Enhancing Mechanical Product Design through ChatGPT: Exploring Fluid Dynamics Simulation and Analysis Capabilities
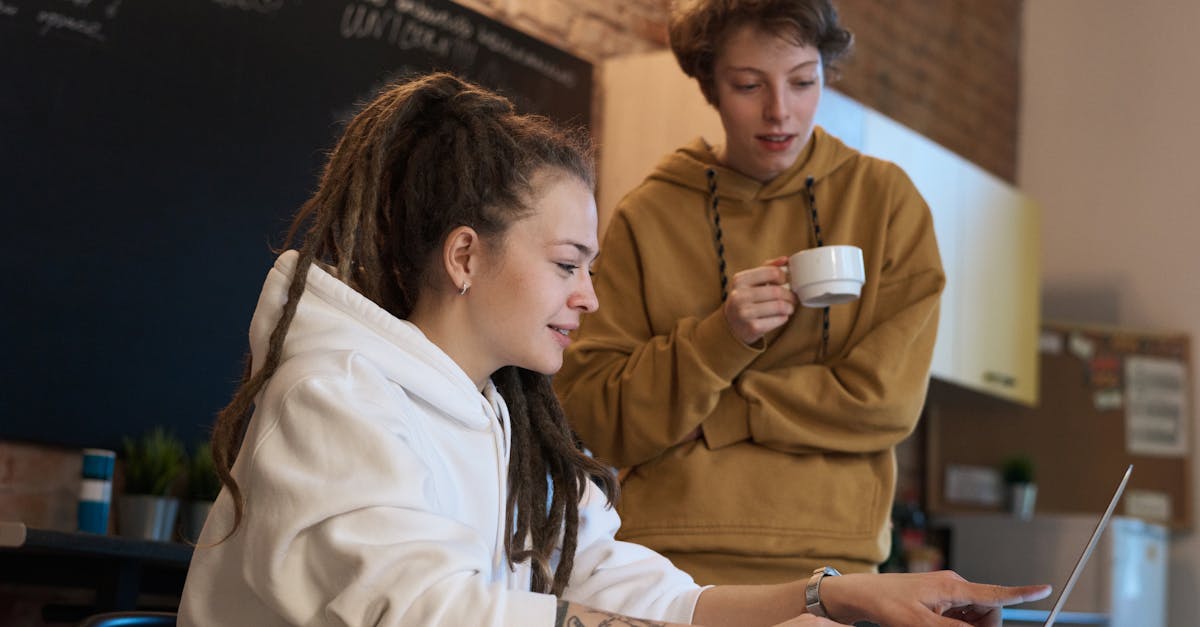
Fluid dynamics is a branch of physics that deals with the mechanics of fluids, including liquids, gases, and plasmas. It explores the behavior of fluids when subjected to different forces and flows. Mechanical product design in fluid dynamics involves the application of this science in designing products that interact with fluid flows. These products can range from simple pipes and pumps to complex aerodynamic systems.
One key aspect of mechanical product design in fluid dynamics is the use of simulations and analysis to understand how fluid flows interact with the design. Designers utilize various computational tools and software to simulate and analyze fluid behavior, allowing them to optimize the performance and efficiency of their designs.
Technology
In recent years, advancements in computer-aided design (CAD) software have revolutionized mechanical product design. CAD software enables designers to create detailed 3D models of their products and simulate fluid flow within the design. This technology allows engineers to visualize and analyze the complex behavior of fluid flow, providing valuable insights into the design's performance.
Computational fluid dynamics (CFD) is a specific area of technology widely used in mechanical product design. CFD software uses numerical methods and complex algorithms to solve and simulate fluid flow equations. These simulations provide designers with valuable information about the pressure distribution, flow velocity, temperature, and other critical parameters within the design.
Area: Fluid Dynamics
Fluid dynamics is a broad scientific field that explores the behavior of fluids in motion. It encompasses a wide range of phenomena, including laminar and turbulent flow, boundary layers, fluid viscosity, pressure distribution, and more. Understanding these concepts is crucial for mechanical product designers, as they must consider the fluid dynamics when designing products that interact with fluids.
Fluid dynamics plays a vital role in various industries, including aerospace, automotive, energy, and manufacturing. In the automotive industry, for example, understanding the flow of air around a vehicle can help designers optimize its aerodynamics, reducing drag and increasing fuel efficiency.
