Optimizing Data Collection and Analysis for CNC Programming Technology with ChatGPT
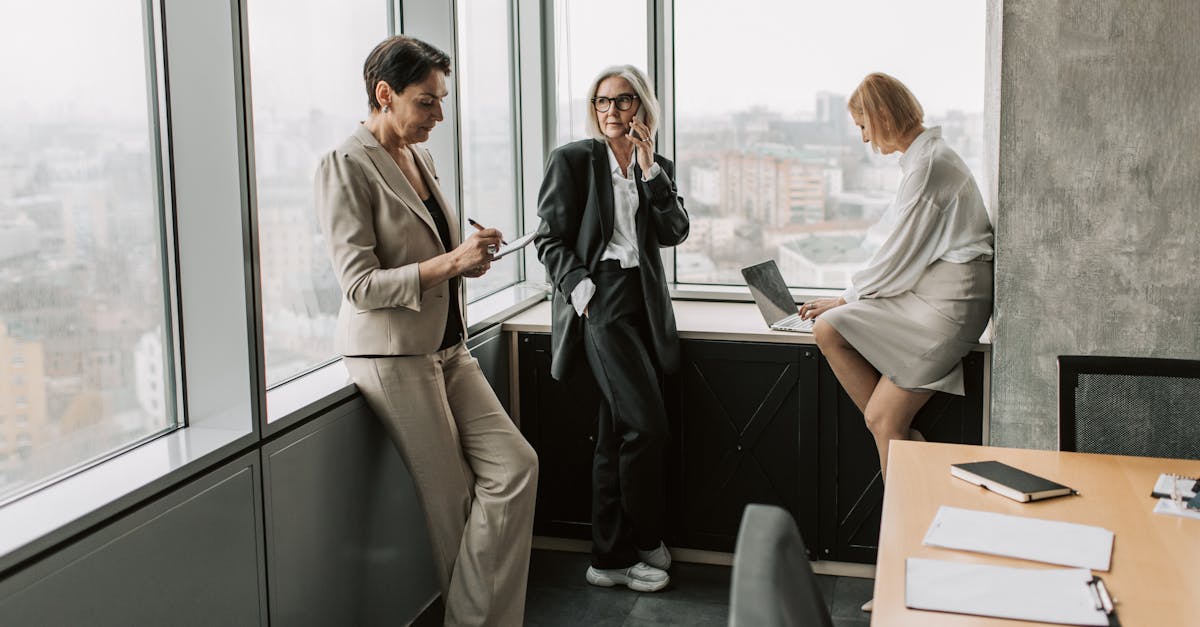
Computer Numerical Control (CNC) programming is a technology used in the CNC manufacturing process for the precise control of machine tools. It involves the use of computer programs to automate the operation of machine tools by providing instructions for the movement and manipulation of the tooling equipment.
One area where CNC programming finds extensive use is in data collection and analysis. CNC machines are equipped with sensors that can capture various types of data during the manufacturing process. This data can include measurements of tooling positions, machining parameters such as speed and feed rates, and other relevant information.
The data collected by CNC machines can be stored and analyzed for various purposes. It provides valuable insights into the manufacturing process, allowing users to monitor and optimize production. By analyzing the collected data, manufacturers can identify patterns, trends, and potential issues that might affect the quality and efficiency of the manufacturing process.
Data analysis in CNC programming can help in improving overall productivity and reducing manufacturing costs. By understanding the relationship between different variables, such as tool wear and cutting parameters, manufacturers can optimize their machining processes to prolong tool life and lower tooling costs. It also helps in identifying bottlenecks and optimizing workflow, leading to enhanced efficiency and reduced cycle times.
CNC programming allows for the collection of real-time data, which can be used to detect anomalies or deviations from expected values during the manufacturing process. By comparing current data with historical data, manufacturers can identify and address issues before they result in expensive errors or failures. This proactive approach to quality control can help in ensuring the production of high-quality and consistent products.
In addition, the collected data can be leveraged to improve machine performance. By analyzing data related to machine diagnostics, such as vibration levels or temperature readings, manufacturers can identify potential machine faults or maintenance needs. This enables proactive maintenance scheduling, reducing unplanned downtime and maximizing machine availability.
