Utilizing ChatGPT for Enhanced Efficiency in Manufacturing Employee Scheduling
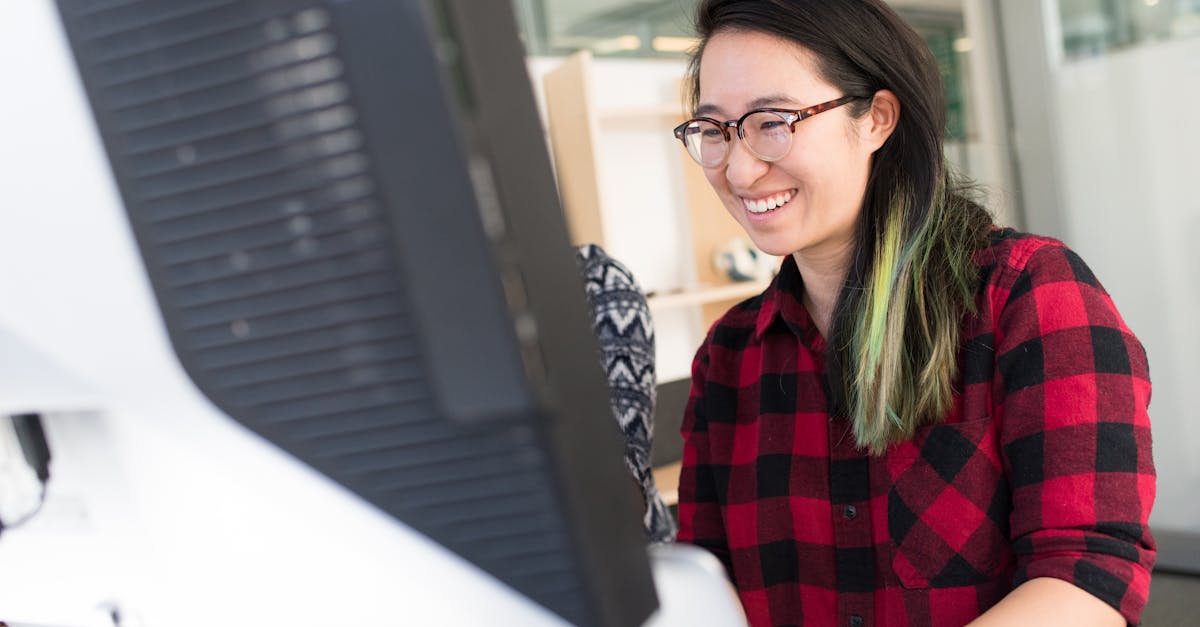
Introduction
In the manufacturing industry, efficient employee scheduling is critical for optimizing productivity and ensuring optimal utilization of resources. Manual scheduling can be time-consuming and prone to errors, leading to inefficiencies and increased labor costs. However, with the advent of technology, automated employee scheduling systems have emerged as a powerful tool for manufacturing companies.
Technology
The technology used in employee scheduling systems for manufacturing is a combination of advanced algorithms and computer software. These systems take into account various factors such as workload, employee availability, and skills required for different tasks.
Area of Application
The area of application for employee scheduling in manufacturing is vast. It can be applied to different types of manufacturing facilities, including plants, factories, and warehouses. Regardless of the scale of the operation, employee scheduling technology ensures that the right employees are assigned to the right tasks at the right time.
Benefits of Employee Scheduling in Manufacturing
Employee scheduling systems offer several benefits for manufacturing companies:
- Efficient Resource Allocation: By analyzing the workload and employee availability, scheduling systems help manufacturers allocate human resources more efficiently. This prevents understaffing or overstaffing situations, enabling optimal utilization of labor.
- Improved Productivity: With accurate scheduling, employees can plan their workday effectively and focus on their assigned tasks without wasted downtime. This leads to increased productivity and streamlined operations.
- Reduced Labor Costs: Automated scheduling systems can help manufacturers avoid costly overtime by ensuring that shifts are adequately covered, and workload is distributed evenly among employees.
