Enhancing Quality Control in Leading Cross Functional Teams with ChatGPT
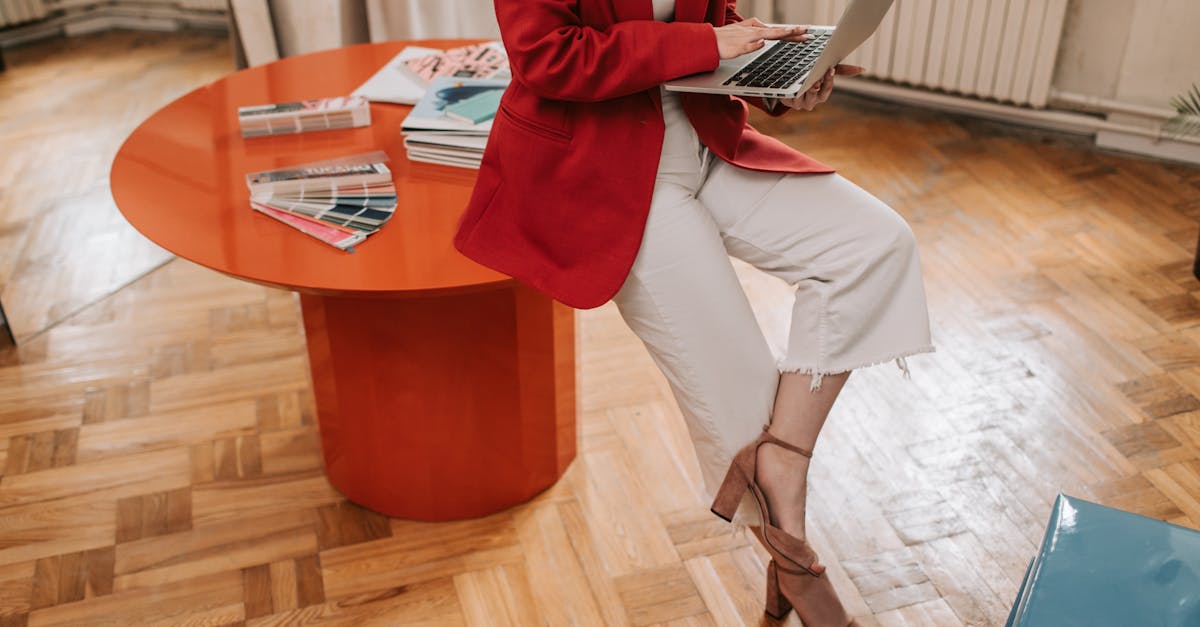
Quality control is a crucial aspect of any organization that aims to deliver products or services of the highest standards. In order to achieve this, effective leadership is needed to oversee the process and ensure that quality metrics are tracked and managed smoothly. This is where leading cross functional teams comes into play.
Understanding Cross Functional Teams
A cross functional team is a group of individuals with diverse skill sets and expertise that come together to work towards a common goal. In the context of quality control, a cross functional team may consist of members from different departments such as production, engineering, marketing, and customer service, all working collaboratively to ensure that quality standards are met.
The Role of Technology in Leading Cross Functional Teams
Technology plays a significant role in leading cross functional teams in quality control. Here are some ways it can be utilized:
- Track and Manage Quality Metrics: Technology enables team leaders to gather and analyze data related to quality control metrics such as defect rates, customer complaints, and product specifications. This allows them to identify areas of improvement and take proactive measures to enhance quality standards.
- Collaborative Communication: With technology, cross functional teams can easily communicate and share information in real-time, regardless of their physical locations. This improves collaboration and ensures that everyone is on the same page, leading to better decision-making and problem-solving.
- Automation: Automation tools can be employed to streamline quality control processes, reducing manual errors and improving efficiency. For example, automated testing software can quickly identify defects and issues, allowing the team to take immediate corrective actions.
- Documentation and Knowledge Management: Technology allows for easy documentation and management of quality control processes, including standard operating procedures, work instructions, and training materials. This ensures consistency and provides a centralized repository of knowledge for the team to refer to.
- Performance Tracking: Technology can be utilized to track and evaluate the performance of individual team members and the overall team. This helps in identifying areas of improvement and providing timely feedback and support.