CNC programming also facilitates the integration of data with other systems, such as Enterprise Resource Planning (ERP) or Manufacturing Execution Systems (MES). The integration allows for seamless data flow throughout the manufacturing operation, enabling better coordination and decision-making. Real-time data integration provides a holistic view of the manufacturing process, allowing manufacturers to make informed decisions and adapt quickly to changing production demands.
In conclusion, CNC programming is a powerful technology that can be utilized for data collection and analysis in CNC manufacturing processes. The ability to collect, store, and analyze data provides manufacturers with valuable insights for process optimization, quality control, and productivity improvements. By leveraging CNC programming for data analysis, manufacturers can enhance their manufacturing capabilities and stay competitive in today's rapidly evolving industry.
Comments:
Thank you all for reading my article on Optimizing Data Collection and Analysis for CNC Programming Technology with ChatGPT. I hope you find the information useful. Feel free to ask any questions or share your thoughts!
Great article, Michael! I appreciated how you explained the importance of data collection and analysis for CNC programming technology. It's fascinating how AI can enhance efficiency and accuracy in this field.
Thank you, Sarah! I'm glad you found the article interesting. AI indeed has the potential to revolutionize CNC programming, leading to improved productivity and precision.
I have some experience with CNC programming, and I must say that data collection and analysis are crucial for optimizing the process. Are there any specific tools or techniques you recommend for efficient data collection?
Hi Andrew! Absolutely, efficient data collection is key. Some commonly used tools for CNC programming data collection include sensors, machine monitoring systems, and digital simulations. These can provide valuable insights for analysis and optimization.
I found it fascinating how ChatGPT can assist in CNC programming technology. Are there any limitations or challenges we should be aware of when implementing AI in this field?
Hello Olivia! AI integration in CNC programming does come with its challenges. One major concern is the accuracy and reliability of the AI models. Ensuring proper training and validation are essential to minimize errors and risks.
Data analysis is the backbone of any optimization process, and CNC programming is no exception. Michael, you explained it really well in your article. Thanks for sharing!
Thank you, Emma! I'm glad you found the explanation helpful. Data analysis plays a crucial role in identifying patterns, optimizing parameters, and improving CNC programming outcomes.
I'm curious about the implementation of ChatGPT in CNC programming. How does it handle complex instructions or scenarios that require decision-making beyond predefined rules?
That's a great question, Daniel. ChatGPT can handle complex instructions by using its contextual understanding and the ability to generate human-like responses. It can adapt to scenarios beyond predefined rules, which makes it helpful in CNC programming tasks.
Michael, your article shed light on the potential benefits of AI in CNC programming. However, do you think AI can completely replace human expertise in this field?
Hi Sophia. While AI shows promise in CNC programming, it's unlikely to replace human expertise entirely. Human skills, creativity, and domain knowledge are still vital for tackling unique challenges and ensuring optimal results.
The advancement of CNC programming technology is fascinating! Michael, I enjoyed reading your article, and it's great to see AI being integrated into such fields.
Thank you, Lucas! It's indeed an exciting time with the integration of AI in CNC programming, bringing new possibilities and advancements to the industry.
I found your article very informative, Michael, especially the part about optimizing data collection. It's crucial for companies to gather relevant data to make informed decisions and improve CNC programming processes.
Exactly, Natalie! Optimized data collection enables companies to identify inefficiencies, make data-driven decisions, and continuously improve their CNC programming processes.
As an industry professional, I appreciate your insights into the role of data analysis in CNC programming. Data-driven optimization has become a necessity in today's competitive manufacturing landscape.
Thank you, James! You're absolutely right. In a highly competitive landscape, leveraging data-driven optimization is crucial to stay ahead and improve performance in CNC programming.
Great article, Michael! I'm excited to see how AI advancements can transform CNC programming technology.
Thank you, Lily! AI advancements definitely hold tremendous potential for transforming CNC programming and pushing the boundaries of what's achievable.
Michael, your article was a great read! I was wondering if you have any recommendations for companies planning to adopt AI in their CNC programming systems?
Hi David! If a company plans to adopt AI in CNC programming, it's crucial to start with a clear roadmap and understanding of the specific problem areas they want to address. Collaborating with AI experts and gradually implementing solutions can lead to successful adoption.