Usage: Simulation and Analysis
The primary usage of mechanical product design in fluid dynamics is to provide simulation and analysis capabilities. By simulating fluid flow within a design, engineers can understand how different factors affect the performance and efficiency of the product.
Through analysis, designers can identify areas of high pressure, excessive turbulence, or flow separation within the design. This information allows them to make informed design changes, optimizing the product's performance and ensuring proper functionality.
Additionally, using simulation and analysis, designers can test different design iterations virtually, saving time and resources compared to physical prototyping. They can evaluate multiple design options and select the one that yields the desired fluid flow behavior before manufacturing the product.
The simulation and analysis tools used in mechanical product design enable engineers to:
- Visualize and analyze fluid flow behavior within the product
- Optimize flow characteristics to reduce energy loss or improve efficiency
- Identify potential design flaws or areas of concern
- Predict and mitigate potential issues before the product is manufactured
In conclusion, mechanical product design in fluid dynamics leverages technological advancements in CAD and CFD software to simulate and analyze fluid flow within a design. This field plays a crucial role in industries where fluid interaction is significant, enabling engineers to optimize the efficiency, performance, and functionality of their products. By utilizing simulation and analysis tools, designers can make informed decisions and create designs that are well-suited for fluid flow.
Comments:
Thank you all for taking the time to read my article on enhancing mechanical product design through ChatGPT! I'm excited to hear your thoughts and feedback.
Great article, Jason! I found the concept of using ChatGPT for fluid dynamics simulation and analysis very intriguing. Have you personally tested its capabilities in this area?
Thank you, Michael! Yes, I have. ChatGPT proved to be quite effective in providing insights into fluid dynamics simulations. Its ability to analyze complex data and generate detailed reports was impressive.
I'm a mechanical engineer, and this article caught my attention. It would be great if ChatGPT could assist in optimizing product designs based on fluid dynamics analysis. Has that been explored as well?
Absolutely, Emily! One of the major advantages of using ChatGPT is its ability to offer design optimization suggestions based on fluid dynamics analysis. It can provide valuable insights to improve product performance.
I can see how ChatGPT could save a lot of time in the design process, but how accurate are its simulations compared to traditional methods?
Good question, Matthew. While ChatGPT provides reasonably accurate simulations, it's important to validate the results with traditional methods. It excels in generating quick insights, but an additional check is advisable for critical applications.
The use of AI in mechanical product design is fascinating. Do you think ChatGPT has the potential to revolutionize the industry?
Indeed, Sarah! ChatGPT has immense potential to revolutionize mechanical product design. With its ability to generate valuable feedback during the design process, engineers can iterate and improve designs more efficiently, leading to innovative and optimized products.
I can see the benefits of using ChatGPT for analysis, but what about its application in the initial design phase? Can it help generate new design concepts?
Definitely, Richard! ChatGPT can assist in the initial design phase by generating new concepts and ideas based on the input provided. Its creative potential can be leveraged to explore innovative design directions.
That's fascinating, Jason! I'm excited to see how ChatGPT can truly enhance the entire product design workflow.
As important as fluid dynamics analysis is, what other aspects of mechanical product design can benefit from the use of ChatGPT?
Great question, Linda! ChatGPT can also be valuable in areas like structural analysis, material selection, and manufacturing process optimization. Its versatility lends itself to various aspects of the design lifecycle.
It's impressive how AI continues to transform different industries. What are the limitations to consider when using ChatGPT in mechanical product design?
Indeed, Sarah. One limitation is that ChatGPT's recommendations should always be validated with traditional engineering knowledge and approaches. Additionally, it may struggle with highly complex or niche design problems where domain-specific expertise is essential.
I'm curious about the implementation process of ChatGPT in an existing design workflow. Could you provide some insights, Jason?
Absolutely, Daniel. Integrating ChatGPT into an existing design workflow usually involves training the AI model with relevant datasets and fine-tuning it for specific design requirements. Once integrated, it can provide real-time feedback during the design process.
The ethical considerations of using AI in product design are crucial. How do you address those concerns, Jason?
You're right, Emily. Ethical considerations are paramount. Transparent and explainable AI algorithms are crucial to ensure the decisions made by ChatGPT are understandable and traceable. Regular audits and human oversight help in maintaining ethical standards.
Are there any specific software tools or platforms that work well with ChatGPT for mechanical product design?