The Benefits of Leading Cross Functional Teams in Quality Control
Leading cross functional teams in quality control brings several benefits to an organization:
- Enhanced Collaboration: By bringing together individuals from different backgrounds and expertise, cross functional teams foster collaboration and encourage the sharing of ideas and best practices.
- Better Problem Solving: The diverse perspectives and skills within a cross functional team enable more comprehensive problem-solving and decision-making. Issues can be approached from multiple angles, leading to innovative solutions.
- Improved Quality Standards: By effectively tracking and managing quality metrics, cross functional teams can ensure that the organization maintains the highest quality standards. This leads to improved customer satisfaction and loyalty.
- Increased Efficiency: Through the use of technology and streamlined processes, cross functional teams can optimize work processes and reduce waste, resulting in increased efficiency and productivity.
- Developing Skill Sets: Working in cross functional teams provides team members with opportunities to learn and develop new skills. Exposure to different areas of expertise enhances their knowledge and makes them well-rounded professionals.
Conclusion
Leading cross functional teams in quality control is a strategic approach that leverages the power of technology and collaborative teamwork to achieve the highest quality standards. By effectively tracking and managing quality metrics, organizations can ensure customer satisfaction, increase efficiency, and foster innovation.
Comments:
Thank you all for reading my article on enhancing quality control in leading cross-functional teams with ChatGPT. I'm excited to hear your thoughts and engage in a discussion!
Great article, Brett! I found your insights on using ChatGPT for quality control really interesting. It seems like it can definitely improve communication and collaboration within cross-functional teams.
I agree with you, Sarah. ChatGPT has the potential to streamline team communication across various departments and ensure everyone is on the same page.
I have some concerns about relying too heavily on AI for quality control. What if there are nuanced issues that ChatGPT might miss? Human judgment still plays a crucial role, doesn't it?
You make a valid point, Emily. While ChatGPT can assist with quality control, human judgment is indeed essential in identifying nuanced issues and making final decisions.
I'm curious about the potential challenges of implementing ChatGPT for quality control. How do you handle potential biases or training the AI to understand industry-specific requirements?
Great question, Michael. Overcoming biases can be challenging, but by using diverse training data and continuous feedback loops, we can reduce biases. Additionally, fine-tuning the AI model on industry-specific requirements helps ensure better results.
I appreciate the practical tips you shared, Brett. It's important to establish clear guidelines and expectations when using ChatGPT for quality control to ensure its effectiveness.
While ChatGPT can be an excellent tool, it's crucial not to solely rely on it. Human involvement and judgment are still paramount to maintain quality standards.
Brett, have you personally used ChatGPT for quality control in cross-functional teams? I'd love to hear about any specific successes or challenges you encountered.
Yes, Jacob! In my experience, using ChatGPT has improved communication efficiency and accuracy. However, managing user expectations and providing adequate training to team members were essential steps in achieving success.
I wonder if the implementation of ChatGPT would require additional training or technical expertise for team members. Not everyone may be familiar with AI tools.
That's a valid concern, Liam. Providing training and support to team members is crucial. Simple user interfaces and clear guidelines can help bridge any knowledge gaps.
While ChatGPT can enhance quality control, it's important to consider potential privacy and security risks associated with using AI-powered tools extensively within cross-functional teams.
Very true, Evelyn. Proper data handling and ensuring compliance with privacy regulations must be a priority when implementing AI tools like ChatGPT.
How scalable is ChatGPT for large cross-functional teams? Are there any limitations when it comes to handling a high volume of communication within the tool?
Scalability is an important consideration, Daniel. While ChatGPT can handle a significant volume of communication, there may be some limitations during peak usage. Planning for server capacity and response time is crucial for large teams.
I like the idea of leveraging AI to improve quality control, but I'm concerned about potential overreliance on technology. We should strike a balance between AI and human involvement.
Absolutely, Grace. The key is to use AI as a supportive tool without replacing human judgment and decision-making. Finding the right balance and ensuring human involvement is essential.
Great article, Brett! I believe ChatGPT can significantly improve inter-departmental collaboration and prevent miscommunications within cross-functional teams.
Thank you, Karen! Indeed, ChatGPT can bridge communication gaps and foster collaboration, enabling smoother interactions between departments.
Are there any limitations when it comes to ChatGPT's ability to understand context or handle complex technical discussions within cross-functional teams?