I've always been intrigued by CNC programming, and your article highlighted some exciting aspects. How do you see the future of AI in this field?
Hello Ruby! The future of AI in CNC programming looks promising. We can anticipate further advancements in machine learning algorithms, AI-driven automation, and increased integration of AI technologies, leading to more efficient and intelligent CNC programming systems.
Data optimization in CNC programming is vital for improving productivity and reducing errors. Loved reading your article, Michael!
Thank you, Sophia! I'm glad you found the article insightful. Data optimization plays a key role in enhancing productivity and ensuring accurate results in CNC programming.
AI has limitless applications, and integrating it into CNC programming is a smart move. Michael, your article was an excellent overview of this exciting topic.
Thank you for your kind words, Oliver! AI integration in CNC programming indeed opens up new possibilities and brings efficiency to this field.
Your article was a great read, Michael! I'm curious if you have any specific success stories where AI optimization in CNC programming led to tangible improvements.
Hi Mia! There are indeed success stories where AI optimization in CNC programming resulted in significant improvements. For example, a company using AI-driven optimization reduced production time by 20% while maintaining high precision standards.
I enjoyed reading your article, Michael. As CNC programming evolves, how do you see human roles changing in response to increased AI integration?
Thanks, Daniel! With increased AI integration, human roles in CNC programming are likely to shift towards more strategic tasks, such as refining algorithms, overseeing AI systems, and utilizing their expertise to handle unique challenges beyond the capabilities of AI.
Michael, your article beautifully explains the link between data collection, analysis, and CNC programming optimization. Well done!
Thank you, Grace! I appreciate your kind words. The connection between data collection, analysis, and CNC programming optimization is indeed crucial to achieving optimal results.
Could you provide some insights into the potential cost savings that AI integration can bring to CNC programming systems?
Certainly, Ethan! AI integration in CNC programming can lead to significant cost savings through improved efficiency, reduced errors, better resource management, and optimized production processes. Companies can save on time, materials, and overall operational costs.
As an AI enthusiast, I find it fascinating to see AI making its way into various industries. Michael, your article perfectly explores its applications in CNC programming.
Thank you, Grace! AI's impact and applications across industries continue to grow, and CNC programming is no exception. It's an exciting intersection that brings improved efficiency and precision.
Data collection and analysis are crucial to make sound decisions and optimize CNC programming processes. Your article, Michael, highlighted its significance splendidly.
Thank you, Aaron! I'm glad you found the significance of data collection and analysis well presented in the article. Making informed decisions through data-driven insights is key to successful CNC programming.
Michael, your article was an excellent resource! I'm curious about the potential impact of AI in CNC programming training and education.
Hello Nora! AI can significantly impact CNC programming training and education by providing interactive simulations, virtual training environments, and AI-assisted learning platforms. These technologies can enhance the learning experience and help individuals acquire CNC programming skills more effectively.
I've been following AI advancements, and their integration into CNC programming is a fascinating development. Great article, Michael!
Thank you, Benjamin! The integration of AI into CNC programming is indeed an exciting development, opening up new possibilities and propelling the industry forward.
The optimization of data collection and analysis can undoubtedly revolutionize CNC programming. Michael, your article provided valuable insights into this transformation.
Thank you, Ava! I'm glad you found the insights valuable. Revolutionizing CNC programming through optimized data collection and analysis can greatly enhance efficiency and outcomes.
Your article highlighted the importance of chatbots in CNC programming. How do you see their role evolving in the future, Michael?
Hi William! Chatbots can play a crucial role in CNC programming by assisting in generating code, providing real-time guidance, and answering queries. In the future, we can anticipate more advanced and proactive chatbot functionalities, further enhancing their role in this field.
Michael, your article was well-written and informative, providing an excellent analysis of the benefits of AI integration in CNC programming.
Thank you, Evelyn! I'm glad you found the article well-written and informative. AI integration offers immense benefits to CNC programming, driving efficiency and precision.
Your article, Michael, showcased the immense potential of AI in CNC programming. It's an exciting time for the industry.
Thank you, Samuel! It is indeed an exciting time for the CNC programming industry as AI continues to reshape the way we approach optimization and efficiency.
