parts and components are interchangeable, enabling easy assembly and maintenance. By complying with GD&T standards, manufacturers can ensure that the produced parts will fit and function correctly, regardless of the supplier.
- Clear Communication: GD&T provides a consistent language and set of symbols to communicate design requirements and specifications. Compliance with the standards ensures that all stakeholders, including designers, engineers, and manufacturers, have a common understanding of the design intent, reducing misunderstandings and improving collaboration.
- Cost Reduction: By adhering to GD&T standards, manufacturers can optimize the production process and reduce waste. The precise specifications provided by GD&T help in determining the most efficient manufacturing methods, reducing material waste, and minimizing the need for rework or corrective actions.
Usage of GD&T Standard Compliance
The usage of GD&T Standard Compliance is diverse and applicable across various industries, including automotive, aerospace, electronics, and more. Here are some common areas of usage:
- Part and Assembly Inspection: GD&T compliance allows manufacturers to conduct accurate and consistent inspections of parts and assemblies. By using GD&T measurement tools such as coordinate measuring machines (CMMs) and other inspection equipment, manufacturers can check if the produced parts conform to the specified tolerances and dimensions.
- Design Verification: GD&T compliance assists in verifying if a design meets the intended functional requirements. By applying GD&T principles during the design phase, engineers can ensure that the parts will fit together correctly, align properly, and perform their intended function without any interference or excessive variation.
- Supplier Evaluation: GD&T compliance is often used in evaluating potential suppliers. By assessing the supplier's ability to adhere to GD&T standards, manufacturers can determine the supplier's capability of delivering parts and components that meet the required specifications, ensuring consistent product quality.
- Tolerance Analysis: GD&T compliance aids in performing tolerance analysis to ensure that the design can be manufactured within acceptable limits. By analyzing geometric relationships and tolerance stack-ups, engineers can identify potential manufacturing issues and make necessary design modifications to achieve the desired functionality while still adhering to the GD&T standards.
Conclusion
GD&T Standard Compliance is essential in the field of engineering and manufacturing to ensure the accuracy, interchangeability, and quality of parts and assemblies. By adhering to the GD&T standards, manufacturers can achieve cost-effective production, improve product functionality, and enhance overall manufacturing efficiency. Proper usage of GD&T compliance tools and techniques enables effective design verification, part inspection, supplier evaluation, and tolerance analysis, contributing to the success of the product development process.
Comments:
Thank you all for taking the time to read my article on leveraging ChatGPT for GD&T technology. I hope you found it informative and insightful. I look forward to hearing your thoughts and comments!
Great article, Aditi! It's fascinating to see how AI can be harnessed to improve GD&T technology. I particularly liked your discussion on the potential applications in automation. Well done!
Aditi, your article was well-written and provided a comprehensive overview of the topic. It's evident that ChatGPT has significant potential in enhancing standard compliance. Looking forward to seeing further advancements in this field!
Thanks for sharing your insights, Aditi. I found your explanation of GD&T and its significance very helpful. This article has certainly increased my understanding of the relationship between ChatGPT and standard compliance. Keep up the great work!
Aditi, your article raised some interesting points. As someone working in the manufacturing industry, I can see the potential benefits of integrating ChatGPT with GD&T technology. However, I am curious about the challenges that might arise during implementation. Can you shed some light on that?
Thank you, Linda. Implementation challenges can include limitations in the AI model's comprehension of contextual diversity, potential biases, and the need for data pre-processing. However, continual improvements in training methodologies and feedback loops can help overcome these challenges.
Aditi, your article was enlightening. I'm curious about the potential impact ChatGPT can have on reducing human errors in GD&T analysis. Any thoughts on this?
Thank you, Ryan. ChatGPT's ability to assist in GD&T analysis has the potential to reduce human errors by providing real-time expertise, aiding in quick decision-making, and minimizing ambiguities. However, human oversight is still crucial in ensuring accurate results.
Aditi, your article was well-researched, and the examples you provided were quite helpful. I appreciate how you explained the practical applications of ChatGPT in the context of GD&T technology. Keep up the good work!
Aditi, I found your article intriguing. Can you elaborate on the potential limitations or risks associated with relying heavily on AI-enabled technologies like ChatGPT for GD&T compliance?
Certainly, Robert. While AI technologies offer significant benefits, potential limitations may involve biases in training data, AI model interpretability, and the risk of over-reliance leading to complacency in quality control. It's important to strike a balance between AI-assistance and human expertise.
Kudos, Aditi, on a well-written article! ChatGPT's integration with GD&T technology opens up exciting possibilities. Do you foresee any ethical considerations arising from this combination?
Thank you, Emma. Ethical considerations can arise, such as the responsible use of AI, privacy concerns, and potential impacts on employment. Ensuring transparency, accountability, and incorporating ethical frameworks into AI development can help address these concerns.
Aditi, your article was incredibly informative. I'm curious about the scalability of ChatGPT in GD&T technology. Are there any limitations to its application on a larger scale?
