Transforming Root Cause Analysis in TQM Technology with ChatGPT: An Innovative Approach
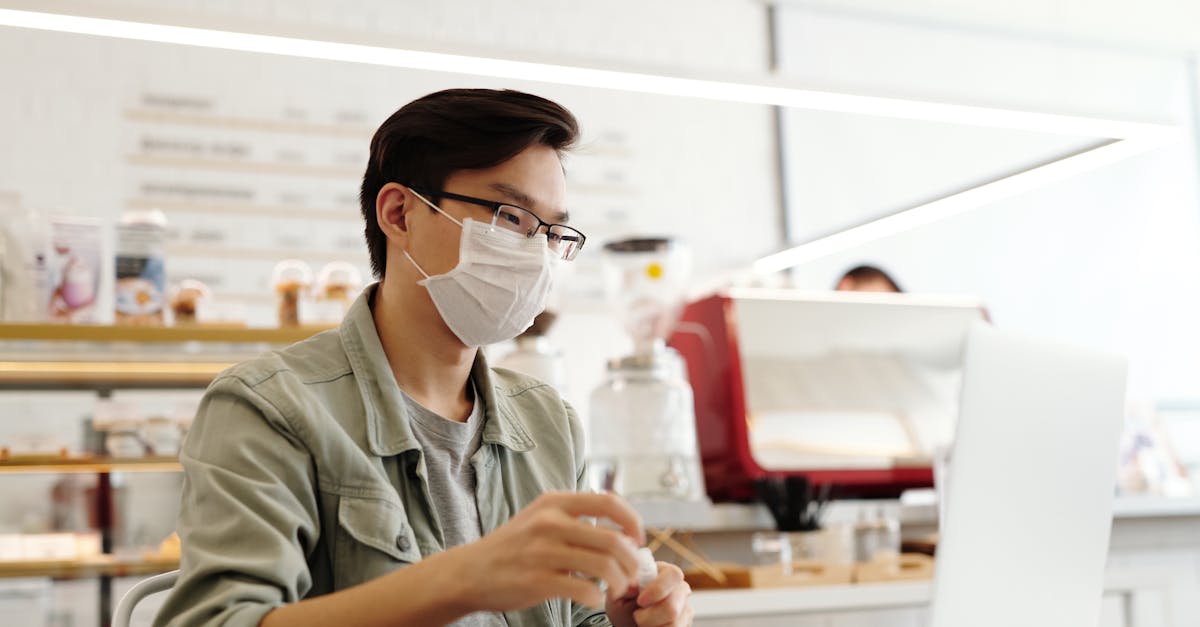
Total Quality Management (TQM) is a management approach aimed at continuously improving the quality of products and services offered by an organization. One of the most important tools used in TQM is Root Cause Analysis (RCA), which helps in identifying the underlying causes of defects or problems within processes.
What is Root Cause Analysis?
Root Cause Analysis is a systematic technique employed to identify the fundamental reasons behind a problem or non-conformance within a process. It strives to find the root cause, rather than merely addressing symptoms or immediate causes. RCA focuses on understanding the cause and effect relationship within complex systems and aims to prevent problems from recurring.
The Role of RCA in TQM
Within the TQM framework, RCA plays a crucial role in problem-solving and process improvement. It helps organizations in pinpointing the root cause of defects or failures rather than placing blame on individuals or teams. By identifying and addressing the root causes, organizations can prevent the recurrence of similar issues, leading to better quality products and services.
Process of Root Cause Analysis
The process of Root Cause Analysis typically involves the following steps:
- Identifying the Problem: The first step is to clearly define the problem or non-conformance that needs to be addressed. It is essential to identify the specific issue and its impact on the overall process.
- Gathering Data: In this step, relevant data related to the problem is collected. This may include process data, customer feedback, or any other information that can provide insights into the problem at hand.
- Identifying Possible Causes: Brainstorming sessions or analytical techniques are used to generate a list of potential causes for the identified problem. It is important to consider all possible causes to ensure a comprehensive analysis.
