GPT-Powered Intelligence: Revolutionizing Risk Assessment in Mechanical Product Design
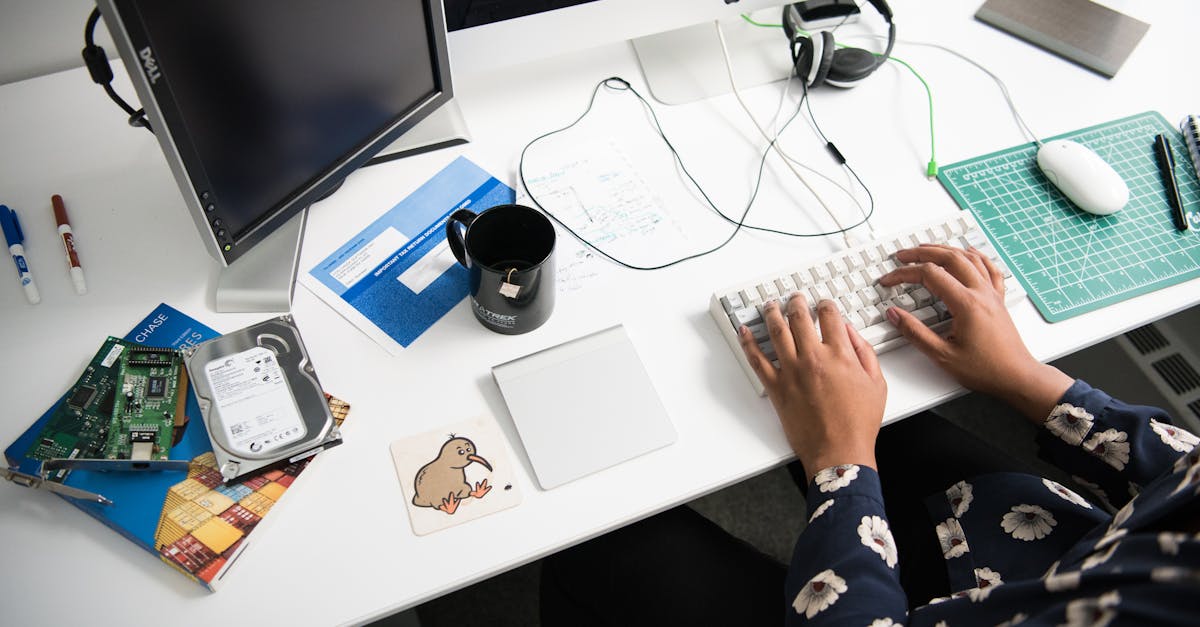
The field of mechanical product design is a vital aspect of engineering where products are designed and developed for various industries. However, during the design and production phases, there are inherent risks and challenges that need to be carefully evaluated to ensure the success and safety of the end product. This is where risk assessment plays a crucial role.
What is Risk Assessment?
Risk assessment is a systematic process that aims to identify, analyze, and evaluate potential risks associated with a particular activity or project. In the context of mechanical product design, risk assessment involves assessing the potential risks and challenges that may arise during the design and production phases.
The Importance of Risk Assessment in Mechanical Product Design
1. Safety: Safety is of paramount importance in mechanical product design. By conducting a thorough risk assessment, designers and engineers can identify potential hazards and take measures to minimize or eliminate them. This ensures that the end product is safe for both users and manufacturers.
2. Cost Management: Risk assessment helps in managing costs associated with design and production. By identifying potential risks early on, design flaws or issues can be addressed before they become costly problems. This prevents delays, rework, and other cost-intensive challenges that may occur during the production phase.
3. Quality Assurance: A comprehensive risk assessment allows designers to evaluate the reliability and quality of the product. By identifying and addressing potential risks, the design process can be optimized, leading to a higher-quality end product that meets the required specifications and standards.
Steps in Risk Assessment for Mechanical Product Design
The risk assessment process in mechanical product design typically involves the following steps:
1. Hazard Identification: The first step is to identify potential hazards or risks associated with the product design and production. This may include mechanical failures, material limitations, safety hazards, or any other factors that may pose a risk in the intended use of the product.
2. Risk Analysis: Once the hazards have been identified, the next step is to analyze the risks associated with each hazard. This involves determining the likelihood of the risk occurrence and the potential severity of its consequences. This analysis helps prioritize risks based on their potential impact.
3. Risk Evaluation: After analyzing the risks, an evaluation is carried out to determine the acceptability of the risks. This involves comparing the risks against predefined criteria or standards to assess whether they can be tolerated or if additional mitigation measures are necessary.