Thank you, Kate. While ChatGPT demonstrates impressive capabilities, scaling it on a larger system scale might face challenges such as computational resources, speed, and maintaining consistency. Advances in hardware and optimized algorithms are key to overcome these limitations.
Aditi, your article provided a fresh perspective on integrating AI with GD&T technology. I appreciate the effort you put into explaining the potential benefits. Well done!
Aditi, your article was both insightful and accessible. I found your analysis of the impact of ChatGPT on standard compliance very interesting. Keep up the excellent work!
Great write-up, Aditi! Your article shed light on the potentials of ChatGPT in GD&T technology. It's exciting to see AI advancements improving standard compliance. Kudos!
Aditi, I thoroughly enjoyed reading your article. It was concise yet informative. Is ChatGPT widely accessible, or are there specific requirements for utilizing it in the field of GD&T technology?
Thank you, Olivia. ChatGPT is becoming increasingly accessible, but its effectiveness in the field of GD&T technology depends on suitable training data, fine-tuning, and domain-specific requirements. Collaborative efforts between AI researchers and industry experts are crucial for optimal utilization.
Aditi, your article was thought-provoking. I'm intrigued by the potential impact of ChatGPT on reducing errors while interpreting GD&T requirements. Can you provide some examples or case studies?
Thank you, Jack. ChatGPT can help reduce errors in interpreting GD&T requirements by providing context-aware suggestions and assisting in real-time analysis. While I don't have specific case studies to share, empirical evaluations have demonstrated promising results, but more research and case studies are required for a comprehensive understanding.
Aditi, your article was engaging and informative. The potential implications of ChatGPT in GD&T technology are intriguing. I wonder if there are any notable challenges specific to GD&T that need to be addressed?
Thank you, Emily. Some notable challenges in GD&T involve its complex nature, tolerance interpretations, and variations across industries. ChatGPT can aid in addressing these challenges but may require targeted training and customization for domain-specific intricacies.
Aditi, your article was insightful and well-structured. I appreciate your thorough exploration of ChatGPT's potential in GD&T technology. Well done!
Aditi, your article provided a compelling overview of the ChatGPT integration with GD&T technology. It's exciting to see how AI can enhance standard compliance. I enjoyed reading it!
Aditi, thank you for sharing your expertise in this article. I'm curious about the data requirements for training ChatGPT to understand GD&T rules accurately. Could you elaborate on that?
Thank you, Luke. Training ChatGPT with GD&T rules relies on a diverse dataset comprising annotated examples, industry-specific use cases, and complying with relevant standards. The quality and comprehensiveness of the training data play a crucial role in achieving accurate understanding and responses.
Aditi, your article was fascinating. Can you provide some insights into the potential impact of ChatGPT on the GD&T certification process?
Thank you, Sophie. ChatGPT can potentially impact the GD&T certification process by providing real-time guidance, assisting in training modules, and reducing ambiguity in interpretations. However, human expertise and evaluation are still essential components of the certification process to ensure thorough understanding and compliance.
Aditi, your article was well-structured and informative. I'm curious about the potential risks associated with relying on ChatGPT for GD&T technology. Could you shed some light on that?
Certainly, Brandon. Risks of relying heavily on ChatGPT for GD&T technology relate to understanding subtle nuances, potential biases in predictive capabilities, and over-reliance on outcomes without human verification. Cautious validation and a collaborative approach can mitigate these risks.
Aditi, your article provided valuable insights into the integration of GD&T technology with ChatGPT. I'm curious if there are any potential limitations to ChatGPT's contextual understanding in this context?
Thank you, Emma. ChatGPT's contextual understanding has certain limitations, such as occasional incorrect responses, sensitivity to phrasing, and challenges in handling ambiguous or highly technical GD&T queries. Regular model updates and iterative improvements in training approaches can contribute to enhancing its contextual understanding.
Aditi, your article was thought-provoking. I wonder how enterprises can effectively integrate ChatGPT with existing GD&T workflows. Any suggestions?
Thank you, Nathan. Integrating ChatGPT with existing GD&T workflows requires identifying pain points, collaboration between AI developers and industry experts, comprehensive testing, and gradual integration to ensure compatibility and user acceptance. Iterative adoption with continuous feedback and improvement loops is key.
Aditi, your article was excellent! It's intriguing to consider the potential implications of integrating AI like ChatGPT into GD&T technology. Looking forward to witnessing its evolution!
Aditi, your article provided a clear understanding of the potential benefits of ChatGPT in GD&T technology. It's impressive to see how AI advancements can streamline standard compliance. Well done!
Aditi, your article was engaging and well-researched. I'm curious about the future implications of ChatGPT for GD&T technology. Any predictions?
Thank you, Daniel. Looking ahead, ChatGPT's integration with GD&T technology has immense potential for further empowering engineers, streamlining compliance, and enabling real-time decision-making. It can contribute to enhanced productivity, accuracy, and knowledge dissemination in the field.