- Analyzing Causes: The potential causes are then analyzed further to determine their impact and likelihood of contributing to the problem. Techniques such as Pareto analysis or fishbone diagrams can be used to prioritize potential causes.
- Determining Root Cause: The next step involves identifying the root cause or causes that are most likely responsible for the problem. This is done by analyzing the relationship between the identified causes and the observed problem.
- Developing Corrective Actions: Once the root cause is determined, appropriate corrective actions can be developed. These actions should aim to eliminate or mitigate the root cause to prevent similar problems from occurring in the future.
- Implementing and Monitoring: The developed corrective actions are then implemented and monitored to verify their effectiveness. Regular follow-up and review are important to ensure that the problem is resolved and does not reoccur.
Benefits of Root Cause Analysis in TQM
Root Cause Analysis offers several benefits when applied within the TQM framework:
- Improved Problem-Solving: RCA helps in addressing the actual cause of a problem, leading to more effective problem-solving and preventing the recurrence of similar issues.
- Preventative Action: By targeting the root cause, RCA helps in implementing preventative actions that can minimize the occurrence of defects or failures.
- Enhanced Quality: RCA enables organizations to improve the quality of their processes, products, and services, resulting in higher customer satisfaction.
- Data-driven Decision Making: Root Cause Analysis relies on data and analysis rather than assumptions, allowing organizations to make informed decisions based on facts.
- Continuous Improvement: RCA supports the TQM philosophy of continuous improvement by uncovering areas for enhancement and driving process optimization.
Conclusion
Root Cause Analysis is a critical tool used within the Total Quality Management framework. By identifying the root cause of defects or problems, organizations can significantly enhance their problem-solving capabilities and drive continuous improvement. The systematic approach of RCA empowers organizations to address the fundamental cause, leading to long-term solutions and preventing recurring issues. Implementing Root Cause Analysis as part of TQM can result in better quality products and services, increased customer satisfaction, and improved overall organizational performance.
Comments:
This article presents an interesting perspective on using ChatGPT for transforming root cause analysis in TQM technology. I'm curious to learn more about how this approach can improve the efficiency and accuracy of the analysis process.
Anna, I agree. It seems like ChatGPT could assist in automating portions of the analysis by engaging in dynamic conversations to uncover potential causes. This approach might also help in reducing bias and improving data-driven decision-making.
Elizabeth, that's a great point. By eliminating bias and encouraging data-driven analysis, ChatGPT can potentially lead to more objective and reliable root cause identification.
I believe integrating ChatGPT into the root cause analysis process has the potential to streamline the identification of underlying issues. It could bring a fresh perspective and provide quick insights, ultimately enhancing TQM practices.
Michael, I agree with your thoughts on integrating ChatGPT into the root cause analysis process. It could help in uncovering hidden patterns and correlations in large datasets faster than traditional methods.
Emily, absolutely! ChatGPT's ability to analyze vast amounts of data in real-time could be a game-changer for organizations aiming to improve their TQM practices. It has the potential to save time and resources.
Michael, I'm glad we share the same opinion. It will be fascinating to see how organizations adopt this innovative approach and the impact it has on their overall quality management processes.
Although the use of ChatGPT in root cause analysis could speed up the process, I wonder about the reliability of the results. How accurate is ChatGPT in understanding complex issues and providing accurate recommendations?
I share the same concern, David. While ChatGPT can be useful, it's crucial to validate its recommendations by involving human experts and subjecting the analysis to a thorough review. Human oversight remains crucial in critical decision-making processes.
Thank you all for your comments and insights. I appreciate the concerns raised regarding the reliability of ChatGPT. Laura, you make an important point about the need for human oversight. Combining the strengths of both artificial intelligence and human expertise can yield the best results.
Thank you all for taking the time to read my article on transforming root cause analysis in TQM technology with ChatGPT! I'm excited to hear your thoughts and opinions.
Great article, Abraham! I found it really interesting how ChatGPT can be applied to improve root cause analysis in TQM. It seems like a promising approach to enhance problem-solving in organizations.