4. Risk Control: If the identified risks are found to be unacceptable, risk control measures are implemented to reduce or eliminate the risks. This may involve modifying the design, selecting alternative materials, or incorporating safety mechanisms to mitigate the risks identified during the assessment process.
5. Monitoring and Review: Risk assessment is an ongoing process that should be monitored and reviewed throughout the design and production phases. Regular review and evaluation of the risks ensure that any changes or new risks are identified and addressed promptly to maintain the safety and quality of the product.
Conclusion
In the field of mechanical product design, conducting a thorough risk assessment is essential to identify and mitigate potential risks and challenges during the design and production phases. By assessing potential hazards early on, manufacturers can ensure the safety, cost-effectiveness, and quality of their products. Risk assessment is a continuous process that requires careful monitoring and regular review to adapt to changing circumstances and technological advancements. By implementing a robust risk assessment process, designers and engineers can create innovative and reliable mechanical products that meet the needs and expectations of users while minimizing risks.
Comments:
Thank you all for your comments on my article. I appreciate your thoughts and insights.
This is a fascinating use of GPT-powered intelligence. It seems like a game-changer for risk assessment in mechanical product design.
Indeed, Michael. GPT-powered intelligence has opened up new possibilities in various industries, and the field of mechanical product design is no exception. It enables us to analyze risks more efficiently and make better-informed decisions.
I agree with Michael. This technology has the potential to revolutionize how we approach risk assessment. It could greatly improve product safety and reliability.
While GPT-powered intelligence may be impressive, I wonder about the reliability of its predictions. How accurate is it compared to traditional risk assessment methods?
That's a valid concern, David. GPT models have shown promising results in many domains, but it's important to establish their accuracy and compare them against traditional methods. Further research and testing are required to gain more insights into the reliability of GPT-powered risk assessment.
I'm curious about the training process for GPT models in this context. How is the data collected and used to ensure accurate risk assessment?
Great question, Sophia. Training GPT models for risk assessment involves providing them with a diverse dataset consisting of various mechanical designs, associated risks, and outcomes. The model learns patterns and associations from this data to make predictions. However, data quality and biases can affect accuracy, so careful data curation and validation are crucial.
I'm concerned about potential biases in the data used to train these AI models. How can we ensure that the risk assessments are fair and unbiased?
Bias mitigation is a critical aspect of AI development, Mark. It's important to address biases in the training data and validation processes. By continuously monitoring and refining the models, we can strive for fair and unbiased risk assessments. Transparency in the AI development process is also crucial to ensure accountability.
This technology sounds promising, but I worry about the potential job losses it might cause. Could it replace human experts in risk assessment?
Valid concern, Sarah. While GPT-powered intelligence can augment risk assessment processes, it is not meant to replace human experts. These models can assist experts by analyzing large volumes of data and identifying patterns, allowing them to make more informed decisions. Human expertise and critical thinking remain invaluable in interpreting and contextualizing the results.
I can see the benefits of using GPT-powered intelligence in risk assessment, but I also worry about the ethical implications. How can we ensure the responsible use of this technology to avoid any unintended consequences?
Ethical considerations are crucial when deploying AI technologies, Daniel. Clear guidelines and regulations need to be established to address responsible use. Continuous oversight, accountability, and transparency can help mitigate unintended consequences. Collaboration between experts from various fields is essential to shape ethical and responsible AI practices.
The potential of GPT-powered intelligence to improve risk assessment is undeniable. It should be exciting to see how this technology evolves and gets integrated into mechanical product design.
Indeed, Grace. The ongoing advancements in GPT models and AI-driven technologies hold tremendous promise for enhancing risk assessment and elevating the field of mechanical product design.
Are there any specific industry applications where GPT-powered risk assessment has already been successfully implemented?
Several industries have begun exploring the potential of GPT-powered risk assessment, Andrew. For example, automotive manufacturers are using it to evaluate safety risks in vehicle design. Aerospace companies are also utilizing it to assess risks in aircraft components. The technology shows promising results, but further adoption and refinement are needed.
I'm excited about the prospects of GPT-powered intelligence in risk assessment. It has the potential to accelerate design iterations and reduce time-to-market while ensuring product safety.
Absolutely, Melissa. The efficient analysis provided by GPT-powered intelligence can significantly expedite the design process, allowing companies to innovate rapidly without compromising on safety and reliability.
I wonder if GPT models can be trained to consider real-time data in risk assessment. This could help account for dynamic factors influencing product safety.
That's an interesting proposition, Adam. Integrating real-time data into risk assessment models can certainly enhance their predictive capabilities by accounting for dynamic factors. It could lead to more accurate and adaptive risk assessments, especially in fast-changing industries.