Would you recommend any specific AI platforms or frameworks for companies looking to integrate AI in their CNC programming systems, Michael?
Hi Adam! There are several AI platforms and frameworks available for integrating AI in CNC programming. Some popular ones include TensorFlow, PyTorch, and Caffe. Choosing the right platform depends on the specific requirements and expertise of the company.
CNC programming is an intriguing field, and your article, Michael, provided valuable insights into the role of AI in its optimization.
Thank you, Eliana! I'm glad you found the article insightful. AI's integration in CNC programming offers exciting prospects for enhanced optimization and improved results.
I'm curious about the impact of AI integration on the workload of CNC programmers. Could it lead to reduced human labor requirements?
Hi Nathan! AI integration in CNC programming can indeed reduce certain repetitive tasks and improve automation. While it may lead to optimized human labor requirements, the need for human expertise in handling unique challenges and overseeing AI systems will still be essential.
Michael, your article provided valuable insights into the optimization of data collection and analysis for CNC programming. Thank you!
You're welcome, Sophie! I'm glad you found the insights valuable. Optimizing data collection and analysis is instrumental in achieving efficient CNC programming outcomes.
Your article, Michael, perfectly explained the significance of data collection and analysis in CNC programming optimization. Well done!
Thank you, Liam! I'm glad you found the explanation of data collection and analysis in CNC programming optimization well presented. It's a critical aspect of achieving optimal results.
As AI becomes more prevalent, its integration into CNC programming is crucial for staying competitive. Great article, Michael!
Thank you, Leah! The integration of AI in CNC programming indeed provides companies with a competitive edge, improving efficiency and driving innovation.
Michael, your article was a fantastic read! It's inspiring to see how AI is augmenting CNC programming technology.
Thank you for your kind words, Ruby! AI's augmentation of CNC programming technology holds immense potential for new advancements and improved outcomes.
Great article, Michael! AI integration in CNC programming holds tremendous promise, and you explained it all brilliantly.
Thank you, Caleb! AI integration in CNC programming does indeed hold tremendous promise for pushing the boundaries of what can be achieved. I'm glad you found the explanation effective.
Optimizing data collection and analysis is essential for staying competitive in CNC programming. I loved reading your article, Michael.
Thank you, Lucy! Optimizing data collection and analysis is crucial for competitiveness and continuous improvement in CNC programming. I'm glad you enjoyed the article.
As CNC programming evolves, integrating AI is bound to become a necessity for manufacturers. Michael, your article covered this topic brilliantly.
Thank you, Aiden! Integrating AI into CNC programming is indeed becoming increasingly essential for manufacturers who aim to enhance efficiency and maintain competitiveness.
Michael, your article was thoroughly researched and well-written. You provided valuable insights into AI's role in CNC programming optimization.
Thank you, Grace! I appreciate your feedback. Thorough research and providing valuable insights were my goals when writing the article on AI's role in CNC programming optimization.
I found your article highly informative, Michael. How do you see AI impacting CNC programming quality control processes?
Hello Sebastian! AI can greatly impact CNC programming quality control processes by enabling real-time monitoring, predictive analytics for defect prevention, and precise quality assessment. It can significantly enhance the overall quality control measures.
Your article, Michael, was a comprehensive exploration of AI integration in CNC programming. It's amazing to see how technology evolves.
Thank you, Emily! Technology evolves at a remarkable pace, and CNC programming is witnessing significant advancements through the integration of AI. It's an exciting time indeed!
Your article provided great insights, Michael. I'm excited to see how AI advancements will continue to shape the CNC programming industry.
Thank you, Leo! AI advancements will undoubtedly continue to shape the CNC programming industry, further enhancing efficiency, precision, and innovation.
Great article, Michael! AI's integration with CNC programming opens up new doors for process optimization.
Thank you, Emily! AI's integration in CNC programming indeed brings new possibilities for optimizing processes and achieving enhanced outcomes.
The optimization of data collection and analysis is fundamental to improving CNC programming. Your article, Michael, explained it superbly.
Thank you, Sebastian! Optimizing data collection and analysis is indeed fundamental in improving CNC programming outcomes. I'm glad you found the explanation superb.
Your article was insightful, Michael! How do you see AI integration impacting CNC programming automation processes?