I agree, Emily. The potential of ChatGPT to assist in root cause analysis sounds compelling. It could enable more efficient identification and resolution of underlying issues, ultimately leading to improved quality management.
I'm a bit skeptical about relying heavily on AI technology for root cause analysis. While it may offer benefits, how can we ensure its accuracy and reliability in complex situations?
Valid concern, Jennifer. Explainable AI and transparency in the decision-making process are crucial areas to address when implementing AI tools like ChatGPT. It's essential to have proper validation methods in place and continuously evaluate the system's performance.
I understand your skepticism, Jennifer. However, with proper training and validation, AI technology like ChatGPT can become a valuable aid in root cause analysis. It's all about finding the right balance and utilizing it as a tool alongside human expertise.
I'm curious if ChatGPT can handle the complexity of real-world problems that often require a deep understanding of specific industries or domains. How adaptable is it to different contexts?
Excellent question, Richard. While ChatGPT has limitations, it can be fine-tuned and trained on domain-specific data to make it more adaptable. However, it's important to recognize that human expertise is still crucial, especially in complex situations.
Richard, I share your concern. AI tools like ChatGPT should not be seen as a substitute for domain expertise, but rather as a complementary tool to support the decision-making process.
I think using ChatGPT in root cause analysis can be beneficial, but it's important to ensure that biases in the training data don't influence the analysis. Otherwise, it could lead to incorrect or biased conclusions.
You make a valid point, Sarah. Bias mitigation is essential in AI development and deployment. Continuous monitoring and addressing biases should be a part of the process to ensure the accuracy and fairness of the analysis.
I'm excited about the potential time and cost savings that ChatGPT can bring to root cause analysis. It could streamline the process and allow teams to focus more on implementing solutions rather than spending excessive time on analysis.
I completely agree, Michael. Faster root cause analysis means quicker problem resolution, which is crucial for maintaining quality standards and customer satisfaction.
While ChatGPT can be useful, I worry about the potential loss of the human touch in root cause analysis. Human interactions and intuition play a significant role in understanding complex issues. How can we maintain that?
I understand your concern, Robert. AI technologies like ChatGPT should be seen as tools to augment human analysis, not replace it. The key is to find the right balance, leveraging AI capabilities while still valuing human experience and intuition.
Robert, you're absolutely right. The human element in root cause analysis should never be overlooked. AI tools can support the process, but they should never be a substitute for human judgment and critical thinking.
I see ChatGPT as a valuable tool for collaboration and knowledge sharing in root cause analysis. It can facilitate brainstorming and help teams explore various perspectives, leading to more comprehensive problem-solving approaches.
That's a great point, Michael. AI can act as a virtual team member, providing insights and suggestions based on its vast knowledge. It can enhance the collective intelligence of the team and foster innovative problem-solving.
I have concerns about the security and privacy implications of using ChatGPT for root cause analysis. How can we ensure that sensitive information is protected when using AI tools?
Valid point, Daniel. Data security and privacy should be a top priority when implementing AI tools. Proper data anonymization and encryption, along with access controls, should be in place to protect sensitive information.
Data security is indeed crucial, Daniel. Organizations should ensure compliance with relevant data protection regulations and deploy proper security measures when using AI tools for sensitive tasks like root cause analysis.
Thank you, Abraham. Data security should always be a priority, especially when AI tools interact with sensitive information.
Thank you, Abraham. Compliance with regulations and industry standards is essential when utilizing AI tools for tasks involving sensitive information.
I share your concerns, Daniel. Organizations need to have robust data protection measures in place and ensure compliance with relevant regulations when using AI tools for root cause analysis or any other sensitive tasks.
Abraham, do you have any examples of organizations that have successfully implemented ChatGPT for root cause analysis? I'd love to know more about real-world use cases.
Certainly, Sarah! One example is a manufacturing company that utilized ChatGPT to analyze production line issues. It helped the team identify underlying causes and implement targeted improvements, resulting in significant cost savings.