That's a valid concern, Owen. While ChatGPT has improved in understanding context, it might still struggle with highly technical discussions. It's important to assess its suitability for specific team requirements.
I'd be interested to know if ChatGPT supports multiple languages. In cross-functional teams, language diversity is common, and it's important to ensure inclusivity.
Great question, Emma. ChatGPT currently supports multiple languages, which makes it more accessible and inclusive for cross-functional teams with diverse language preferences.
I'm concerned about the potential loss of personal touch and human connection when using AI tools like ChatGPT extensively. How can we address this?
That's an important consideration, Aiden. While AI tools can enhance efficiency, finding a balance by also encouraging human interaction and fostering personal connections is crucial for team dynamics.
I wonder if chat-based tools like ChatGPT could potentially lead to misinterpretations or misunderstandings within cross-functional teams. Has this been a concern in your experience?
Great question, Amy. Misinterpretations can happen, especially in chat-based communications, which is why it's important to establish clear communication guidelines and foster a culture of asking for clarifications when needed.
I'm interested in knowing how ChatGPT can be integrated into existing team collaboration platforms. Is it a standalone tool or can it seamlessly integrate with platforms like Slack or Microsoft Teams?
Good question, Lucas. ChatGPT can be integrated into existing collaboration platforms like Slack or Microsoft Teams, making it a seamless addition to the team's communication ecosystem.
Have you encountered any resistance or skepticism from team members who may be hesitant to embrace AI tools like ChatGPT for quality control?
Indeed, Joshua. Resistance is natural when introducing new technology. Addressing concerns, providing user training, and highlighting the benefits of ChatGPT can help alleviate skepticism and encourage adoption.
What about the potential cost implications of implementing ChatGPT for quality control? Are there any significant financial considerations?
Cost is a valid consideration, Ellie. While using AI tools like ChatGPT may have associated expenses, the cost needs to be evaluated against the potential benefits of improved quality control, efficiency, and collaboration.
I'm intrigued by the idea of using AI-powered tools for quality control. Could you share any specific examples of how ChatGPT has improved quality control in real-world scenarios?
Certainly, Henry! One example is how ChatGPT helped cross-functional teams catch errors and inconsistencies in documentation, allowing for quicker revisions and improving overall quality.
Do you have any recommendations for organizations that are considering incorporating ChatGPT into their quality control processes? What factors should they consider?
Great question, Ava. Organizations should evaluate their specific needs, train team members effectively, consider privacy and security aspects, manage expectations, and have clear guidelines for successful implementation of ChatGPT in quality control processes.
What potential limitations or risks do you see in relying on AI tools for quality control within cross-functional teams? Are there any ethical concerns?
Valid concerns, Lily. Limitations can include biases in the AI model, privacy risks, and overreliance on technology. Ethical concerns arise in ensuring fair judgment, transparency, and maintaining human oversight.
How can organizations measure the effectiveness of using ChatGPT for quality control? Are there any specific metrics or indicators to monitor?
Monitoring metrics like error rates, turnaround time, and feedback from team members can provide insights into the effectiveness of ChatGPT in quality control. Regular evaluations and adjusting the system based on user feedback help measure success.
In situations where there are disagreements or conflicts within cross-functional teams, how can ChatGPT help facilitate resolution or provide unbiased insights?
Excellent question, Zoe. ChatGPT can act as a neutral mediator, providing alternative viewpoints and suggestions. However, it's important to have open discussions and human involvement to address conflicts effectively.
Are there any legal or compliance considerations organizations should be aware of when implementing AI-based tools like ChatGPT in quality control processes?
Absolutely, Nathaniel. Compliance with data protection regulations, intellectual property rights, and ensuring proper consent for data usage are vital legal considerations when implementing AI-powered tools like ChatGPT.
Do you foresee AI tools like ChatGPT completely revolutionizing quality control processes in the future? What advancements can we anticipate?
AI tools like ChatGPT have immense potential to revolutionize quality control processes, but they will likely work in tandem with human judgment. Advancements may include better contextual understanding, improved model training, and enhanced customization options.
Thank you all for this engaging discussion! Your valuable insights and questions highlight the importance of carefully integrating AI tools like ChatGPT into quality control processes. Let's continue exploring the possibilities and addressing the challenges together!