I'm curious about the limitations of GPT-powered intelligence in risk assessment. Are there any challenges or scenarios where it may not be as effective?
Good question, Lily. While GPT models have shown remarkable capabilities, there are limitations. They heavily rely on the data provided during training, so if the training data doesn't capture all relevant scenarios or introduces bias, it can impact accuracy. Unseen or novel situations may also pose challenges. Ongoing research aims to address these limitations.
I'm curious if GPT-powered risk assessment can be applied to other domains beyond mechanical product design?
Absolutely, Oliver. GPT-powered risk assessment has the potential for broader applications beyond mechanical product design. Industries like healthcare, finance, and cybersecurity are already exploring its possibilities. It's a versatile technology that can be adapted to various domains where risk assessment is crucial.
I can see how GPT-powered intelligence can streamline risk assessment, but what are the potential cost considerations when implementing this technology?
Cost is a valid consideration, Julia. Implementing GPT-powered risk assessment involves infrastructure requirements, data collection, and model development costs. However, as the technology evolves and adoption increases, the costs are expected to decrease over time. It's essential to evaluate the benefits and long-term value it brings to justify the investment.
I'm excited about the possibilities of GPT-powered intelligence in risk assessment, but I'm also concerned about data privacy. How can we ensure the protection of sensitive information?
Data privacy is a critical aspect, Aiden. Protecting sensitive information should be a top priority. Anonymization techniques, secure data storage protocols, and compliance with relevant privacy regulations can help safeguard personal and company data. Responsible data usage and stringent security measures are essential to maintain user trust.
Thank you for the detailed explanation, Jason. Ensuring accurate and unbiased risk assessment is crucial, especially when it comes to mechanical product design.
You're welcome, Sophia. It's important to explore the potential of emerging technologies in risk assessment, but also remain cautious and thoroughly evaluate their effectiveness.
I appreciate your response, Jason. Establishing fairness and avoiding biases in risk assessment is key to ensuring the safety and reliability of products.
Thank you for addressing my concern, Jason. The collaboration between AI and human experts can lead to better risk assessment outcomes.
I agree, Jason. Ethical considerations and responsible use of AI technologies are essential to prevent any unintended consequences.
Thanks for the insights, Jason. It's interesting to see how GPT-powered risk assessment is being implemented across different industries.
I'm glad to hear that, Jason. Accelerating the design process while maintaining safety is a major advantage for businesses.
Agreed, Jason. Real-time data integration could make risk assessment more responsive and adaptable to changing circumstances.
Thank you for the clarification, Jason. Understanding the limitations of GPT-powered intelligence is essential when utilizing this technology.
That's exciting to hear, Jason. GPT-powered risk assessment has the potential to revolutionize multiple industries.
Considering long-term value is crucial, Jason. The cost-benefit analysis of implementing GPT-powered risk assessment is important for decision-making.
Thank you, Jason. Privacy protection must be a priority to maintain public trust in AI-powered risk assessment systems.
I agree, Michael. This technology has great potential to improve risk assessment in mechanical product design.
I'm curious about the training process for GPT models in this context. How is the data collected and used to ensure accurate risk assessment?
I'm concerned about potential biases in the data used to train these AI models. How can we ensure that the risk assessments are fair and unbiased?
This technology sounds promising, but I worry about the potential job losses it might cause. Could it replace human experts in risk assessment?
I can see the benefits of using GPT-powered intelligence in risk assessment, but I also worry about the ethical implications. How can we ensure the responsible use of this technology to avoid any unintended consequences?
The potential of GPT-powered intelligence to improve risk assessment is undeniable. It should be exciting to see how this technology evolves and gets integrated into mechanical product design.
Are there any specific industry applications where GPT-powered risk assessment has already been successfully implemented?
I'm excited about the prospects of GPT-powered intelligence in risk assessment. It has the potential to accelerate design iterations and reduce time-to-market while ensuring product safety.
I wonder if GPT models can be trained to consider real-time data in risk assessment. This could help account for dynamic factors influencing product safety.
I'm curious about the limitations of GPT-powered intelligence in risk assessment. Are there any challenges or scenarios where it may not be as effective?
I'm curious if GPT-powered risk assessment can be applied to other domains beyond mechanical product design?
I can see how GPT-powered intelligence can streamline risk assessment, but what are the potential cost considerations when implementing this technology?
I'm excited about the possibilities of GPT-powered intelligence in risk assessment, but I'm also concerned about data privacy. How can we ensure the protection of sensitive information?