- Enhanced Learning and Development: Employee scheduling systems can take into account employee skills and qualifications when assigning tasks. This allows manufacturers to identify areas for training and development, leading to a more skilled workforce.
Challenges in Employee Scheduling
While employee scheduling technology offers significant advantages, there are certain challenges to overcome:
- Complexity: Manufacturing operations often involve intricate workflows and varying job requirements. Designing scheduling algorithms capable of handling this complexity can be a challenge.
- Unpredictability: Manufacturing schedules are influenced by factors such as customer demands, equipment breakdowns, and unexpected events. Scheduling systems need to be flexible and adaptive to accommodate these changes seamlessly.
- Employee Preferences: Considerations must be given to employee preferences, such as shift preferences, time-off requests, and personal constraints. Balancing these preferences with operational needs can be tricky.
- Integration: Implementing employee scheduling systems involves integration with other manufacturing software, such as ERP systems, time tracking systems, and payroll management. Proper integration is crucial for smooth operations.
Conclusion
Employee scheduling technology is a valuable tool for manufacturing companies aiming to optimize productivity and reduce labor costs. By automating the scheduling process, manufacturers can ensure efficient resource allocation, improved productivity, and enhanced employee development. While challenges exist, advancements in technology continue to make employee scheduling in manufacturing more effective and easier to manage.
Comments:
Thank you all for your valuable comments! I appreciate your participation in this discussion.
This article highlights an important use case for ChatGPT in manufacturing. Employee scheduling can be a complex task, and if ChatGPT can enhance efficiency, it's definitely worth exploring.
I agree with Tony. Employee scheduling is often a time-consuming process, so any technology that can streamline it is a great help.
Has anyone here actually tried using ChatGPT for employee scheduling? I'm curious to hear about real-world experiences.
I haven't personally used ChatGPT for scheduling, but I've heard positive feedback from colleagues who have. It has helped them automate certain aspects and reduce errors in the process.
I think it's important to consider data privacy and security when using ChatGPT for employee scheduling. How are the confidential employee details handled?
Great point, Daniel! Ensuring data privacy and security is paramount. In the case of ChatGPT, it's crucial to implement appropriate access controls and encryption to protect sensitive information.
I work in manufacturing, and I can see the potential of ChatGPT for scheduling. Being able to get quick suggestions and automated reminders could significantly improve efficiency.
But wouldn't relying too much on ChatGPT for scheduling take away the human touch? I value the personal element in managing employee schedules.
I understand your concern, Alex. While ChatGPT can assist in scheduling, it should never replace the role of a human manager. It can serve as a tool to make the process more efficient and accurate.
I agree with Tony. The human touch is essential, but technology can serve as a valuable aid. It can handle the repetitive tasks, allowing managers to focus on more strategic aspects of scheduling.
That makes sense, Tony and Sarah. It's all about finding the right balance between automation and human involvement.
Finding that balance is indeed crucial. ChatGPT can be a useful tool to support managers, but it should never replace their decision-making abilities.
Another concern I have is the potential bias in the scheduling recommendations provided by ChatGPT. How can we ensure fairness in the process?
Valid point, Daniel. Bias in AI systems is a significant concern. To ensure fairness, it's crucial to train ChatGPT on diverse datasets and continuously evaluate its performance to address any biases that may arise.
I think it's important for organizations to have clear guidelines and policies in place when using ChatGPT for scheduling. This can help mitigate the risk of bias and ensure fairness.
Absolutely, Robert! Transparent guidelines and accountability are essential in leveraging technology like ChatGPT effectively.
I wonder how ChatGPT compares to other scheduling software available in the market. Are there any specific advantages it offers?
From what I've read, ChatGPT offers more natural language processing capabilities, which could make it easier and more intuitive for non-technical users to interact with the system.
That's interesting, Sarah! User-friendly interfaces can make a big difference in the adoption of such tools, especially for managers who may not be familiar with technical jargon.
One advantage I see with ChatGPT is its ability to learn from user interactions. Over time, it can improve its responses and suggestions based on the feedback it receives.