Hello Olivia! AI integration can significantly impact CNC programming automation processes by enabling intelligent decision-making, improving efficiency, and reducing manual intervention. It paves the way for more streamlined and automated workflows.
I find AI's integration into CNC programming fascinating. Your article provided a comprehensive overview, Michael.
Thank you, Lily! I'm glad you found the integration of AI into CNC programming fascinating. It's a field filled with exciting possibilities for efficiency and precision.
As a CNC programmer, your article resonated with my experience. AI integration has transformed the way we approach optimization. Well done, Michael!
Thank you for your kind words, David! It's great to hear that the article resonated with your experience as a CNC programmer. AI integration has indeed brought transformative changes to the field of optimization.
Michael, your article highlighted the importance of data-driven decision-making in CNC programming optimization. Well explained!
Thank you, Chloe! Data-driven decision-making is at the core of CNC programming optimization, guiding the path towards improved efficiency and quality outcomes.
AI's integration into CNC programming holds immense potential for efficiency and precision. Your article brilliantly covered this, Michael.
Thank you, Carter! The integration of AI in CNC programming, indeed, holds immense potential for enhancing efficiency, precision, and overall outcomes. I'm glad you found the coverage brilliant.
I found your article captivating, Michael! How do you see AI shaping the future of CNC programming careers?
Hello Abigail! AI is set to reshape CNC programming careers by augmenting human capabilities, automating repetitive tasks, and enabling professionals to focus on more complex challenges. It will redefine roles and requirements, emphasizing a synergy between AI and human expertise.
Thank you for sharing your insights, Michael. How can small-scale companies with limited resources embrace AI in CNC programming?
Hi Samuel! Small-scale companies can embrace AI in CNC programming by starting small and focusing on specific problem areas. Leveraging open-source AI frameworks, collaborating with AI experts, and gradually scaling up the adoption can help overcome limited resources.
Your article, Michael, highlighted the potential for AI in optimizing CNC programming. It's exciting to witness this progress.
Thank you, Alexandra! Witnessing the progress AI brings to optimizing CNC programming is indeed an exciting journey, marked by increased efficiency and technological advancements.
The integration of AI in CNC programming is fascinating, and your article showcased its impact beautifully. Well done, Michael!
Thank you, Joseph! The integration of AI in CNC programming is indeed fascinating, and its impact on the industry is profound. I'm glad you found the article well presented.
Michael, your article provided an excellent overview of how AI revolutionizes CNC programming. Thank you for sharing your insights!
You're welcome, Sophia! I'm pleased to hear that you found the article to be an excellent overview of how AI revolutionizes CNC programming. Sharing insights is a pleasure.
AI's integration in CNC programming is transformative. Your article, Michael, brilliantly captured the essence of this transformation.
Thank you, David! The transformative impact of AI's integration in CNC programming is indeed significant. I'm glad you found the article to capture its essence.
Michael, your article was incredibly informative. Can you expand on the potential impact of AI integration in CNC machining?
Hi Levi! AI integration in CNC machining can have a profound impact, enabling advanced optimization algorithms, predictive maintenance, autonomous decision-making, and accurate models for predicting machining outcomes. It revolutionizes the entire CNC machining process.
Your article, Michael, highlighted how AI integration can drive efficiency in CNC programming. It's impressive to see the advancements.
Thank you, Ella! The advancements in AI integration are impressive, and the positive impact on efficiency in CNC programming is remarkable. It's an exciting time for the industry.
The role of AI in CNC programming is fascinating. Michael, your article provided a detailed exploration of its benefits.
Thank you, Lucas! The role of AI in CNC programming indeed brings fascination and promises numerous benefits for optimizing the entire process. I'm glad you found the exploration detailed.
Your article, Michael, shed light on the impact of AI in CNC programming technology. Well explained and researched!
Thank you, Jonathan! Shedding light on the impact of AI in CNC programming technology and providing well-explained and researched information were my objectives. I'm glad you found it so.
The integration of AI in CNC programming holds immense potential. Michael, your article skillfully captured this.
Thank you, Nathan! The potential held by AI integration in CNC programming is immense, and capturing it skillfully in the article was my intention. I'm glad it resonated with you.
