Unveiling the Power of ChatGPT: Exploring Model Inspection in Hypermesh Technology
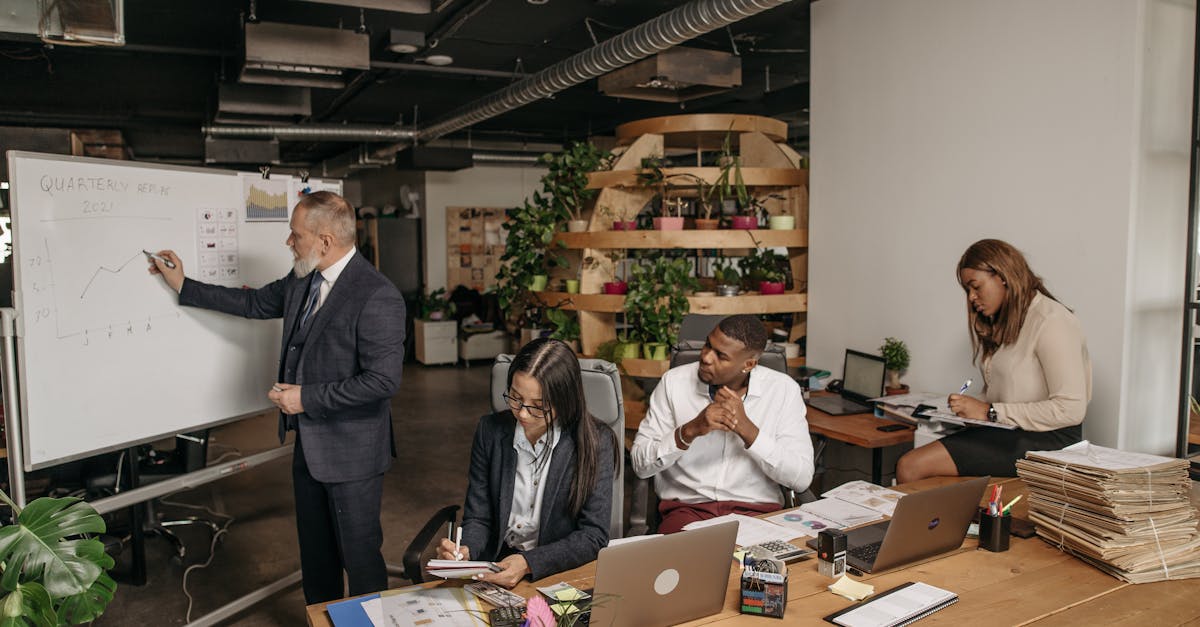
Hypermesh is a powerful software tool used for pre-processing finite element models. It is widely employed in various industries such as automotive, aerospace, and manufacturing for its versatile capabilities in meshing and model setup. In this article, we will focus on a specific area of Hypermesh functionality known as model inspection.
What is Model Inspection?
Model inspection is a crucial step in the finite element analysis (FEA) process. It involves carefully scrutinizing the mesh and the overall model setup to identify any potential issues or errors that may affect the accuracy of simulation results. Model inspection ensures the reliability and validity of FEA predictions.
Common Errors and Fixes
During model inspection, several common errors can be encountered. Here are some of them and their possible fixes:
1. Element Quality Issues
Element quality is a key factor that influences the accuracy of an FEA model. Poorly shaped or distorted elements can cause numerical instability and inaccurate results. Hypermesh provides various tools and functions to check and improve element quality, such as the Mesh Quality Index (MQI) and the Element Quality Index (EQI). It is important to address element quality issues by refining or re-meshing problematic regions.
2. Boundary Conditions
Applying incorrect or incomplete boundary conditions can lead to unrealistic results. Model inspection helps in verifying that all required boundary conditions, such as loads and constraints, are correctly defined. Hypermesh allows users to visualize and review the boundary conditions to ensure they are accurately represented in the model before analysis.
3. Element Connectivity
Incorrect element connectivity can cause discontinuities, gaps, or overlapping elements, leading to inaccurate stress distribution and deformation patterns. Model inspection in Hypermesh allows users to identify and resolve element connectivity errors to ensure a proper representation of the physical model.
4. Material Orientation
Assigning incorrect material orientations to elements can result in erroneous calculation of material properties, leading to inaccurate simulation results. Hypermesh provides visualization and editing tools to review and correct material orientations during model inspection.
5. Mesh Quality and Size
Model inspection involves checking for inconsistent mesh densities, excessive skewness, and properly capturing geometric details. Hypermesh offers various mesh quality assessment tools, such as the Mesh Skewness Index (MSI) and the Mesh Density Check, to help in identifying and resolving mesh quality and size issues.