There are several software tools that can be integrated with ChatGPT, depending on the specific needs of the design process. Some popular options are SolidWorks, ANSYS, and Autodesk Fusion 360.
How accessible is ChatGPT for engineers who may not have much experience with AI?
Good question, Linda. ChatGPT is designed to be user-friendly, even for engineers with limited AI experience. The goal is to make it easily accessible and provide a seamless integration into their existing design workflows.
I can see how ChatGPT can greatly benefit product design teams. Are there any downsides to using this AI technology?
While ChatGPT offers numerous advantages, a potential downside is the availability and quality of training data. Ensuring diverse and accurate datasets is crucial to avoid biases or limitations in the AI model's predictions.
Are there any ongoing research or development efforts to further enhance ChatGPT for mechanical product design?
Absolutely, Daniel! Ongoing research focuses on improving data integration, refining simulation accuracy, and addressing specific design challenges. The goal is to continuously enhance the capabilities of ChatGPT in the field of mechanical product design.
It's impressive to see how AI technologies like ChatGPT are transforming traditional industries. What are the potential cost savings associated with its implementation?
Great point, Emily! By reducing the need for physical prototyping and extensive trial-and-error iterations, ChatGPT can significantly cut down product development costs. It enables more efficient use of resources and streamlines the design process.
I'm curious about the training process of ChatGPT. How are the AI models trained for fluid dynamics simulations?
Training ChatGPT models for fluid dynamics simulations involves using a combination of historical data, numerical simulations, and expert knowledge. This diverse information helps the model understand the intricacies of fluid dynamics and develop accurate predictions.
What kind of computing power is needed to run ChatGPT effectively for fluid dynamics simulations?
Running ChatGPT for fluid dynamics simulations can require significant computing power, especially for complex analyses. High-performance CPUs or GPUs are often used to ensure efficient execution and accurate results.
Do you foresee any potential challenges in adopting ChatGPT for fluid dynamics analysis within large engineering organizations?
Certainly, Richard. Scaling the implementation of ChatGPT across large engineering organizations might pose challenges in terms of computational infrastructure, data management, and ensuring uniform standards for AI usage. However, these can be overcome with careful planning and collaboration.
Can ChatGPT be applied to other engineering domains besides mechanical product design?
Absolutely, Linda! ChatGPT can be adapted to various engineering domains such as electrical, civil, or aerospace engineering. Its flexibility allows it to provide valuable insights and analysis in different areas of engineering.
I can see how ChatGPT can be a game-changer in mechanical product design. What are some key takeaways from your research, Jason?
Great question, Sarah! Key takeaways include the ability of ChatGPT to enhance fluid dynamics simulations, optimize designs based on analysis, and streamline the overall product design process. It has the potential to revolutionize how engineers approach mechanical product design.
As an industrial designer, I find this topic intriguing. Are there any constraints to keep in mind when using ChatGPT for product design?
Absolutely, Emma. When using ChatGPT, it's important to consider constraints such as material limitations, manufacturing capabilities, or cost factors. These constraints need to be factored into the design process to ensure the feasibility and practicality of the end product.
How do you see the future of ChatGPT and other AI technologies influencing the design industry?
The future looks promising, Daniel. AI technologies like ChatGPT will likely play an increasingly significant role in the design industry. They have the potential to revolutionize design workflows, enable faster iterations, and unlock innovative solutions, ultimately leading to better products.
With the growing capabilities of AI, do you think there will come a time when ChatGPT can entirely replace human expertise in certain design aspects?
While AI technologies are advanced and continue to evolve, human expertise will always be critical in design. ChatGPT augments human capabilities, enabling engineers to explore new ideas, optimize designs, and improve efficiency. It is a valuable tool rather than a complete replacement.
What potential challenges do you foresee in terms of implementation and acceptance of AI technologies like ChatGPT within the design industry?
Implementation and acceptance challenges could arise from factors like cultural resistance to AI adoption, the need for specialized training to use AI tools effectively, and concerns regarding data privacy and security. Proper education, communication, and transparent policies can help address these challenges.
Do you have any recommendations for engineers who are considering integrating AI technologies like ChatGPT into their design workflows?
Definitely, Emily! My recommendation would be to start by identifying specific challenges in your design workflow that AI can potentially address. Collaborate with experts in AI and gradually integrate AI technologies like ChatGPT into your processes. It's important to have a well-thought-out implementation plan to maximize its benefits.