Your article was enlightening, Michael! Can you elaborate on the challenges AI may face in CNC programming implementation?
Hi Sophie! Challenges AI may face in CNC programming implementation include ensuring the accuracy and reliability of AI models, dealing with complex edge cases, overcoming initial costs and resource requirements, and addressing potential resistance to new technologies. Proper training, validation, and gradually overcoming these challenges are necessary for successful implementation.
Great article, Michael! AI's integration in CNC programming undoubtedly brings numerous benefits to the industry.
Thank you, Ethan! The integration of AI in CNC programming certainly brings numerous benefits, enhancing efficiency, precision, and overall outcomes. I'm glad you found the article great.
Optimizing data collection and analysis is pivotal in CNC programming. Michael, your article provided valuable insights into this optimization.
Thank you, Eliana! Optimizing data collection and analysis plays a central role in CNC programming, and I'm glad the article provided valuable insights into this crucial aspect.
Your article, Michael, showcased the potential of AI integration in CNC programming flawlessly. It's an exciting advancement.
Thank you, Aaron! The potential of AI integration in CNC programming is indeed exciting, opening up new horizons and possibilities. I'm glad you found the showcase flawless.
AI's impact on CNC programming is remarkable. I loved reading your article, Michael.
Thank you, Rachel! AI's impact on CNC programming is indeed remarkable, transforming processes, optimizing efficiency, and enhancing outcomes. I'm glad you enjoyed reading the article.
Your article was a fantastic read, Michael! How can companies overcome resistance and foster a smooth transition during AI integration in CNC programming?
Hi Anna! Overcoming resistance and fostering a smooth transition during AI integration in CNC programming involves effective communication, providing training and support to employees, showcasing successful case studies, and gradual implementation to build trust and familiarity. Including employees in the decision-making process and emphasizing the benefits of AI can help gain support and cooperation.
Your article provided an excellent overview of AI's impact in CNC programming. Well done, Michael!
Thank you, Daniel! I'm pleased to hear that the article provided an excellent overview of AI's impact in CNC programming. Well-done was my aim, and I'm glad you think so.
AI integration has great potential in CNC programming. Michael, your article highlighted this brilliantly.
Thank you, Sophia! The great potential held by AI integration in CNC programming is indeed remarkable. I'm glad you found the article's highlighting brilliant.
Your article, Michael, shed light on the transformative power of AI in CNC programming. It was an engaging read.
Thank you, Jackson! Shedding light on the transformative power of AI in CNC programming was my goal, and I'm glad the article engaged you.
Michael, your article was a great resource for understanding AI's impact on CNC programming. Thank you for sharing your knowledge!
You're welcome, Lucy! I'm delighted to hear that you found the article to be a great resource for understanding AI's impact on CNC programming. Sharing knowledge is a pleasure.
Data collection and analysis are integral to optimization in CNC programming. Your article, Michael, explained this importance beautifully.
Thank you, Jackson! Data collection and analysis play a pivotal role in optimizing outcomes in CNC programming, and I'm glad you found the explanation beautiful.
Your article was comprehensive and well-articulated, Michael! I'm excited to witness how AI transforms CNC programming technology.
Thank you, Sophie! A comprehensive and well-articulated article was my intention, and I'm glad you found it so. Witnessing how AI transforms CNC programming technology is indeed an exciting journey.
Great article, Michael! AI's integration in CNC programming presents a huge opportunity for process optimization.
Thank you, Benjamin! AI's integration in CNC programming indeed presents a huge opportunity for optimizing processes, enhancing efficiency, and driving innovation.
Your article provided valuable insights into AI's integration in CNC programming, Michael. It's an exciting development for the industry.
Thank you, Zoe! I'm glad you found the article to provide valuable insights into AI's integration in CNC programming. It's a truly exciting development with immense potential for the industry.
I'm excited about the potential of AI in CNC programming. Your article, Michael, captured this potential perfectly.
Thank you, Julian! The potential of AI in CNC programming is certainly exciting, and capturing it perfectly in the article was my goal. I'm delighted it resonated with you.
Michael, your article was a fantastic read! How do you see AI impacting the overall competitiveness of CNC programming companies?