That's fascinating, Abraham! It demonstrates the practical value of ChatGPT in quality management. Real-world examples like these provide more confidence in adopting such AI-powered solutions.
Abraham, I would appreciate more information on how organizations can successfully integrate ChatGPT into their existing root cause analysis processes. Any specific recommendations?
Certainly, Michael! It's essential to start with a clear understanding of the organization's needs and goals. Assess the strengths and limitations of ChatGPT and identify the areas where it can provide the most value. Conduct pilot tests, gather feedback, and continuously refine the integration process.
Michael, apart from the technical aspects, it is important for organizations to provide training and familiarization sessions to the employees who will be using ChatGPT. Building a culture that embraces AI adoption is vital.
Abraham, in your opinion, what are the key challenges organizations might face when implementing ChatGPT for root cause analysis, and how can they overcome them?
Jennifer, one challenge is ensuring the availability of quality training data to provide accurate and reliable results. Organizations should invest time and resources in data collection and annotation. Another challenge is preventing model drift by continuously updating and retraining the AI models as the organization evolves.
I appreciate your response, Abraham. Organizations need to be vigilant in securing sensitive data and addressing potential privacy risks when adopting AI tools like ChatGPT.
I appreciate your response, Abraham. AI tools like ChatGPT can be valuable resources, but we should always keep in mind the need for transparency and accountability in their decision-making processes.
I completely agree, Jennifer. AI is a tool that can assist and augment human expertise, but it should never replace critical thinking and domain knowledge in complex problem-solving tasks.
Thank you for your insights, Abraham. A comprehensive integration plan that considers both technical and organizational aspects is key to successful ChatGPT adoption in root cause analysis.
I completely agree with you, Jennifer. Human judgment plays a significant role in understanding root causes. Besides, the analysis could also involve legal or ethical considerations that AI alone might not handle well.
Absolutely, Jennifer. AI tools should always be implemented responsibly, and organizations should prioritize ethical frameworks and guidelines to mitigate potential risks, biases, and privacy concerns.
I'd be interested in knowing more about the potential limitations of ChatGPT in root cause analysis. Are there any specific scenarios where it might not be as effective?
Richard, ChatGPT might face challenges in scenarios where there is limited or low-quality data available for training. Also, when the root cause analysis requires a deep understanding of highly specialized or rare domains, the AI system might struggle to provide accurate insights.
Thank you, Abraham. Fine-tuning ChatGPT on domain-specific data sounds like a practical approach to enhance its adaptability to diverse contexts in root cause analysis.
Abraham, I appreciate your insights in this article. Could you recommend any additional resources or research papers for those who want to explore the topic further?
Of course, Sarah! Some recommended resources on AI in root cause analysis include 'AI for Root Cause Analysis: A Comprehensive Survey' by Chen et al., and 'Transforming Quality Management with Artificial Intelligence' by Park and Kim. These provide in-depth analysis and further references.
Thank you, Abraham, for mentioning those resources. It's always helpful to have additional references when diving deeper into the subject.
That's true, Emily. Collaborative problem-solving yields better outcomes. AI tools like ChatGPT can supplement the collective intelligence of teams by offering different perspectives and insights.
I agree with you, Emily. ChatGPT can facilitate diverse perspectives and create an inclusive problem-solving environment. Combining human expertise with AI guidance can lead to better-rooted solutions.
I agree, Michael. Faster root cause analysis can enable organizations to respond promptly to issues and minimize the impact on operations and customer satisfaction.
I'm with you on that, Emily. ChatGPT's ability to facilitate collaboration and knowledge sharing can lead to more effective root cause analysis by leveraging the collective intelligence of teams.
Thank you, Abraham, for acknowledging the importance of maintaining the human touch in root cause analysis. Balancing AI capabilities with human intuition and experience is indeed crucial for effective problem-solving.
Agreed, Robert. The human touch brings empathy and context to root cause analysis, fostering a better understanding of underlying issues.