Indeed, Tony! Adaptive learning is a powerful feature of ChatGPT. It can continuously enhance its capabilities and become more tailored to specific user needs.
Considering the variability and unpredictability in manufacturing, how well does ChatGPT handle unexpected scheduling changes and adapt to new situations?
That's an excellent question, Daniel. While ChatGPT can provide assistance, its performance may be limited in highly dynamic situations. Human intervention may still be required to handle unexpected changes.
I think ChatGPT can be a great asset for handling routine scheduling tasks, but having human managers with the ability to handle unexpected situations is crucial.
Agreed, Sarah. Technology should complement human decision-making rather than replace it entirely.
I have a question for Lois, the article's author. Are there any case studies or real-world examples of companies successfully implementing ChatGPT for scheduling?
Good question, Robert! While I couldn't find specific case studies during my research, there are anecdotal reports of companies in manufacturing leveraging ChatGPT for more efficient scheduling. However, further research and documentation would be beneficial to gain deeper insights.
I appreciate the honest response, Lois. Real-world case studies would indeed provide valuable insights and help understand the potential benefits and challenges.
It would be interesting to hear about the scalability of ChatGPT for large manufacturing organizations. Are there any limitations to consider?
Scalability is a valid concern, Tony. While ChatGPT can be a valuable solution for employee scheduling, larger organizations might require more advanced and specialized systems to handle their complex needs. It's important to evaluate the specific requirements before adopting ChatGPT.
I'm concerned about potential biases in the training data of ChatGPT. How can organizations ensure they don't inadvertently reinforce existing biases in their scheduling processes?
Addressing biases is crucial, Daniel. Organizations should carefully curate and diversify their training data to avoid reinforcing existing biases. Regular audits and evaluations can help identify and rectify any biases that may surface.
I think fostering diversity and inclusivity within the organization is also important. By having diverse perspectives involved in the scheduling process, we can mitigate biases and ensure fairness.
Absolutely, Emily. A diverse workforce can help identify and challenge biases, creating more equitable scheduling practices.
Considering the potential benefits of ChatGPT for scheduling, I believe proper training and education on its use is crucial. Managers need to understand its limitations and how to best utilize its capabilities.
I agree, Tony. It's important to approach technology like ChatGPT with a mindset of continuous learning and improvement.
ChatGPT sounds promising for employee scheduling, but it's essential to also consider the costs associated with implementing and maintaining it. ROI calculations and long-term benefits must be evaluated.
You're absolutely right, Karen. Conducting a thorough cost-benefit analysis is crucial before integrating any new technology, ChatGPT included.
I think it's wonderful that we're discussing these potential applications of AI in manufacturing. It shows how technology continues to evolve and impact various industries.
Indeed, Sarah! The advancements in AI and machine learning offer exciting possibilities for improving efficiency and productivity in manufacturing.
While there may be challenges and considerations surrounding the use of ChatGPT for scheduling, it's encouraging to see the potential positive impacts it can have on manufacturing operations.
I agree, Daniel. It's always important to evaluate the pros and cons, but the potential benefits of leveraging AI in manufacturing should not be overlooked.
The technology landscape is constantly evolving, and it's crucial for organizations to stay informed and adapt to keep up with the changing times.
Absolutely, Tony! Continuous learning and adaptation are key to embracing the benefits that technology like ChatGPT can bring to manufacturing.
Thank you, Lois, for sharing this informative article and engaging with us in this discussion. It has been enlightening to hear different perspectives on the topic.
Yes, thank you, Lois. I appreciate your active participation. This conversation has given me a lot to think about regarding the potential of ChatGPT in employee scheduling.
Thank you, Lois, and thank you all for your insightful comments. It's been a great exchange of ideas.
Indeed, thank you, Lois, and everyone involved in this conversation. It's been a pleasure discussing this topic.
Thank you, Lois, for initiating this discussion. It's evident that ChatGPT has captured the interest and curiosity of many in the manufacturing field.