Hi Anna! AI significantly impacts the overall competitiveness of CNC programming companies by enabling improved efficiency, higher precision, reduced errors, optimized workflows, better resource management, and the ability to take on complex projects with agility. It enhances companies' ability to deliver quality products and services more competitively.
Your article, Michael, vividly outlined the potential impact of AI in CNC programming optimization. It's an exciting prospect.
Thank you, Isaac! Outlining the potential impact of AI in CNC programming optimization and highlighting the excitement it brings was my intention in the article. I'm glad you found it vivid.
Your article provided a deep understanding of AI's integration in CNC programming. Thank you for sharing your expertise, Michael!
You're welcome, Esther! Deepening the understanding of AI's integration in CNC programming through sharing expertise was my goal, and I'm glad you found it valuable. Thank you!
Michael, your article was a captivating read. How can AI integration enhance the precision of CNC programming?
Hello Leo! AI integration can enhance the precision of CNC programming by using advanced algorithms, machine learning models, and real-time monitoring. It improves accuracy in defining optimal toolpaths, predicting machining outcomes, and minimizing errors, resulting in higher precision throughout the process.
Your comprehensive article, Michael, perfectly demonstrated the impact of optimizing data collection and analysis in CNC programming.
Thank you, Ella! Demonstrating the impact of optimizing data collection and analysis in CNC programming was my objective, and I'm glad you found the article comprehensive and effective in doing so.
Michael, your article highlighted the potential of AI in CNC programming exceptionally. It's an exciting time for the industry.
Thank you, Aiden! I'm pleased to hear that the article effectively highlighted the potential of AI in CNC programming. It is indeed an exciting time for the industry, marked by innovations and advancements.
Your article, Michael, provided valuable insights into the integration of AI in CNC programming. It's a fascinating field.
Thank you, Liam! Providing valuable insights into the integration of AI in CNC programming and exploring this fascinating field were my intentions. I'm glad you found it insightful.
AI's integration in CNC programming brings immense potential. Your article, Michael, covered this brilliantly.
Thank you, Emily! AI's integration in CNC programming indeed brings immense potential, and aiming to cover it brilliantly in the article was my goal. I'm glad it resonated with you.
Your article shed light on the exciting role of AI in CNC programming, Michael. It's fascinating to witness this integration.
Thank you, Ethan! Shedding light on the exciting role of AI in CNC programming and witnessing its integration is indeed fascinating. I'm glad you found the article captivating.
Your article provided a comprehensive overview of AI integration in CNC programming. Michael, well done!
Thank you, Oliver! Providing a comprehensive overview of AI integration in CNC programming was my goal, and I'm glad you found it well-done.
I appreciate your expertise and the insights you shared in your article, Michael. Where do you see AI's integration in CNC programming heading in the future?
Thank you for your kind words, Emily! The future of AI's integration in CNC programming holds promise for even more advanced algorithms, increased automation, enhanced real-time decision-making, and further optimization across the entire process. It will continue to push the boundaries of what's achievable and redefine efficiency.
Your article, Michael, highlighted the significance of data analysis in CNC programming optimization. I found it captivating.
Thank you, Victoria! Highlighting the significance of data analysis in CNC programming optimization and making it captivating were my objectives. I'm glad you found it so.
Michael, your article provided a detailed and insightful exploration of AI in CNC programming. Well done!
Thank you, Leo! A detailed and insightful exploration of AI in CNC programming was my aim, and I'm glad you found it well-executed.
I'm intrigued by the potential of AI in CNC programming. Your article, Michael, explained it with remarkable clarity.
Thank you, Hunter! The potential of AI in CNC programming is indeed intriguing, and explaining it with remarkable clarity was my intention. I'm delighted you found it clear.
Your article elucidated the positive impact of AI integration in CNC programming, Michael. It's an exciting development.
Thank you, Sophia! Elucidating the positive impact of AI integration in CNC programming was one of my objectives, and I'm glad you found the article effective. It's an exciting development indeed.
I enjoyed reading your article, Michael. How does AI integration impact the learning curve for aspiring CNC programmers?
Thanks, Oliver! AI integration can positively impact the learning curve for aspiring CNC programmers by providing interactive learning environments, AI-assisted guidance, and virtual scenarios for practice. It can accelerate the acquisition of skills and offer hands-on learning opportunities that emulate real-world CNC programming challenges.