Conclusion
Model inspection is a critical process in ensuring the accuracy and reliability of finite element models. Hypermesh provides extensive functionalities and tools to support model inspection procedures. By addressing common errors and issues during model inspection, analysts can confidently proceed with accurate simulations, making informed decisions based on reliable results.
Remember, thorough model inspection and resolution of identified issues is essential for obtaining dependable and trustworthy predictions from finite element analysis.
Comments:
Great article! I've always been curious about the inner workings of ChatGPT.
Indeed, it's fascinating how technology like ChatGPT can be inspected.
I agree! Model inspection can help us understand how these AI systems generate responses.
Hypermesh technology is revolutionizing the industry.
Absolutely! It allows us to gain insights into the decision-making process of AI models.
Exactly, Sarah! It's crucial to ensure AI models are making fair and unbiased decisions.
Thank you all for your comments! I'm glad you find the topic interesting.
Hypermesh has certainly made a significant impact on our operations.
I agree, Samantha! Using Hypermesh has improved our productivity.
This article is really informative. It's great to see how far AI technology has come.
Definitely! AI advancements are continuously pushing boundaries.
It's astonishing how AI models can perform at such high levels.
I'm curious to know how model inspection is carried out. Anyone know specifics?
From what I understand, model inspection involves analyzing the internal representations and processes of the AI model.
Interesting, Oliver! I'll look into it further. Thanks!
You're welcome, Sophia! Feel free to ask if you have any more questions.
Hypermesh surely has potential. Can't wait to see its future applications.
Hypermesh has really improved the efficiency of our design process.
Model inspection can help identify biases and improve the fairness of AI systems.
That's true, Robert. Bias detection in AI is crucial for building trust.
Absolutely, Olivia! It's vital to ensure fairness and avoid reinforcing existing biases.
Our team has seen tremendous benefits since integrating Hypermesh into our workflow.
AI continues to amaze me. It'll be interesting to see what the future holds.
This article provides great insights into the capabilities of ChatGPT.
Absolutely, Logan! ChatGPT has revolutionized natural language processing.
Hypermesh has enhanced our collaboration, allowing for seamless feedback.
I'm pleased to see your enthusiasm about ChatGPT and Hypermesh! They indeed have incredible potential.
Ethan, can you share any insights on the challenges faced during model inspection?
Certainly, David! One challenge is interpreting the internal representations of the model.
Thanks for the response, Ethan. Overcoming those challenges must require expertise.
Indeed, David. Expertise and continuous research play a significant role in improving model inspection techniques.
AI technology is evolving rapidly, and ChatGPT seems to be at the forefront.
The collaboration features in Hypermesh have been a game-changer for our team.
Another challenge is assessing the decision-making process for complex AI models.
Ethan, I appreciate your insights. Model inspection seems like a complex task.
Identifying and mitigating biases is an ongoing effort in AI research.
You're right, Jonathan. Continuous improvement is necessary to build inclusive AI systems.
AI's potential is vast, and it raises intriguing ethical considerations.
I'm amazed by the progress made in AI. Can't wait to see what's next!
I agree, Karen! AI advancements have the potential to revolutionize various fields.
Hypermesh has transformed our product development cycle. It's incredible.
Fairness and ethics need to be at the forefront when developing AI applications.
You're absolutely right, Liam. Ethical considerations should guide AI development.
Thank you all for your valuable comments and insights! It's been a great discussion.
Thank you, Ethan, for sharing your knowledge. This discussion has been enlightening.
You're welcome, Sophia! I'm glad you found the discussion helpful.
Definitely! It's great to have these insightful discussions.
Agreed, Sophia! Engaging in discussions helps us expand our understanding.
Well said, Ethan! Thank you once again for facilitating this discussion.
You're most welcome, Sophia! It's been a pleasure to have you here.
Likewise, Ethan! Looking forward to more informative articles and discussions.
Absolutely, Sophia! Stay tuned for more interesting content.
This article has opened my eyes to the potential of model inspection. Thank you!
You're welcome, Oliver! I'm glad this article could provide you valuable insights.
Definitely. Keep up the great work, Ethan!
Thank you, Oliver! I appreciate your support.
No problem, Ethan! Looking forward to what you'll share next.
Likewise, Oliver! Stay tuned for more exciting content.
This article has given me a deeper understanding of model inspection. Thank you!
You're welcome, Emily! I'm glad the article could enhance your understanding.
Definitely. The insights shared here are invaluable.
Thank you, Emily! I appreciate your feedback.
No problem, Ethan! Looking forward to future articles.
Likewise, Emily! I'll continue to provide informative content.
Thank you, Ethan! Have a great day.
You too, Emily! Take care.