AI's potential in CNC programming optimization is incredible. Your article, Michael, perfectly underscored this.
Thank you, Victoria! The incredible potential AI holds in CNC programming optimization formed a focal point in the article. I'm glad it resonated with you.
Your article was highly informative, Michael. How do you see AI integration impacting CNC programming innovation?
Hi Ethan! AI integration significantly impacts CNC programming innovation by enabling faster prototyping, advanced algorithms for optimization, intelligent decision-making, and increased agility in tackling complex projects. It fosters continuous innovation by pushing the boundaries of what can be achieved.
Your article, Michael, delved into the potential of AI in CNC programming seamlessly. It's an exciting prospect.
Thank you, Daniel! Delving into the potential of AI in CNC programming seamlessly and emphasizing the excitement it brings was my aim. I'm glad you found it seamless.
AI's integration into CNC programming is revolutionary. Your article, Michael, wonderfully explored this revolution.
Thank you, Liam! The integration of AI into CNC programming is indeed revolutionary, and exploring this revolution wonderfully in the article was my intention. I'm glad you found it fascinating.
Your article provided valuable insights into AI's potential in CNC programming optimization. Thank you for sharing your expertise, Michael!
You're welcome, Emily! Providing valuable insights into AI's potential in CNC programming optimization was my goal, and I'm glad you found it valuable. Sharing expertise is a pleasure.
Michael, your article was fascinating! How do you envision the collaboration between AI and human expertise in CNC programming?
Thank you, Thomas! Envisioning the collaboration between AI and human expertise in CNC programming involves leveraging AI's capabilities for automation, optimization, and real-time decision-making while relying on human expertise for complex problem-solving, creativity, and overseeing AI systems. It emphasizes synergy and complementarity between AI and human skills.
The optimization of data collection and analysis is crucial in CNC programming. Michael, your article explained its significance brilliantly.
Thank you, Sarah! The significance of optimizing data collection and analysis in CNC programming formed a focal point in the article, and I'm glad you found the explanation brilliant.
Your article, Michael, showcased the possibilities of AI integration in CNC programming flawlessly. It's an exciting time for the industry.
Thank you, William! Showcasing the possibilities of AI integration in CNC programming flawlessly and emphasizing the exhilaration it brings was my intention. I'm delighted it resonated with you.
The impact of AI in CNC programming is remarkable. Your article, Michael, covered this topic brilliantly.
Thank you, Ella! The remarkable impact of AI in CNC programming formed a significant aspect of the article's coverage. I'm glad you found it brilliant.
Michael, your article provided valuable insights into AI's impact on CNC programming. It's an exciting field to explore.
Thank you, Julian! Providing valuable insights into AI's impact on CNC programming and highlighting the excitement it brings while exploring the field were my goals. I'm glad you found it exciting.
Your article was highly informative, Michael! How do you see AI integration influencing CNC programming scalability?
Hi Ava! AI integration influences CNC programming scalability by enabling higher efficiency, faster decision-making, optimized resource allocation, and the ability to handle more complex projects. It enhances scalability by minimizing errors and improving precision, allowing companies to take on larger and more demanding CNC programming tasks.
Your article, Michael, highlighted the potential of AI in CNC programming optimization perfectly. It's a game-changer.
Thank you, Caleb! Highlighting the potential of AI in CNC programming optimization perfectly was my intention, and I'm delighted you found it to be a game-changer.
Michael, your article provided a comprehensive exploration of AI's impact on CNC programming. Well done!
Thank you, Lily! A comprehensive exploration of AI's impact on CNC programming and delivering it effectively was my aim. I'm glad you found it well-executed.
AI integration is transforming CNC programming. Your article, Michael, showcased this revolution marvelously.
Thank you, David! Showcasing the revolution brought by AI integration in CNC programming marvelously was my goal. I'm glad you found it to be so.
Your article provided valuable insights and predictions regarding the future of AI in CNC programming, Michael. Thank you for sharing your expertise!
You're welcome, Sophie! Providing valuable insights and predictions regarding the future of AI in CNC programming is a pleasure. Thank you for appreciating and acknowledging the shared expertise.